Reduce Unplanned Downtime: A $20 Billion Challenge in the Chemical Industry
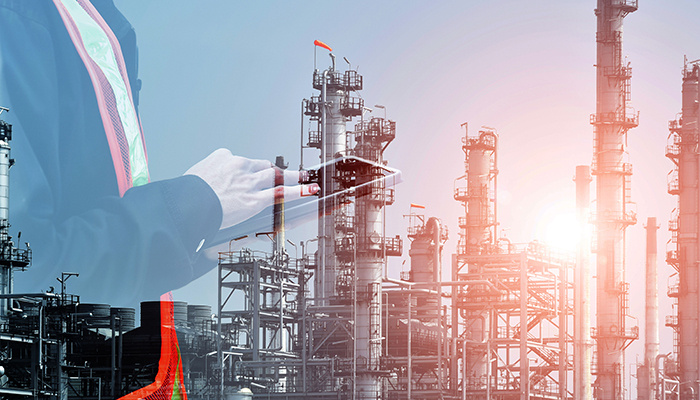
In the dynamic landscape of the chemical industry, operational efficiency and safety are paramount. Companies must ensure smooth operations, minimize downtime, and maintain high productivity levels while adhering to stringent safety regulations. A unified connected worker strategy, seamlessly integrated with ERP systems, and robust shift handover processes are essential to achieve these goals. This blog explores how Innovapptive's connected worker solutions enhance key operational KPIs such as Mean Time to Repair (MTTR), unplanned downtime, and compliance costs.
Let's Start with Math: The ROI of Reducing Unplanned Downtime
Let's consider an average chemical plant that experiences 10 unplanned downtime incidents per year. Suppose each incident causes a downtime of 5 hours, resulting in significant production losses and additional costs.
According to industry reports, the average loss per hour of downtime in the chemical industry is approximately $100,000 (Deloitte United States) (MC). With an estimated total annual downtime of 50 hours, this results in an annual cost of downtime of $5,000,000.
- Current Cost of Downtime:
- Average loss per hour: $100,000
- Total annual downtime: 50 hours
- Annual cost of downtime: 50 hours x $100,000 = $5,000,000
- Projected Savings with Innovapptive's Solutions:
- Reduction in downtime by 20%: 10 hours saved
- Cost savings: 10 hours x $100,000 = $1,000,000
By reducing unplanned downtime by just 20%, the plant can save approximately $1 million annually. This substantial saving highlights the significant ROI impact of implementing Innovapptive's connected worker solutions.
The Financial Impact of Unplanned Downtime
Unplanned downtime is a significant issue for the chemical industry, costing an estimated $20 billion annually (Sight Machine) (Arcweb Technologies). This downtime not only leads to lost production but also affects maintenance costs, customer satisfaction, and safety compliance. For instance, even a 1% downtime rate can result in substantial financial losses, with costs rising dramatically in larger facilities.
Real-World Incident: The Need for Enhanced Safety
On July 14, 2023, the Dow Louisiana Operations plant in Plaquemine, Louisiana, experienced multiple explosions that highlighted the critical need for robust safety measures and seamless communication. The explosions, which occurred at the Glycol II Ethylene Oxide Finishing unit, prompted an immediate response from emergency services and hazmat teams. The incident underscored the importance of efficient shift handovers and real-time data access to prevent such disasters and ensure the safety of both workers and the surrounding community (County Local News).
Following the incident, authorities emphasized the importance of stringent safety protocols and the integration of advanced digital solutions to enhance operational safety and efficiency.
Innovapptive's Mobile-First Approach
Innovapptive's connected worker solutions prioritize a mobile-first strategy, offering world-class, easy-to-use mobile apps tailored for operations, maintenance, and storeroom departments. Along with the capability to handle daily rounds, handovers, preventive and corrective work orders, ad-hoc inspections, and inventory management through easy-to-use mobile apps, Innovapptive's solution comes pre-packed with 45+ modules and 300+ features designed to empower frontline & back-office staffs and solve operational challenges efficiently.
Operational KPIs and Improvements
1. Mean Time to Repair (MTTR)
Impact: Reducing MTTR is critical for maintaining production schedules and minimizing downtime costs.
Innovapptive’s Contribution: The AI-driven round builder and in-built chat for collaboration streamline the issue resolution process, significantly reducing repair times.
- Direct SAP Integration: Seamlessly connects to SAP for efficient work order management.
- Historical Information Access: Provides technicians with historical data from previous work orders and asset historians for quick, informed decision-making.
- Computer Vision-Based Issue Identification: Utilizes AI to identify issues through visual inspections, enhancing accuracy and speed.
- Real-Time Collaboration Tools: In-built chat and collaboration features allow for immediate communication between field operators and supervisors.
2. Unplanned Downtime
Impact: Unplanned downtime can lead to substantial financial losses and disrupt production.
Innovapptive’s Contribution: Features like direct ERP connectivity, dynamic route planning, and risk-based priority settings help preempt issues and address them before they escalate.
- Control Centers and Back-office Platform: Provides 360 Degree live visibility of field activities, enabling back-office staff to take immediate action.
- Computer Vision: Detects defects and issues early, preventing minor problems from escalating.
- Spare Parts Information: Ensures quick access to spare parts information, reducing time lost in searching for necessary components.
3. Compliance Costs
Impact: High compliance costs can strain resources and reduce profitability.
- Task Completion Summaries: Detailed reports upon work order completion to ensure compliance.
- Custom Compliance Dashboards: Pre-built, configurable dashboards for supervisors to monitor compliance.
- Operational KPI Tracking: Dashboards to track and visualize key operational performance indicators.
14 Key and Disruptive Differentiators of Innovapptive’s Solutions
- Unified Operational Platform: One platform to connect your operations, maintenance, and storerooms, ensuring cohesiveness across all departments.
- Certified SAP Integration: Ensures seamless connectivity with SAP systems.
- Mobile Operator Rounds: with Advanced Predictive Analysis Capabilities: Enhance operational efficiency with predictive insights.
- Automated Shift Handover Reports with Acknowledgements: Ensure safety and compliance with automated, acknowledged handover reports.
- Approval Framework: Manage round approvals and key process approvals before work like permits and handling MOCs (Management of Change).
- End-to-End Work Order Management: From issue reporting to work order execution, streamline every step.
- Embedded Checklist Capabilities: Integrate checklists directly into work orders for comprehensive task management.
- Asset 360: Provide technicians with historical information from historians and previous work for a quick start.
- End-to-End Inventory Management: Facilitate efficient spare parts collection and inventory management.
- Offline/Online Functionality: Ensure continuous operations even in areas with poor connectivity.
- In-Built Collaboration Tools: Facilitate real-time communication between field operators and back-office supervisors.
- AI/ML Capabilities: Multiple AI capabilities including predictive insights, SOP creation, and paper form conversions.
- Computer Vision-Based Issue Identification: Detects the slightest wear and tear before they escalate into major issues.
- Risk-Based Priority Determination: Automatically prioritizes issues based on impact and likelihood, eliminating human error.
And the list goes on. Innovapptive's solutions are designed to cover every aspect of your operational needs, ensuring a truly connected and efficient work environment.
Enhancing Safety and Compliance
Safety is a top priority in the chemical industry. Innovapptive's connected worker solutions enhance safety by providing digital work instructions, real-time data access, and comprehensive audit trails. This not only ensures compliance with safety regulations but also fosters a safer work environment.
Research Findings
Recent studies indicate that integrating connected worker solutions with ERP systems can lead to significant improvements in operational efficiency and safety. According to a report by ARC Advisory Group, companies that implemented digital operator rounds saw a 20% reduction in unplanned downtime and a 30% improvement in compliance with safety regulations (Sight Machine).
Conclusion
A unified connected worker strategy with strong ERP integration and seamless shift handover is crucial for the chemical industry. Innovapptive’s mobile-first solutions empower frontline workers, streamline operations, and enhance key operational KPIs. By adopting these advanced technologies, chemical companies can achieve higher efficiency, reduced downtime, and improved safety, positioning themselves for sustained success in a competitive market.
For more information on how Innovapptive’s solutions can transform your operations, visit our website.
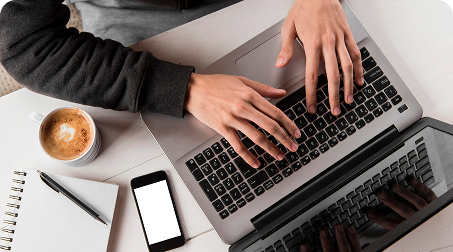
See It In Action
Schedule a personalized demo to see how our solutions can help your business thrive.
- 20-08-2025
Building the future of Industrial Operations with Innovapptive and AWS
Most manufacturers have already gone digital. Yet business outcomes haven’t moved in step. Many...
- 22-04-2025
The $3.6B Unlock: Solving the Chemical Industry’s Labor Crisis and EBITDA Pressure in One Move
“Constraints don’t slow innovation—they force it.”
- 21-04-2025
Chemical Industry's Margin Erosion: A Wake-Up Call for Operational Efficiency Amid China's Oversupply
The global chemical industry is facing mounting challenges, with revenue declines and shrinking...