Four Must-Haves for a Mobile Plant Maintenance Solution
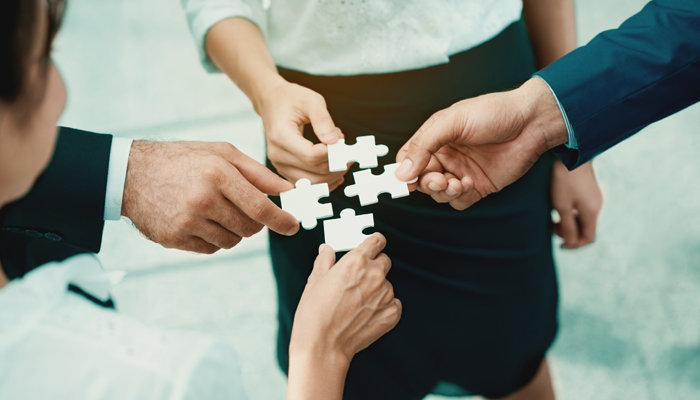
In today’s rapidly evolving industrial landscape, organizations in asset-intensive sectors such as oil & gas, utilities, and manufacturing need modern, scalable solutions to stay competitive. For SAP Plant Maintenance users, having a reliable mobile plant maintenance solution can significantly enhance operational efficiency, workforce productivity, and equipment reliability.
Innovapptive’s mobile plant maintenance solution is specifically designed to integrate with SAP Plant Maintenance, offering the flexibility, real-time data access, and collaboration tools necessary to streamline maintenance processes. Below are the four essential components that ensure your plant maintenance solution can meet the complex needs of asset-intensive operations.
![]() |
Digital operator rounds |
Maintaining asset reliability and safety in industrial facilities begins with efficient operator rounds. With Innovapptive’s Digital Operator Rounds, plant operators can capture and input critical data directly into the SAP system in real time. This data helps detect equipment issues early and prevents costly downtime.
Traditional methods, such as paper-based checklists, often lead to delays, data entry errors, and missed opportunities for proactive maintenance. Innovapptive’s solution digitizes these rounds, allowing operators to log data using mobile devices, ensuring that critical issues are addressed promptly and that information is available company-wide. This enhances overall operational visibility and helps managers respond to potential problems before they escalate.
![]() |
Work order management |
Innovapptive’s mobile plant maintenance solution enables real-time work order management, a critical feature that ensures timely execution of preventive, predictive, or reactive maintenance tasks. By integrating with SAP, facility managers can monitor the status of work orders instantly, prioritize urgent tasks, and reduce delays caused by manual processes.
This feature also allows teams to schedule maintenance more effectively, preventing disruptions in production and optimizing asset uptime. Real-time communication between maintenance teams and plant managers enables quicker decision-making, helping to maintain operational continuity.
orders.
![]() |
Digital work instructions |
As the workforce evolves, with experienced technicians retiring and newer employees stepping in, the need for efficient knowledge transfer is becoming more urgent. Innovapptive’s mobile plant maintenance solution addresses this challenge with digital work instructions, which provide clear, step-by-step guidance to field technicians directly on their mobile devices.
These digital instructions can include augmented reality (AR) features, multimedia content, and real-time updates, helping technicians complete tasks more accurately and efficiently. With instant access to instructions, your team can reduce downtime and increase wrench time, ensuring that maintenance tasks are completed correctly the first time, without delays.
![]() |
Configurable forms and checklists |
Compliance with industry regulations and safety protocols is essential in asset-intensive industries. Innovapptive’s mobile plant maintenance solution includes configurable forms and checklists that allow managers to quickly update and distribute regulatory documents to field teams. These mobile forms can be customized on the fly, ensuring that technicians are always working with the most up-to-date information.
This feature helps companies avoid regulatory penalties and ensures that safety standards are consistently met. With real-time access to updated checklists and forms, field teams can maintain compliance more easily, improving overall operational safety and reducing the risk of costly errors.
Transform Your Maintenance Operations with Innovapptive
Innovapptive’s mobile plant maintenance solution is built to empower industrial teams with real-time data, actionable insights, and seamless SAP integration. From digital operator rounds to real-time work order management, our platform ensures that your team is equipped with the tools needed to maximize productivity, reduce downtime, and maintain compliance.
To experience these benefits firsthand, book a live demo or contact our Connected Worker platform experts at 1-844-464-6668.
FAQs
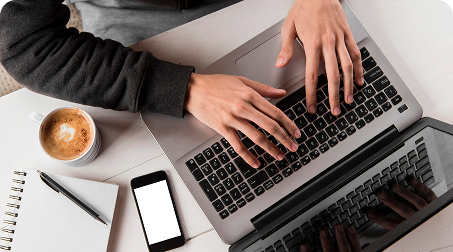
See It In Action
Schedule a personalized demo to see how our solutions can help your business thrive.
- 22-04-2025
The $3.6B Unlock: Solving the Chemical Industry’s Labor Crisis and EBITDA Pressure in One Move
“Constraints don’t slow innovation—they force it.”
- 21-04-2025
Chemical Industry's Margin Erosion: A Wake-Up Call for Operational Efficiency Amid China's Oversupply
The global chemical industry is facing mounting challenges, with revenue declines and shrinking...
- 21-04-2025
Why Wrench Time Isn’t Improving: The Hidden Costs of Traditional Maintenance Scheduling
For years, industrial leaders have relied on a common but flawed assumption: "Better planning and...