How to Effectively Leverage Time-Based Maintenance Strategies
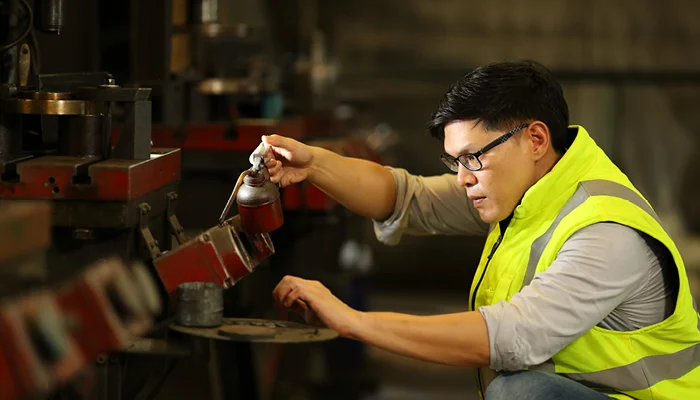
In the industrial world, ensuring your equipment operates reliably is key to maintaining productivity and avoiding costly downtime. Time-based maintenance—a common preventive maintenance strategy—ensures regular care for assets based on a set schedule. Much like changing your oil every 3,000 miles or getting your teeth cleaned every six months, time-based maintenance focuses on keeping equipment in top condition through periodic servicing.
What is Time-Based Maintenance?
Time-based maintenance (TBM), also referred to as periodic maintenance, is a scheduled strategy where routine maintenance tasks—such as lubrication, cleaning, or part replacements—are performed at regular intervals. These intervals are typically based on manufacturer recommendations, historical data, or mean time between failures (MTBF) metrics. The goal of TBM is to reduce equipment wear, enhance reliability, and prevent unplanned failures.
Advantages of Time-Based Maintenance
Incorporating time-based maintenance strategies into your overall maintenance plan can offer several benefits:
-
Ease of Implementation: Time-based maintenance activities are simple to schedule and require minimal training. Tasks like cleaning or lubrication can be easily repeated without needing specialized equipment like sensors.
-
Improved Asset Reliability: By maintaining a regular service schedule, companies can enhance equipment reliability, reducing unexpected breakdowns and saving on corrective maintenance costs.
-
Cost-Effective: Unlike condition-based maintenance, which requires continuous monitoring via sensors, time-based maintenance is easier and less expensive to implement for certain types of equipment.
-
Efficient Resource Allocation: By having a predetermined maintenance schedule, maintenance managers can better allocate resources—technicians, tools, and parts—minimizing downtime and increasing productivity.
-
Predictability: For assets that run continuously, wear and tear are more predictable, making time-based maintenance the right strategy to minimize failures.
Challenges of Time-Based Maintenance
Despite its benefits, time-based maintenance also has limitations. The primary challenge lies in its reliance solely on equipment age or runtime without considering the asset's condition or external factors:
-
Lack of Condition Monitoring: Time-based maintenance doesn't account for real-time equipment health. External factors such as temperature, pressure, and environmental conditions may affect asset performance, causing unpredictable failures that time-based schedules cannot prevent.
-
Over-Maintenance and Under-Maintenance: If the maintenance schedule is too frequent, it can lead to over-maintenance, which wastes resources and increases the risk of human errors, such as improper reassembly. On the other hand, a schedule that’s too infrequent risks under-maintenance, increasing the likelihood of equipment failure.
-
Not Suitable for All Assets: Time-based maintenance works best for equipment that operates continuously. It’s less effective for assets that are only used occasionally, as their wear and tear patterns are harder to predict.
Best Practices for Implementing Time-Based Maintenance
To ensure the success of your time-based maintenance strategy, consider these best practices:
-
Identify Suitable Equipment: Time-based maintenance is ideal for equipment like fire extinguishers, smoke alarms, or HVAC units that require regular inspections to maintain safety and compliance.
-
Leverage Historical Data: Use historical asset data, including OEM recommendations and MTBF statistics, to plan optimal maintenance schedules. This ensures that maintenance is neither too frequent nor too sparse, reducing the risk of asset failure.
-
Use an Enterprise Asset Management (EAM) System: A comprehensive EAM solution breaks down data silos, providing high-quality asset data that maintenance managers can use to create effective time-based maintenance schedules. By integrating real-time data with historical trends, an EAM system helps streamline planning and improve maintenance execution.
-
Monitor and Adjust: While time-based maintenance is predictable, it’s essential to monitor equipment performance and adjust schedules as necessary. In some cases, introducing condition-based maintenance for critical assets may be beneficial to complement the time-based approach.
Recent Trends in Maintenance Strategies
As technology evolves, new trends are emerging that enhance the effectiveness of time-based maintenance:
-
Mobile Maintenance Solutions: Leveraging mobile EAM solutions allows technicians to access maintenance schedules and record tasks on the go, increasing productivity and ensuring timely execution.
-
Data-Driven Maintenance: By combining time-based and predictive maintenance strategies, companies can make smarter decisions, maximizing uptime and minimizing unnecessary maintenance efforts.
-
IoT and Sensors: Although time-based maintenance typically doesn’t rely on sensors, the integration of IoT technologies can provide additional insights, allowing businesses to monitor certain assets more closely and adjust time-based schedules based on actual performance data.
Final Thoughts
Time-based maintenance remains a valuable strategy in ensuring equipment longevity and operational efficiency. While it may not be ideal for all assets, this approach is easy to implement, predictable, and cost-effective for equipment with regular wear patterns. By using an EAM system, analyzing historical data, and adopting mobile maintenance tools, companies can optimize their time-based maintenance strategy, keeping their assets in peak condition.
Maximize your asset performance with an optimized time-based maintenance strategy. Schedule a demo today to learn how our EAM solutions can streamline your maintenance processes.
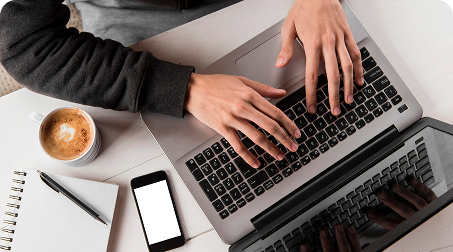
See It In Action
Schedule a personalized demo to see how our solutions can help your business thrive.
- 20-08-2025
Building the future of Industrial Operations with Innovapptive and AWS
Most manufacturers have already gone digital. Yet business outcomes haven’t moved in step. Many...
- 22-04-2025
The $3.6B Unlock: Solving the Chemical Industry’s Labor Crisis and EBITDA Pressure in One Move
“Constraints don’t slow innovation—they force it.”
- 21-04-2025
Chemical Industry's Margin Erosion: A Wake-Up Call for Operational Efficiency Amid China's Oversupply
The global chemical industry is facing mounting challenges, with revenue declines and shrinking...