Industry 4.0 vs. Traditional Manufacturing: Key Differences, Benefits & Digital Transformation Guide
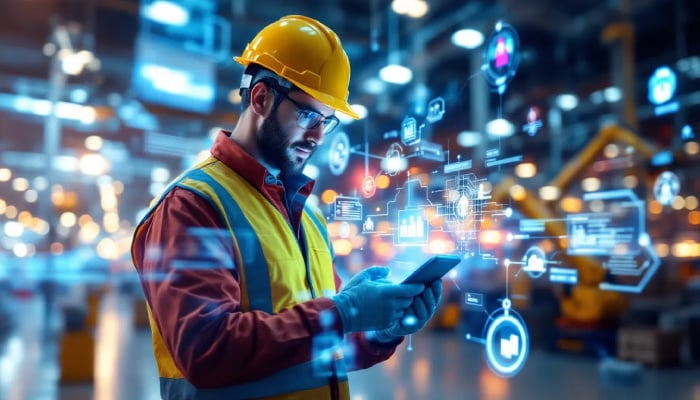
The shop floor is no longer just a place of machines and manual labor—it’s becoming a smart, dynamic ecosystem. As technologies like AI, IoT, and predictive analytics migrate from the boardroom to the factory floor, manufacturers are facing a pivotal choice: embrace the future or risk falling behind.
This isn’t just about adopting new tools—it’s about unlocking transformational value. According to the World Economic Forum’s Global Lighthouse Network (2025), top digital factories that embraced Fourth Industrial Revolution technologies saw an average 53% increase in labor productivity and a 26% reduction in manufacturing conversion costs. These gains aren’t theoretical—they’re happening now.
The tug-of-war between traditional manufacturing and Industry 4.0 is real, and the path forward demands more than incremental upgrades—it calls for a complete mindset shift. So, where do legacy operations fit into this connected, AI-driven world? And more importantly, how can companies evolve without dismantling their existing systems?
Traditional Manufacturing: Familiar But Fading
Traditional manufacturing has been the cornerstone of industrial development for centuries. Characterized by manual processes, segmented operations, and a heavy reliance on human intervention, this approach has its merits but also significant limitations.
Core challenges include:
- Siloed operations: Paper-based work orders and disconnected systems delay communication and create blind spots.
- Reactive maintenance: Unexpected equipment breakdowns eat into productivity and margins.
- Heavy workforce dependency: As skilled workers retire, their knowledge retires with them, increasing training and compliance challenges.
- Lack of agility: Process changes take time, slowing innovation and response to disruption.
Industry 4.0: A Connected, Intelligent Evolution
Enter Industry 4.0—a fusion of advanced technologies that blur the lines between the physical and digital worlds. This paradigm leverages the Internet of Things (IoT), artificial intelligence (AI), robotics, and big data analytics to create smart factories. In these environments, machines and systems communicate and collaborate in real time, enabling unprecedented levels of efficiency and adaptability.
According to McKinsey, equipping frontline operators with digital collaboration and “connected worker” tools can boost productivity in key processes by 20–30%. Real-time access to expert knowledge, remote assistance, and mobile work instructions help workers resolve issues faster—in areas like maintenance and quality control—driving significant performance gains on the factory floor.
Pillars of Industry 4.0:
- IoT-powered asset visibility: Real-time data from connected sensors across machines and facilities.
- Predictive and prescriptive maintenance: AI models anticipate failures and recommend fixes before disruptions occur.
- Digital work instructions: Paper is replaced with mobile-first workflows, streamlining task execution and knowledge capture.
- Data-driven decisions: Dashboards and analyticsක Dashboards and analytics unify data across sites, enabling faster, more confident action.
- Empowered workers: Frontline teams use intuitive apps, visual SOPs, and AR-enabled tools to work smarter and safer.
Bridging the Gap with Connected Worker Platforms
Transitioning to Industry 4.0 doesn’t mean ripping out legacy systems. The key is digitizing the last mile of work—where people, assets, and data intersect. That’s where solutions like an AI-first Connected Worker Platform become game-changers.
By digitizing critical workflows—such as maintenance, inventory management, and field operations—we enable manufacturers to:
- Connect frontline workers to enterprise systems like SAP in real time.
- Replace paper-based inspections, maintenance, and inventory tasks with mobile apps.
- Offer AI-based guidance and data capture to improve compliance, safety, and productivity.
- Empower both field and plant workers to work independently, yet collaboratively, with full visibility.
Traditional vs. Industry 4.0
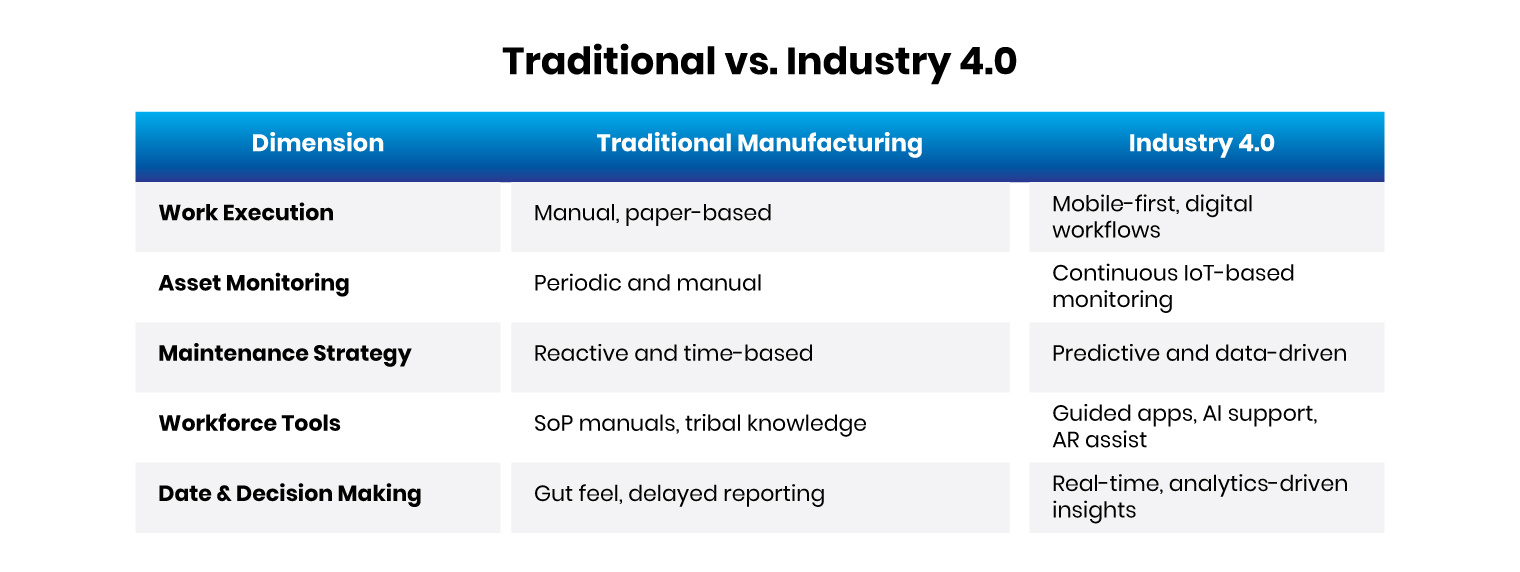
Why the Shift Can’t Wait
The urgency of embracing Industry 4.0 isn’t just about staying ahead of the competition—it’s about staying in business. The increasing volatility of supply chains, the shortage of skilled workers, rising energy costs, and sustainability mandates make traditional models untenable in the long term.
Manufacturers that digitize their frontline operations and unify their systems gain more than efficiency—they gain resilience. With solutions like Innovapptive’s, they can:
- Reduce downtime through predictive maintenance and intelligent inspections.
- Enhance workforce productivity by providing step-by-step digital work instructions.
- Improve safety and compliance through real-time reporting and mobile audits.
- Accelerate onboarding and reduce training time with AI-enabled guidance and visual SOPs.
These benefits go beyond incremental improvements—they represent a fundamental shift in how work is done.
The Future is Human-First and AI-Enabled
Despite its technological nature, Industry 4.0 is ultimately human-centric. It’s not about replacing people but equipping them with better tools, real-time insights, and safer environments.
Innovapptive’s focus on connecting workers, assets, and enterprise systems directly supports this vision. By enabling seamless communication between back-office teams and field workers, the platform fosters a collaborative culture that’s agile, efficient, and scalable.
As AI continues to evolve, the possibilities for prescriptive recommendations, autonomous planning, and hyper-personalized support for workers will only grow. Manufacturers who invest in these capabilities today are positioning themselves for sustained leadership tomorrow.
Innovapptive doesn’t replace traditional manufacturing—it supercharges it.
Conclusion: Don’t Just Catch Up—Leap Ahead
The manufacturing landscape is evolving at an unprecedented pace. To remain competitive, manufacturers must not only understand the differences between traditional methods and Industry 4.0 but also take proactive steps toward digital transformation. Innovapptive's Connected Worker Platform offers the tools and insights necessary to navigate this complex journey.
Ready to transform your operations and lead in the era of smart manufacturing? Discover how Innovapptive can accelerate your Industry 4.0 journey by visiting their website:
Embrace the future of manufacturing today, and position your organization at the forefront of innovation and efficiency.
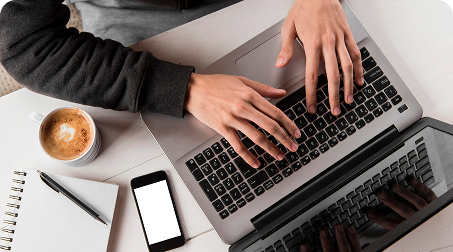
See It In Action
Schedule a personalized demo to see how our solutions can help your business thrive.
- 20-08-2025
Building the future of Industrial Operations with Innovapptive and AWS
Most manufacturers have already gone digital. Yet business outcomes haven’t moved in step. Many...
- 22-04-2025
The $3.6B Unlock: Solving the Chemical Industry’s Labor Crisis and EBITDA Pressure in One Move
“Constraints don’t slow innovation—they force it.”
- 21-04-2025
Chemical Industry's Margin Erosion: A Wake-Up Call for Operational Efficiency Amid China's Oversupply
The global chemical industry is facing mounting challenges, with revenue declines and shrinking...