Keys to Effectively Develop Your Reliability Centered Maintenance Process
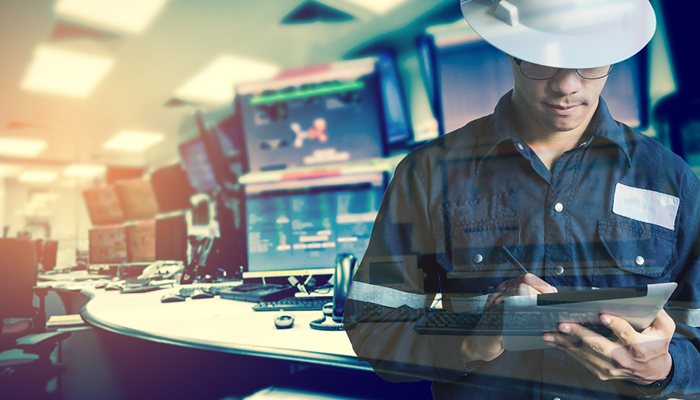
Reliability Centered Maintenance (RCM) is a corporate level maintenance process to help you ensure that tasks are performed in an efficient, cost-effective, reliable, and safe manner. A well-managed RCM program is the application of a specific maintenance strategy on each of the assets of the facility. Having a program in place that establishes an effective RCM program to document the entire process (system, equipment, or part life cycle) for every asset in the facility is critical for the success of your maintenance process.
Equipment breakdown is not always straight-line, or linear. It’s definitely unwanted!
The purpose of RCM is to ensure that your maintenance and inspection tasks are positioned around refining the reliability and safety of your equipment, such as your oil pumps, heavy trucks, production line, etc. Tasks may be preventive, predictive, or involve nondestructive inspections in order to identify or monitor flaws. Strategies are optimized to ensure the productivity of the plant is maintained using cost-effective techniques.
RCM identifies what functions are most critical and then optimizes, or attempts to, your maintenance strategies in order to minimize system failures and increase equipment reliability and availability. Your most critical assets are those that are likely to fail often or have large consequences of failure. With this maintenance strategy, failure modes and their consequences are identified; all while the function of your equipment is considered. Cost-effective maintenance techniques that minimize the possibility of failure can then be determined and adopted to improve the reliability of your facility.
While there is no set standard for RCM programs there are a few main principles that are necessary for a strong program:
- Preserve system function
- Identify failure modes that can affect the system function
- Prioritize failure modes
- Select valid and real tasks to control the failure modes
The RCM process identifies the functions of your assets that are most vital and then seeks to maximize maintenance strategies so that system failures are eliminated or kept at a minimum and equipment reliability is increased. There are seven questions that RCM process answers, according to the SAE JA1011 standard, which detail the minimum criteria processes must comply with to be considered RCM.
- What are the functions and expected standards of performance of an asset in its present operating context (functions)?
- What ways can an asset fail to fulfill its functions (functional failures)?
- What are the causes of each functional failure (failure modes)?
- What happens when failures occur (failure effects)?
- What ways do each failure matter (failure consequences)?
- What should be done to predict or prevent failure (proactive tasks and task intervals)?
- What should be done if a suitable proactive task is not identified (default actions)?
Leverage Top Mobile Work Order Management Solution for RCM
When established correctly, RCM helps companies establish and enhance system-wide insight of your asset lifecycle as well as an unmatched understanding of how maintenance and operations work together for integration. Successful companies seeking to improve your asset performance, reduce costs, and enhance capacities turn to mWorkOrder, Innovapptive’s SAP-certified mobile work order management solution to leverage the latest in mobile technologies with your SAP® Plant Maintenance (PM) implementation. This turns your EAM system into a source of great business efficiency.
Key Benefits include
- Increased Efficiency – enhanced compliance activities, reduced business interruptions, increase asset utilization, and increase uptime while reducing unplanned downtime and maintenance backlog.
- Reduced Costs – manage lifecycle costs, optimize maintenance and inspection intervals, prevent unexpected events, make data-driven decisions, improve first-time resolution rates.
- Improved Productivity – optimize assets, extend and improve asset life and reliability, reduce operating costs, improve sustainable reliability, improve customer satisfaction.
To experience Innovapptive’s mWorkOrder for yourself, select the “Request Live Demo” button. You can also speak with an Innovapptive Solution Expert via phone at (713)275-1804 or via email at sales@innovapptive.com.
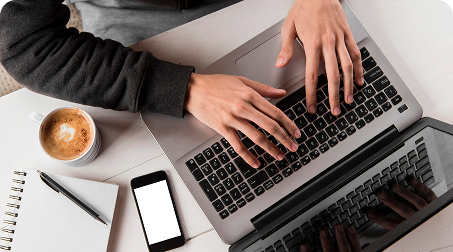
See It In Action
Schedule a personalized demo to see how our solutions can help your business thrive.
- 22-04-2025
The $3.6B Unlock: Solving the Chemical Industry’s Labor Crisis and EBITDA Pressure in One Move
“Constraints don’t slow innovation—they force it.”
- 21-04-2025
Chemical Industry's Margin Erosion: A Wake-Up Call for Operational Efficiency Amid China's Oversupply
The global chemical industry is facing mounting challenges, with revenue declines and shrinking...
- 21-04-2025
Why Wrench Time Isn’t Improving: The Hidden Costs of Traditional Maintenance Scheduling
For years, industrial leaders have relied on a common but flawed assumption: "Better planning and...