Looking Ahead: 3 Challenges Facing the Oil and Gas Industry in 2022 (and How Connected Worker Platforms Solve These Challenges)
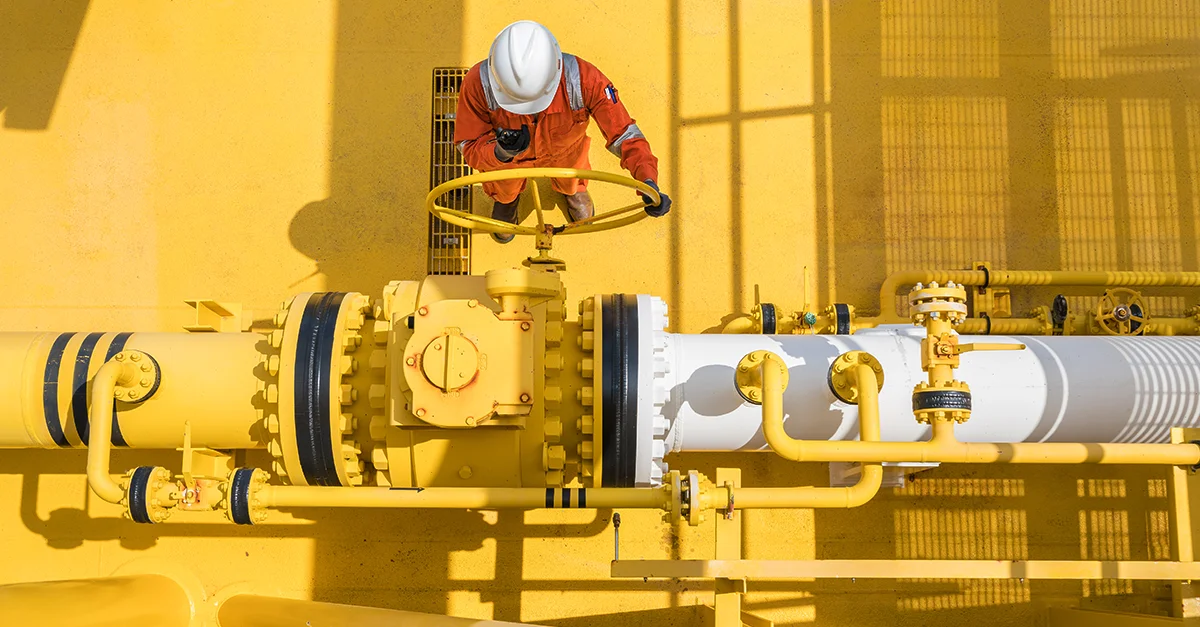
The oil and gas industry faces several unique operational challenges that manual data collection and sharing systems don’t help. Digital transformation technologies like connected worker platforms empower frontline workers, streamline workflows, and improve decision making.
Though digital transformation in the industry has been happening at a rapid pace, by not utilizing connected worker technologies, it's struggling with three major challenges:
- Minimizing operating costs
- Regulatory compliance
- Occupational safety
Let’s drill down into these challenges and see how connected worker solutions can help the industry thrive in 2022.
Challenge 1: Minimize Operating Costs
Crude oil prices are volatile. Companies can’t influence external factors such as geopolitics. However, they have control over internal operational functions like maintenance and inventory management to optimize costs and stay competitive.
Maintenance:
Maintenance is critical for an asset-intensive industry like oil and gas. An unplanned shutdown of an onshore facility can cost an operator $7 million dollars per day. Oil and gas companies should move from reactive maintenance to predictive maintenance strategies to boost equipment reliability and prevent unexpected failures. This will save millions of dollars.
Inventory Management:
Inventory management in offshore facilities should be aligned with maintenance management. Inventory carrying costs at such facilities is higher than usual, and unavailability of MRO spare parts can bring the production to a grinding halt. Oil and gas companies should maintain optimal inventory levels to minimize operating costs. Having knowledge of maintenance schedules and asset health information helps this cause.
Labor Shortage:
The oil and gas industry is also facing a labor shortage post the COVID-19 pandemic. This is adding to the widening skills gap created by the Great Crew Change and increasing labor costs. Oil and gas companies should focus on boosting technician productivity while maintaining operational efficiency.
Challenge 2: Regulatory Concerns
The oil and gas industry is highly monitored as it has a direct impact on the environment. Studies show that offshore rigs are releasing more greenhouse gases than expected. This is raising concerns among governments and regulatory agencies. They are imposing stricter rules and hefty fines.
SOPs and Waste Management:
Oil and gas companies should follow standard operating procedures (SOPs) for natural resource consumption and waste management. For example, water is a critical resource for extraction of oil and gas. Companies should follow a robust mechanism right from water acquisition, storage, and treatment to disposal after use. Their maintenance strategies should incorporate ways to detect leaks before they release hazardous products into the environment.
Safety Manuals and Checklists:
Oil and gas companies should provide updated manuals and safety checklists to their maintenance technicians. As the technicians gain tribal knowledge about the equipment and processes, it should be captured, preserved, and served for future reference.
Challenge 3: Occupational Safety
The oil and gas industry is notorious for safety incidents as it deals with heavy equipment and hazardous materials. According to the CDC, the fatality rate for the oil and gas industry is seven times higher than other industries. Most safety incidents in the oil and gas industry are due to equipment failures and leaks.
Training and Expertise Gap:
Young, inexperienced technicians are entering the oil and gas industry. They need expert training and guidance to perform their jobs efficiently. However, the Great Crew Change has induced a critical skills gap. Companies must find a way to offer real-time, visual support to the technicians. The crew should be aware of the best practices and be able to make informed decisions on the field without waiting for commands from the control room when they come across an issue.
How Connected Worker Platforms Solve These Challenges
Minimizing operating costs, regulatory compliance, and occupational safety - these three challenges stem from one problem: data silos in the oil and gas industry. The industry has been evolving technologically. They use ERP systems like SAP and EAM systems like IBM Maximo. However, these systems don’t include frontline technicians, who play a key role in operations.
Breaking Data Barriers:
Technicians visit the control room and carry paper binders for any information they require to perform a job. They hand over documentation to have data uploaded into the back-office ERP and EAM systems. Managers and top decision-makers only receive updates from the field after the back-office systems are updated. If any human error occurs, inaccurate data leads to wrong decisions.
Empowering the Frontline Workforce:
In 2022, this frontline workforce largely contains millennials and Gen Zers, who grew up with technology around them. They expect to use digital technologies in their jobs, even when working in a non-technical environment. Connected worker platforms bring the power of back-office systems to these frontline workers and empower them through mobile technology. Mobile maintenance management solutions and mobile inventory management solutions break data barriers and information silos in the industrial environment.
Learn More About Connected Worker Platforms
Innovapptive offers a best-in-class Connected Worker platform to help oil and gas companies advance their digital transformation maneuvers. You can request a live demo of our Connected Worker platform or call 844-464-6668 to talk to our experts.
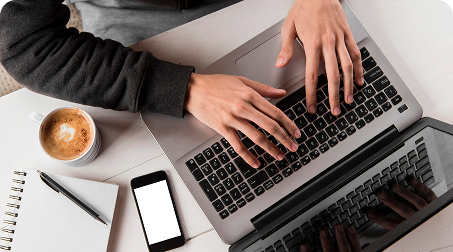
See It In Action
Schedule a personalized demo to see how our solutions can help your business thrive.
- 20-08-2025
Building the future of Industrial Operations with Innovapptive and AWS
Most manufacturers have already gone digital. Yet business outcomes haven’t moved in step. Many...
- 22-04-2025
The $3.6B Unlock: Solving the Chemical Industry’s Labor Crisis and EBITDA Pressure in One Move
“Constraints don’t slow innovation—they force it.”
- 21-04-2025
Chemical Industry's Margin Erosion: A Wake-Up Call for Operational Efficiency Amid China's Oversupply
The global chemical industry is facing mounting challenges, with revenue declines and shrinking...