Manual Data Reporting Robs IBM Maximo Asset Management Users of Needed Efficiency
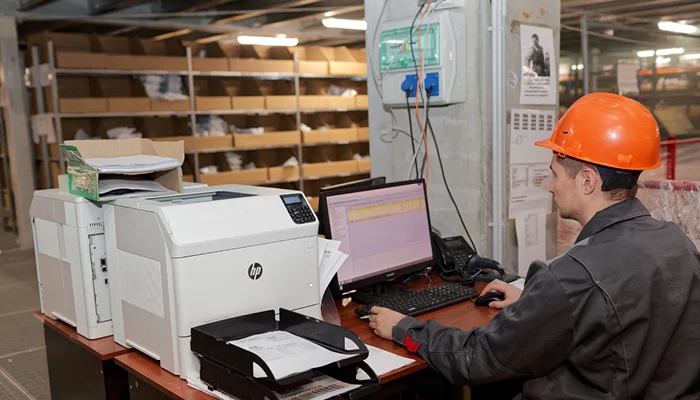
The IBM Maximo asset management system revolutionized the industrial plant back office when it debuted. It still offers a wide range of benefits years after it first hit the market. Some users, however, aren't taking advantage of IBM Maximo's full potential. How? They're using the system in tandem with a paper-based, manual maintenance reporting process. That is causing these users lots of problems.
Paper-based maintenance reporting and uploading robs IBM Maximo Asset Management users of the system’s full productivity benefits. Discover how integrating a mobile maintenance solution with Maximo delivers greater operational visibility, flexibility and agility.
Paper and IBM Maximo No Longer Mix
Using paper forms and checklists worked well enough at the turn of the millennium. After all, that's pretty much all that existed as far as operational data collection and sharing methods went. That's no longer the case two decades into the 21st century. Advancing technology and digital transformation are rapidly altering the landscape of asset-intensive companies, such as industrial plants and manufacturing facilities.
Unfortunately, most IBM Maximo users still rely on the same paper forms and manual data entry processes they employed in 2001. Paper-based maintenance reporting today causes many avoidable problems. Let's look at just a few of the bigger ones:
- Poor visibility into plant operations
- Lag time between data recording and when it reaches decision makers
- Data inaccuracy, such as transcription or typographical errors
- Data loss, including incomplete data or inconsistent capture
- Faulty recordkeeping
- Long hours wasted by workers on computers at the office entering data
- Less time out in the field addressing maintenance issues
If you’re an IBM Maximo asset management user, do these problems sound familiar?
Paper-based Reporting Systems Stifle Technician Productivity
As a maintenance manager or supervisor, you'd love to get eight solid hours of wrench time per shift from each member of your team of technicians. That's not very likely, even on the best day. It's impossible using a manual data collection and sharing system.
A paper-based process makes it much harder for technicians to access important information such as equipment specifications, operating manuals, standard operating procedures, work instructions, work orders, inventory, etc. They're stored in binders or in a filing cabinet. Lots of things can happen to paper records, most of them bad. They can:
- Be misfiled
- Be misplaced
- Be in use by someone else
- Get lost
- Be destroyed
These factors often mean frontline maintenance workers spend more time finding paper-based information than turning a wrench. If this is happening at your plant, you're not alone.
According to The Anatomy of Work Index, people spend about 60% of their workday on such unproductive tasks as:
- Playing tag with colleagues for input
- Waiting for feedback and approvals
- Searching for files and documents
- Duplicating efforts
These tasks can cost a company as many as 19 working days per year for just one employee. Wouldn’t you rather have 19 working days of wrench time?
They Also Hinder Operational Visibility
Decision makers at plants using a paper-based maintenance reporting system in tandem with IBM Maximo suffer impaired vision into the real-time operational status of their facility. The reason why is simple.
Frontline workers must manually enter all the data they gathered during their shift into IBM Maximo. It's a laborious, time-consuming process. Maintenance technicians need to know how to maintain and repair machinery, not be typists. Having a technician type in data introduces the chance of error. It also takes them away from their primary task, reducing wrench time.
Hiring someone else to enter the data also increases the risks of inaccuracy. Deciphering handwriting is a difficult chore. Having a dedicated person to enter information increases administrative costs.
Finally, a paper-based reporting system delays critical operation information from reaching decision makers for review and prompt action. This delay opens a spectrum of pain points, all of which a reactive, run-to-fail maintenance program aggravates. These include:
- More unplanned downtime
- Longer production outages
- Greater labor inefficiency
- Less equipment reliability
- Shorter asset life
- Additional safety risks
- Higher maintenance costs
If your plant or facility is experiencing such problems, you’re likely wondering if there’s a better way.
More Efficient IBM Maximo Maintenance Reporting Through Mobile
Innovapptive, a connected worker solution pioneer, specializes in mobile plant maintenance systems that integrate seamlessly with IBM Maximo. Unlike inefficient paper-based manual processes, these solutions improve data accuracy, transform reactive processes, increase technician productivity, cut downtime and raise safety and regulatory compliance. They’ll enable your organization to realize IBM Maximo's potential. Schedule a free demo of a world-class mobile solution today, or call 888-464-6668 to speak to one of our industry experts.
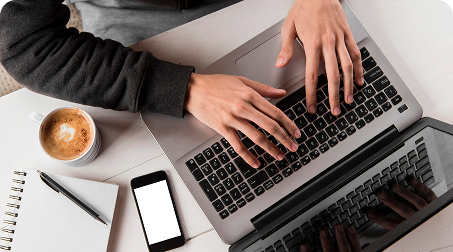
See It In Action
Schedule a personalized demo to see how our solutions can help your business thrive.
- 20-08-2025
Building the future of Industrial Operations with Innovapptive and AWS
Most manufacturers have already gone digital. Yet business outcomes haven’t moved in step. Many...
- 22-04-2025
The $3.6B Unlock: Solving the Chemical Industry’s Labor Crisis and EBITDA Pressure in One Move
“Constraints don’t slow innovation—they force it.”
- 21-04-2025
Chemical Industry's Margin Erosion: A Wake-Up Call for Operational Efficiency Amid China's Oversupply
The global chemical industry is facing mounting challenges, with revenue declines and shrinking...