Stop Hindering Your IBM Maximo Asset Management System with Manual, Paper-based Reporting
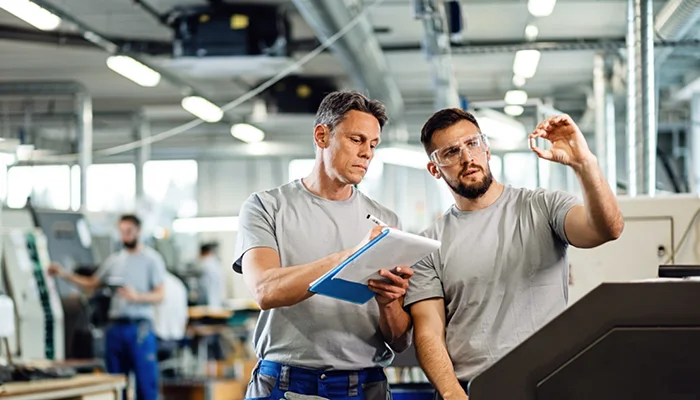
Using a paper-based maintenance reporting system alongside your IBM Maximo asset management system is creating inefficiencies, increasing downtime, and hindering productivity. If maintenance technicians are still manually entering data into IBM Maximo, valuable time is being wasted that could be used for proactive maintenance and work order management.
Challenges of Paper-Based Maintenance Reporting
Reliance on manual data entry and paper checklists comes with several operational drawbacks:
-
Limited Operational Visibility – Decision-makers receive outdated information, leading to delayed responses.
-
Rigid Data Collection & Sharing – Paper forms cannot adapt to evolving maintenance needs or regulatory requirements.
-
Multiple Information Silos – Lack of digital integration restricts cross-team collaboration and access to critical asset management data.
-
Reduced Wrench Time – Technicians spend more time on paperwork than performing actual preventive maintenance rounds.
-
Increased Maintenance Backlogs – Slow data entry and lack of real-time operator data tracking create growing backlogs.
-
Higher Equipment Downtime – Delayed maintenance due to inefficient reporting processes leads to costly machine failures and increased mean time between failures (MTBF).
IBM Maximo's Capabilities and Its Limitations
The IBM Maximo asset management system is a powerful tool for asset lifecycle management, predictive maintenance, and work order tracking. However, its efficiency is hindered by manual reporting processes. Maintenance teams that still rely on paper-based data collection fail to fully leverage IBM Maximo’s capabilities in optimizing equipment reliability and reducing downtime.
Enhancing IBM Maximo with Mobile Workforce & Connected Worker Solutions
Mobile workforce management solutions and connected worker platforms bridge the gap between field operations and enterprise asset management systems like IBM Maximo. By digitizing work order tracking, equipment condition monitoring, and asset performance management, organizations can improve operational efficiency and real-time visibility.
Key Benefits of Digital and Mobile Integration with IBM Maximo
1. Real-Time Operational Visibility
-
Access live maintenance status updates from any device using mobile enterprise asset management.
-
Ensure compliance tracking and meet regulatory standards with electronic logbooks.
-
Enable IBM Maximo field service management teams to make data-driven decisions instantly.
2. Automated Work Order Management
-
Digitally generate, assign, and track work orders using work order management software.
-
Reduce maintenance backlog with automated work order routing.
-
Improve work order completion rates with instant task management for operators.
3. Increased Technician Productivity
-
Minimize manual data entry errors by integrating IBM Maximo mobile work order solutions.
-
Improve asset uptime with mobile-driven preventive maintenance planning.
-
Streamline shift turnover processes and optimize operator efficiency tools.
4. Predictive Maintenance & Data-Driven Insights
-
Enable condition-based maintenance software with IBM Maximo asset intelligence.
-
Use historical maintenance data to forecast potential failures and increase mean time between failures.
-
Reduce unexpected equipment breakdowns and unplanned downtime.
5. Seamless Integration with ERP & Asset Management Systems
-
Sync IBM Maximo asset management with SAP asset management and other enterprise systems.
-
Standardize maintenance workflows across different locations using digital work instructions.
-
Enhance inventory management and spare parts tracking for field teams with work order automation.
From Reactive to Proactive: The Digital Transformation of Maintenance
By integrating mobile workforce management solutions, connected worker technology, and real-time repair tracking, maintenance operations shift from reactive maintenance to a predictive and proactive maintenance model. Field technicians can access customizable rounds checklists, update work orders online, and receive instant notifications for urgent maintenance tasks.
Get More from Your IBM Maximo System with Innovapptive
Innovapptive specializes in mobile workforce management, helping companies achieve:
-
Improved asset reliability with predictive maintenance solutions.
-
Optimized work order execution using reliability-centered maintenance.
-
Faster decision-making through real-time equipment monitoring.
Schedule a Free Demo Today
Maximize the potential of IBM Maximo by eliminating manual reporting inefficiencies. Schedule a free demo or call 888-464-6668 to explore how Innovapptive’s mobile work order management solution can transform your maintenance operations.
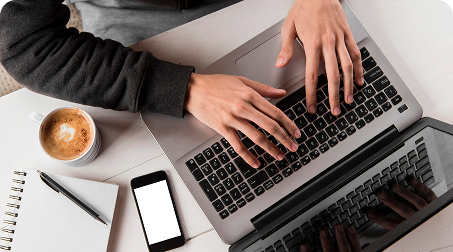
See It In Action
Schedule a personalized demo to see how our solutions can help your business thrive.
- 22-04-2025
The $3.6B Unlock: Solving the Chemical Industry’s Labor Crisis and EBITDA Pressure in One Move
“Constraints don’t slow innovation—they force it.”
- 21-04-2025
Chemical Industry's Margin Erosion: A Wake-Up Call for Operational Efficiency Amid China's Oversupply
The global chemical industry is facing mounting challenges, with revenue declines and shrinking...
- 21-04-2025
Why Wrench Time Isn’t Improving: The Hidden Costs of Traditional Maintenance Scheduling
For years, industrial leaders have relied on a common but flawed assumption: "Better planning and...