Maximizing Value from Integrated Mobile Maintenance Rounds
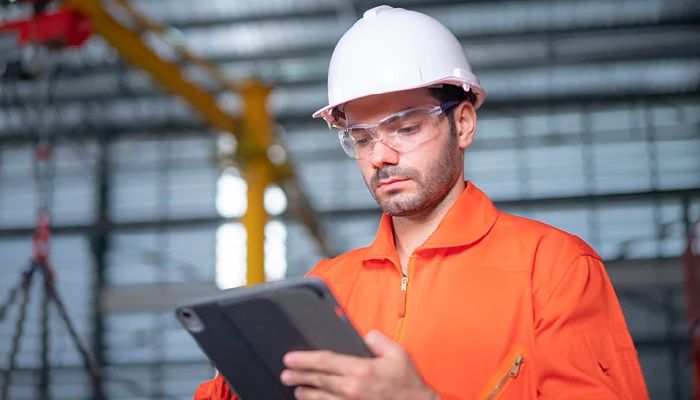
Maintenance rounds (also often called operator rounds) are critical to improving plant performance and achieving business goals without unplanned interruption. In today’s dynamic business environment, where agility and flexibility are of increasing importance, businesses must find ways to operate in more efficient, more cost-effective ways. Organizations, especially those having enterprise assets or equipment, require plant checks or maintenance rounds to monitor asset health and detect technical issues, damages, or other failures. Transitioning from manual inspections to mobile maintenance rounds offers big advantages in driving greater efficiency, equipment uptime, and safety.
Problems in the Maintenance Rounds Process
Inspections usually involve a technician or operator touring the unit or plant with a preprinted manual checklist to fill out and turn in to a supervisor at the end of the round. Most industrial facilities assign rounds to a more experienced operator who is familiar with the plant and its policies and procedures. Sometimes, however, in industries with high turnover, a less experienced employee may be tasked with completing the rounds, opening the door to potential errors.
Companies are also being required to do more in less time, which may result in a harried operator or technician rushing through the rounds or not completing each section. This leads to potentially critical issues being overlooked or missed, undermining the entire process.
The checklist itself can sometimes pose a problem. Perhaps it’s not well thought out, poorly organized, confusing, or omits important data points. There could be delays in the review and approval process due to a lack of information/data.
Solving Problems with Mobile Maintenance Rounds
Plant managers want faster and better operational information to assess risk and prevent downtime. While nearly three-quarters of plants recently surveyed said zero downtime was a top priority, 70% also reported they had no idea when their equipment was due for maintenance or upgrades.* A digital operator round solution can change this.
Mobile maintenance rounds replace error-prone manual checklists with an efficient electronic process utilizing mobile handheld devices. Technicians access digital forms on their devices to conduct inspection rounds. These dynamic digital forms can be quickly and easily changed on the fly to better meet an industrial facility’s situational needs.
Technicians scan equipment barcodes and complete the digital form by checking customized data fields to document operational status and safety conditions. The inspector can’t advance to the next piece of equipment or location until all fields for the current step are completed as a safeguard.
The solution immediately uploads collected data electronically into the back-office system. Decision makers can view inspection data in real-time via their mobile device or desktop application and communicate with the technician during the round.
Supervisors, managers, and directors have immediate access to mission-critical information via handy mobile devices or desktop apps. This means they can respond quickly to trends and problems, enabling them to solve maintenance issues before they result in lost production, or worse, shutdowns.
Leadership can make more informed decisions based on field-verified facts rather than experience or intuition. With fast and accurate data, labor and resources can be deployed more effectively, reducing duplication of effort and waste.
Finally, with immediate access to key information, technicians can fix the problem the first time, cutting inefficient and time-consuming reworks.
Integration with ERP Systems
The integration of digital operator rounds with ERP systems empowers operators with quick access to key data and support. Other features, including uploading multimedia and annotations on images and documents, help companies capture the tribal knowledge of their operators. Data is uploaded into your ERP system in real-time, enabling you to pass it on to other operators. This prevents the loss of tribal knowledge when an experienced technician retires.
For example, a senior operator might recommend checking the filters of a motor frequently during summer. He knows from years of experience that the motor will accumulate more dust as a bay door is kept open for air and it brings in more dust during the summer months. A new operator is less likely to know this is important until the senior operator adds it to the operator round.
Integration with Work Order Management Software
Critical equipment failures need to be addressed immediately to avoid grave dangers to the workforce and company. When a digital operator rounds solution is integrated with a work order management software, it triggers work orders as soon as a critical issue is identified during a round. This helps companies prevent safety incidents and unexpected shutdowns.
If the solution is also integrated with mobile work instructions, it offers real-time, visual guidance to field technicians from experts while performing rounds. This expedites rounds and saves time while enhancing efficiency.
Maximizing Value from Integrated Mobile Maintenance Rounds
To learn more about one such leading-edge solution,watch this video. You can also schedule a free demo or call 844-464-6668 to speak to one of our experts.
* Source: Vanson Bourne
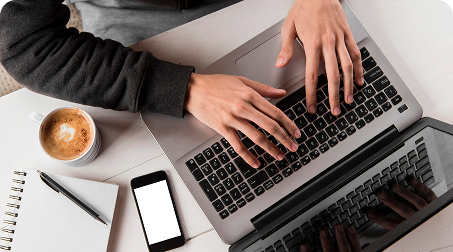
See It In Action
Schedule a personalized demo to see how our solutions can help your business thrive.
- 20-08-2025
Building the future of Industrial Operations with Innovapptive and AWS
Most manufacturers have already gone digital. Yet business outcomes haven’t moved in step. Many...
- 22-04-2025
The $3.6B Unlock: Solving the Chemical Industry’s Labor Crisis and EBITDA Pressure in One Move
“Constraints don’t slow innovation—they force it.”
- 21-04-2025
Chemical Industry's Margin Erosion: A Wake-Up Call for Operational Efficiency Amid China's Oversupply
The global chemical industry is facing mounting challenges, with revenue declines and shrinking...