5 Ways Digital Operator Rounds are Revolutionizing Plant Maintenance and Safety in 2024
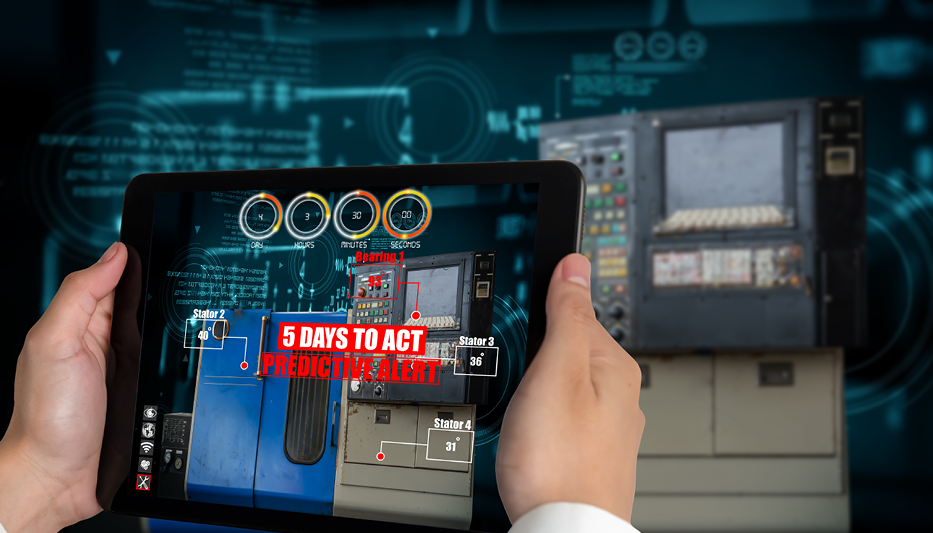
Imagine a seasoned operator meticulously fills out a paper checklist during their daily rounds, carefully noting equipment readings and observations. This process, while seemingly efficient, is riddled with hidden inefficiencies. Studies show that manual data entry consumes a significant amount of an inspector's time, and paper forms are prone to errors and inconsistencies, leading to inaccurate data and missed problems. Additionally, collating and analyzing data from paper forms is a time-consuming and error-prone task, hindering timely decision-making.
What Are Digital Operator Rounds?
Innovapptive’s Digital Operator Rounds replace error-prone paper checklists with an efficient electronic rounds process utilizing mobile handheld devices (smartphones, tablets, barcode scanners, etc.). Technicians access digital forms on their devices to conduct the inspection rounds. Users can quickly and easily change these dynamic digital forms on the fly to better meet a plant’s situational needs.
Technicians scan equipment barcodes and complete the digital form by checking customized data fields to document present operational status and safety conditions. The inspector can’t advance to the next piece of equipment or location until all fields for the current step are completed as a safeguard (something not present in a paper-based system). Collected data is immediately uploaded electronically into the back-office system. Decision-makers can view inspection data in real time via their mobile device or desktop application and communicate with the technician during the round.
Case For Digital Operator Rounds
More than two out of every three plants recently surveyed revealed they had no idea when their equipment was due for routine maintenance or important upgrades. It’s no surprise then that 82% of industrial plants have suffered at least one unplanned shutdownin the last three years. Such downtime can run up to $250,000 an hour, and at an average of four hours per shutdown, those costs add up quickly, squeezing already tight profit margins.
Source: Aberdeen Research
On the safety front, industrial plants reported 5,333 workplace deaths and 2.8 million non-fatal injuries in 2019 (the most recent figures available). Most industrial accidents occur due to slips and falls or contact with objects and equipment. Plants are constantly looking for ways to minimize safety risks and the resulting lost work time, fines and penalties.
Digital operator rounds offer a game-changing solution that helps businesses ditch outdated methods and completely transform plant maintenance and safety. By harnessing the power of mobile technology, digital operator rounds makes inspections faster and more streamlined, improves the accuracy of collected data, and fosters real-time understanding – all of this while increasing production uptime, strengthening safety measures, and giving your workforce the tools they need to succeed.
The Benefits of Digital Operator Rounds
Digital operator rounds offer a multitude of benefits that appeal to both bottom-line and management stakeholders in any industrial setting:
1. Reduce Unplanned Downtime and Boost Uptime
Unplanned downtime can devastate plant productivity. Innovapptive’s digital operator rounds support predictive maintenance and help operators detect potential issues early by:
- Facilitating thorough inspections: Digital forms ensure consistent equipment evaluations, reducing the risk of missed problems.
- Supporting real-time data collection: Data flows automatically to a central system, offering insights into equipment health.
- Enabling proactive maintenance schedules: Use data insights to create effective, data-driven maintenance schedules.
- Resource optimization: Allocate resources effectively based on real-time equipment status, maximizing productivity.
2. Improve Compliance and Safety Risk Mitigation
Compliance with safety regulations is essential for industrial operations. Innovapptive’s digital operator rounds provide a structured, reliable approach to maintaining safety standards and reducing risk by:
- Standardizing inspections: Digital checklists ensure each inspection is completed accurately, reducing human error.
- Empowering hazard reporting: Operators can instantly report hazards with detailed notes and images, ensuring rapid responses.
- Data-driven safety insights: Collected data helps identify recurring safety issues, enabling targeted improvements and safer environments.
3. Increase Operational Efficiency and Cost Reduction
Paper-based processes are time-consuming and costly. Digital operator rounds reduce administrative overhead by:
- Eliminating manual data entry: Mobile data capture minimizes errors and speeds up inspections.
- Lowering administrative costs: Digitized forms reduce paper-related costs, and automated data processing lessens the need for data entry staff.
- Streamlining workflows: Real-time access to data optimizes resource utilization and decision-making, reducing overall operational costs.
4. Improve Data Quality and Real-Time Visibility
Effective decision-making depends on accurate, consistent data. Digital operator rounds enhance data quality and visibility by:
- Standardizing data collection: Consistent digital forms reduce errors and ensure high-quality data.
- Automating data entry: Digital capture minimizes human error and boosts data integrity.
- Real-time insights: Decision-makers can access real-time data for faster responses to emerging issues, ensuring informed, proactive maintenance.
5. Empower Frontline Workers and Enhance Engagement
Engaged workers drive productivity and efficiency. Innovapptive’s digital operator rounds empower frontline workers by:
- Providing intuitive mobile apps: Easy-to-use apps streamline data collection, allowing operators to focus on key tasks.
- Supporting continuous learning: Operators access manuals and training materials directly on their mobile devices, promoting skill development.
- Enhancing job satisfaction: Eliminating paperwork and providing easy access to information improves morale and productivity.
Beyond the Numbers: The Human Impact of Digital Operator Rounds
While the quantifiable benefits of mobile operator rounds are undeniable, its impact extends far beyond mere numbers. By bridging the gap between operation excellence programs and maintenance activities, digital operator rounds foster improved communication and collaboration between teams. This breakdown of technology/information silos empowers operators like Sarah and Mike to proactively engage with maintenance by seamlessly reporting issues through the digital operator rounds solution. This timely communication allows maintenance personnel to address problems quickly and efficiently, minimizing production downtime and ensuring safe and smooth production.
Furthermore, digital operator rounds contribute to a more positive and engaging work environment for frontline workers. By eliminating the tedium of paper-based inspections and providing access to readily available information, it empowers operators and fosters a sense of ownership over their work. This, in turn, leads to increased job satisfaction, improved morale, and ultimately, a more productive workforce.
Ready To Experience The Power of Digital Operator Rounds?
Schedule a free demo with Innovapptive today and discover how our cutting-edge solutions can help propel your plant towards increased efficiency, improved safety, and sustained success. Additionally, consider a discovery meeting with our team of experts to gain a deeper understanding of how digital operator rounds can be customized to meet your specific needs.
Don't wait – take the first step towards a more efficient and safer future for your plant!
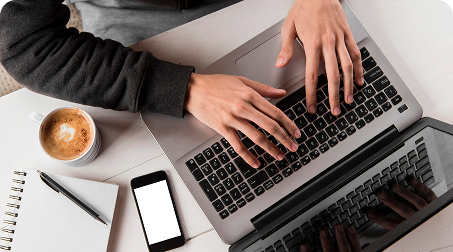
See It In Action
Schedule a personalized demo to see how our solutions can help your business thrive.
- 20-08-2025
Building the future of Industrial Operations with Innovapptive and AWS
Most manufacturers have already gone digital. Yet business outcomes haven’t moved in step. Many...
- 22-04-2025
The $3.6B Unlock: Solving the Chemical Industry’s Labor Crisis and EBITDA Pressure in One Move
“Constraints don’t slow innovation—they force it.”
- 21-04-2025
Chemical Industry's Margin Erosion: A Wake-Up Call for Operational Efficiency Amid China's Oversupply
The global chemical industry is facing mounting challenges, with revenue declines and shrinking...