Mining Operations: Unearth Hidden Profits with Connected Worker Solutions
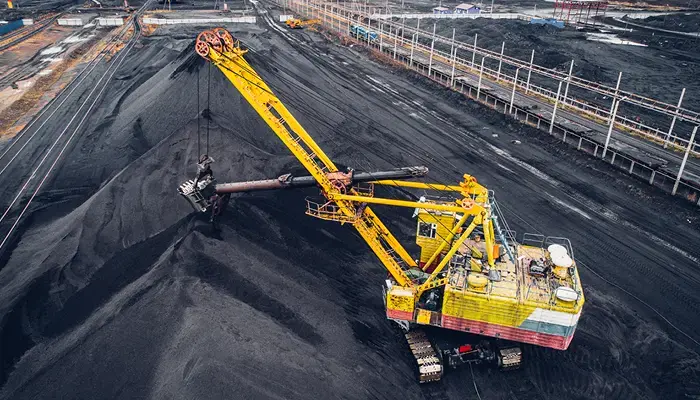
Are $15 Billion of Lost Profits Picking Your Pocket?
The mining industry thrives on efficiency. Every hour of operation translates to valuable resources extracted, processed, and delivered. But a silent thief lurks beneath the surface – unplanned downtime. Industry estimates place the annual cost of this hidden enemy at a staggering $15 billion (GlobalData). That's enough to buy a fleet of the world's largest dump trucks – the Belaz 75710, capable of hauling a mind-blowing 450 tons of material (BelAZ)! This downtime is hemorrhaging your bottom line.
Let's Start with Math: The ROI of Reducing Unplanned Downtime
Say your mine operates 24/7 and produces 100 tons of valuable ore per hour. Now, consider a single, 8-hour downtime incident. Here's the cost breakdown:
- Lost Production: 8 hours x 100 tons/hour = 800 tons of ore
- Lost Revenue: 800 tons x $50/ton = $40,000
But that's just one incident! Industry averages suggest eight unplanned downtime events per year (McKinsey & Company). Suddenly, the financial hemorrhage becomes a full-blown crisis, potentially costing $320,000 annually.
The Potential Savings: What If You Could Save 20%?
Now, imagine if you could reduce unplanned downtime by just 20%. Here's how the numbers change:
- Reduced Downtime: 8 hours x 20% = 1.6 hours saved per incident
- New Downtime Duration: 8 hours - 1.6 hours = 6.4 hours per incident
- Saved Production: 1.6 hours x 100 tons/hour = 160 tons of ore per incident
- Saved Revenue per Incident: 160 tons x $50/ton = $8,000
With 8 downtime events per year, the annual savings could be significant:
- Annual Saved Revenue: 8 incidents x $8,000 = $64,000
Beyond Finance: The Impact of Unplanned Downtime
The impact goes beyond lost revenue. Downtime can also lead to:
- Increased maintenance costs: Rushing to fix breakdowns is like using duct tape to mend a leaking pipe – a temporary solution that costs more in the long run.
- Safety risks: Downtime pressure can lead to rushed restarts, compromising safety protocols and potentially causing accidents.
- Customer dissatisfaction: Delays due to downtime leave customers hanging, impacting relationships and future business.
Optimize Machine Idle Time: Let's Talk Numbers
Even beyond unplanned downtime, there are inefficiencies that cost money. An idling time of 1,000 hours (for 27 machines) can cost mining companies up to $1.28 million each year. While idling or waiting time cannot be completely avoided, running non-productive machines still incurs high operational costs and adds to emissions (International Mining). Innovapptive optimizes machine idle time through precise wrench time calculations and planning via our unique control center-based planning tool. This ensures that every machine's time is utilized efficiently, reducing idle time and operational costs.
Real-World Incident: The Need For Predictive Maintenance
Imagine this: a critical piece of machinery malfunctions, grinding your entire operation to a halt. Technicians scramble to diagnose the issue, leading to delays in repairs, lost production, and a domino effect on safety and customer satisfaction. Now, envision if this issue was identified earlier using our AI-powered computer vision and incident management tools. The problem could have been detected and addressed proactively, avoiding the breakdown and keeping the operation running smoothly. This not only saves time and money but also boosts worker morale and safety.
Supercharge Your Profits With Connected Worker Platform
Innovapptive isn't just another software company; we're a game-changer for the mining industry. Our cloud-based Connected Worker Platform goes beyond traditional solutions, empowering your workforce and optimizing operations. Here's how we redefine your frontline:
- AI-Powered Mobile-First Approach: Imagine a digital toolbox accessible anywhere on-site, online, or offline. Innovapptive prioritizes user-friendly mobile apps for operations, maintenance, and inventory management, ensuring critical information is readily available in the palm of your workers' hands in the mine.
- Unified Platform: Break down departmental silos. The platform centralizes everything where all teams – operations, maintenance, and warehouse teams – work together with a unified view of data and tasks. This eliminates communication gaps and fosters collaboration..
- Seamless ERP Integration: Effortlessly integrate Innovapptive with your existing ERP systems, streamlining work order management and data flow. ERPs like SAP are not easy to handle, but it's important that they reflect the latest data – right data = right money, a leading indicator to better reliability numbers and profit.
- AI/ML-Powered Solutions: Harness the power of artificial intelligence for predictive maintenance, computer vision-based issue identification, and risk-based priority determination. Our AI acts like a futuristic prospector, sniffing out potential problems before they snowball into major breakdowns.
- Real-Time Collaboration: Dashboards, chat, and skill management functions help to upskill mine workers and ensure seamless communication between your team members, regardless of location. Built-in chat features enable immediate problem-solving, preventing delays caused by miscommunication.
- Automated Shift Handovers: Eliminate the risk of missed information during shift changes with automated handover reports and acknowledgments. This ensures a smooth transition of knowledge and tasks.
- Optimized Downtime Management: Our platform significantly reduces unplanned downtime by enabling proactive maintenance and immediate incident resolution. This leads to better MTTR, MTBF, and overall operational efficiency. Value dashboards help supervisors to track, tune, and act on missed actions.
- Enhanced Safety and Compliance: Innovapptive’s tools improve compliance with safety regulations and reduce the likelihood of accidents, fostering a safer work environment.
- Shift Handovers, Operator Rounds, and Approval Workflows: Our best-in-class drag-and-drop configuration engine makes managing these processes a breeze. Users will love the ease of customization.
- Sustainable Operational Efficiency: By optimizing processes and leveraging AI-powered solutions, Innovapptive helps you achieve sustainable success in the competitive mining industry.
Research Findings
Studies by ARC Advisory Group suggest that mining companies implementing Connected Worker solutions can experience a 25% reduction in unplanned downtime and a 35% improvement in compliance with safety regulations (Mining Technology).
In this context, let's revisit our original downtime scenario. With a 25% reduction, that 8-hour downtime shrinks to 6 hours, translating to a saved revenue of:
- Saved Revenue: ($40,000 lost revenue) x (25% reduction) = $10,000
Now, multiply that by the average 8 downtime events per year, and you're looking at a potential annual saving of $80,000. Considering the industry-wide cost of downtime, these figures become even more compelling.
Unlock Your Mining Operations Potential
Downtime is a persistent challenge, but it doesn't have to be a backbreaker for your mining operation. Innovapptive's Connected Worker Platform equips your workforce with the tools and technologies they need to work smarter, not harder. By fostering collaboration, optimizing processes, and leveraging AI-powered solutions, Innovapptive can significantly reduce downtime, improve safety, and unlock hidden profits for your mine.
For more information on how Innovapptive’s solutions can transform your operations, visit our website.
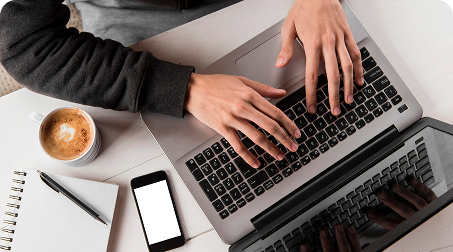
See It In Action
Schedule a personalized demo to see how our solutions can help your business thrive.
- 20-08-2025
Building the future of Industrial Operations with Innovapptive and AWS
Most manufacturers have already gone digital. Yet business outcomes haven’t moved in step. Many...
- 22-04-2025
The $3.6B Unlock: Solving the Chemical Industry’s Labor Crisis and EBITDA Pressure in One Move
“Constraints don’t slow innovation—they force it.”
- 21-04-2025
Chemical Industry's Margin Erosion: A Wake-Up Call for Operational Efficiency Amid China's Oversupply
The global chemical industry is facing mounting challenges, with revenue declines and shrinking...