Mobilizing the utility workforce for operating efficiency
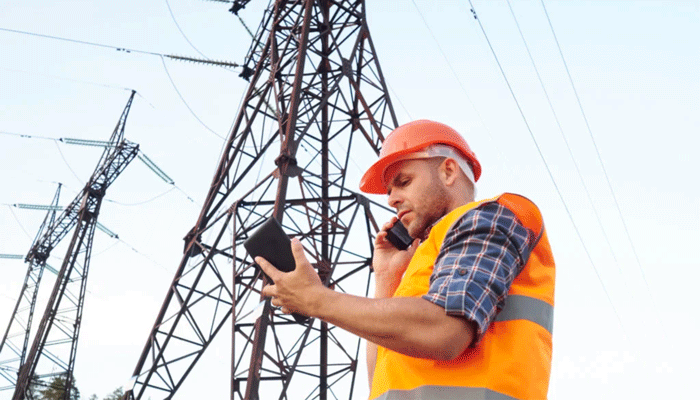
The business world always keeps changing and few industries are undergoing such an extensive shift as the utility and energy sectors. Today most of the utility companies manage their network and customer connections with teams of workers in the field. The delivery of utility services to the customers and businesses involves engaging teams to take inspection, maintenance/service, meter readings and respond to customers’ as well as equipment’s problems. Moreover, changes in consumers’ demand and expectations are enforcing utility companies to modernize and mobilize their traditional approach. However, with competition coming from all corners of the industry, maintaining the position and achieving the company’s vision is being tough. Organizations want to experience the latest innovation and stay ahead of the competitors.
Some common challenges in utility industry:
- Geographically dispersed assets too difficult and labor-intensive to track and maintain.
Mostly, utility companies’ assets and their workforce are distributed. The field workers/technician need to travel to complete their tasks. It is necessary for the back-end administration team to keep the track on their tasks and progress. As a result, the utility company has a pressure to increase their operational efficiency and field work effectiveness.
- Paper-based approach and manual routing of information lead to unnecessary errors, inefficiency, and costs.
A majority of field workers/technician/engineers are always on the move. Traditionally, at the end of a field operation, technicians or workers would prepare handwritten notes or filling out forms, and later re-entering it into the system. They have to spend a considerable amount of time in such activity, which is not only time-insensitive but also prone to errors.
- loss of connectivity hampers field work functions and causes latency.
Providing field services in remote area proves to be daunting and many times vulnerable to failures and data losses. As workers reach in no network area, they have to note down the information somewhere or on a piece of paper and later re-enter it into the system.
- Unavailability of real-time alerts & lack of field automation delays decision-making and process flow.
Lack of real-time alerts and field automation cause delays and engage field workers/technicians to focus on other tasks rather than doing their main tasks. Moreover, field workers/technicians have to resort to collecting and capturing the information manually and later re-entering it into the application.
- Lack of synchronization of field inspection and maintenance work.
Field operators/workers need to perform inspections and maintenance on a frequent basis. This requires a substantial amount of paperwork such as paper forms related to equipment needed for service, checklists for safety measures, guidelines to follow and access to a significant amount of information. Field workers get overwhelmed due to this lengthy process.
The Solution: Need of a consumer grade mobile solution which can tightly integrate with any backend ERP
Mobility is an essential to harness the disruptive technologies in business. One of the main objectives of enabling utility workers with mobile devices is to increase the operational efficiency and their productivity. It gives the ability to transfer information in real-time that enables quick response to critical issues, marinating safety measure as well as the controlling costs. The organization can monitor almost all activities and check individual performance.
Wrench time can significantly be improved with the right mobile solution for the technicians. It allows schedulers/planners to use their mobile devices to create, view and update maintenance plans in real time.
Mobile access to business data can eliminate the mountain of paper from inspection and maintenance functions. The ability to access the information from anywhere, anytime with any device can free up the workers time and efforts. This can be utilized in completing more critical tasks. With mobility supervisor, managers get visibility into the real-time status of all notifications, work orders, as well as they, can better monitor service and productivity levels of individuals. The full potential of the workforce can only be realized when they have enough information to appropriately perform their tasks. The higher ROI can be achieved when companies are able to get the most out of their existing software and hardware. The enterprise-grade mobile solution should easily mingle with their available device. It should empower field workers to use device’s features. For example, by using GIS facility available on the device, field workers locate individual inspection points and find shortest routes with turn by turn navigation. And if mobile devices are equipped with global position system (GPS) technology, so supervisor/managers can easily monitor the real-time physical location of all workers to support dynamic schedule changes throughout the day.
Utility Industry across the world are increasingly turning to mobile to achieve process efficiencies, costs and create customer focus. Companies, which are mobilizing their processes are not only growing faster than their peer companies but also leveraging real-time visibility and driving a better customer engagement. It’s high time for field service sectors for improve the operational efficiency and enhance worker’s productivity by going mobile.
Innovapptive offerings for Utility Industry:
mWorkOrder: The mWorkOrder mobile app for SAP Plant Maintenance (PM) empowers maintenance crews to work more safely, productively, and independently, whether installing new equipment or maintaining, inspecting and repairing existing assets. This SAP® Certified solution leverages the SAP Plant Maintenance (PM) module at the back-end to deliver a consistent, reliable and a productive asset maintenance experience across a wide range of industries. More at www.innovapptive.com/mworkorder
RACE™ Dynamic Forms: RACE™ Dynamic Forms is the solution to help you build robust mobile forms that will revolutionize your field data capture. Whether the objective is to improve productivity, increase visibility into operations, save time and gain data accuracy. RACE™ Dynamic Forms, make your paper forms digital by recreating them as electronic forms accessible through mobiles, tablets and web browsers.
If you would like a demo of Innovapptive’s mWorkOrder(SAP Plant Maintenance) solution, please click on the link. Alternatively, if you would like to discuss with an Innovapptive solution expert, you can reach out to us by emailing us at sales@innovapptive.com or you can reach a sales representative at (713) 275-1804.
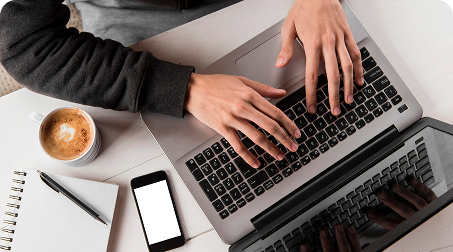
See It In Action
Schedule a personalized demo to see how our solutions can help your business thrive.
- 22-04-2025
The $3.6B Unlock: Solving the Chemical Industry’s Labor Crisis and EBITDA Pressure in One Move
“Constraints don’t slow innovation—they force it.”
- 21-04-2025
Chemical Industry's Margin Erosion: A Wake-Up Call for Operational Efficiency Amid China's Oversupply
The global chemical industry is facing mounting challenges, with revenue declines and shrinking...
- 21-04-2025
Why Wrench Time Isn’t Improving: The Hidden Costs of Traditional Maintenance Scheduling
For years, industrial leaders have relied on a common but flawed assumption: "Better planning and...