Mastering OSHA Incident Reporting for Workplace Safety
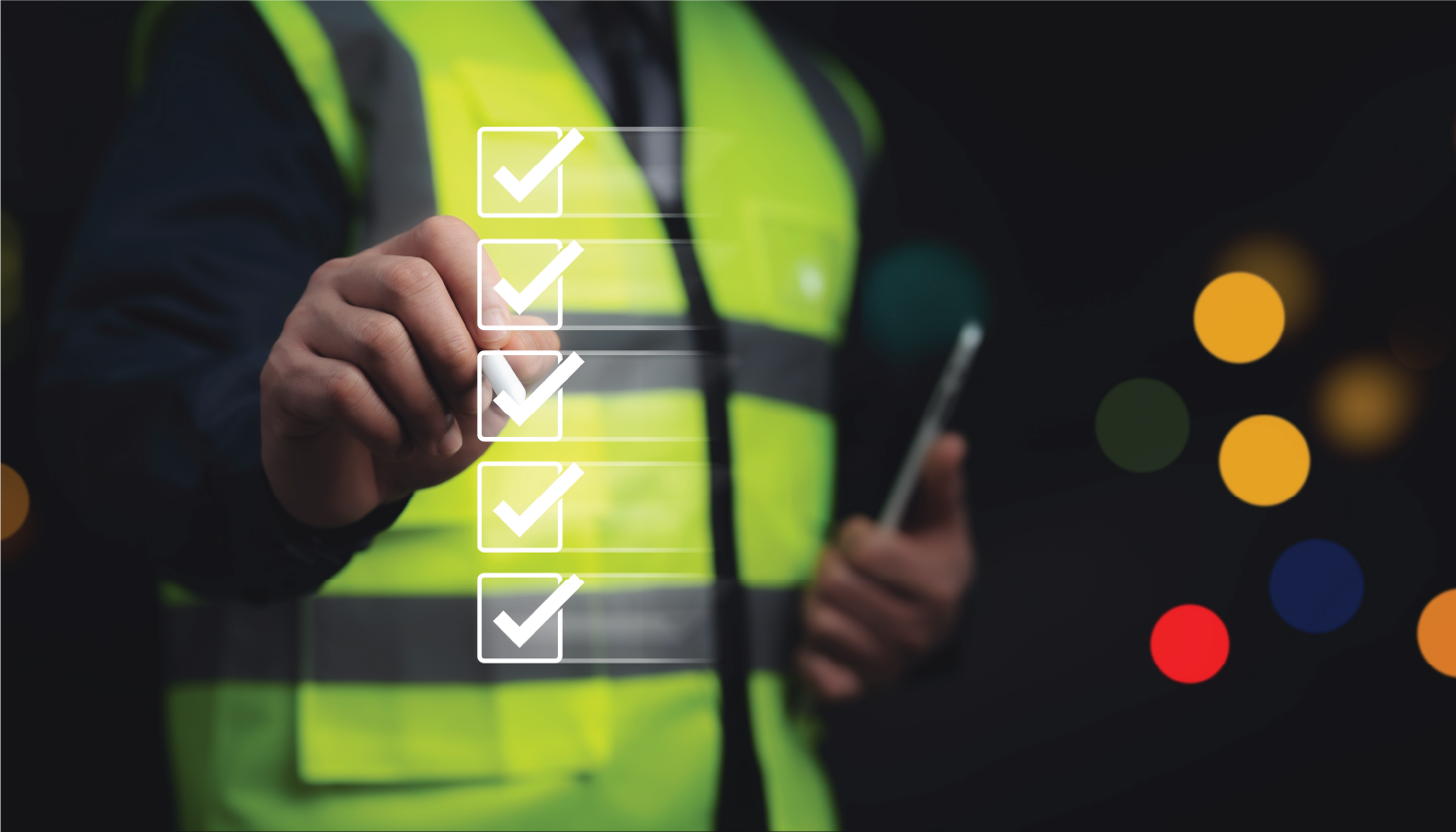
Safety incidents are more than just events—they're valuable opportunities to improve workplace conditions and protect employees. For safety managers, EHS professionals, and operations managers, understanding how to efficiently document and analyze workplace incidents is critical. One key tool in this process is the OSHA Incident Report.
This guide explores everything you need to know about OSHA incident reporting, from its importance to step-by-step reporting instructions. You'll also discover how proper reporting can help identify trends, reduce risk, and prevent future accidents.
What is an OSHA Incident Report?
An OSHA (Occupational Safety and Health Administration) Incident Report is a formal documentation of workplace injuries, illnesses, or fatalities. This report is required under OSHA regulations to track serious workplace incidents and ensure compliance with federal safety standards.
There are two primary forms involved in incident reporting for OSHA compliance:
- OSHA Form 300: Log of work-related injuries and illnesses
- OSHA Form 301: Individual incident report form with detailed information about each recorded case
These reports play a pivotal role in tracking safety trends, improving procedures, and protecting personnel.
Why is OSHA Incident Reporting Crucial?
OSHA incident reporting is more than a compliance requirement—it directly impacts the health of your workforce and the safety culture within your organization. Here's why accurate and thorough incident reporting matters:
- Compliance: Avoid costly fines and penalties by meeting regulatory requirements under OSHA's Recordkeeping Rule.
- Trend Analysis: Identify recurring incidents, underlying hazards, and high-risk areas to proactively improve workplace safety.
- Preventative Measures: Use data collected from incident reports to implement measures that reduce the risks of future injuries or illnesses.
- Legal Protection: Accurate records can serve as legal documentation in case of claims or investigations.
- Employee Trust: Transparent reporting fosters a culture of safety, showing employees that their well-being is a top priority.
Key Differences Between Near Misses, Incidents, and Accidents
- Near Miss: An unplanned event that did not result in injury or damage but had the potential to do so (e.g., a falling object narrowly missing someone).
- Incident: An unplanned event that resulted in minor injury, illness, or property damage.
- Accident: An event causing significant injury, illness, fatality, or extensive damage to property.
Each of these occurrences offers valuable lessons. Near misses and minor incidents, in particular, provide critical opportunities to intervene before a more severe accident happens.
Step-by-Step Guide to OSHA Incident Reporting
Creating accurate and effective OSHA incident reports is a structured process. Follow these five essential steps to ensure compliance and extract maximum safety insights.
Step 1: Record the Basic Details
Collect fundamental information immediately after the incident has occurred. Include the following details:
- The time, date, and location of the incident
- Names of all individuals involved
- Witnesses and their contact information
- The type of incident (e.g., injury, illness, property damage)
Step 2: Investigate the Root Cause
Understanding why the incident occurred is critical to prevent repetition. Use root cause analysis techniques such as the 5 Whys, fishbone diagrams, or fault tree analysis. Collect data such as:
- Environmental conditions at the incident site
- The state of equipment or machinery involved
- Employee actions and safety training compliance
Step 3: Document the Incident Thoroughly
Now, it’s time to create the formal report. For OSHA purposes, you’ll need:
- OSHA Form 301: Report detailed information about the incident, including a description of the event, the injured party’s role, and contributing factors.
- OSHA Form 300 (Log): Record the case summary. This log tracks all workplace injuries and illnesses within a calendar year.
Be thorough and unbiased—clear documentation ensures no critical details are overlooked.
Step 4: Submit the Report if Required
Under certain conditions, OSHA mandates direct reporting. For serious incidents like:
- Fatalities: Must be reported within 8 hours.
- Hospitalizations, Amputations, or Loss of Eye(s): Must be reported within 24 hours.
Reports can be filed via the OSHA website, telephone, or your local OSHA office.
Step 5: Analyze and Act
Once the report is complete, use the insights gained to:
- Identify recurring trends
- Implement corrective measures, such as updated equipment, training programs, or engineering controls
- Share lessons learned with relevant departments to promote safe practices
Best Practices for Efficient Reporting
While incident reporting requires accuracy and compliance, it doesn’t have to be overly complicated. Here are strategies to streamline your OSHA reporting process.
1. Establish a Clear Reporting Protocol
Define a standardized process for on-site reporting, including who is responsible for completing forms and notifying OSHA if needed. Develop a checklist to ensure no steps are missed.
2. Train Employees Regularly
Empower your team to recognize and report hazards, near misses, and injuries. Provide periodic training on OSHA requirements and the importance of timely reporting.
3. Leverage Digital Tools
Advanced software solutions simplify incident reporting, ensuring accurate records and real-time trend analysis. Look for programs that:
- Automate OSHA form generation
- Offer digital safety dashboards
- Provide mobile access for field reporting
4. Keep Records Organized and Accessible
OSHA requires records to be maintained for five years. Use cloud-based tools or enterprise safety management platforms to securely store and retrieve reports when needed.
5. Encourage a Safety-Focused Culture
Promote open communication about potential risks and incidents. Employees should feel comfortable reporting near misses or concerns without fear of retaliation.
Transforming Incident Reporting into a Safety Asset
OSHA incident reports aren’t just paperwork—they’re powerful tools for improving workplace safety. When combined with trend analysis, employee training, and proactive interventions, these reports lead to a stronger safety culture and fewer workplace accidents.
By adopting efficient reporting practices and leveraging digital solutions, safety managers, EHS professionals, and operations teams can transform compliance into a competitive advantage.
Want to take your incident reporting process to the next level? Explore smart safety management platforms that automate OSHA reporting and deliver actionable insights in real time.
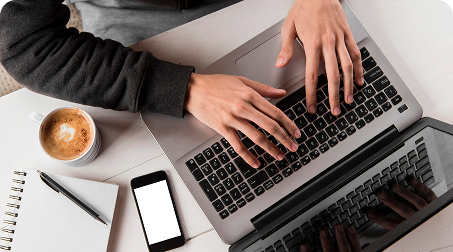
See It In Action
Schedule a personalized demo to see how our solutions can help your business thrive.
- 20-08-2025
Building the future of Industrial Operations with Innovapptive and AWS
Most manufacturers have already gone digital. Yet business outcomes haven’t moved in step. Many...
- 22-04-2025
The $3.6B Unlock: Solving the Chemical Industry’s Labor Crisis and EBITDA Pressure in One Move
“Constraints don’t slow innovation—they force it.”
- 21-04-2025
Chemical Industry's Margin Erosion: A Wake-Up Call for Operational Efficiency Amid China's Oversupply
The global chemical industry is facing mounting challenges, with revenue declines and shrinking...