Overcoming 5 Key Challenges in Supply Chain with Mobile Inventory and Warehouse Management
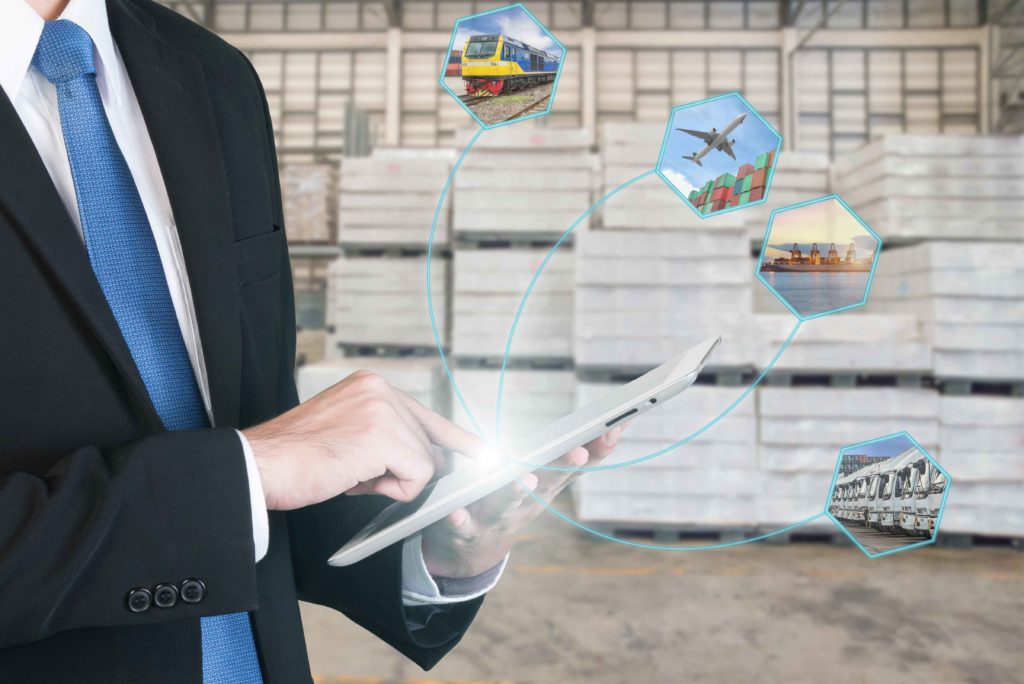
Inventory plays a pivotal role in supply chain operations, as it is a core focus of supply chains. Most activities in the supply chain, such as purchases, transfers, or management, are directly linked to inventory. Having up-to-date inventory data is imperative for effective supply chain operations. In today’s competitive environment, there is enormous demand for consumer products, and to meet this demand, organizations need to maintain appropriate inventory levels in their warehouses and distribution centers. Organizations are now realizing the significant impact effective inventory management systems can have on their bottom line.
In a hyper-competitive business environment, the more warehouse employees have inventory visibility, the better for effective supply chain operations. This visibility helps control the entire flow of inventory, shortening cycle times and improving overall customer service. A lack of accurate insight into inventory management challenges can prevent organizations from gaining a competitive advantage. While most organizations use supply chain software like SAP ERP to manage their operations, these systems are often desktop-based and aren’t feasible for real-time use on the warehouse floor where inventory is handled.
Addressing Key Challenges in Supply Chain Management
1. Absence of Mobility
Managing warehouse and distribution operations becomes challenging when there is a lack of mobility. Employees at the warehouse spend valuable time traveling back and forth between their desks/systems and the warehouse, causing delays in processes. Sometimes, changes in customer orders happen quickly, but warehouse employees are unaware of these changes. As a result, they begin preparing inventory for an outdated order. By the time the order is nearly complete, they are informed of changes, and all their efforts are wasted. This not only wastes time but can also negatively impact the company’s reputation and its relationship with customers.
2. Customer Expectations
Global competition gives customers more choices, and this is making them expect quicker shipping times, order accuracy, and better customer service. This challenge is one that many organizations face. Failure to meet customer expectations can lead to significant losses. Employees may not always be at the front line when it comes to customer service. With legacy systems in place, warehouse and inventory employees often don’t receive real-time updates on inventory levels and stock availability. This can jeopardize customer service if organizations fail to deliver products on time.
3. Inaccurate Data & Redundancy
Whether managing millions of products or smaller orders from the warehouse, inaccurate inventory data and redundancy always pose a significant threat. Irrelevant, incomplete, or redundant data is as harmful as having no data at all, and organizations face difficulties in operating efficiently. Legacy systems often require employees to manually record inventory data, which can result in duplicate or incorrect entries. This wastes time, increases labor costs, and leads to operational inefficiencies, affecting the company’s overall performance.
4. Complex Configuration
Organizations need simple solutions that are quick to install and easy to use. They aim to reduce time spent on configuration and maintenance activities and save on installation and ongoing maintenance costs. However, systems with complex configurations require more time and extensive training, making them less efficient for employees. An ideal solution should be user-friendly and require minimal setup to ensure faster adoption.
5. Integration with Existing Software
Integration is a crucial aspect that cannot be underestimated. Organizations need software solutions that can easily integrate with their existing ERP systems. These solutions should be able to manage inventory transactions on the go without requiring users to access their desktops. Ideally, the solution should also be customizable to meet specific operational requirements.
Enriching Content with Solutions for Inventory Management Challenges
To overcome these challenges, organizations can turn to innovative solutions like Innovapptive’s mInventory application. The mobile inventory management system empowers businesses to enhance stock accuracy, efficiently manage customer orders in real-time, and eliminate delays and errors. The application integrates seamlessly with SAP servers, streamlining transactions and communication.
Warehouse operations can be performed directly on mobile devices through barcode scanning or manual input, ensuring real-time updates to the ERP system. This solution enables businesses to:
- Gain real-time visibility into inventory data, which improves stock accuracy and order fulfillment.
- Reduce manual processes and eliminate redundant data entry, saving labor costs and time.
- Integrate seamlessly with existing ERP systems, providing a unified approach to inventory and order management.
- Improve inventory control and reduce waste by optimizing stock levels.
- Ensure that employees can manage order management and demand forecasting from anywhere within the warehouse.
These features make Innovapptive’s solution an essential tool for addressing inventory management challenges and enhancing supply chain performance.
Conclusion: Embracing Mobility for Inventory Success
By leveraging mobile inventory management solutions, organizations can overcome the most common inventory management challenges, such as lack of mobility, customer expectations, inaccurate data, complex configurations, and integration issues. Innovapptive’s mInventory solution empowers businesses to take control of their inventory in real-time, improving overall supply chain efficiency and customer satisfaction.
If you're interested in exploring how Innovapptive's mInventory (Mobile Inventory and Warehouse Management) solution can address your organization’s inventory management challenges, Request a Live Demo today. For further inquiries or to discuss how Innovapptive’s solution aligns with your operational needs, please reach out via email at sales@innovapptive.com or contact our sales representatives at (713) 275-1804.
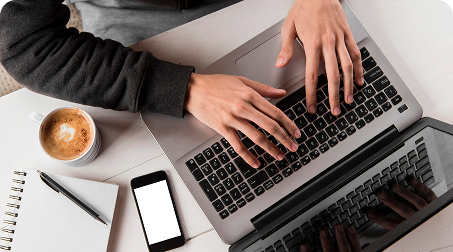
See It In Action
Schedule a personalized demo to see how our solutions can help your business thrive.
- 22-04-2025
The $3.6B Unlock: Solving the Chemical Industry’s Labor Crisis and EBITDA Pressure in One Move
“Constraints don’t slow innovation—they force it.”
- 21-04-2025
Chemical Industry's Margin Erosion: A Wake-Up Call for Operational Efficiency Amid China's Oversupply
The global chemical industry is facing mounting challenges, with revenue declines and shrinking...
- 21-04-2025
Why Wrench Time Isn’t Improving: The Hidden Costs of Traditional Maintenance Scheduling
For years, industrial leaders have relied on a common but flawed assumption: "Better planning and...