Reduce Bottlenecks & Increase Equipment Uptime in Your Production Plants
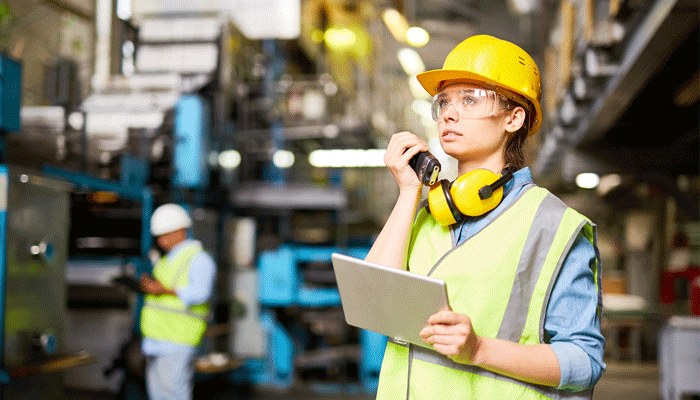
Fast Facts about Manufacturing Downtime and Bottlenecks
- 82% of companies have experienced unplanned downtime over the past three years.
- Unplanned downtime can cost a company as much as $260,000 an hour!
- Bottlenecks in manufacturing processes can cause unplanned downtime.
(Aberdeen Research)
Wait. What was that last one?
Think about it: a bottleneck is just like a car accident or unannounced construction on your highway ride home. A bottleneck in traffic happens when a road area is narrowed, fewer cars pass, a queue forms behind the jam as each driver waits to get through the spot. Queue one of the lovely headaches of urban sprawl.
But I digress...
Efficient management of manufacturing plants while reducing bottlenecks isn’t an easy task. Bottlenecks in processes can create unplanned downtime. Just like in traffic, bottlenecks in manufacturing happen when the flow of production is curtailed due to limited capacity reducing the capacity of the whole chain. Bottlenecks in production can be any, or a combination of, the following:
- Congestion points occur in product flowing.
- Any resource whose capacity is less than the demands placed upon it.
- A manufacturing process that limits throughput.
- Temporary blockades to increased output.
- A facility, operator, etc. that impedes production.
- Any unexpected downtime/breakdown that limits output.
Manufacturers across all industries face the challenge to maximize the availability of critical equipment/assets. They need to ensure that assets run at peak capacity throughout their life-cycle. Whether you operate in aerospace, automotive or other industrial sectors, increased equipment up-time is critical to achieve maximum asset ROI and reduce costs.
A very good example of a bottleneck to production is equipment breakdown/unplanned downtime. It is a massive inconvenience and leads to costly repairs. It also costs your maintenance managers/technicians significant time and causes millions in lost production for your organization.
The direct costs that you face as a manufacturer are very impactful. They range from lost production, reduced system and equipment availability, wasted labor (rescheduling), as well as unexpected costs of repairing equipment and depleted inventories. With such amazing direct costs of downtime, lost profit is inevitable. At the same time, you also face potential indirect costs such as lost opportunity and customer dissatisfaction.
Eliminating downtime is essential – how can you do it?
Knowing when, where, and how downtime occurs is essential to prevent it.
- Regular maintenance of your plant’s assets/equipment
- Essential to keep them operating at their best for the most extended periods possible.
- Switching your maintenance strategy from preventive (run-to-failure) to predictive
- Helps you maximize your production plant equipment uptime.
- Reducing your reliance on paper-based and manual processes
- A cause for user/operator error and a leading cause of downtime on your production line.
- Identifying potential issues early helps minimize your long-term maintenance costs.
- Replacing obsolete equipment to improve performance is an essential step to reducing your manufacturing downtime.
- Ensure that your workers have clear understandings of tasks assigned to them work more effectively
- Having the service and maintenance history of equipment available to your technicians
- Help your technicians perform their jobs more efficiently and effectively.
- Readily available service and maintenance histories also help you identify trends and patterns that would have been otherwise undiscovered.
Innovapptive’s Solution to Increase Equipment Uptime and Reduce Production Bottlenecks
Having the right mobile plant maintenance solution in place can help you increase your plant equipment uptime and reduce costs while maximizing ROI on your SAP investments. Innovapptive understands maintenance challenges faced by today’s manufacturers and it offers a solution for SAP Mobile Plant Maintenance - mWorkOrder.
mWorkOrder gives your maintenance technicians/operators anytime, anywhere access to the information they need to do their jobs effectively while maximizing your asset reliability. It leverages the SAP Plant Maintenance (PM) module at the back-end to deliver a consistent, reliable and productive asset maintenance experience across a wide range of industries. mWorkOrder enables your users to view their assigned activities and access work order history and asset information to facilitate diagnosis and repair.
With mWorkOrder, your enterprise improves your asset performance by increasing your field technician wrench time and increase workforce capacity by providing high visibility of real-time asset information. Increased worker productivity, improved safety, and greater overall efficiency are just a few of the potential benefits mWorkOrder offers. Using mWorkOrder, your maintenance schedulers and/or technicians can make smarter, more informed decisions in real-time. Learn what’s new in mWorkOrder 7.0.
Find out more about how Innovapptive is helping customers manage bottlenecks. Check out this link to one of our most demanded whitepapers on bottlenecks: Overcoming Obstacles in Asset Management.
Request a Demo of Innovapptive’s Mobile Solutions
Innovapptive offers a comprehensive portfolio of mobile solutions to help you reduce bottlenecks, boost equipment uptime, and achieve maximum ROI on SAP investments. To schedule a demo, click here, or contact us at sales@innovapptive.com or call (713) 275-1804.
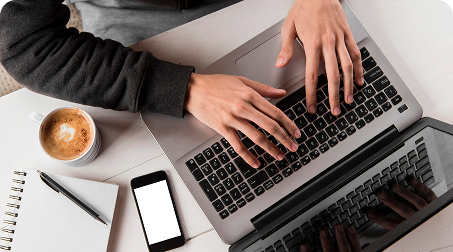
See It In Action
Schedule a personalized demo to see how our solutions can help your business thrive.
- 20-08-2025
Building the future of Industrial Operations with Innovapptive and AWS
Most manufacturers have already gone digital. Yet business outcomes haven’t moved in step. Many...
- 22-04-2025
The $3.6B Unlock: Solving the Chemical Industry’s Labor Crisis and EBITDA Pressure in One Move
“Constraints don’t slow innovation—they force it.”
- 21-04-2025
Chemical Industry's Margin Erosion: A Wake-Up Call for Operational Efficiency Amid China's Oversupply
The global chemical industry is facing mounting challenges, with revenue declines and shrinking...