Reduce Unscheduled Downtime and Improve EHS Compliance with Mobile Operator Rounds
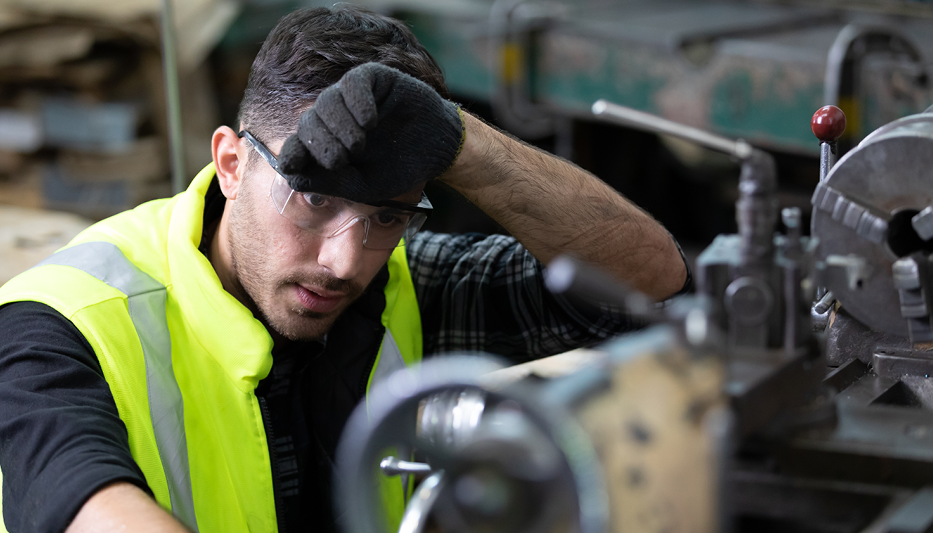
Downtime and environmental, health and safety (EHS) compliance cost industrial manufacturing and process plants serious money, harming already thin profit margins, negatively impacting stakeholders and investors, and cutting into front-line worker morale. Daily operator rounds from plant maintenance technicians identify potential issues before they become problems. However, paper-based inspections often fail to provide accurate, timely information for decision makers to assess risks, prioritize assignments and take remedial action. Mobile operator rounds — using hand-held digital devices such as smartphones and tablets — offer a flexible, agile and dynamic solution to manual paper inspection problems.
Mobile Operator Rounds to Combat Unplanned Downtime and Missed Production
The average manufacturing plant suffers 800 hours of unscheduled downtime every year, equaling nearly 15.5 hours every week. This is no small figure when you consider the typical automotive plant loses $22,000 per minute when production stops. A 15-minute shutdown (the length of a coffee break) could run $330,000 in missed production, lost revenues and wasted resources. Unplanned downtime costs plants a combined estimated $50 billion every year.
Roughly 10% (and maybe even less) of industrial equipment ever actually wears out. The overwhelming majority of mechanical failures within a plant are avoidable. Poorly executed manual operator rounds either miss the signs of these potential failures before they occur or don’t warn decision makers in enough time to take proper pre-emptive action.
That’s because manual, paper-based inspection programs limit visibility. Decision makers are stuck in information silos. They have no way of knowing the status or condition of vital plant production equipment outcome until paper inspection checklists are turned in or manually uploaded into the back-office system.
Mobile operator rounds improve the inspection data collection process, enabling technicians to gather accurate, mission-critical information in less time. Information is immediately uploaded into the back-office system because data capture and sharing is digital, letting decision makers view inspection results in real time.
Better EHS Compliance Using Mobile Operator Rounds
The National Association of Manufacturers (NAM) calculates that environmental and safety regulations cost the average manufacturer an estimated $10,497 per worker. These costs are higher for small companies.
In 2019, the Environmental Protection Agency imposed $471.8 million in combined federal administrative and judicial civil penalties and criminal fines. The agency also charged 137 criminal defendants, up 22% from 2018.
Agencies and the politicians that create EHS rules and regulations are becoming sensitive to desires for a cleaner environment. They have heard pleas for a safer workplace. Worker health has become a priority not only for politicians and regulators, but for the plants themselves to the ongoing COVID-19 crisis.
Manufacturers need ways to better identify threats and assess risks. They’re seeking ways to mitigate exposure, improve their ability to comply with a myriad of ever-more-complex regulations and overlapping agencies and limit the potentially negative consequences of fines, sanctions and penalties.
A mobile operator rounds solution improves the accuracy, thoroughness and timeliness of daily EHS compliance inspections. Digital forms are faster to complete than outdated, error-prone paper checklists. They enable technicians to gather more data with fewer information gaps and be shared with decision makers in real time so that proper remedial steps can be quickly taken to correct the situation.
Mobile Operator Rounds: Flexible, Accurate and Timely
How does a mobile operator rounds solution work? Simply put, hand-held mobile devices (smartphones, tablets, wearables, etc.) replace paper checklists and binders. Technicians access digital forms on their device to conduct the round. These digital forms are dynamic, unlike paper checklists, meaning they can be quickly and easily changed on the fly to better meet a plant’s situational needs.
A mobile operator rounds solution can be customized as needed so a technician can’t proceed to the next inspection area without completing all the necessary steps for the zone in which he or she is currently working. This results in more thorough and complete inspections for equipment maintenance and EHS compliance versus a traditional paper checklist.
Technicians scan equipment barcodes and complete the digital form by checking customized data fields to indicate the present operational status and safety condition. That information is immediately uploaded electronically into the back-office system.
No one has to wait until the end of the round or later to access this critical data. Everything is shared in real time. Decision makers can view inspection information on their own mobile device or on a desktop app. They can also communicate and collaborate with the technician as he or she is conducting the round.
This capability means nothing is overlooked, questions or concerns can be instantly addressed, risk and threat levels quickly ascertained, and action taken before downtime is incurred or a safety threat emerges.
Ready to Learn More about Mobile Operator Rounds?
Innovapptive is a pioneer in the development of Connected Worker solutions that empower plant front-line workers to get their jobs done faster, better, cheaper and safer. Our Mobile Operator Rounds delivers a streamlined data collection process, gives technicians and decision makers greater agility and flexibility to share information and collaborate in real time, reduces downtime and mitigates safety risks. Click here to schedule a free demo, or call us at 844-464-6668.
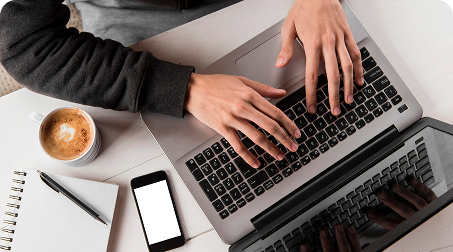
See It In Action
Schedule a personalized demo to see how our solutions can help your business thrive.
- 22-04-2025
The $3.6B Unlock: Solving the Chemical Industry’s Labor Crisis and EBITDA Pressure in One Move
“Constraints don’t slow innovation—they force it.”
- 21-04-2025
Chemical Industry's Margin Erosion: A Wake-Up Call for Operational Efficiency Amid China's Oversupply
The global chemical industry is facing mounting challenges, with revenue declines and shrinking...
- 21-04-2025
Why Wrench Time Isn’t Improving: The Hidden Costs of Traditional Maintenance Scheduling
For years, industrial leaders have relied on a common but flawed assumption: "Better planning and...