Revolutionize Shift Handovers: Embrace Digital Solutions and Ditch Paper Reports
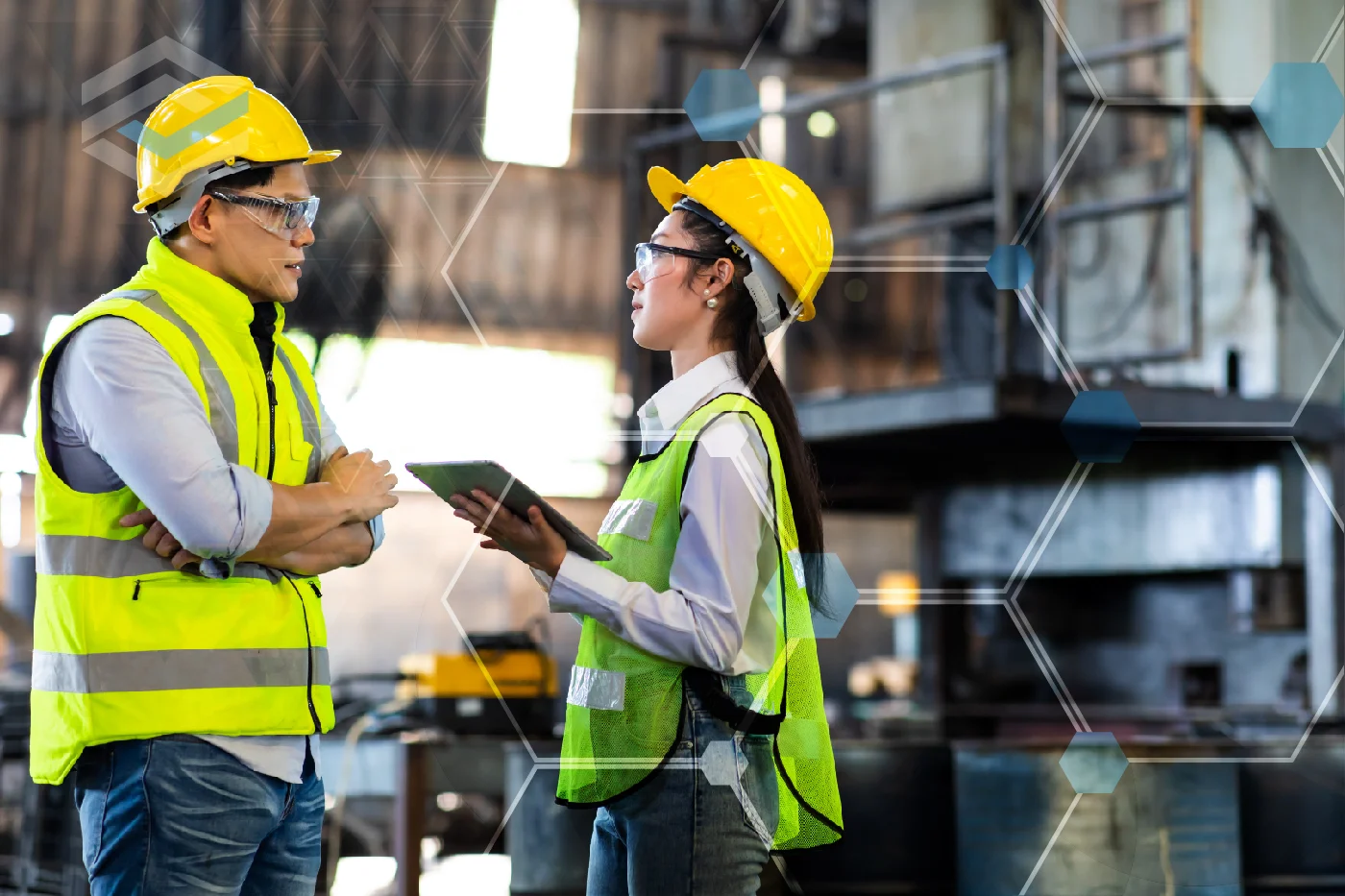
Imagine you're a pilot preparing for a transatlantic flight. You wouldn't rely on crumpled notes scrawled by the previous crew to navigate your way across the ocean, would you? Yet, in countless industrial settings with 24/7 operations, the critical task of shift handover often relies on a similarly archaic method: paper-based forms.
Imagine a power plant or a manufacturing facility where vital information is lost or misinterpreted during a shift change. The consequences can range from production delays and equipment damage to safety hazards and potential downtime. While paper forms may seem like a familiar and simple solution, they introduce a multitude of pain points that can significantly hinder operational efficiency, data accuracy, and ultimately, safety in your organization. Let's delve deeper into these pain points and understand why it's time to ditch paper and embrace the digital revolution in shift handovers.
Pain Points of Paper-Based Shift Handovers
In a sprawling manufacturing plant, the night shift operator is preparing to hand over responsibility to the incoming morning crew. In their hands, they hold a stack of paper forms, each filled with scribbled notes, equipment readings, and critical observations. This scene, unfortunately, plays out in countless industrial settings daily, highlighting the resilience of paper-based shift handovers.
While seemingly familiar and straightforward, this outdated approach creates a multitude of pain points that hinder operational efficiency, data accuracy, and ultimately, safety in large enterprises and industrial setups. Let's look into the specific challenges associated with paper-based handovers and unmask the data-driven truth behind their detrimental impact:
Information Discrepancies and Human Error: Relying solely on handwritten notes creates a breeding ground for information discrepancies. Crucial details can be easily misinterpreted, omitted, or inaccurately recorded, leading to confusion and potential problems during the next shift. Imagine a scenario where the outgoing night-shift operator hastily jots down a note about a "slight vibration" in a critical piece of machinery. However, the incoming morning crew, misinterpreting the scribbled note, assumes it's a minor issue and overlooks it. This oversight could potentially escalate into a major equipment failure, impacting production and incurring significant costs.
Illegibility and Miscommunication: Poor handwriting and inconsistent formatting on paper forms can create ambiguity and hinder effective communication. This can lead to misunderstandings, wasted time clarifying details, and even potential safety hazards.
Time Wastage and Duplication of Effort: Completing paper forms can be time-consuming, with operators often spending valuable minutes searching for information and filling out redundant details across multiple forms. This reduces productivity and diverts their attention away from critical tasks. Furthermore, information might be unnecessarily duplicated across different paper forms, leading to inconsistencies and making it difficult to track trends or retrieve specific data points later.
Inefficient Data Management and Security Concerns: Paper-based records are difficult to manage, organize, and store. This makes it challenging to retrieve specific information when needed, hindering effective decision-making and hindering the identification of trends and patterns. Additionally, paper documents are susceptible to loss, damage, and unauthorized access, raising concerns about data security and confidentiality.
Missed Alerts and Compromised Safety: Critical information, such as safety observations, equipment malfunctions, and maintenance needs, can easily be overlooked or lost amidst handwritten notes and various forms. This can lead to missed alerts and delayed responses, potentially compromising safety and increasing the risk of accidents and incidents. For instance, a crucial safety observation about a faulty pressure gauge might be buried amongst other notes on a paper form, going unnoticed by the incoming shift and increasing the risk of a pressure-related incident.
Embracing the Future: Mobile/Automated Shift Handovers
Paper-based shift handovers are riddled with inefficiencies. Mobile solutions offer a powerful alternative, enabling streamlined workflows through intuitive interfaces. This translates to quicker handovers, freeing up valuable time. Additionally, digital solutions eliminate the risk of human error and misinterpretation, ensuring data accuracy. Real-time dashboards enhance visibility for informed decision-making. Communication flourishes with features like photos and comments, fostering a smooth knowledge transfer. Predictive maintenance and real-time alerts empower proactive responses, improving safety. Finally, data analysis from mobile handovers paves the way for continuous improvement, optimizing operations for long-term success. Ditch the paper and embrace the digital revolution in shift handovers.
Benefits of Digital Shift Handover Solutions
Mobile Operator Rounds replace paper forms with a mobile app, empowering operators to conduct comprehensive and efficient handovers using their smartphones or tablets. The app guides them through pre-defined checklists, ensuring all critical information is captured consistently and accurately.
Here's how this digital approach addresses the challenges mentioned earlier:
- Reduced Information Discrepancies: Standardized checklists and digital forms ensure consistent information recording, minimizing the risk of omissions and misinterpretations.
- Eliminating Human Error: By replacing manual data entry with digital recording, the risk of typos, missed entries, and illegibility is significantly reduced.
But the benefits go beyond simply addressing pain points. Digital solutions offer a multitude of advantages that enhance operational effectiveness:
Digital Reporting: Digital solutions generate real-time reports automatically, providing immediate visibility into critical operational data. These reports can encompass:
- Equipment status and readings
- Maintenance activities and observations
- Safety notes and alerts
Instant Access: Digital solutions provide instant access to essential information for both outgoing and incoming crews. This eliminates the need to search through physical files or rely on handwritten notes, allowing for:
- Faster and more efficient handovers: Operators can access critical information quickly, regardless of their location within the facility.
- Improved knowledge transfer: Incoming crews can readily review previous observations and procedures, ensuring a smooth transition and seamless understanding of the current operational state.
Data Integration: Digital solutions can integrate seamlessly with existing data systems like CMMS and SCADA platforms. This allows for:
- Centralized data storage: All shift handover data is stored in a single, secure location, facilitating easy access and retrieval.
- Automated data analysis: Integration with other systems enables powerful data analysis, providing valuable insights into trends, performance metrics, and potential areas for improvement.
Real-Time Visibility: Digital solutions offer real-time visibility into ongoing operations through features like
- Live dashboards: Supervisors and managers can monitor key performance indicators (KPIs) and operational data in real time, allowing for immediate intervention and course correction if needed.
- Alerts and notifications: The system can be configured to send automated alerts for critical events, equipment malfunctions, or safety concerns, enabling a proactive response and minimizing potential risks.
Safety Enhancements: Digital solutions play a crucial role in enhancing safety within industrial settings by:
- Standardizing safety procedures: Ensures consistent and accurate documentation and communication of critical safety protocols across all shifts.
- Capturing and sharing safety observations: Allows operators to easily record and share safety observations and near misses, fostering a culture of safety awareness and continuous improvement.
- Real-time safety alerts: Enables immediate notification of potential safety hazards or incidents, allowing for prompt response and mitigation of risks.
Stand Out from the Crowd: Innovapptive's Mobile Operator Rounds Solution
Innovapptive's Mobile Operator Rounds solution goes beyond simply offering a digital alternative to paper forms. It's a comprehensive platform designed to revolutionize shift handovers in industrial settings by addressing the pain points and unlocking numerous benefits.
Capabilities
Mobile Operator Rounds empowers your workforce with a suite of features that streamline handovers and enhance operational efficiency:
- Pre-defined checklists: Ensure consistent and comprehensive information collection, covering all critical aspects of each operation.
- Customizable forms: Create and modify checklists to fit specific needs and procedures of different departments or equipment.
- Offline functionality: Operators can complete rounds and record data even in areas with limited or no internet connectivity.
- Data capture options: Capture various data types, including text, photos, videos, and voice recordings, providing a richer and more informative picture of operational status.
- Automated reporting: Generate real-time reports automatically, eliminating manual data entry and providing instant insights.
Overcoming Challenges: Innovapptive's Mobile Operator Rounds doesn't just replace paper forms; it actively overcomes the challenges associated with traditional handovers:
- User-friendly interface: The intuitive mobile app ensures ease of use for operators of all technical backgrounds, minimizing training requirements and maximizing adoption rates.
- Data validation: Built-in data validation rules ensure data accuracy and consistency, minimizing the risk of errors and omissions.
- Audit trails: Maintain a complete record of all operator rounds, including timestamps and user information, providing transparency and accountability.
- Offline data synchronization: Data captured offline is automatically synchronized once an internet connection is available, ensuring data integrity and eliminating the risk of lost information.
Key Differentiators of Innovapptive's Mobile Operator Rounds
Innovapptive's Mobile Operator Rounds solution goes beyond basic functionalities often found in similar offerings. Here are some key features that set it apart and contribute significantly to optimizing OEE:
- Automated Handover Reports: Eliminate manual report generation by automatically compiling data from completed rounds into standardized and informative reports. This saves time, improves data accuracy, and provides valuable insights for monitoring OEE trends and identifying areas for improvement.
- Dynamic Route Optimization: Enhance efficiency by optimizing operator routes based on real-time factors like equipment location, maintenance priorities, and historical data. This minimizes time spent traveling and maximizes time spent on critical inspection and maintenance tasks.
- Context-Driven Collaboration: Foster effective communication by enabling operators to add context to their observations through text, photos, and videos. This eliminates ambiguity and ensures clear understanding, leading to faster problem resolution and reduced downtime.
- Conditional Logics: Utilize customizable rules and triggers to automate specific actions based on collected data. For example, automatically trigger work orders or send notifications to maintenance personnel when equipment readings exceed pre-defined thresholds. This proactive approach helps prevent equipment failures and minimizes unplanned downtime.
- IoT and PI Integration: Seamlessly integrate with existing IoT sensors and plant information (PI) systems, allowing for real-time data collection and analysis. This rich data pool empowers you to gain deeper insights into equipment health and performance, enabling data-driven decision-making to optimize maintenance strategies.
- Data Collection and Audit Trail: Ensure data integrity and compliance by providing a centralized repository for all captured data, including observations, photos, and timestamps. This comprehensive audit trail allows for easy retrieval of historical data, facilitates root cause analysis, and supports regulatory compliance, contributing to a more accountable and efficient operation.
- Operation and Maintenance Integration: Bridge the gap between operations and maintenance teams by providing a unified platform for communication, collaboration, and data sharing. This streamlines workflows, improves collaboration, and enables proactive maintenance practices.
- Observation Dashboards: Gain valuable insights at a glance with customizable dashboards that visually represent key performance indicators (KPIs) related to equipment health and operator performance. This real-time visibility empowers informed decision-making and allows you to identify areas for improvement to continuously optimize your handover process and maximize OEE.
Embrace the Digital Future and Revolutionize Your Handovers
The limitations of paper-based shift handovers are undeniable: wasted time, human error, and compromised safety. By embracing the digital revolution and implementing a comprehensive solution like Innovapptive's Mobile Operator Rounds, you can transform your handovers and reap a multitude of benefits:
- Increased Operational Efficiency: Streamlined workflows, reduced paperwork, and real-time data access lead to significant time savings and improved productivity.
- Improved Data Quality and Informed Decision Making: Eliminate human error and gain reliable data insights for informed decision-making, enabling proactive maintenance and optimized OEE.
- Enhanced Safety and Reduced Risks: Real-time alerts, improved communication, and clear documentation minimize safety risks and prevent equipment failures.
- Improved Employee Engagement and Satisfaction: User-friendly tools and streamlined processes can boost employee engagement and improve overall satisfaction.
- A Sustainable Future for Industrial Operations: Paperless solutions contribute to a more sustainable future by reducing paper waste and minimizing environmental impact.
Innovapptive's Mobile Operator Rounds stands out with its innovative features like automated reports, dynamic route optimization, and data integration, further amplifying the benefits and driving significant OEE improvement.
Don't let paper-based handovers hold you back. Embrace the digital future and revolutionize your shift handovers with Innovapptive. Unlock the potential of your operations and achieve new levels of efficiency, safety, and profitability.
Ready to Ditch Paper and Embrace a Digital Future?
Contact us today for a free demo and discover how our Mobile Operator Rounds solution can transform your shift handovers and propel your industrial operations to new heights.
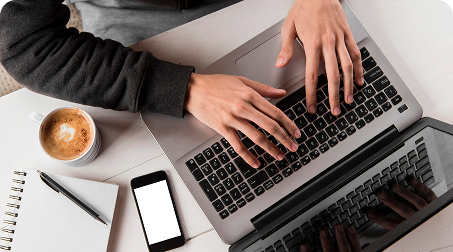
See It In Action
Schedule a personalized demo to see how our solutions can help your business thrive.
- 20-08-2025
Building the future of Industrial Operations with Innovapptive and AWS
Most manufacturers have already gone digital. Yet business outcomes haven’t moved in step. Many...
- 22-04-2025
The $3.6B Unlock: Solving the Chemical Industry’s Labor Crisis and EBITDA Pressure in One Move
“Constraints don’t slow innovation—they force it.”
- 21-04-2025
Chemical Industry's Margin Erosion: A Wake-Up Call for Operational Efficiency Amid China's Oversupply
The global chemical industry is facing mounting challenges, with revenue declines and shrinking...