Role of Route Optimization in Your Maintenance Process Optimization
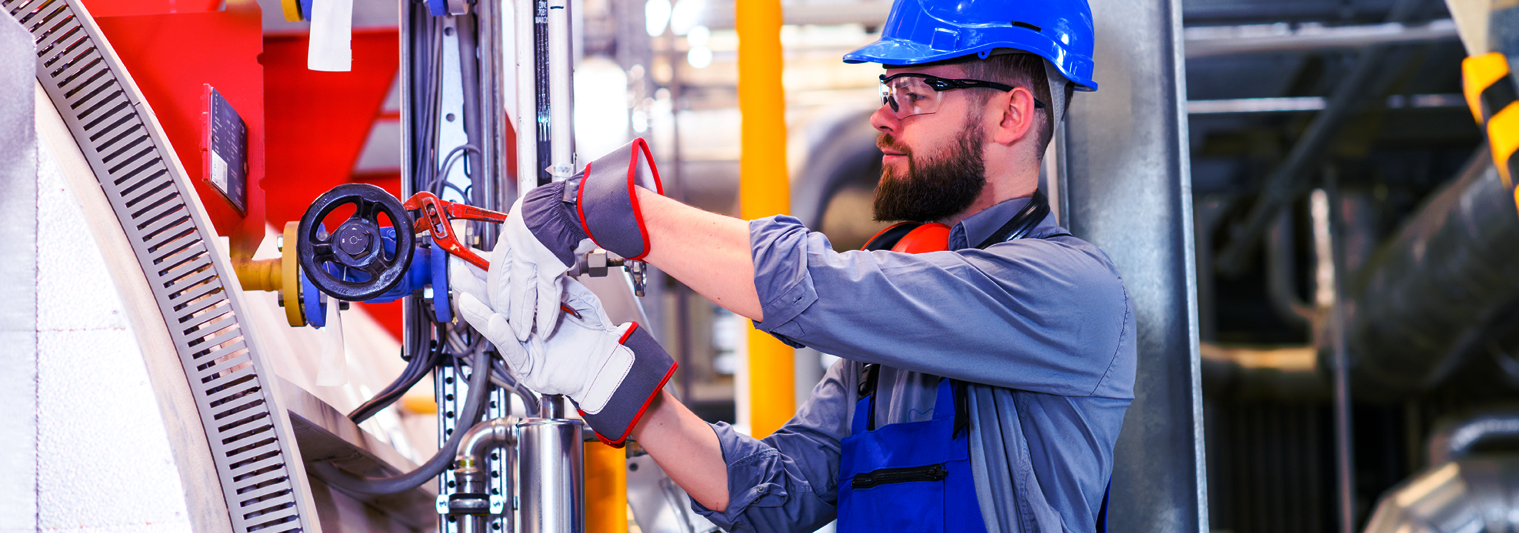
Asset management isn’t just knowing where your assets are, it’s about knowing how they are performing. For maintenance of assets, sending the right technician to the right job at the right time with the right tools and information is critical. A significant amount of asset maintenance time is spent reacting to issues rather than proactively resolving them. However, sometimes, organizations are bombarded with so many service request or work orders. The dispatcher needs to respond to the service requests and ensure maintenance technicians are utilized efficiently.
Today’s ever-changing market conditions and challenges such as generating more revenue, improving customer satisfaction and reducing costs drive c-level executives to find ways to optimize their maintenance processes. To deal with such challenges, organizations need a solution for asset maintenance that not only increases the productivity and efficiency of the maintenance crew but also helps in completing maintenance work faster. A solution, which has the latest features such as GIS mapping or route based-tracking of assets. It can result in reduced maintenance costs, proper utilization of maintenance crew and extended asset life -- all of which contribute to a lower total cost of ownership.
With this information, organizations able to:
- Save money
- Save time (which can be used for other important activities, other than route planning)
- Minimize white space in technicians’ schedules
- More number of jobs per day
- More satisfied customers
Innovapptive’s solution for Plant Maintenance – mWorkOrder, offered within our next generation Connected Workforce Platform, provides your maintenance technicians anytime, anywhere access to the right information they need to efficiently complete their work orders. The robust solution delivers a consistent, reliable and productive asset maintenance experience across a wide range of industries. Armed with GIS mapping, or route optimization, mWorkOrder empowers your schedulers and dispatchers to assign/reassign work orders to your technician closest to the asset needing repair. As a result, once your technicians receive a work order notification on their mobile devices. They can reach sites through optimized routes and attend to requests in the shortest possible time. Organizations that employ mWorkOrder can respond to problems and spend more time focusing on solution strategy rather than worrying about asset performance.
With mWorkOrder’s route optimization feature, organizations can change the game by sending the right worker quickly for the job, every time. They can accelerate their business with increased operational efficiency. Having access to the right information enables technicians to focus on their actual work and complete work orders in their first visit. More completed work orders in a day result in improved wrench time. mWorkOrder works in an offline mode, allowing remote workers to enter asset data from the asset’s location in an offline mode.
With the mWorkOrder solution, organizations help:
- Technicians access route plans and reach the exact location of a physical asset needing repair.
- Dispatchers/supervisors assign work orders to technicians in a location-based manner which reduces travel time.
- Technicians/maintenance crews quickly track critical/high priority tasks to be completed.
- Maintenance crews instantly access information such as asset location, repair histories, work order details, and material required through mobile devices.
- Technicians continue to work with or without network connectivity for seamless user experience.
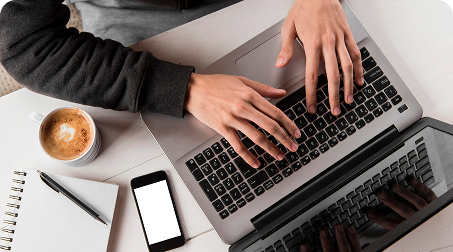
See It In Action
Schedule a personalized demo to see how our solutions can help your business thrive.
- 22-04-2025
The $3.6B Unlock: Solving the Chemical Industry’s Labor Crisis and EBITDA Pressure in One Move
“Constraints don’t slow innovation—they force it.”
- 21-04-2025
Chemical Industry's Margin Erosion: A Wake-Up Call for Operational Efficiency Amid China's Oversupply
The global chemical industry is facing mounting challenges, with revenue declines and shrinking...
- 21-04-2025
Why Wrench Time Isn’t Improving: The Hidden Costs of Traditional Maintenance Scheduling
For years, industrial leaders have relied on a common but flawed assumption: "Better planning and...