Solving the Front-line Worker Skills Gap with Digital Work Instructions
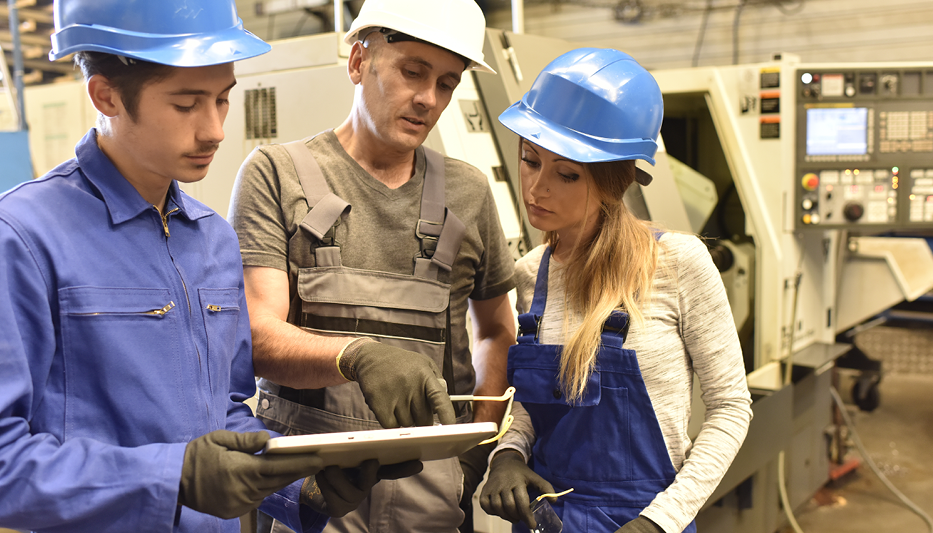
Industrial process plants and manufacturing facilities are confronting twin problems that could lead to a loss in production and revenues in the coming years. These issues may also result in a greater number of safety incidents that might lead to additional fines and penalties. What are these dire concerns? First, the industrial workforce is aging, and those in the Baby Boomer generation are retiring in great numbers and taking their extensive tribal knowledge with them. Incoming Millennials and Gen-Z front-line workers naturally lack this deep well of experience to draw from as they are just starting their careers. This creates a worrisome skills gap. One way to overcome this gap is to employ a Digital Work Instructions solution that enables the quick and easy electronic transfer of tribal knowledge from one generation of front-line workers to the next.
What Are Digital Work Instructions?
A Digital Work Instructions solution electronically connects a veteran plant employee with a less-experienced front-line colleague at the equipment repair site. The veteran employee could be sitting in a nearby office or be across the plant at another unit, at another facility in the same state or country, or even across the world.
The two are connected via a desktop app, tablet or mobile device, in the case of the veteran employee, and for the rookie, a mobile device, tablet or wearable such as smartglasses or a smartwatch. Using this digital work instructions software and tools, veteran employees can issue verbal instructions to less-experienced co-workers. They can also send PDFs, SOPs, inspection sheets, and checklists that will help a newbie better understand how to correctly perform the necessary repairs the first time. The rookie can also ask questions and get real-time feedback from the veteran, increasing the new hire's knowledge base and skill set. This allows for the passing of essential tribal knowledge and the closing of the skills gap.
Digital Work Instructions: A Use Case
Let's examine a Digital Work Instructions solution in action. A piece of rotating equipment has failed at an industrial plant. If it's not repaired quickly, it could affect production and ultimately, revenues. Unfortunately, the plant has also been hit by a rash of recent retirements in the maintenance department and has had a tough time finding suitable skilled replacements.
On the day of the equipment failure, the department is staffed by several new hires. A veteran employee is also on duty, but working on an important project in another part of the plant. The maintenance manager has to send one of the rookies to check out the rotating equipment with the hope it is an easy, quick repair.
Turns out, it'll be a more complex job than initially thought. However, rather than fret, the maintenance manager tells the rookie tech to contact the senior worker across the plant for guidance using the Digital Work Instructions solution.
The new hire dons a pair of smart glasses and engages in a real-time video conference with the experienced co-worker from the repair site. The veteran tech asks the newbie to show him various components within the piece of rotating equipment. The video close-up through the smart glasses enables the vet to see exactly what the rookie is looking at, even though the two are a half-mile apart.
Thanks to this view, the experienced worker is quickly reminded of a similar problem he encountered on a work order a few years ago. So, he issues verbal instructions to his younger counterpart on specific items to check and answers questions from the newbie on the right procedures to follow. The experienced worker also sends PDFs of an inspection list and pages from the piece of equipment's repair manual related to the problem. While watching the rookie work via an app on his mobile device, the veteran offers anecdotal tips to make the job easier. Finally, the experienced worker asks the new hire to perform a few tests to make sure the repair was done correctly before the equipment is returned to service.
Ready to Learn More on Using Digital Work Instructions to Solve Skills Gap Problems?
By digitally working together, the rookie successfully repaired the rotating equipment in less time than it might have taken had the new hire worked alone. This was possible thanks to guidance from his veteran colleague, even though the two were on opposite sides of the plant. The seasoned tech could remotely "see" what the newbie saw and was able to pass along valuable knowledge, expertise and work experience in real time without ever leaving his important project. The rookie tech is now more prepared for the next work order thanks to this virtual on-the-job training session.
Innovapptive offers a Digital Work Instructions solution as part of its Connected Worker platform. This easy-to-use system can enable your plant or facility to successfully meet the challenge of retiring Baby Boomer workers and the skills gap it produces. Rather than losing valuable tribal knowledge and expertise, you can instead pass it along to a new generation of operators and technicians.
To learn more, schedule a free demo today by calling 844-464-6668 or by clicking here
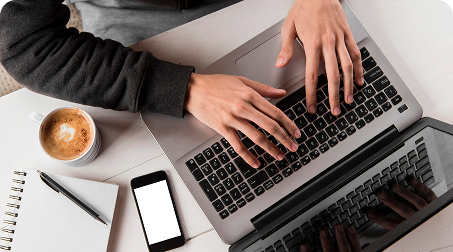
See It In Action
Schedule a personalized demo to see how our solutions can help your business thrive.
- 20-08-2025
Building the future of Industrial Operations with Innovapptive and AWS
Most manufacturers have already gone digital. Yet business outcomes haven’t moved in step. Many...
- 22-04-2025
The $3.6B Unlock: Solving the Chemical Industry’s Labor Crisis and EBITDA Pressure in One Move
“Constraints don’t slow innovation—they force it.”
- 21-04-2025
Chemical Industry's Margin Erosion: A Wake-Up Call for Operational Efficiency Amid China's Oversupply
The global chemical industry is facing mounting challenges, with revenue declines and shrinking...