The 3C Approach: Driving World-Class Operations Through Connection, Collection, and Collaboration
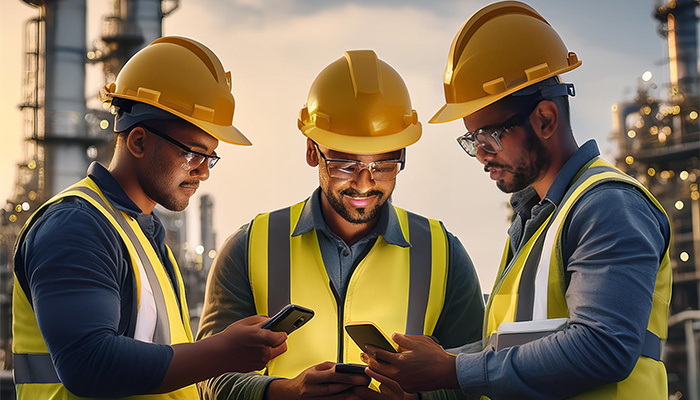
Key Takeaways
- Anticipate Disruptions: Prevent unexpected failures by integrating data for real-time operational visibility.
- Improve Efficiency: Streamline data collection processes to support predictive maintenance and reduce downtime.
- Achieve Operational Excellence: Implement the 3C approach—Connect, Collect, Collaborate—to drive world-class industrial operations.
Introduction
An oil refinery runs at full capacity, processes crude oil, and meets production targets. Suddenly, a critical compressor fails, leading to an unexpected shutdown. The consequences are immediate—production stops, deadlines are missed, and costs start to escalate. Maintenance teams scramble to diagnose the issue, but the financial and operational damage is already significant by the time the repairs are complete. The company has not only lost valuable production time but also risks tarnishing its reputation with key stakeholders.
This scenario is all too common in the oil and gas industry, where operational efficiency is critical to success. Equipment failures, regulatory compliance issues, and operational inefficiencies can disrupt even the most carefully managed operations. But what if these disruptions could be anticipated and prevented? This is where a modern operations platform comes into play, powered by the 3C approach: Connect, Collect, Collaborate.
Understanding the Complexity of Modern Operations
Industries today operate in a complex and challenging environment, where they must balance multiple priorities to stay competitive and sustainable. The fast pace of technological change, evolving regulatory demands, and rising consumer expectations add to the pressure on businesses. Organizations are struggling to balance multiple priorities:
- Regulatory Compliance: Adhering to increasingly stringent regulations can be time-consuming and costly.
- Efficiency Demands: The need to optimize processes, reduce waste, and minimize downtime is more pressing than ever.
- Technological Integration: Integrating new technologies into existing operations can be complex and disruptive.
- Data Management: Managing and analyzing vast amounts of data to extract valuable insights can be overwhelming.
These challenges are interconnected and can amplify one another. For example, non-compliance with regulations can lead to fines and penalties, which can reduce efficiency and increase costs. Similarly, the inability to manage data effectively can hinder decision-making and limit the potential benefits of new technologies.
To address these challenges, organizations must adopt a holistic approach that considers all aspects of their operations. This includes implementing strategies to improve regulatory compliance and efficiency, integrate new technologies effectively, and manage data effectively.
Introducing the 3C Approach: A Blueprint for Operational Excellence
The 3C approach is a holistic strategy designed to address the complexities of modern industrial operations. It focuses on three core principles:
- Connect: Integrating data sources to create a unified, real-time view of operations.
- Collect: Streamlining the collection and analysis of data to support predictive maintenance and operational efficiency.
- Collaborate: Fostering collaboration across departments to ensure seamless operations and continuous improvement.
Connect: Building a Unified Operational View
In industrial settings, data is often siloed across various systems, leading to inefficiencies and costly errors. Integrating data sources across the enterprise creates a unified, real-time view of operations, essential for predictive maintenance.
- Integrating Data Sources: A modern operations platform connects ERP, IoT, and historian systems, creating a single source of truth. This integration enables real-time monitoring and proactive maintenance, reducing the risk of unexpected failures.
- ERP and Historian Integration: Seamless integration of ERP and historian systems allows companies to track asset performance more effectively.
- IoT and Cloud Connectivity: Connecting IoT sensors and cloud services provide real-time data analysis, enabling predictive maintenance.
Collect: Leveraging Data for Predictive Insights
The second pillar of the 3C approach is Collect. The value of connected data depends on its quality and completeness. Predictive maintenance relies on accurate, timely data, and a modern operations platform excels in streamlining data collection processes.
- Streamlining Data Collection: The platform’s mobile applications are designed for seamless data collection, even in challenging environments. Offline capabilities ensure data is captured in remote locations and synced automatically when connectivity is restored.
- AI/ML Integration for Predictive Maintenance: The platform leverages AI and ML to analyze data and generate predictive insights, allowing companies to identify potential issues before they escalate.
- User-Friendly Interface: The platform’s mobile apps are designed with the user in mind, ensuring that operators can quickly input data, capture images, and annotate information. This intuitive design leads to more reliable data collection and effective predictive maintenance.
Collaborate: Fostering Cross-Functional Alignment
The third and final pillar of the 3C approach is collaboration. Operational excellence is not just about connecting and collecting data—it’s about ensuring all departments are aligned and working towards the same goals. Collaboration is key to maintaining operational efficiency and driving continuous improvement.
- Fostering Collaboration across Departments: The platform breaks down silos and fosters real-time communication across teams, ensuring everyone is on the same page.
- Automated Shift Handovers: Automated, rule-driven shift handovers ensure that critical information is passed seamlessly between shifts, reducing errors and maintaining continuity.
- Real-Time Dashboards and Contextual Collaboration: Real-time dashboards provide a comprehensive view of operations, allowing decision-makers to monitor KPIs and respond quickly to issues. Contextual collaboration tools enable teams to share information in real time, improving issue resolution.
Innovapptive: Your Partner for Operational Excellence
As industries continue to evolve, the need for operational excellence will only become more critical. The 3C approach offers a proven blueprint for achieving this excellence. Innovapptive’s mobile operator rounds solution embodies this approach, providing the tools and insights needed to stay ahead in a competitive industrial landscape.
- Real-World Success: Proven results across diverse industries, including oil and gas, pharmaceuticals, and manufacturing.
- Tangible Results: Experience reduced unplanned downtime, improved data accuracy, and improved collaboration.
- Future-Proof Solutions: Stay ahead of the curve with a platform that empowers you to embrace the latest advancements in predictive.
Innovapptive's commitment to operational excellence is rooted in its 3Cs philosophy. By seamlessly integrating data sources, streamlining data collection processes, and fostering collaboration, our platform delivers unparalleled solutions for predictive maintenance and operational efficiency. Schedule a free demo today to learn more.
FAQs
- Q1: What is the 3C approach?
A1: The 3C approach stands for Connect, Collect, Collaborate. It’s a holistic strategy designed to optimize industrial operations by integrating data sources (Connect), streamlining data collection for predictive maintenance (Collect), and fostering cross-functional collaboration (Collaborate).
- Q2: How does the 3C approach improve operational efficiency?
A2: The 3C approach improves efficiency by creating a unified view of operations, enabling predictive insights through accurate data collection, and enhancing collaboration across departments. This results in fewer disruptions, better decision-making, and more streamlined operations.
- Q3: What are the key benefits of implementing the 3C approach with Innovapptive’s platform?
A3: Innovapptive’s platform delivers tangible benefits such as reduced unplanned downtime, improved data accuracy, and enhanced cross-functional collaboration. The platform integrates seamlessly with existing systems and leverages advanced technologies like AI/ML to support predictive maintenance and operational excellence.
- Q4: How does Innovapptive’s platform facilitate collaboration?
A4: The platform facilitates collaboration through features like automated shift handovers, real-time dashboards, and contextual collaboration tools, ensuring that all departments are aligned and can work together efficiently to resolve issues and improve operations.
- Q5: Can Innovapptive’s platform be integrated with our existing systems?
A5: Yes, Innovapptive’s platform is designed for compatibility with existing ERP systems, historian systems, and IoT devices. This ensures a smooth integration process, enabling your organization to leverage its current infrastructure while adopting new technologies.
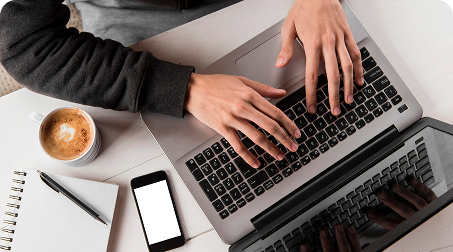
See It In Action
Schedule a personalized demo to see how our solutions can help your business thrive.
- 20-08-2025
Building the future of Industrial Operations with Innovapptive and AWS
Most manufacturers have already gone digital. Yet business outcomes haven’t moved in step. Many...
- 22-04-2025
The $3.6B Unlock: Solving the Chemical Industry’s Labor Crisis and EBITDA Pressure in One Move
“Constraints don’t slow innovation—they force it.”
- 21-04-2025
Chemical Industry's Margin Erosion: A Wake-Up Call for Operational Efficiency Amid China's Oversupply
The global chemical industry is facing mounting challenges, with revenue declines and shrinking...