6 Top Considerations When Adopting Your Mobile Workforce Solutions
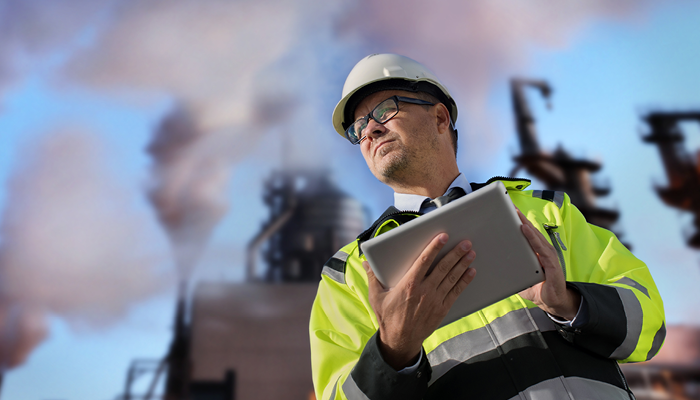
Mobile workforce solutions provide a competitive advantage to enterprise companies, and in the process, redefine the way businesses manage their operations. Clients in multiple industries are using mobile solutions to be more agile and flexible, enabling their field engineers and technicians to have better access to information and respond quickly to customers' needs.
With workflow automation and digital innovation growing in field services, mobility is EVERYWHERE. As consumers, we have become more demanding for instant go-anywhere access, and in the field or on the plant floor it’s no different. Flexibility and convenience are must-have attributes for mobile enterprise solutions.
6 points to consider helping move your company towards a truly connected mobile workforce platform:
- Mobility is about anytime, anywhere access to information.
- It is critical that your mobility solution makes it possible to achieve this.
- Fresh to market platforms and solutions offering everything under the sun may sound phenomenal, but only in theory.
- Overly-complicated systems can be challenging to use so they should be avoided, worked around or ignored altogether.
- Select a mobile workforce solution or connected workforce platform that is easy to use.
- Mobile solutions should be agile.
- With new technologies appearing daily, keeping up to speed with changes is essential for enterprise companies.
- Time is money, as the saying goes.
- Being able to deliver faster ROI is critical for mobility solutions. Implementations should be quick and straightforward, allowing users to maintain productivity.
- Lengthy deployments defeat the objectives of improving the speed of processes which connected workforce platforms offer.
- Ease of integration is an essential requirement. You don’t need to rework your whole plant maintenance solution.
- With Innovapptive’s Connected Workforce Platform™ and RACE™ (Rapid App Configurator Engine) technology, you can achieve out-of-the-box integrations with SAP Plant Maintenance, geospatial systems and more that meet your unique business requirements.
- The key to mobility solutions is “Mobile.”
- It is critical for your chosen mobile workforce solution to work across a variety of digital devices (phones, tablets, handhelds, etc.) and different operating systems as well.
Innovapptive’s Connected Workforce Platform answers all the requirements, easily. Our platform helps asset-intensive organizations better connect executives, the back office, field technicians, plant operators, warehouse operators, and maintenance planners, to maximize revenues and profitability. Combining field-ready business applications that are device agnostic, with the power of no-code configuration tools in RACE™, we provide a system of engagement that connects various ERP or enterprise back-end systems.
Join Innovapptive in Booth 1926 at Sapphire NOW May 7-9 in sunny Orlando, Florida. Our team of solution and industry experts will be available for demos and discussions on our next generation Connected Workforce Platform-which digitally connects your executives, your entire industrial workforce, and your back office to minimize plant outages and improve operational excellence.
We’ll see you there!
Want to Discover More?
Innovapptive – a Connected Worker Platform provider – has a simple mission: “Connect and create conversations between people, machinery and work processes while improving people’s lives.” Innovapptive offers the only Connected Worker Platform that digitizes the last mile of your front-line workers into SAP and IBM (watch a short video here). We’d like to show how our Connected Worker Platform and related applications can help you successfully start and complete your journey to more efficient, safe and productive plant operations. Schedule a free demo today by calling 844-464-6668 or or by clicking here.
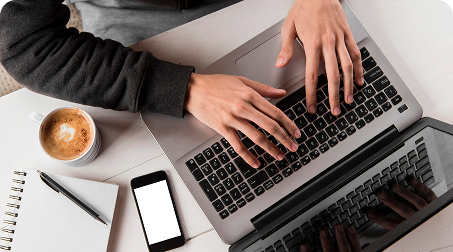
See It In Action
Schedule a personalized demo to see how our solutions can help your business thrive.
- 20-08-2025
Building the future of Industrial Operations with Innovapptive and AWS
Most manufacturers have already gone digital. Yet business outcomes haven’t moved in step. Many...
- 22-04-2025
The $3.6B Unlock: Solving the Chemical Industry’s Labor Crisis and EBITDA Pressure in One Move
“Constraints don’t slow innovation—they force it.”
- 21-04-2025
Chemical Industry's Margin Erosion: A Wake-Up Call for Operational Efficiency Amid China's Oversupply
The global chemical industry is facing mounting challenges, with revenue declines and shrinking...