Using a Connected Worker Platform to Improve Social Distancing Protocols
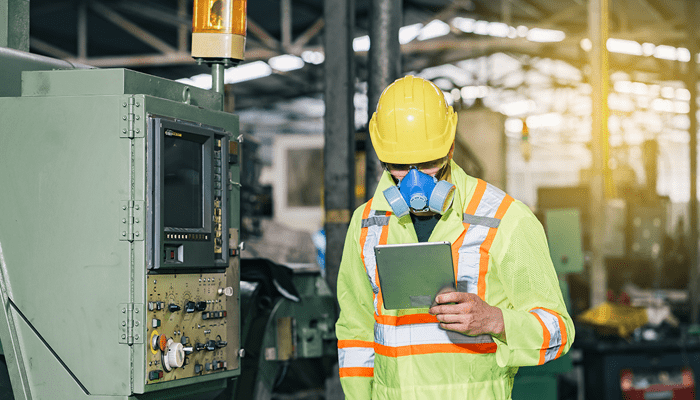
It’s not an exaggeration to refer to world history as pre-COVID-19 and post-COVID-19. It’s certainly worth remembering how this pandemic originated, emerged and compelled us to adopt a new normal - social distancing - in our personal and professional lives. In terms of spread and impact, COVID-19 has outpaced every other pandemic in history. But this is much more than a health emergency; it’s a human and economic crisis attacking societies at their cores.
The World Trade Organization (WTO) has forecasted a 13 to 32 percent drop in world merchandise trade in 2020 due to the current economic disruption. The International Monetary Fund (IMF)’s World Economic Outlook for April 2020 projected that the world's real GDP growth rate will be -3 percent. In advanced economies and developing ones, this will be -6.1 percent and -1 percent respectively. These projections show that COVID-19’s economic crisis is worse than the 2008 economic crisis, when the world’s real GDP growth rate was only -0.1 percent.
In the process of preventing the spread of the coronavirus, nations are sacrificing economic activity. Unemployment rate across the world has soared up. In a developed economy like America, over 26 million people have applied for unemployment benefits through early May - an estimated 14.7 percent jobless rate, the highest mark since the Great Depression. In India, the unemployment rate stood at 23.52 percent in April 2020. If such a recession were to persist for an extended period, it could even become the world’s second Great Depression, something that could cripple the world economy for years.
Social distancing - the new normal and a new challenge for industries
In the absence of a vaccine, workplaces are more susceptible to COVID-19. This may result in absenteeism, change in commerce patterns and supply chain disruptions. Commerce patterns and supply chains are not in the total control of an employer. But, occupational safety is achievable in workplaces through social distancing to mitigate absenteeism and keep operations running smoothly.
Social distancing means reduced workforce, which results in lost productivity. Implementing social distancing could come at a premium, particularly for asset-intensive industries. The “new normal” challenges are exaggerating the already aging workforce coupled with a tight labor market has resulted in critical skills and talent gaps impacting the ability of asset-intensive industries to recruit, train and retain a workforce with suitable competencies. The Manufacturing Institute estimates that because of the skills gap 2.4 million job openings in manufacturing will likely go unfilled through 2028, representing half of all open positions.
In the wake of this COVID-19 health and economic emergency, industrial companies are taking all necessary steps, including rapid implementation of connected worker strategies. Connected worker solutions digitizes the last mile of ERP systems for the front line worker to eliminate paper-based processes and form a vital part of industrial digital transformation (IX). They open new doors for businesses to gain competitive advantage during and post the COVID-19 era.
Connected Worker Strategy to Win over the COVID-19 Crisis
Industrial companies are slowly shifting their focus from digital transformation to industrial transformation. Connected Worker is one of the vital use cases of industrial transformation. An LNS research reports that 46 percent of industrial companies have already deployed connected worker technologies for better productivity, quality and safety. However, most of these initiatives have stuck at pilot tests and/or showed little impact. Longer integration time (than expected) and lack of subject matter expertise prove to be the primary reasons behind this failure.
The ideal solution you choose must close the last mile of the front-line worker by empowering him with the right information, at the right time. Apart from unlocking SAP, an ideal connected worker solution provides guided and step-by-step work instructions on their operations. However, it makes no sense to invest into a silo SaaS platform that can only deliver work instructions to your front-line worker.
No-Code Platforms to Connect Front-Line Workers
Industrial companies which are non-IT-intensive in nature want digital transformation to be a smooth road, even in the absence of large tech teams and a big budget. So, low-code/no-code platforms - known for their agility, simple cost structure, and cross-platform mobility - have proven to be the right choice for them. These platforms make application building highly accessible for non-programmers and enterprises with less engineering efforts.
For better understanding, see how Innovapptive’s RACE Dynamic Forms, an enterprise-grade no-code platform, helps companies perform COVID-19 risk assessments at their workplaces:
It goes without saying that a siloed approach will take industrial transformation nowhere. Combining information across business and industrial operations will dramatically optimize performance and boost outcomes. Looking for a trusted advisor who can help you transform your industrial business to combat marginal pressures and talent challenges and occupational risks during the COVID-19 crisis and after? Reach out to our experts on 888-464-6668 or visit www.innovapptive.com.
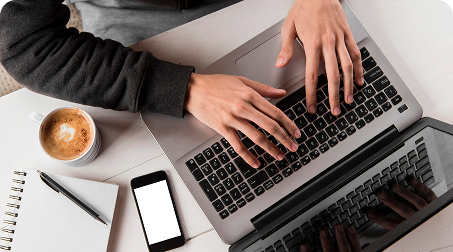
See It In Action
Schedule a personalized demo to see how our solutions can help your business thrive.
- 20-08-2025
Building the future of Industrial Operations with Innovapptive and AWS
Most manufacturers have already gone digital. Yet business outcomes haven’t moved in step. Many...
- 22-04-2025
The $3.6B Unlock: Solving the Chemical Industry’s Labor Crisis and EBITDA Pressure in One Move
“Constraints don’t slow innovation—they force it.”
- 21-04-2025
Chemical Industry's Margin Erosion: A Wake-Up Call for Operational Efficiency Amid China's Oversupply
The global chemical industry is facing mounting challenges, with revenue declines and shrinking...