A Connected Worker Strategy is an Imperative in the COVID-19 Era
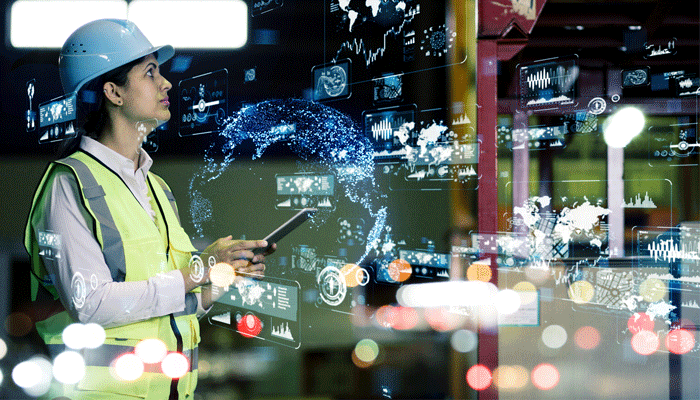
You and your legacy work order management system have been through a lot together over the years. But thanks to the ongoing COVID-19 crisis, you’re likely finding your tried and true friend is just no longer up to the task. It lacks the flexibility, agility and speed you need to keep up with rapidly changing environmental, health and safety compliance regulations and guidelines. It can’t change and adapt to help you protect workers, and maintain production and revenues in an age of lockdowns and social distancing.
What do you do now? Should you replace your legacy system? Can you afford to? With all that’s at stake, can you afford not to?
The old ways of working will no longer work in the COVID-19 era. Enterprises must start looking into connected worker strategies to Combat Margin Pressures, Talent Challenges and COVID-19 with a Connected Worker Strategy. View this on-demand webinar here to learn and examine the problems of EHS compliance and legacy systems. It will also help attendees adjust to a new way of thinking and embrace digital technology to solve problems.
Market research giant Gartner suggests companies “establish an outcome-driven technology approach by selecting technology that enhances compliance leaders’ ability to make timely decisions, while streamlining burdensome, manual processes.”
If your current legacy work order management system is not accomplishing this, then it’s time for a change. If you’re wondering if the midst of a crisis is the right time to undertake such a change, that answer is yes. A crisis is the time for bold decisions that will ensure your company will make it through the COVID-19 pandemic, but will thrive and prosper when it eventually ends.
Legacy work order management systems were fine for their times. But as technology has since progressed, industrial plants and facilities are finding themselves increasingly hampered by their legacy systems’ growing limitations compared to modern ones. This is especially evident during a crisis, such as today’s COVID-19 pandemic. The legacy system simply can’t accommodate increased EHS compliance demands and lacks the configurability, customization capabilities and scalability, among others.
Manufacturing plants utilizing a modern digital work order and EHS compliance platform enjoy:
- Immediate access to high-value, real-time electronic data via desktop or any mobile device on which to base informed decisions
- Fast and accurate compliance reporting
- Enhanced compliance with EHS regulations
- Ability to ensure procedures are being followed
- Worker tracing to determine if social distancing protocols are working
- Rapid risk assessment and threat capture
- Ability to respond quickly to trends or problems
- Reduced administrative overhead
Employees using such a platform perform EHS-compliance activities including smartphones, tablets, barcode scanners, wearables, drones, etc. They accomplish tasks, collect data and report to back-office systems of record, like SAP. Supervisors and decision makers can review progress and see results on mobile devices and desktop applications. Because they are using mobile, hand-held devices, employees can better practice COVID-19-prevention measures such as social distancing.
mWorkOrder (watch video here) forms a major component of Innovapptive’s Connected Worker Platform. Plant maintenance technicians using mWorkOrder can perform digital operator rounds, conduct safety inspections, carry out risk assessments and complete environmental checklists, recording information from the production floor and in the field. As the information is collected electronically on digital forms, it’s uploaded immediately into the back-office system. This not only gives EHS compliance managers, directors and executives immediate access, it also cuts down on errors from manual data uploads, reduces administrative overhead and eliminates exposure to potentially contaminated paper forms.
Thanks to immediate electronic access to data, decision makers can spot EHS issues, analyze trends, formulate action plans, issue work orders to remedy problems and track progress at every step, with no delays.
mWorkOrder users have seen the following EHS benefits:
- 70% reduction in regulatory fines
- 70% drop in safety incidents
- 50% improvement in inspection backlogs and compliance.
- 24% drop in unplanned downtime.
RACETM Dynamic Forms – what separates Innovapptive from the field
Manufacturing is a highly regulated business. There are a host of environmental, health and safety regulations on the local, state and federal levels. Staying in compliance with these many regulations can be an onerous, time-consuming task, especially in a paper-based process. Innovapptive has developed an easy-to-use, highly configurable solution that transforms this task from a slow, static paper process into a fast, dynamic digital one.
RACE Dynamic Forms improves data collection for equipment inspections, safety checklists, risk assessments, workplace compliance forms, etc. Super users can digitally edit existing mobile forms or create customized new forms in about 30 minutes or less – with no programming or coding experience required. It can also digitize all your work instructions, SOPs and combine them with important operational data from SAP and IBM Maximo. You’ll get consistent, easy to decipher, and relevant data customizable to your needs. No more depending on IT. Capture data on any mobile device from anywhere within your plant or enterprise and seamlessly relay that information to the back office. View results on a mobile device or desktop to ensure procedures are being followed and accurately track when and where actions were completed. All without touching a single paper form.
In response to the COVID-19 crisis, we’ve enhanced mWorkOrder and RACE Dynamic Forms to better keep manufacturing plant employees safe and free from coronavirus infection. Innovapptive has worked within the latest CDC guidelines to develop several coronavirus digital checklists.
Innovapptive has developed several examples and videos on how you can embrace public health regulation guidelines, practice “social distancing” and reduce the risk of COVID-19 disease spread across your workforce:
- COVID-19 Work Order Execution and Job Safety Instructions – Derived from the CDC’s COVID-19 Preparedness Assessment Test, this checklist mandates technicians complete the coronavirus testing protocol before beginning any work order. This ensures workers don’t take unnecessary risks and remain compliant with health and safety procedures. View a video here.
- COVID-19 Site and Environment Risk Assessment – Conduct regular and thorough risk assessment exercises to determine your organization’s vulnerability to COVID-19. Rank risks by severity and likeliness of occurring, enabling decision makers to take prompt and appropriate action. View a video here.
- COVID-19 Safety Inspection Checklist – Develop and implement a response plan to promote personal protection and social distancing. Ensure your company has taken all needed preventative measures to safeguard workers and stop the spread of COVID-19. View a video here.
- COVID-19 Site Preparedness – Identify specific tasks you can perform today to prepare for, respond to and remain vigilant in the face of the COVID-19 pandemic, or any other public health threat. View a video here.
To learn more about Innovapptive, mWorkOrder and RACE Dynamic Forms, watch our free on-demand webinar - Combat Margin Pressures, Talent Challenges and COVID-19 with a Connected Worker Strategy by clicking here. Once you’ve seen the benefits and versatility of a Connected Worker Platform, call us at 888-464-6668. Our experts are standing by to answer your questions, listen to your needs and to configure a solution to overcome your challenges.
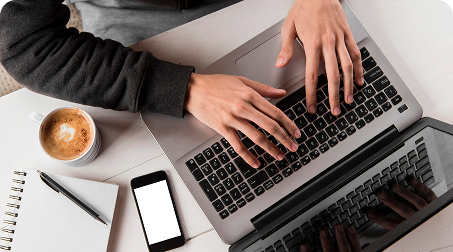
See It In Action
Schedule a personalized demo to see how our solutions can help your business thrive.
- 20-08-2025
Building the future of Industrial Operations with Innovapptive and AWS
Most manufacturers have already gone digital. Yet business outcomes haven’t moved in step. Many...
- 22-04-2025
The $3.6B Unlock: Solving the Chemical Industry’s Labor Crisis and EBITDA Pressure in One Move
“Constraints don’t slow innovation—they force it.”
- 21-04-2025
Chemical Industry's Margin Erosion: A Wake-Up Call for Operational Efficiency Amid China's Oversupply
The global chemical industry is facing mounting challenges, with revenue declines and shrinking...