Optical Character Recognition (OCR) to Overcome Major Supply Chain Bottlenecks
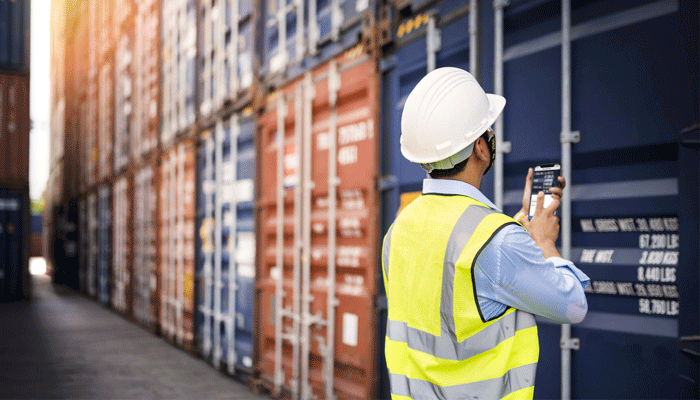
Optical Character Recognition (OCR) creates a digital version of a printed, typed, or handwritten document that computers can read. It avoids the need to manually type or enter text. Why not just take a photo? Because you wouldn't be able to edit anything or search the text because it would just be an image. Scanning the document and running OCR software quickly turns the file into something you can edit and search.
Optical Character Recognition for Supply Chain
In asset-intensive industries, critical warehouse processes are still completely paper-based, inefficient and error prone. The first step to solving a poor goods receipt process is to replace the existing paper-based process with a mobile application that integrates into the back-end ERP systems such as SAP and IBM Maximo.
OCR technology has grown and matured over the years with breakthroughs in Artificial Intelligence. This has opened up opportunities for enterprises to integrate OCR into the mobile solution to tackle supply chain bottlenecks in three key operations:- Goods receipt
- Loading/transport
- Goods returns
%20to%20overcome%203%20Supply%20Chain%20Bottlenecks%20%20_BLOG%20Graphic_20191101.png?width=1200&name=Using%20Optical%20Character%20Recognition%20(OCR)%20to%20overcome%203%20Supply%20Chain%20Bottlenecks%20%20_BLOG%20Graphic_20191101.png)
Its where the four walls of the warehouse interface with the outside world that we see 3 key opportunities to use OCR:
- Goods Receipt
- Loading/Transport
- Returns
A warehouse operation with inbound deliveries from suppliers, product storage and outbound deliveries to customers or field workers (for spare parts).
- Goods Receipt - OCR capability allows you to scan purchase order number, manufacturer’s serial numbers, delivery notes, bill of lading, Customs documentation, etc. using a mobile device. This avoids the need to key in inputs, saving time and more importantly reducing the possibility for errors. The mobile solution will directly upload this data into the ERP system.
- Loading and Transport - The loading process typically involves interfacing with third party transport resources including drivers, trucks and containers. It’s important that you capture accurate information for control and visibility of outbound deliveries to customers.
Use OCR to scan the vehicle registration plate, trailer number, container number, drivers’ licences, etc. This will help you ensure the right delivery is loaded on the right vehicle or container and populated in the shipment document, waybill or manifest which accompanies the vehicle. OCR can give you much greater integrity and accuracy for your outbound supply chain to the customer or field worker.
- Returns - A final warehouse process where OCR can have a big impact is Returns. Product returns are notoriously difficult to control. Asset-intensive industries have big problems with returns through their spare parts operations. Engineers don’t know exactly which parts they will need when they create a work-order in advance of starting repair work. Any parts they don’t need to complete a repair will be sent back to the warehouse as a return, but often without any paperwork. This makes it nearly impossible for the warehouse to identify the parts.
However, once you have OCR in place the serial number on the item can be scanned and it immediately comes back with detail of the part. Serial numbers tend to be used for high-value equipment so this is a great way of improving control on those items.
If you are looking for a mobile inventory management solution that features optical character recognition (OCR) capability while integrating with your ERP system, you’re at the right place. Get a live demo of Innovapptive’s connected mobile warehouse management solution, mInventory: For more details, visit Innovapptive.com or call 1-844-464-6668.
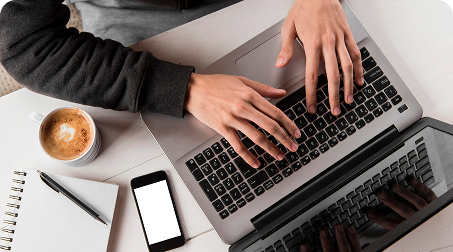
See It In Action
Schedule a personalized demo to see how our solutions can help your business thrive.
- 22-04-2025
The $3.6B Unlock: Solving the Chemical Industry’s Labor Crisis and EBITDA Pressure in One Move
“Constraints don’t slow innovation—they force it.”
- 21-04-2025
Chemical Industry's Margin Erosion: A Wake-Up Call for Operational Efficiency Amid China's Oversupply
The global chemical industry is facing mounting challenges, with revenue declines and shrinking...
- 21-04-2025
Why Wrench Time Isn’t Improving: The Hidden Costs of Traditional Maintenance Scheduling
For years, industrial leaders have relied on a common but flawed assumption: "Better planning and...