Why Effective Workforce Management Is Critical In the Oil and Gas Industry
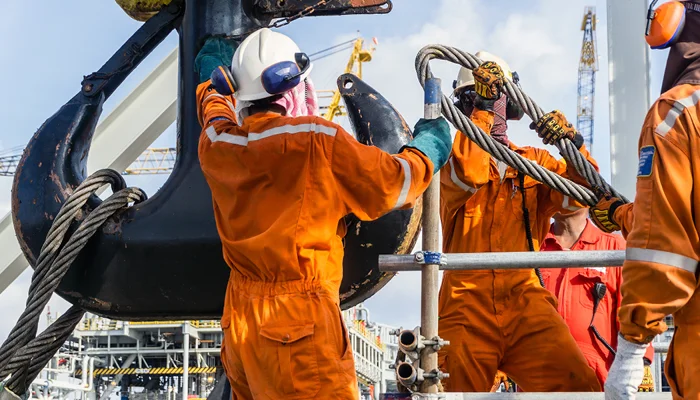
Aging equipment, lack of resources or staff, and poor scheduling rank among some of the biggest maintenance challenges faced by industrial plants. Workforce management and resource allocation (both physical and human) are extremely crucial parts of facility management in any industry. It becomes all the more critical in asset-intensive and hazardous industries like oil and gas. Simply put, the most effective means for ensuring that you get the most value from your resource allocation and workforce productivity is by reducing overall downtime.
Reducing Unplanned Downtime: As the equipment and facilities age, oil and gas operators face greater challenges in maintaining and safely operating their facilities. To avoid any unplanned downtime, the frontline workers need to be adequately trained to recognize asset integrity and reliability. Thorough inspection and maintenance are essential factors for smooth and safe operations, so managers need to have the technical expertise and skill of the frontline workers so that they can assign the right work order to the right person to avoid any mistakes which can cause unexpected downtime.
Bridging Skills Gaps: According to a January 2022 Labor Force Statistics Survey, more than 60,000 American oil and gas workers are over 55 years of age and large-scale losses are being faced by companies across upstream, midstream, and downstream. This is leading to a huge skill gap in the industry where the new workers who lack experience and expertise are more prone to making mistakes that lead to backlogs and unplanned downtime. The lack of remote assistance and disconnected work order processes here only add to the chaos and cost increases. Collaborative work environments are one method to ensure productivity, but even better, digitalization is the real enhancement that new frontline workers need to boost operational efficiency.
Optimizing Time and Cost: The U.S. Energy Information Administration (EIA) predicted that a refinery may require as many as 1,500 - 2,000 skilled outside contractors onsite during a turnaround. This calls for meticulous planning and coordination between onsite and offsite teams. There needs to be greater visibility into the skill levels of the workforce and their work occupancy so that managers can align work effectively. Manual work allocation takes a lot of time and is prone to human error which subsequently results in an extra cost burden in case of consequent downtime.
Mitigating Risk: Because the fatality rate in oil and gas facilities is seven times greater in comparison to other industries, workplace and workforce safety is a key concern to be taken care of. To ensure safety, regular inspection and preventative maintenance of wells and plants are essential which needs frequent deployment of labor and technicians on the site. Particularly in the post-covid world where a majority of the workforce is scattered, effective and collaborative human capital management becomes critical for ensuring continuity and safe functioning of any oil and gas facility.
Issues With Traditional Paper-based Workforce Management Processes
Relying on paper-based processes and legacy systems often leads to conflicting maintenance activities primarily because of communication gaps, overlap in work assignments and ambiguities. A technician, for instance, can receive a manual work order and arrive in the field only to realize another technician is already executing the same work order, resulting in a waste of time and misutilization of the resource.
Contrary to paper-based maintenance processes, mobile work order management solutions deliver real-time visibility into oil and gas operations and maintenance. Maintenance managers can easily see frontline workers assigned to a project with a few clicks.
One of the key factors for effective maintenance in plants with good operational results is proper planning and scheduling. By mobilizing work order processes and using mobile workforce management tools, oil and gas maintenance managers can prioritize work orders and effectively assign resources. They can better plan and schedule work with visibility into real-time progress of previous work orders and knowledge about who is available to take on a new assignment.
Ready To Unlock the Power of Mobile Workforce Management?
Innovapptive, a connected worker solution pioneer, specializes in SAP and IBM Maximo compatible mobile plant maintenance systems that improve technician productivity, transform reactive processes and cut downtime costs. Schedule a free demo of mWorkOrder today, and then call us at 888-464-6668. Our oil and gas experts can show you how replacing a cumbersome paper-based process with a mobile work order solution can dramatically reduce costs and improve efficiencies.
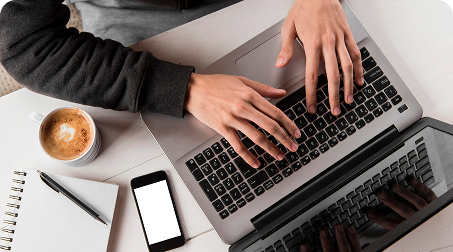
See It In Action
Schedule a personalized demo to see how our solutions can help your business thrive.
- 20-08-2025
Building the future of Industrial Operations with Innovapptive and AWS
Most manufacturers have already gone digital. Yet business outcomes haven’t moved in step. Many...
- 22-04-2025
The $3.6B Unlock: Solving the Chemical Industry’s Labor Crisis and EBITDA Pressure in One Move
“Constraints don’t slow innovation—they force it.”
- 21-04-2025
Chemical Industry's Margin Erosion: A Wake-Up Call for Operational Efficiency Amid China's Oversupply
The global chemical industry is facing mounting challenges, with revenue declines and shrinking...