5 Challenges Confronting Mining Operations (and How Connected Worker Solutions Can Help)
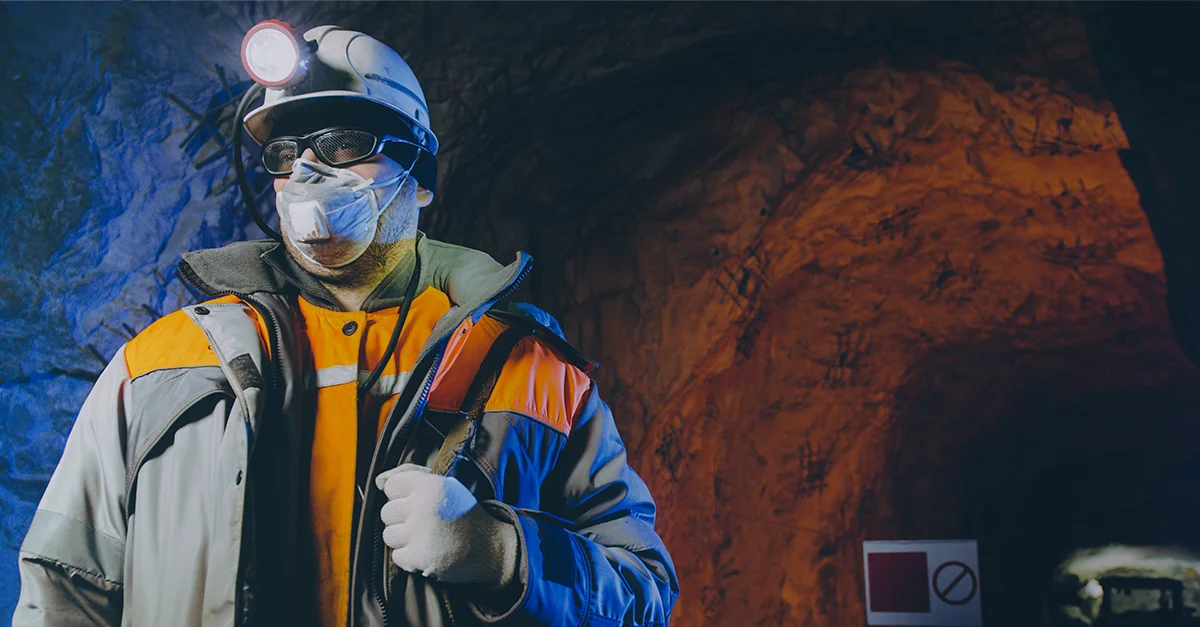
The Evolving Landscape of Mining
The mining industry plays a crucial role in the global economy, supplying essential resources for various sectors. However, it also faces significant challenges related to sustainability, demand uncertainty, technological disruption, workforce skills, and operational costs. These challenges, while significant, also present opportunities for innovation, efficiency improvements, and long-term success.
This blog explores these five key challenges and how connected worker solutions, powered by advancements like AI, blockchain, and mobile technology, can empower mining operations to overcome them and navigate the evolving landscape of 2024 and beyond.
Challenge 1: Climate Action - Navigating Sustainability Demands
Mining activities can have a significant impact on the environment, and stakeholders are demanding stricter regulations and sustainable practices. A recent study revealed that 40% of stream reaches in western watersheds are contaminated by mining activities.
The Net-Zero Challenge: The ambitious goal of achieving net-zero emissions by 2050 requires significant advancements in operational efficiency and environmental responsibility. Mining companies must find ways to reduce their carbon footprint, optimize resource utilization, and implement sustainable practices throughout their operations.
Challenges for Miners:
- Balancing environmental regulations with production targets.
- Reducing energy consumption and greenhouse gas emissions.
- Implementing sustainable practices throughout operations.
How Connected Worker Solutions Can Help:
- Real-time data insights: Gain deeper visibility into your operations, identify areas of inefficiencies that contribute to energy consumption and emissions.
- Data-driven decision-making: Leverage real-time data to optimize equipment performance, implement preventive maintenance strategies, and reduce energy waste.
- Mobile tools for compliance: Empower your workforce with mobile apps that facilitate the implementation and monitoring of environmental regulations, ensuring adherence to sustainability standards.
Challenge 2: Demand Uncertainty - Navigating a Shifting Market with Confidence
The mining industry operates in a dynamic market environment. The shift towards renewable energy sources is impacting the demand for certain minerals while creating opportunities for others. Additionally, technological advancements pose a threat of substitution, making it crucial for mining companies to adapt and forecast future needs effectively.
The Price Fluctuation Challenge: Fluctuating commodity prices and uncertain demand can significantly impact your revenue and profitability. Accurately forecasting future market trends is essential for making informed investment decisions, securing resources, and optimizing production strategies.
Challenges for Miners:
- Predicting future demand for specific minerals in a fluctuating market.
- Mitigating risks associated with price fluctuations.
- Identifying and capitalizing on emerging opportunities.
How Connected Worker Solutions Can Help:
- Real-time data collection and analysis: Gain insights into market trends and potential disruptions.
- Advanced analytics: Make data-driven decisions about resource allocation and production strategies.
- Scenario modeling: Simulate different market scenarios to prepare for potential changes.
Challenge 3: Technology & Innovation - Embracing the Digital Future
Advancements in AI, data science, automation, and blockchain offer immense potential for the mining industries, improving efficiency, optimizing operations, and enhancing decision-making. However, successful integration and user adoption remain crucial challenges.
Challenges for Miners:
- Identifying and implementing relevant use cases for new technologies.
- Overcoming resistance to change from the workforce.
- Ensuring user adoption and maximizing the return on investment.
How Connected Worker Solutions Can Help:
- User-friendly mobile apps: Bridge the gap between technology and the workforce, facilitating adoption.
- Configurable digital work instructions: Deliver step-by-step guidance and training on new technologies.
- Pilot projects and user involvement: Foster smooth technology adoption by involving users and addressing their concerns.
Challenge 4: Skills Gap - Bridging the Knowledge Divide
The mining industry faces a widening skills gap due to two key factors:
- The Great Crew Change: Experienced workers are retiring, taking valuable knowledge and expertise with them.
- The influx of a new generation: Younger workers entering the workforce often possess different skill sets and require targeted training to adapt to the demands of mining operations.
The Knowledge Transfer Challenge: Effectively transferring knowledge from experienced workers to the next generation is critical for ensuring the continuity of operations and maintaining high standards of safety and efficiency. Traditional training methods often struggle to keep pace with the evolving needs of the industry.
Challenges for Miners:
- Effectively transferring knowledge from experienced to new workers.
- Addressing the evolving skillset requirements of the industry.
- Attracting and retaining skilled workers in a competitive market.
How Connected Worker Solutions Can Help:
- Configurable digital work instructions: Capture and codify the knowledge of experienced workers for future generations.
- On-demand training materials: Provide accessible learning opportunities for new recruits and upskilling initiatives.
- Knowledge-sharing platforms: Facilitate collaboration and knowledge transfer between experienced and new workers.
Challenge 5: Operational Costs & Productivity - Optimizing Efficiency
Mining companies face increasing pressure on profit margins due to rising costs of materials, labor, and energy. Optimizing operational efficiency and maximizing productivity are crucial for maintaining profitability and competitiveness in a challenging market.
The Hidden Inefficiency: Frontline workers often rely on paper-based processes and manual data capture, leading to errors, delays, and inefficiencies. This disconnect between the workforce and digital technologies hinders your ability to gain real-time insights and optimize operations effectively.
Challenges for Miners:
- Reducing operational costs and streamlining processes.
- Improving data collection and communication for informed decision-making.
- Bridging the disconnect between frontline workers and digital technologies.
How Connected Worker Solutions Can Help:
- Mobile data capture: Equip workers with mobile apps to eliminate manual data entry errors and streamline data collection.
- Real-time insights: Gain instant visibility into key performance indicators for faster problem-solving and improved decision-making.
- Improved communication and collaboration: Facilitate seamless communication between workers, supervisors, and management, enabling better coordination and faster response times.
Connected Worker Solutions - The Path to a Sustainable Future
The challenges facing the mining industry are complex, but not insurmountable. Connected worker solutions offer a powerful tool to address these challenges and empower mining operations to achieve sustainability, efficiency, and long-term success. By equipping your workforce with the right tools and technologies, you can:
- Reduce your environmental footprint and contribute to a sustainable future.
- Navigate market uncertainty with confidence and make data-driven decisions.
- Embrace digital transformation and unlock the full potential of your workforce.
- Bridge the skills gap and ensure the continuity of knowledge and expertise.
- Optimize operational efficiency and maximize profitability.
Investing in connected worker solutions is not just about addressing current challenges; it's about building a resilient and sustainable future for your mining operations.
If you are ready to take the first step towards a more efficient, sustainable, and profitable future, schedule a free demo to explore how Innovapptive’s connected worker solution like mWOrkOrder can transform your mining operations and empower your workforce to achieve remarkable results.
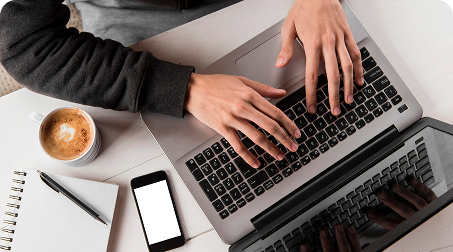
See It In Action
Schedule a personalized demo to see how our solutions can help your business thrive.
- 22-04-2025
The $3.6B Unlock: Solving the Chemical Industry’s Labor Crisis and EBITDA Pressure in One Move
“Constraints don’t slow innovation—they force it.”
- 21-04-2025
Chemical Industry's Margin Erosion: A Wake-Up Call for Operational Efficiency Amid China's Oversupply
The global chemical industry is facing mounting challenges, with revenue declines and shrinking...
- 21-04-2025
Why Wrench Time Isn’t Improving: The Hidden Costs of Traditional Maintenance Scheduling
For years, industrial leaders have relied on a common but flawed assumption: "Better planning and...