7 Reasons Why Oil & Gas Should Embrace SAP Mobile Plant Maintenance
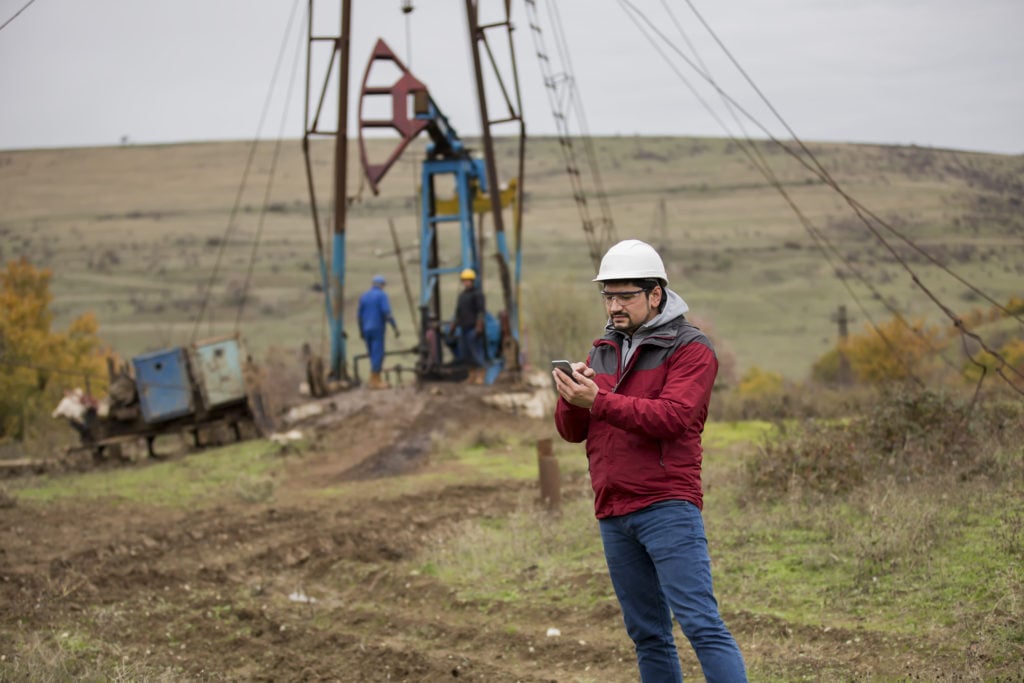
Digital Transformation and the Connected Worker Strategy
The Connected Worker strategy is the next logical step in digital transformation. It joins technology and digital trends such as Cloud, mobile, wearables, augmented reality, AI/ML, virtual assistants and other connected products to achieve business goals. In oil & gas plant maintenance, these include improving operational data collection, streamlining processes and increasing reliability.
Mobile Plant Maintenance at an Oil & Gas Facility
For oil & gas directors, managers and supervisors looking to boost their maintenance processes, here are six solid reasons to consider moving to a Connected Worker strategy and mobile plant maintenance:
- Manual data capture: Manual maintenance data collection processes are slow and cumbersome. Front-line workers must lug around checklists and heavy binders for inspections, operator rounds and when performing work orders. A mobile plant maintenance system digitizes the data collection and distribution process, adding needed speed and efficiency. Front-line workers using mobile devices, such as smartphones, tablets, barcode scanners, smart glasses, smartwatches and drones, perform their duties, collect maintenance data and disseminate it in real time to decision makers. Executives, managers and supervisors can access this real-time data via desktop apps or on their own mobile devices. This enables them to follow work progress, issue instructions or notifications, and make knowledgeable decisions based on verified facts gathered directly in the field only moments before.
- Safety and productivity: Front-line industrial workers need a lot of information in the field to perform their jobs better, faster, cheaper and safer. However, these underserved front-line industrial workers have to perform highly complex jobs with very little on the job assistance or access to information. By combining data from systems such as SAP, necessary attachments, drawings, specifications and capturing the execution of the field data with step by step, visual and guided work instructions in real-time. This experience empowers the front-line worker to minimize incidents/accidents and maximize productivity.
- Data accuracy loss in reporting: Manual data collection processes introduce errors and inaccuracies. Paper forms pass through many hands in their journey. Each pass means someone may misinterpret something, or transfer the wrong information. Time is also a factor in creating reporting inaccuracies. A paper form is a snapshot of a particular point in time. If it takes several hours or even days to get the data entered and make it accessible, it may no longer reflect what’s happening now. A mobile plant maintenance system delivers real-time data collected and verified in the field by an operator or technician at the scene. It’s automatically and immediately uploaded into the back-office system, giving decision makers instant access.
- Poor integration with back-office systems: Plants using manual data collection processes and legacy systems have trouble integrating with their back-office systems. Either someone has to manually input information into them or the older, legacy system limits the effectiveness and utility of newer, more robust technology. This means the plant doesn’t get the full advantage of the technology, the back-office system or data collection capabilities of their maintenance staff. A mobile plant maintenance system offers seamless integration between the front-line worker, technology and the plant’s back-office system. Each can work together, not as three separate components, but as a single effective unit. This enables front-line workers to accomplish more and plants to make optimum use of all of them.
- Lack of communication and collaboration: Traditional maintenance processes discourage communication and collaboration. Few people communicate with each other, creating information silos that result in bottlenecks. Front-line workers also find it hard to collaborate on projects, which hinders productivity and innovation. A mobile plant maintenance system delivers real-time information gathered directly by front-line workers in the field. There’s no delay as with a manual, paper process. Decision makers have total visibility into what’s going on with equipment, compliance and safety, enabling them to take timely actions.
- Lack of process flexibility and agility: Traditional manual processes are rigid and resistant to innovation and change. They're static, not dynamic. For an organization that wants to improve its maintenance efficiency and get ahead of issues to reduce downtime, a traditional, manual process doesn’t offer much in the way of greater productivity. A mobile plant maintenance system makes maintenance teams more nimble, enabling them to quickly pivot workers, resources and priorities according to the real-time situation. Instead of a static paper-form, front-line workers and decision makers utilize dynamic, mobile technology that can be personalized by site, role, user and geographies. The capabilities can be further aligned to ensure higher productivity and worker safety.
- Reworks and backlogs: A mobile plant maintenance system reduces frustrating and costly reworks and backlogs. Such a solution enables remote collaboration between a technician at the location and a supervisor or more experienced worker elsewhere via a two-way video call on smart glasses. The supervisor or senior tech can monitor the situation at all times using a desktop app and provide guided instructions in real time, effectively walking the less-experienced worker through the process. Maintenance work gets done right, the first time. Reworks are reduced, which decreases backlogs. Maintenance becomes more productive and efficient.
Learn More
Innovapptive is the only Connected Worker platform that digitizes the last mile of your front-line workers into SAP and IBM. Our Mobile Plant Maintenance delivers a streamlined data collection process, gives technicians and decision makers greater agility and flexibility to share information and collaborate in real time, reduces downtime and mitigates risks. Click here to schedule a free demo, or call us at 844-464-6668.
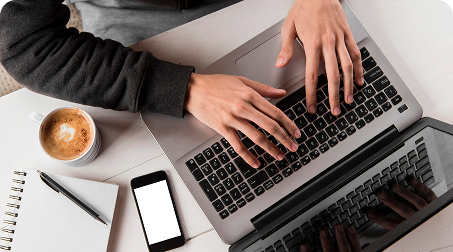
See It In Action
Schedule a personalized demo to see how our solutions can help your business thrive.
- 22-04-2025
The $3.6B Unlock: Solving the Chemical Industry’s Labor Crisis and EBITDA Pressure in One Move
“Constraints don’t slow innovation—they force it.”
- 21-04-2025
Chemical Industry's Margin Erosion: A Wake-Up Call for Operational Efficiency Amid China's Oversupply
The global chemical industry is facing mounting challenges, with revenue declines and shrinking...
- 21-04-2025
Why Wrench Time Isn’t Improving: The Hidden Costs of Traditional Maintenance Scheduling
For years, industrial leaders have relied on a common but flawed assumption: "Better planning and...