The Power of Foresight: A Guide to Proactive Maintenance in Industrial Enterprises
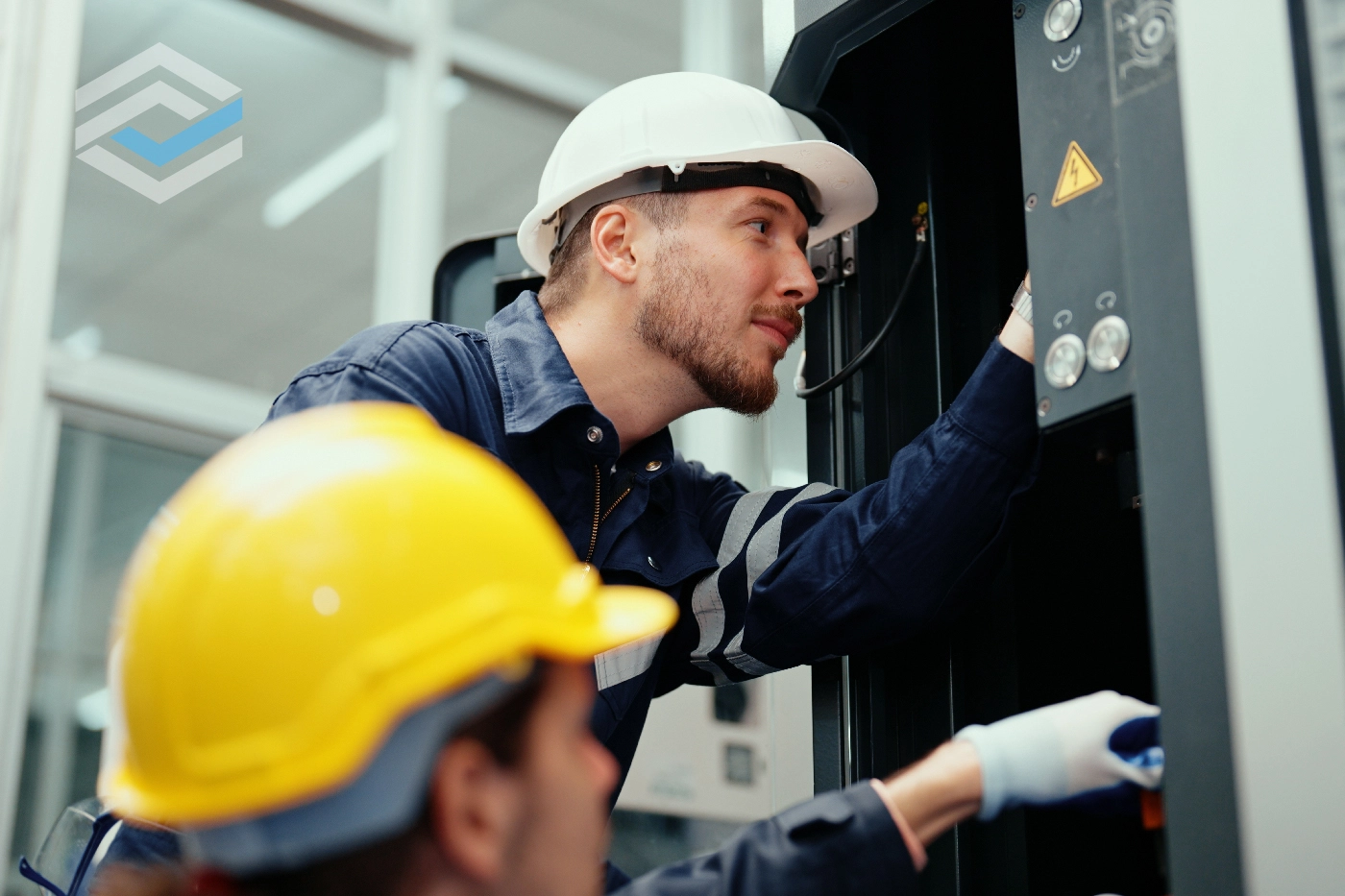
Imagine a world where your factory floor runs smoothly, equipment breakdowns are a rarity, and production goals are consistently met. This isn't a pipe dream; it's the reality achievable through proactive maintenance. In today's competitive industrial landscape, unplanned downtime due to equipment failures can be catastrophic. Lost production, delayed deliveries, and frustrated customers are just a few of the consequences. Proactive maintenance offers a solution, empowering businesses to shift from reactive firefighting to a strategic approach that prioritizes preventing problems before they occur.
What is Proactive Maintenance?
Proactive maintenance, also known as predictive maintenance or condition-based maintenance, is a data-driven strategy that focuses on anticipating and preventing equipment failures. Unlike reactive maintenance, which involves fixing equipment after it breaks down, proactive maintenance involves monitoring equipment health and scheduling maintenance based on real-time data and predictive analytics. This allows technicians to address potential issues before they escalate into major breakdowns, minimizing downtime and maximizing equipment lifespan.
What Are the Characteristics of Proactive Maintenance?
Proactive maintenance has several specific characteristics:
- Data-driven: Proactive maintenance relies on data collected from sensors embedded in equipment to monitor key parameters like vibration, temperature, or pressure.
- Predictive: Advanced analytics software interprets sensor data to predict potential equipment failures and schedule maintenance accordingly.
- Preventative: The primary goal is to prevent breakdowns before they occur, minimizing disruption and costs.
- Continuous: Proactive maintenance is an ongoing process, requiring consistent monitoring and analysis of equipment health data.
Why Is Proactive Maintenance Important?
The benefits of proactive maintenance are numerous and far-reaching. Here are some key reasons why industrial enterprises should prioritize this approach:
- Reduced Downtime: Unplanned equipment failures can lead to significant downtime, impacting production schedules, customer deliveries, and overall profitability. Proactive maintenance significantly reduces downtime by identifying and addressing potential issues before they cause complete breakdowns. According to a McKinsey report: [invalid URL removed], proactive maintenance can reduce unplanned downtime by 30-50%.
- Increased Equipment Lifespan: By addressing minor issues before they snowball into major problems, proactive maintenance allows equipment to operate at optimal efficiency for a longer period. This extends equipment lifespan and reduces the need for costly replacements.
- Improved Safety: Equipment failures can pose safety risks to workers. Proactive maintenance helps identify potential hazards before they cause accidents, creating a safer work environment.
- Reduced Maintenance Costs: While proactive maintenance does require an upfront investment in sensors and data analysis software, it ultimately leads to significant cost savings. By preventing breakdowns, businesses avoid the high costs associated with emergency repairs, part replacements, and lost production.
- Enhanced Operational Efficiency: Proactive maintenance promotes a culture of continuous improvement and preventive action. This leads to smoother operations, improved productivity, and a more predictable production environment.
Proactive Maintenance vs. Preventive Maintenance
Proactive maintenance is often confused with preventive maintenance. While both share the goal of preventing equipment failures, they differ in their approach.
Preventive maintenance relies on scheduled maintenance tasks performed at predetermined intervals, regardless of equipment health. This "check-up" approach can be effective for equipment with predictable wear and tear patterns, but it may lead to unnecessary maintenance for infrequently used equipment.
Proactive maintenance is more data-driven and targeted. By leveraging sensor data and analytics, it allows for maintenance to be scheduled only when necessary, optimizing resource allocation and minimizing unnecessary maintenance activities.
Types of Proactive Maintenance
There are several types of proactive maintenance strategies, each suited to specific equipment and operational needs. Here's an overview of the most common approaches:
- Condition-Based Maintenance (CBM): This method uses sensors to continuously monitor key equipment parameters. Advanced analytics software interprets this data to identify potential failures and trigger maintenance actions.
- Vibration Analysis: By monitoring vibration levels in equipment like motors or bearings, potential issues can be detected and addressed before they cause breakdowns.
- Oil Analysis: Analyzing oil samples from equipment can reveal signs of wear and tear, allowing for proactive maintenance to be scheduled.
- Thermography: Thermal imaging cameras can identify abnormal temperature variations in equipment, indicating potential problems like overheating or electrical faults.
- Ultrasound Inspection: This technique utilizes sound waves to detect cracks, leaks, or other internal defects in equipment.
- Usage-Based Maintenance (UBM): This approach bases maintenance on equipment usage data, such as operating hours, number of cycles completed, or volume of material processed. This ensures maintenance aligns with actual equipment usage and avoids unnecessary downtime.
- Route-Based Maintenance: This strategy groups maintenance tasks for several pieces of equipment located in a specific area. This optimizes technician time and improves maintenance efficiency, particularly for geographically dispersed assets.
Advantages and Disadvantages of Proactive Maintenance
Proactive maintenance offers a compelling set of benefits, but it's not without its drawbacks. Here's a balanced view of the pros and cons:
Advantages:
- Reduced downtime and improved production efficiency (as discussed earlier).
- Increased equipment lifespan and reduced replacement costs.
- Enhanced safety through early detection of potential hazards.
- Lower overall maintenance costs by preventing major breakdowns.
- Improved planning and scheduling for maintenance activities.
- Data-driven insights that lead to better decision-making about equipment health and performance.
Disadvantages:
- Upfront investment is required for sensors, data analysis software, and potentially additional training for personnel.
- Reliance on reliable data collection and advanced analytics capabilities.
- May not be suitable for all types of equipment, particularly older equipment without sensor integration capabilities.
- Requires a cultural shift within the organization to embrace a proactive approach to maintenance.
Requirements or Steps for Implementing Proactive Maintenance
Successfully implementing proactive maintenance requires careful planning and execution. Here are the key steps involved:
- Identify Critical Equipment: Prioritize equipment that is critical to your operations and has a high potential for causing downtime if it fails.
- Establish Data Collection: Implement a system for collecting data from equipment sensors. This may involve installing new sensors on existing equipment or integrating with existing data collection systems.
- Choose Maintenance Strategies: Select the most appropriate proactive maintenance strategies based on the type of equipment and the data being collected.
- Invest in Analytics Software: Implement data analysis software that can interpret sensor data, identify potential issues, and recommend maintenance actions.
- Develop Maintenance Plans: Create detailed maintenance plans that outline the specific actions to be taken when certain thresholds are exceeded or anomalies are detected in the data.
- Train Personnel: Train maintenance personnel on how to interpret data, use the new maintenance strategies, and perform proactive maintenance tasks.
- Monitor and Continuously Improve: Continuously monitor the effectiveness of the proactive maintenance program and make adjustments as needed based on real-world data and experience.
How to Transition from Reactive Maintenance to Being Proactive
Transitioning from a reactive to a proactive maintenance approach requires a strategic shift in mindset and operations. Here are some key steps to consider:
- Conduct a Maintenance Audit: Assess your current maintenance practices, identify weaknesses in your reactive approach, and determine your most critical equipment.
- Develop a Cost-Benefit Analysis: Evaluate the potential cost savings and operational improvements achievable through proactive maintenance.
- Start Small and Scale Gradually: Pilot the program on a small scale with critical equipment before implementing it across the entire organization.
- Invest In Training and Reskilling: Train your maintenance personnel on the principles of proactive maintenance, data analysis, and new maintenance techniques.
- Focus On Building a Data-Driven Culture: Encourage data-driven decision-making and continuous improvement throughout the organization.
The Competitive Advantage: Proactive Maintenance for Operational Excellence
Proactive maintenance is a powerful strategy for industrial enterprises seeking to optimize operations, minimize downtime, and maximize equipment lifespan. By adopting a data-driven and preventive approach, businesses can create a more reliable and efficient production environment, ultimately leading to increased profitability and a competitive edge.
The transition from reactive to proactive maintenance may require an initial investment, but the long-term benefits outweigh the costs. By embracing a culture of continuous improvement and data-driven decision-making, industrial enterprises can unlock the full potential of proactive maintenance and achieve operational excellence.
Ready to Transform Your Maintenance Operations?
Innovapptive specializes in mobile-first, connected worker solutions that empower industrial companies and process plants make a smooth transition to proactive maintenance. Schedule a free demo today and see how Innovapptive can help you achieve:
- Reduced Downtime
- Extended Equipment Lifespan
- Improved Maintenance Efficiency
- Cost Savings
- Enhanced Operational Excellence
Take control of your maintenance strategy and contact us today!
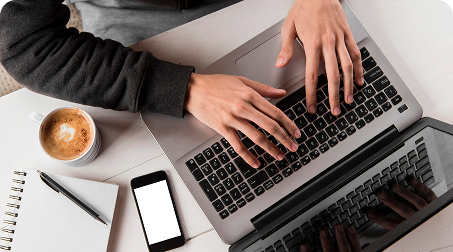
See It In Action
Schedule a personalized demo to see how our solutions can help your business thrive.
Related blogs
- 20-08-2025
Building the future of Industrial Operations with Innovapptive and AWS
Most manufacturers have already gone digital. Yet business outcomes haven’t moved in step. Many...
- 22-04-2025
The $3.6B Unlock: Solving the Chemical Industry’s Labor Crisis and EBITDA Pressure in One Move
“Constraints don’t slow innovation—they force it.”
- 21-04-2025
Chemical Industry's Margin Erosion: A Wake-Up Call for Operational Efficiency Amid China's Oversupply
The global chemical industry is facing mounting challenges, with revenue declines and shrinking...