How Risk-Based Maintenance Optimizes Plant Maintenance
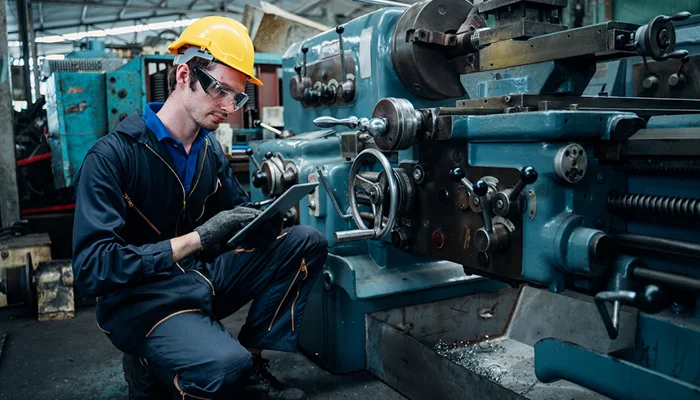
Introduction: Prioritize Critical Assets with Risk-Based Maintenance
In industrial environments, maintenance teams must prevent unexpected equipment failures while ensuring operational continuity and safety. Thousands of pieces of equipment—ranging from large, critical machines to smaller, less essential assets—require precise attention to avoid production disruptions, quality issues, or even workplace accidents.
But how can maintenance teams determine which assets require immediate attention and which can be serviced later? This is where Risk-Based Maintenance (RBM) comes in—a data-driven asset management strategy that optimizes plant maintenance by prioritizing tasks based on the risk associated with equipment failure. With RBM, companies can focus on high-risk assets, ensuring better resource allocation and improved plant efficiency.
What is Risk-Based Maintenance (RBM)?
Risk-Based Maintenance (RBM) is a strategic approach that uses risk assessment to determine which equipment should receive maintenance attention first. It allows maintenance teams to proactively identify potential failures and evaluate their impact on production, safety, and regulatory compliance. RBM enables the prioritization of critical assets, ensuring timely maintenance while reducing unnecessary tasks for low-risk equipment.
The seven key steps in the RBM process include:
-
Data Collection: Gather comprehensive data on equipment, including health indicators, risk of failure, and maintenance history. Modern tools like IoT sensors and CMMS software automate much of this data collection, offering real-time insights.
-
Risk Evaluation: Using data analytics and predictive tools, evaluate the probability and impact of potential equipment failures. Classify assets based on risk severity (low, medium, high, critical).
-
Planning: Develop strategies for risk mitigation, which may include avoiding, transferring, or mitigating the risk in-house.
-
Execution: Maintenance tasks are executed based on asset priority. Field technicians use mobile EAM solutions to access real-time data, ensuring they have the most up-to-date information when performing tasks.
-
Reassessment: Continuously monitor asset health and regularly reassess risks to adjust maintenance plans as needed.
Modern Trends in Risk-Based Maintenance
Risk-Based Maintenance has evolved with technological advancements. Here are some modern trends:
-
Predictive Maintenance: With machine learning and AI, companies can leverage predictive analytics to identify subtle patterns that indicate potential failures. This proactive approach turns reactive maintenance into predictive maintenance, reducing downtime and improving equipment performance.
-
ERP Integration for Maintenance: Seamlessly integrating SAP or IBM Maximo with RBM allows for efficient data exchange and provides maintenance teams with accurate, up-to-date asset information.
-
Mobile Technology: The use of mobile EAM solutions empowers field technicians with real-time access to critical data in the field. Mobile solutions also improve accuracy by allowing technicians to capture new information directly on-site, enhancing overall workflow efficiency.
Benefits of a Data-Driven Risk-Based Maintenance Strategy
Implementing Risk-Based Maintenance offers numerous benefits, including:
-
Reduced Downtime: By predicting potential equipment failures and addressing them proactively, RBM minimizes unplanned downtime and keeps production running smoothly.
-
Improved Production Efficiency: Focusing maintenance efforts on critical assets ensures optimal equipment performance and uninterrupted production.
-
Lower Maintenance Costs: By prioritizing maintenance tasks based on risk, RBM ensures that resources are allocated efficiently, reducing unnecessary maintenance and lowering overall costs.
-
Enhanced Safety: Proactive management of high-risk assets improves workplace safety by preventing dangerous equipment failures.
-
Regulatory Compliance: Regular maintenance of critical assets helps companies meet industry regulations, avoiding costly non-compliance penalties and improving audit readiness.
Innovapptive’s Role in Simplifying Risk-Based Maintenance
Innovapptive’s configurable Mobile EAM solutions streamline the risk assessment process, allowing companies to integrate SAP EAM, IBM Maximo, and other ERP systems into a unified platform. This real-time integration enables maintenance teams to manage asset health, prioritize critical equipment, and allocate resources effectively.
Innovapptive’s mWorkOrder solution offers mobile-enabled features that empower technicians with real-time data access and task management capabilities. With seamless ERP integration, IoT sensor support, and predictive analytics, Innovapptive enables companies to adopt a data-driven risk-based maintenance approach that reduces downtime and boosts plant efficiency.
Ready to enhance your plant maintenance with Risk-Based Maintenance? Schedule a free demo today to learn how Innovapptive’s mobile EAM solutions can optimize your maintenance operations.
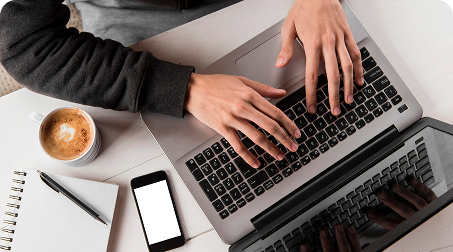
See It In Action
Schedule a personalized demo to see how our solutions can help your business thrive.
- 20-08-2025
Building the future of Industrial Operations with Innovapptive and AWS
Most manufacturers have already gone digital. Yet business outcomes haven’t moved in step. Many...
- 22-04-2025
The $3.6B Unlock: Solving the Chemical Industry’s Labor Crisis and EBITDA Pressure in One Move
“Constraints don’t slow innovation—they force it.”
- 21-04-2025
Chemical Industry's Margin Erosion: A Wake-Up Call for Operational Efficiency Amid China's Oversupply
The global chemical industry is facing mounting challenges, with revenue declines and shrinking...