COVID-19 Response: 7 Advantages of Mobile Technology for Preventive Maintenance Optimization
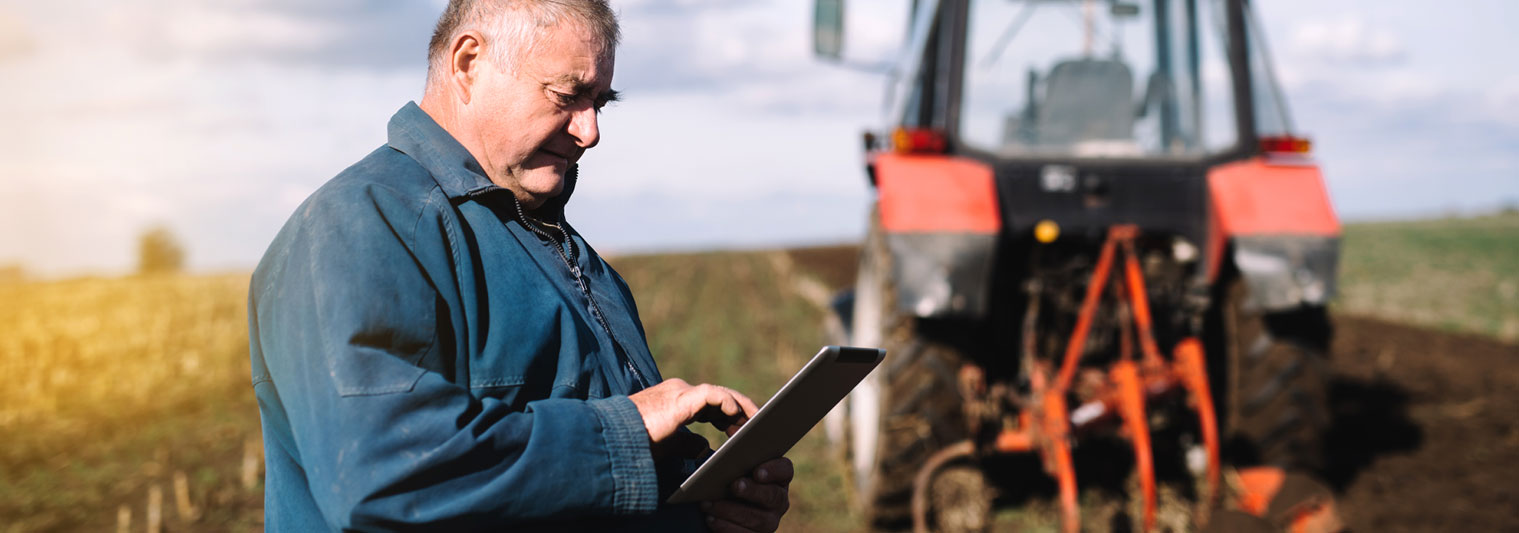
The COVID-19 pandemic has brought the world economy almost to a standstill as the industrial sector is the worst hit by the crisis. Maintenance is a key influencer in industry operations and requires transformation to achieve more productivity with limited resources to survive this crisis. To optimize preventive maintenance operations, companies should embrace mobile technology that will enable better data capture and increase tool time. This technology ought to be easy to use and accessible by maintenance trades persons in every discipline (electrical, mechanical, diesel, civil).
Advantages of mobile technology in preventive maintenance optimization:
1. Portability
A front-line worker equipped with PDAs such as a smartphone, tablet, or scanner can go virtually anywhere within a company. They can digitally collect and transfer valuable information without ever having to fill out a paper form or a spreadsheet. A good mobile solution will even enable data collection in offline mode, syncing up when internet connection is available. Finally, a front-line worker doesn’t need to return to headquarters or a field-office to receive work instructions or to update supervisors on job progress. Managers can electronically issue work orders, prioritize tasks and review job status via desktop or mobile dashboards.
2. Productivity
Mobility reduces the time spent on things other than measurable work. It’s estimated that two-thirds to three-quarters of a craftsperson’s time is wasted on non-productive effort. Only 25-35 percent is devoted to actual wrench time. That means in an eight-hour day a craftsperson is doing less than two hours and 45 minutes of the work expected. The remaining time is spent preparing, transitioning or waiting for instructions, materials and equipment. Mobility reduces that wasted idle time. Workers can spend more time doing and less time waiting, improving wrench time and productivity while reducing costs and duplicated efforts.
3. Ease of use
Various surveys have discovered that only a quarter of the surveyed front-line employees felt SAP was easy to use in their role. Nearly half responded it was either difficult or exceedingly difficult to use SAP. About 60 percent of the staff took between one and five hours to input data into SAP each week. One-in-five took longer than five hours per week.
A mobile-first solution cuts down on the administrative task of inputting data into SAP. Instead, data is electronically collected in the field using handheld devices and automatically relayed to managers and supervisors via SAP to desktop dashboards.
4. Data accuracy
Data inaccuracy is most keenly felt in field inspections. Paper-based, unstructured inspections, disconnected from a system of record like SAP, can create data integrity issues around asset risks, threats and failure.
A mobile-first solution increases data accuracy and confidence as information is collected directly in the field by front-line workers and relayed in real-time back to decision-makers. There is no need to decipher bad handwriting, no searching for missing sheets or forms, no binders to file or carry.
5. Collaboration
Mobility provides greater connectivity at every level of an enterprise. This eliminates troublesome information silos and approval bottlenecks. Data is shared freely and is more accessible. No one is operating in the dark or making uneducated guesses. Instead, data is verified in the field and shared in real-time, providing greater visibility into operations and giving everyone a clear picture of where the company stands at that moment. Now groups can better work together. They can spot trends, identify problems, devise solutions and drive operational efficiencies enterprise wide, not just in their specific area.
6. Real-time solutions for real-time problems
With mobile devices and digital checklists, technicians can perform faster, more-thorough operator rounds and inspections. These checklists can be immediately reviewed by key decision-makers via dashboards. This gives maintenance managers, planners and directors the real-time data they need to spot minor problems before they turn into serious ones that cause unplanned and expensive shutdowns. Preventative maintenance teams can now extend asset life. No more reactively running the equipment to failure, which could result in costly replacement rather than repair.
7. Prevent the spread of COVID-19 and other diseases
Mobile technology replaces paper, which is a carrier of many viruses. PDAs and digital checklists enable workers to receive work orders even without visiting the administration building or meeting people. This empowers new social distancing norms and ensures occupational safety in the agriculture sector.
At Innovapptive, we created a mobile-first work-order management solution called mWorkOrder that helps companies manage operational risks in a time of crisis. mWorkOrder is powered by a patented, “code-free” platform that allows you to immediately respond to business and regulation changes. It empowers maintenance workers to work safely, productively and independently. The solution can be integrated with PDA (Personal Digital Assistants) such as smartphones, tablets, wearables, and barcode scanners.
To see how mWorkOrder will help you optimize your preventive maintenance operations: [Request live demo]
For more details, visit www.innovapptive.com or call 1-844-464-6668 to talk to our experts.
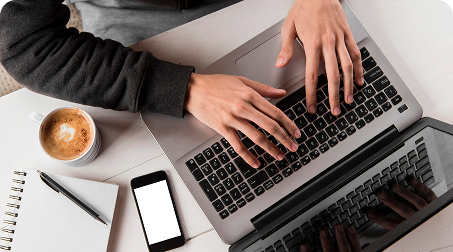
See It In Action
Schedule a personalized demo to see how our solutions can help your business thrive.
- 22-04-2025
The $3.6B Unlock: Solving the Chemical Industry’s Labor Crisis and EBITDA Pressure in One Move
“Constraints don’t slow innovation—they force it.”
- 21-04-2025
Chemical Industry's Margin Erosion: A Wake-Up Call for Operational Efficiency Amid China's Oversupply
The global chemical industry is facing mounting challenges, with revenue declines and shrinking...
- 21-04-2025
Why Wrench Time Isn’t Improving: The Hidden Costs of Traditional Maintenance Scheduling
For years, industrial leaders have relied on a common but flawed assumption: "Better planning and...