Delivering the Promise of Making your Plant Maintenance More Efficient
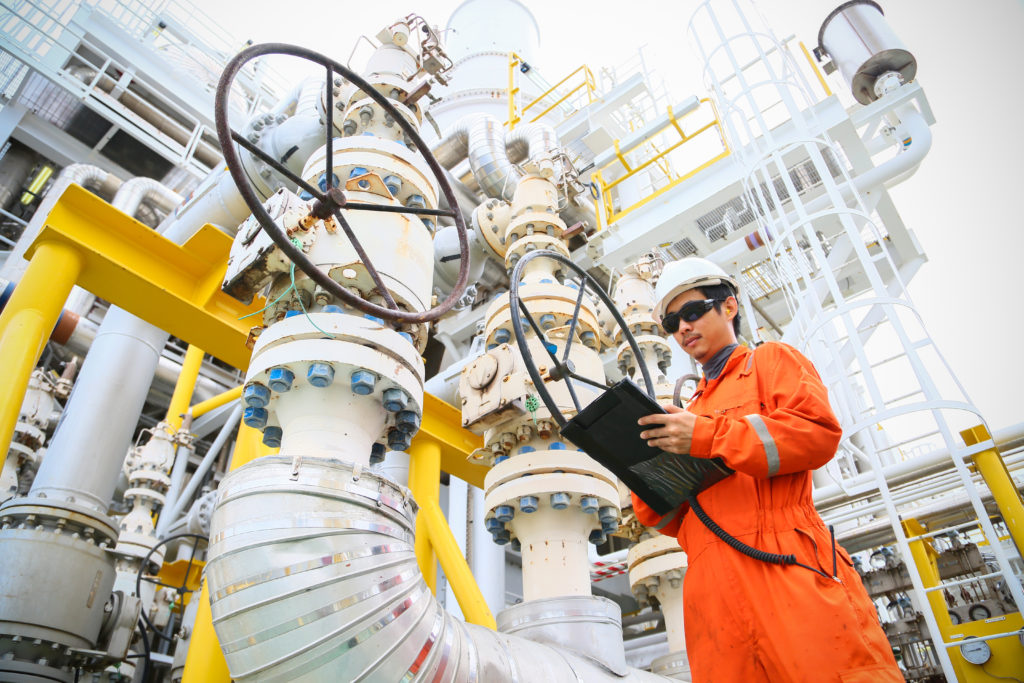
While technology is continuously changing human lives in every area, the struggle for asset-intensive industries didn’t stop yet. The industry around the world is under intense financial pressure, and plant maintenance budgets need to be cut. An asset with high performance and reliability is the backbone of any business. Usually, many companies have assets, which are spread across a wide geographic area, and overseen by a field-based workforce.
The key to efficient plant maintenance is performing the maintenance/repair at the right time with right information. However, organizations that are not yet mobile, are losing valuable wrench time and their field and maintenance workers don’t get the access to information when they really need it. It leads to delayed processes, frustration and ineffective maintenance approach. Sometimes, workers/technicians need to execute maintenance work from outside the office in different locations. It becomes difficult for them to manage all from their wired systems. All they need a simple app with easy navigation. Managers/plant heads always need to achieve higher operational efficiency and ROI so that they can keep costs under control and achieve profits.
Mobility is changing the game at Asset-intensive companies.
Mobility has been proved a great solution to these problems. It enables the organization to empower their workforce with everything they need to efficiently install, inspect, maintain, and repair assets in the field. Mobility provides plant managers better visibility and improved analytics that help in quick decision-making. The mobile application for plant maintenance enables your maintenance/field workers to carry the right information on their mobile devices and access more information from anywhere, anytime. The application generates notifications when the new work orders or any tasks get assigned to them. It also allows workers/technicians to capture real-time data direct from the field and enables them to complete their transaction and sends reports. These days mobile application is coming with GIS/GPS support that helps them to reach the exact location. Moreover, the right mobile application for plant maintenance also guides workers/technicians to follow the correct steps and get real-time data in the field. With the offline access, you can ensure delivery of mission-critical support of assets without any interruptions or delays, leading to better performance and reliability across plants, networks, and the enterprise infrastructure.
Going mobile delivers great benefits, organizations can expect to:
- Simplify maintenance transaction, eliminate paperwork, and improves accuracy
- Reduce unplanned downtime, lower annual maintenance costs and increases asset life
- Shorten maintenance time and increase users’ as well as business productivity
- Enhance operating equipment effectiveness and Increase asset availability
- Empower workforce with the right information & help executives and managers to make better, more informed decisions
Mobilize Your SAP Mobile Plant Maintenance & Work Order Processing: mWorkOrder
Innovapptive’s mobile EAM portfolio is the most configurable enterprise-grade SAP Mobile Plant Maintenance solution on the market. It gives you the power to improve capital asset management in ways that increase reliability, enhance predictive maintenance, ensure regulatory compliance, reduce energy usage, and support sustainability initiatives.
The mWorkOrder mobile solution delivers an intuitive and seamless user experience for your central dispatchers to pro-actively schedule and assign work orders or notifications to maintenance technicians. Your technicians can instantly be alerted through push notifications when they are assigned a new work order or notification. This helps them manage priorities in real time, to avoid any potential equipment failure, unexpected downtime, safety, and environmental risks, all of which negatively impact revenue and equipment uptime. Fully configurable with RACE™, it gives you unparalleled flexibility to zero in on the specialized, industry requirements that can turn your company’s asset management into a competitive advantage. This SAP® Certified solution leverages the SAP Plant Maintenance (PM) module at the back-end to deliver a consistent, reliable and a productive asset maintenance experience across a wide range of industries.
If you would like a demo of Innovapptive’s Mobile Solution, please click on the request live demo link. Alternatively, if you would like to discuss with an Innovapptive solution expert, you can reach out to us by emailing us at sales@innovapptive.com or you can reach a sales representative at (713) 275-1804.
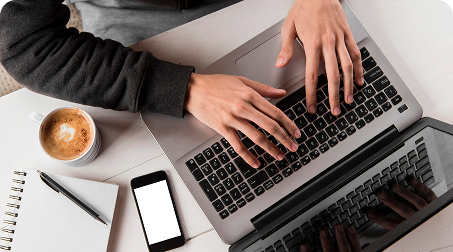
See It In Action
Schedule a personalized demo to see how our solutions can help your business thrive.
- 22-04-2025
The $3.6B Unlock: Solving the Chemical Industry’s Labor Crisis and EBITDA Pressure in One Move
“Constraints don’t slow innovation—they force it.”
- 21-04-2025
Chemical Industry's Margin Erosion: A Wake-Up Call for Operational Efficiency Amid China's Oversupply
The global chemical industry is facing mounting challenges, with revenue declines and shrinking...
- 21-04-2025
Why Wrench Time Isn’t Improving: The Hidden Costs of Traditional Maintenance Scheduling
For years, industrial leaders have relied on a common but flawed assumption: "Better planning and...