Get instant visibility into every work order with a Kanban-style dashboard. Track progress, spot delays, and streamline assignments—all in one place.
Know what’s happening, fix what’s not.
Actionable Maintenance Insights for Maximum Asset Reliability
Convert frontline data into real-time insights for cost savings, asset health, and maintenance KPIs
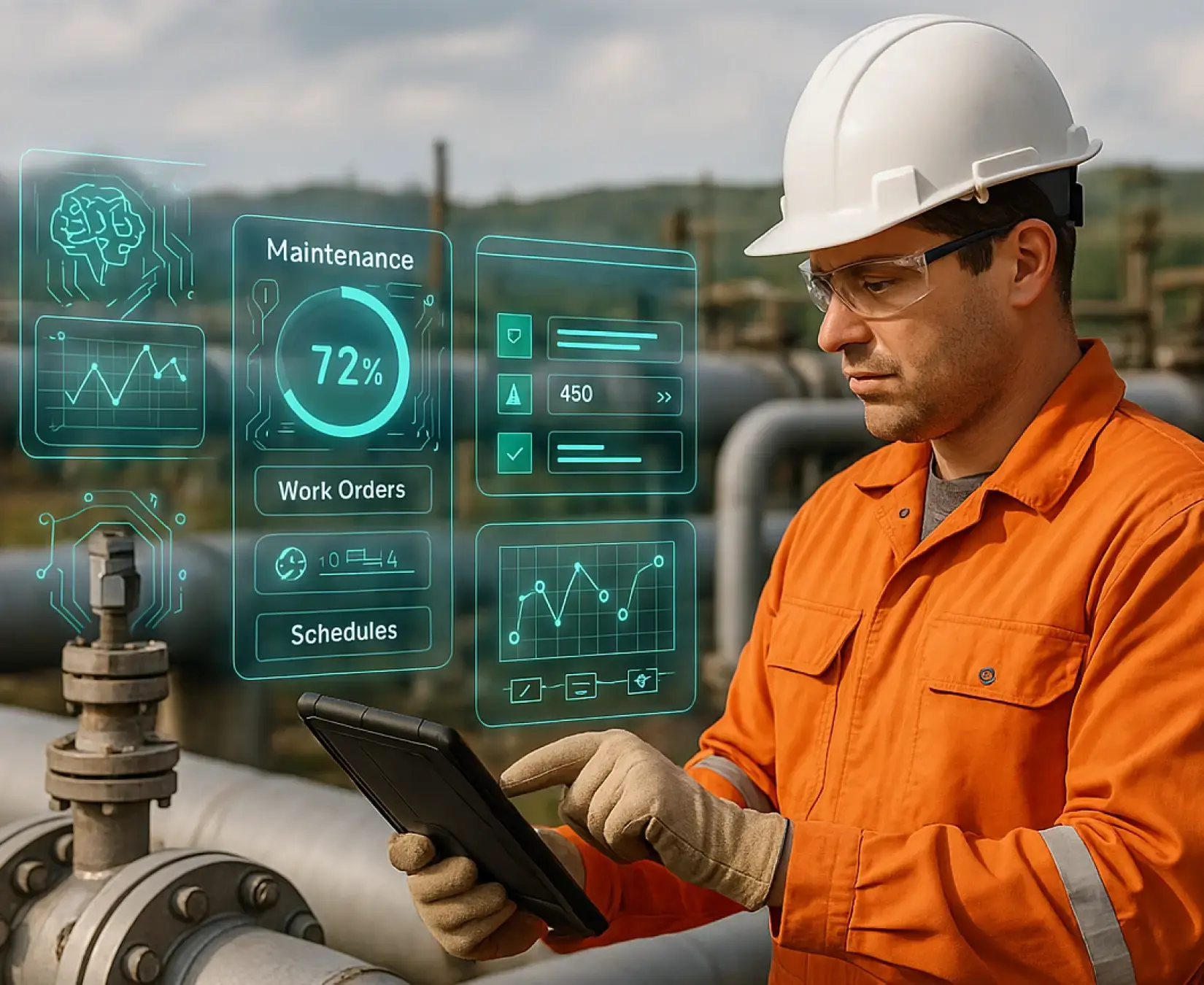
Trusted by Industry Leaders to Drive Operational Efficiency
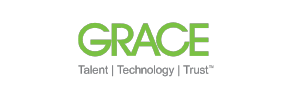
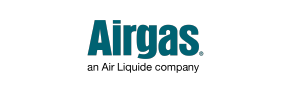
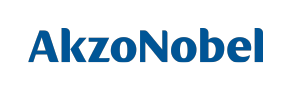
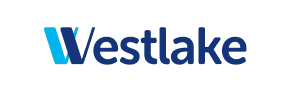
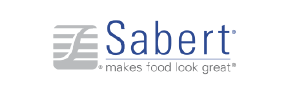
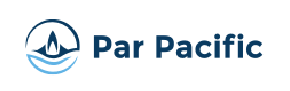
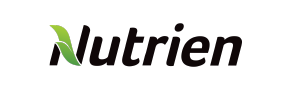
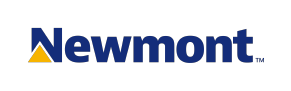
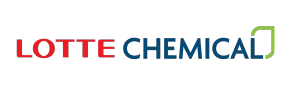
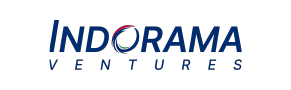
Simplify maintenance with AI-powered insights and end-to-end visibility.
.webp)
.webp)
.webp)
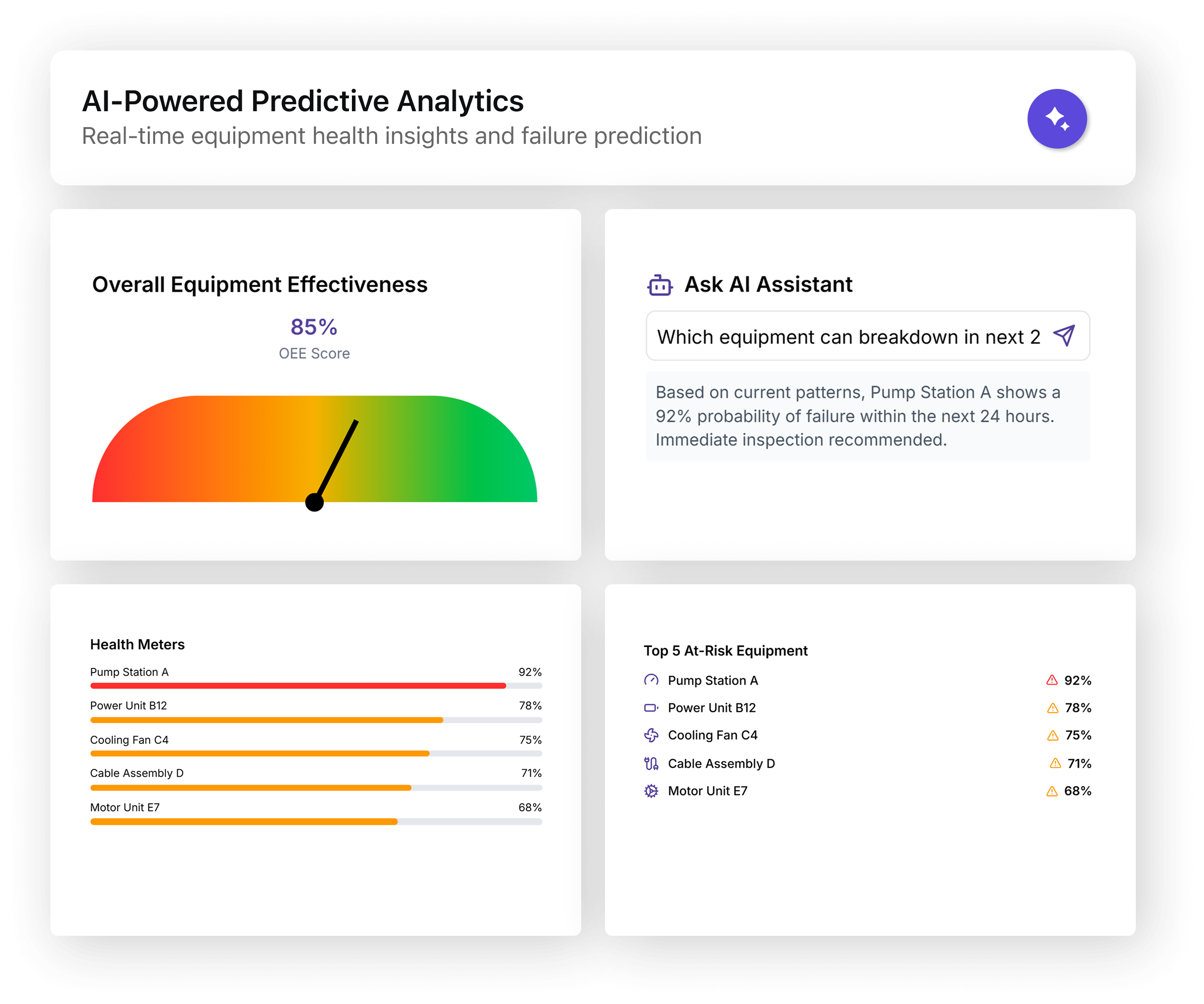
Maintenance Control Center
Supervisor Daily Dashboard
Get a clear view of field execution—what’s complete, what’s delayed, and who needs support. Track technician progress, work order status, and daily priorities in one unified dashboard.
Make faster decisions. Keep your crew on track.
Real-Time Equipment Diagnostics
Keep tabs on asset health in real time—from pressure trends and temperature spikes to operating hours and location data. Quickly spot anomalies, compare against baselines, and take action before issues escalate.
Less guesswork. More uptime.
Predictive Maintenance Intelligence
Leverage AI to monitor equipment health, forecast failures, and prioritize inspections—before downtime hits. With real-time OEE scoring, risk-based rankings, and AI-driven alerts, your team can act on what matters most.
From reactive fixes to proactive decisions.
Cut Equipment Failures by upto 40% with AI-Powered Predictive Analytics
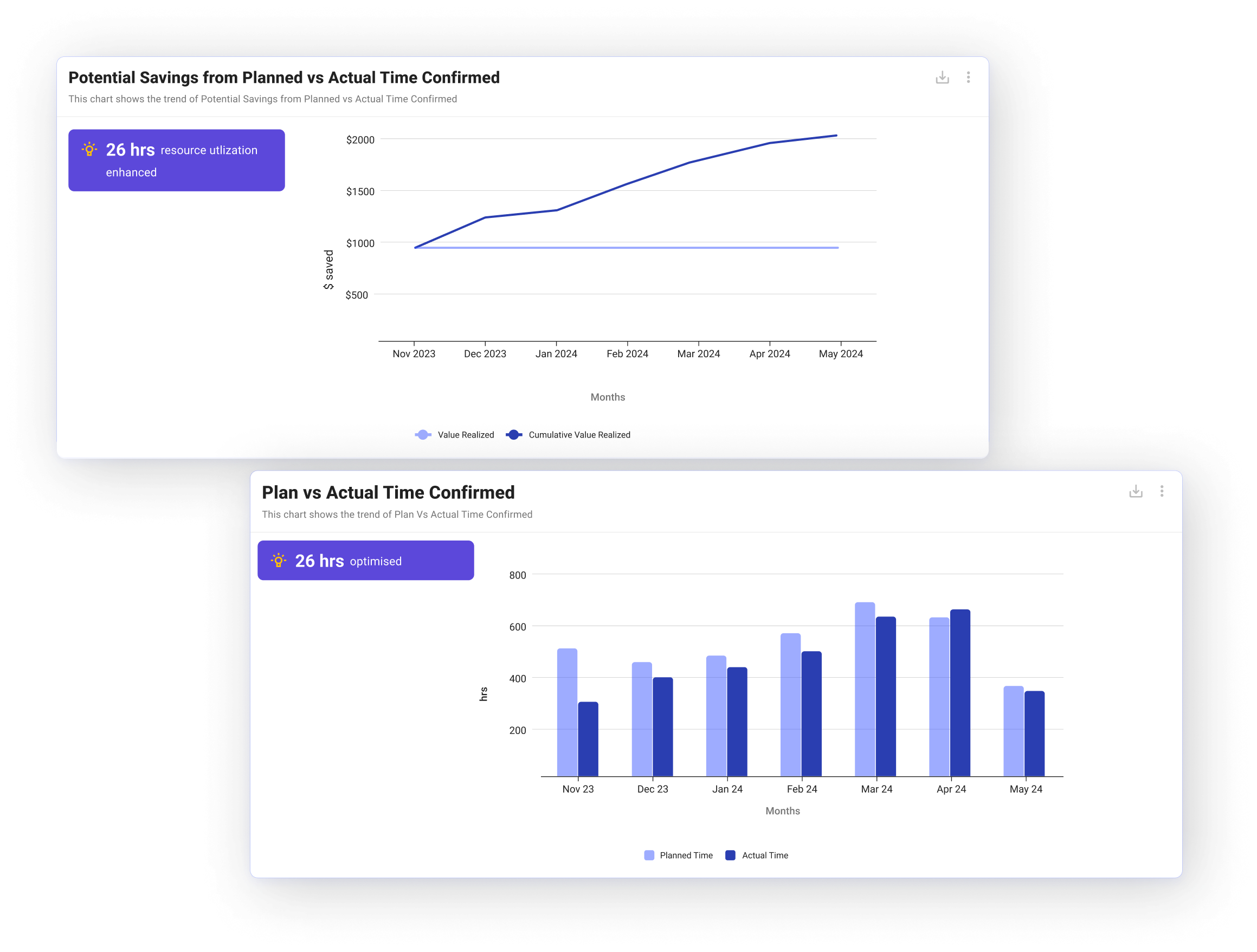
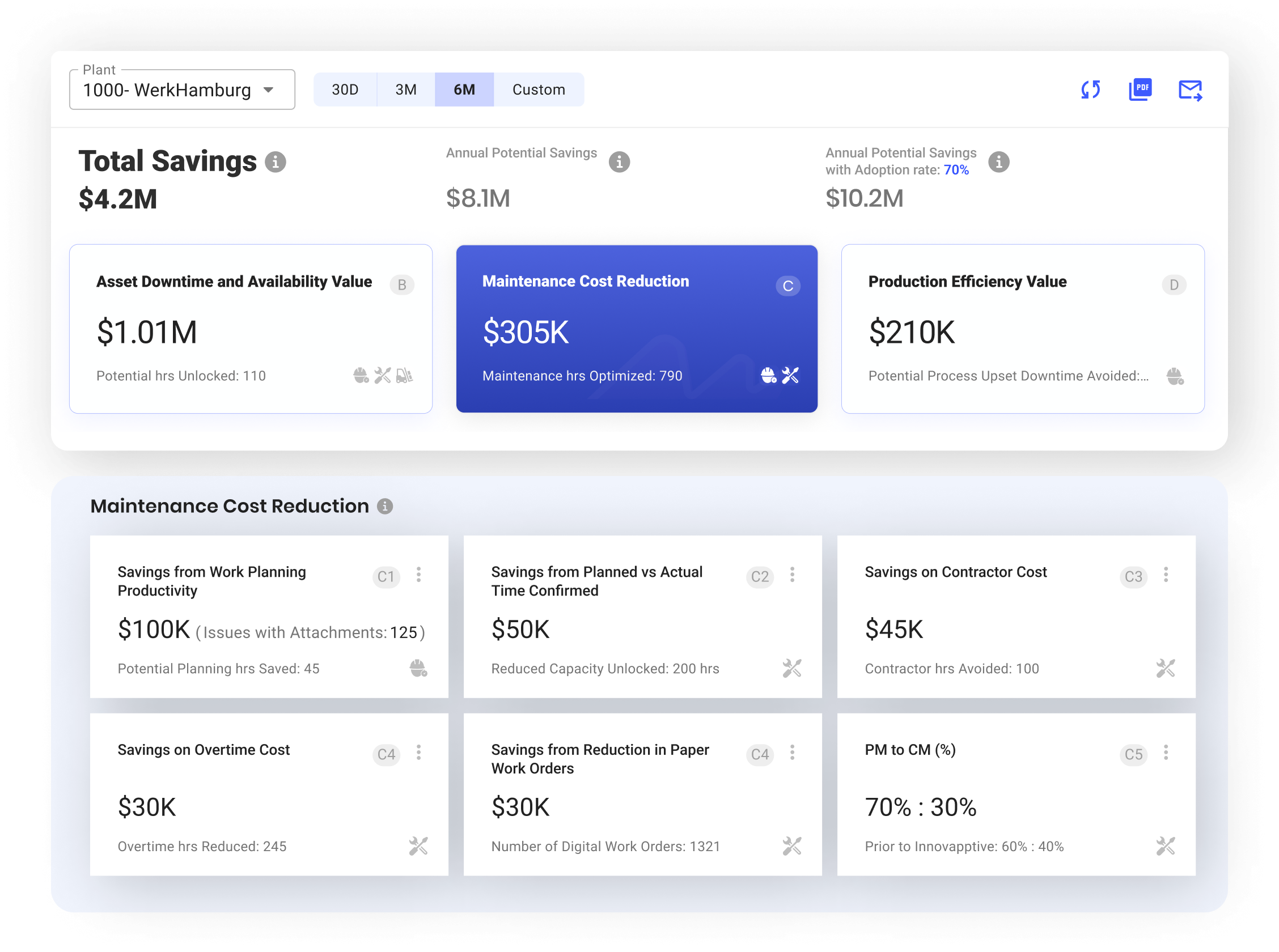
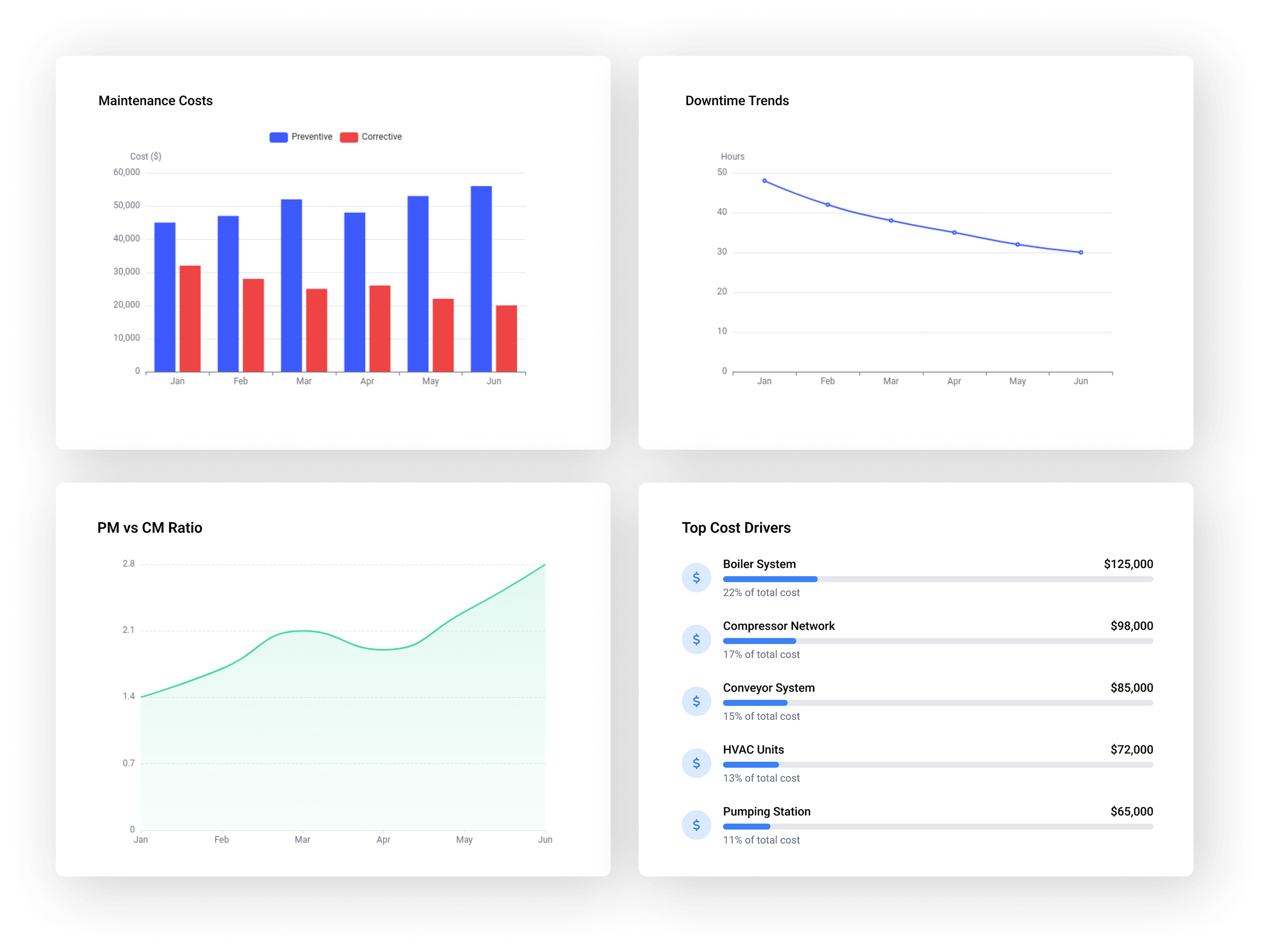
Live Maintenance Insights
Measure and maximize workforce efficiency by comparing planned vs. actual execution. Discover hidden delays, validate productivity, and turn time savings into cost impact.
- Track KPIs like MTTR, MTBF & downtime – all in real time
- Quantify hours saved and cost impact
- Improve planning accuracy over time
360° Value Intelligence Hub
Quantify where your maintenance dollars go—and where they shouldn’t. The Value 360 dashboard breaks down cost reductions, efficiency gains, and time savings into clear, actionable insights.
- Track total savings across downtime, labor, and productivity
- See cost breakdowns by overtime, planning, contractors, and paperwork
- Identify optimization levers tied directly to ROI
Reliability ROI & Cost Drivers
Monitor where your maintenance dollars are going—and how reliability is improving. Track cost trends, downtime reduction, and top asset cost drivers to optimize performance.
- Compare preventive vs. corrective maintenance spend over time
- Track PM-to-CM ratio to assess reliability maturity
- Identify top cost-driving assets to prioritize improvements
Proven Results for Industrial Maintenance Teams
-
35%
Reduction in Unplanned Downtime
-
$4.2M
Annual Savings on Maintenance Costs
-
12,000+
Users Empowered with AI Insights
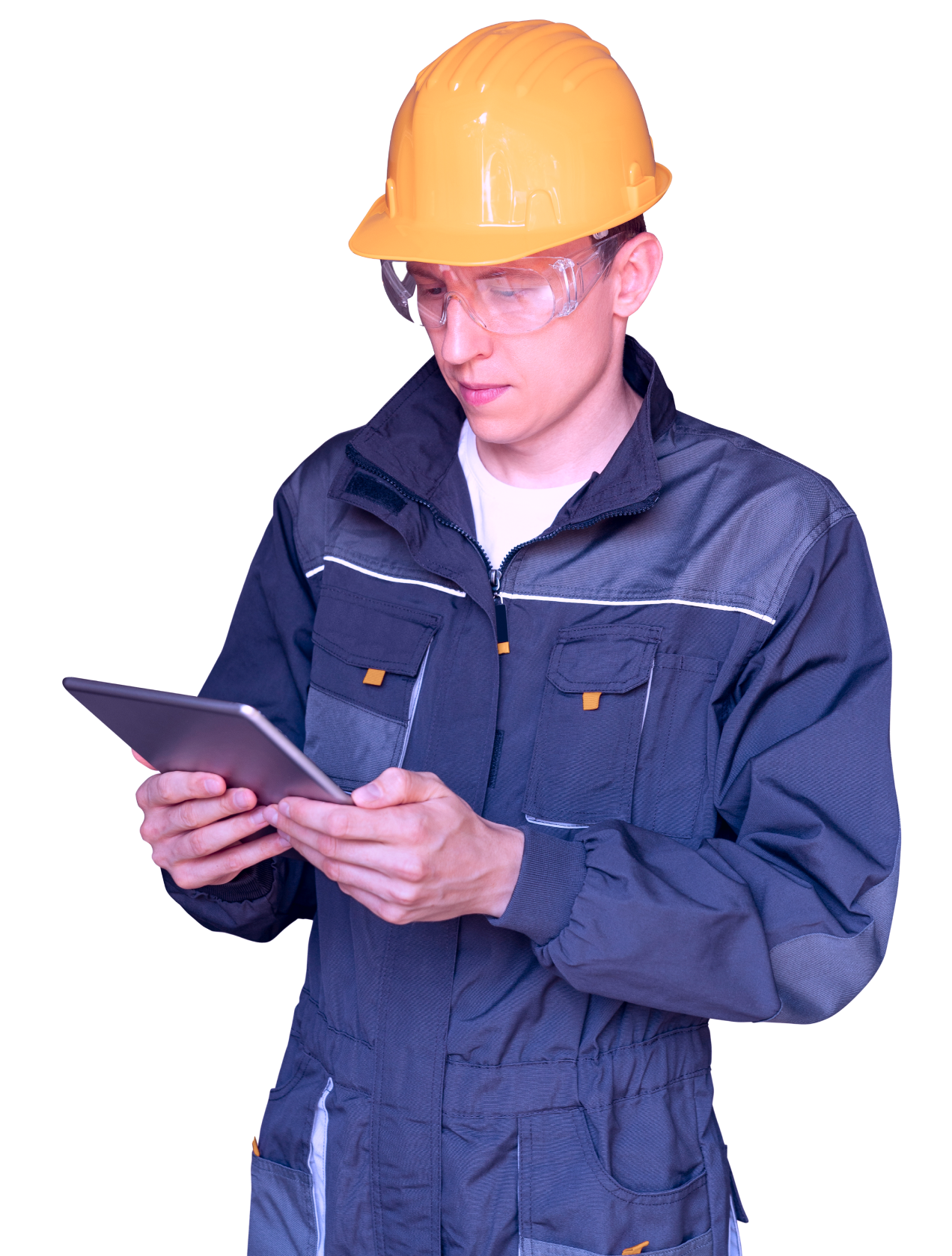
Unlock Smarter Maintenance Decisions with WorkSmartAI™.
WorkSmartAI™ delivers real-time insights by analyzing asset health, technician performance, and work order history. It spots hidden inefficiencies, predicts failures before they occur, and recommends the fastest, most effective actions—helping your team boost uptime, ensure compliance, and reduce costs.
Know More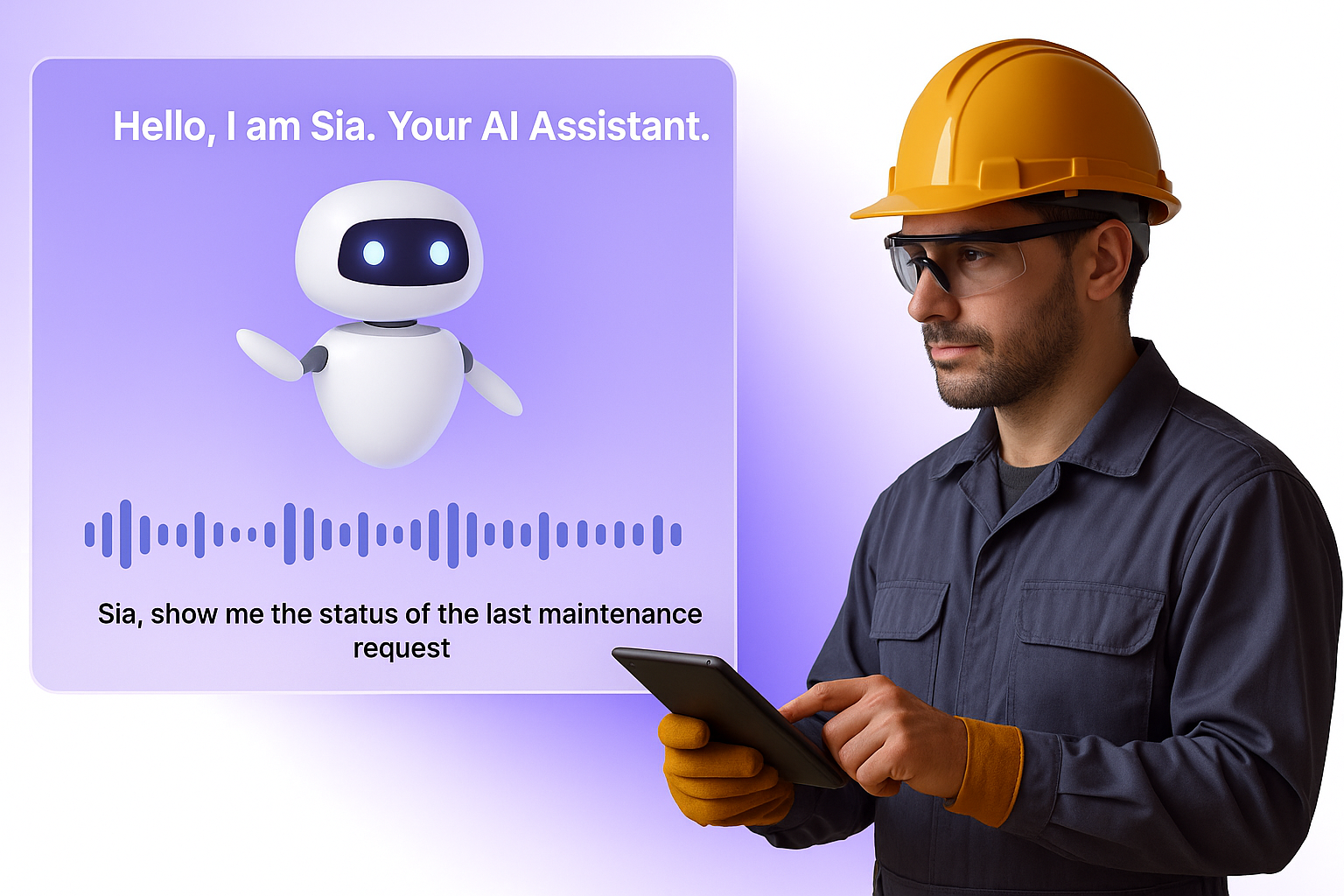
Real Stories. Real Impact. See How Industry Leaders Succeed with Innovapptive.
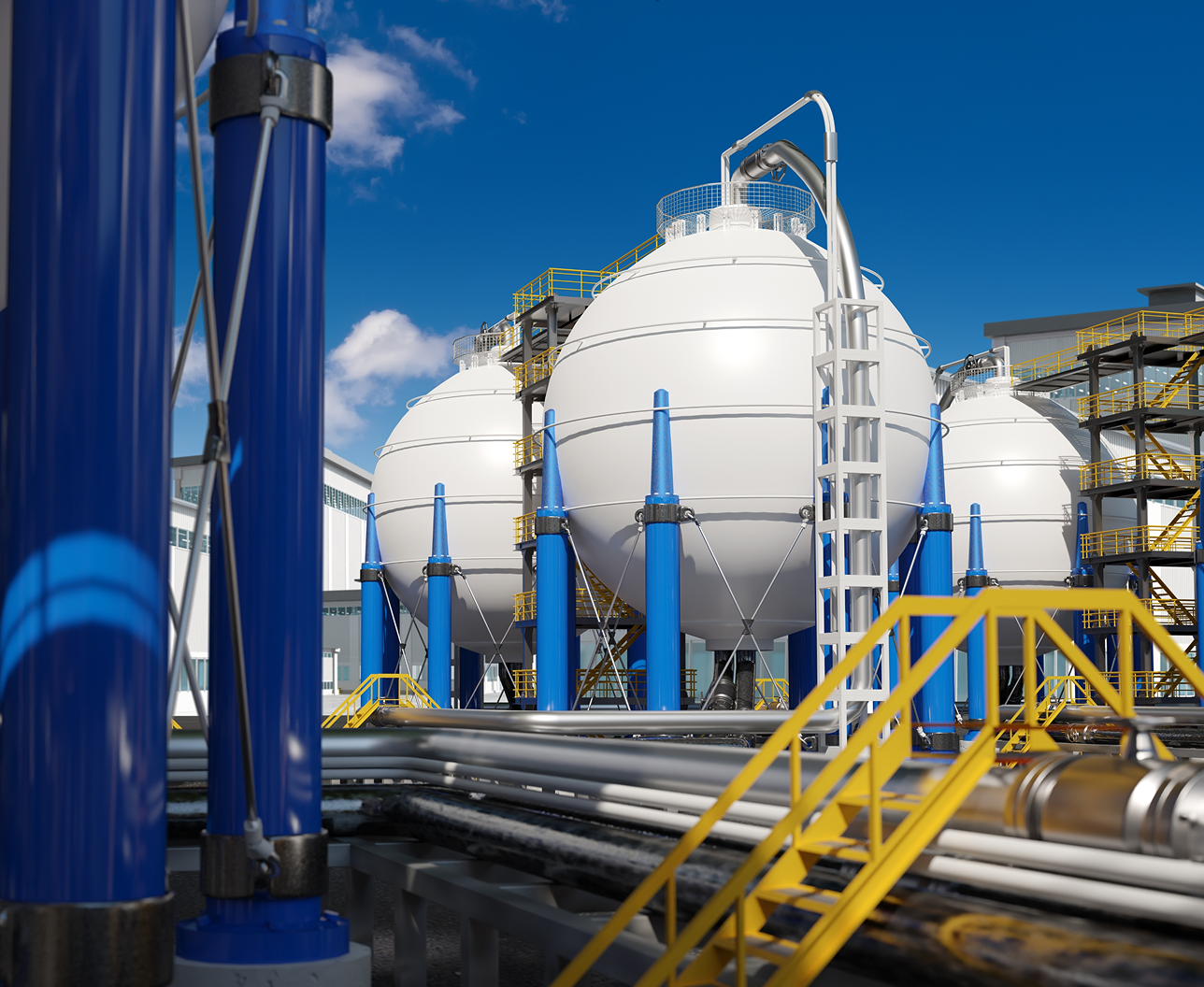
"The user experience has been fantastic. Our operators have adapted to using the device for operator rounds very easily. Even some of our folks who have been here 30-35 years experienced can pick up the device and use it."
Micah Mosley
Operational Excellence Manager, Indorama Ventures

"“I appreciated the sales, project, and executive teams' great efforts for the company win. It's the best solution and a very trusted and strong partnership for the company - a big win.”
Jinmoon Son
IT Manager, Lotte Chemical USA

"Innovapptive mobile solutions are great. They’re a one-stop shop for all the engineering activities and administrative duties. They allow us to keep everything current and up to date."
Lee Whiteley
Regional Field Operations Manager, AkzoNobel
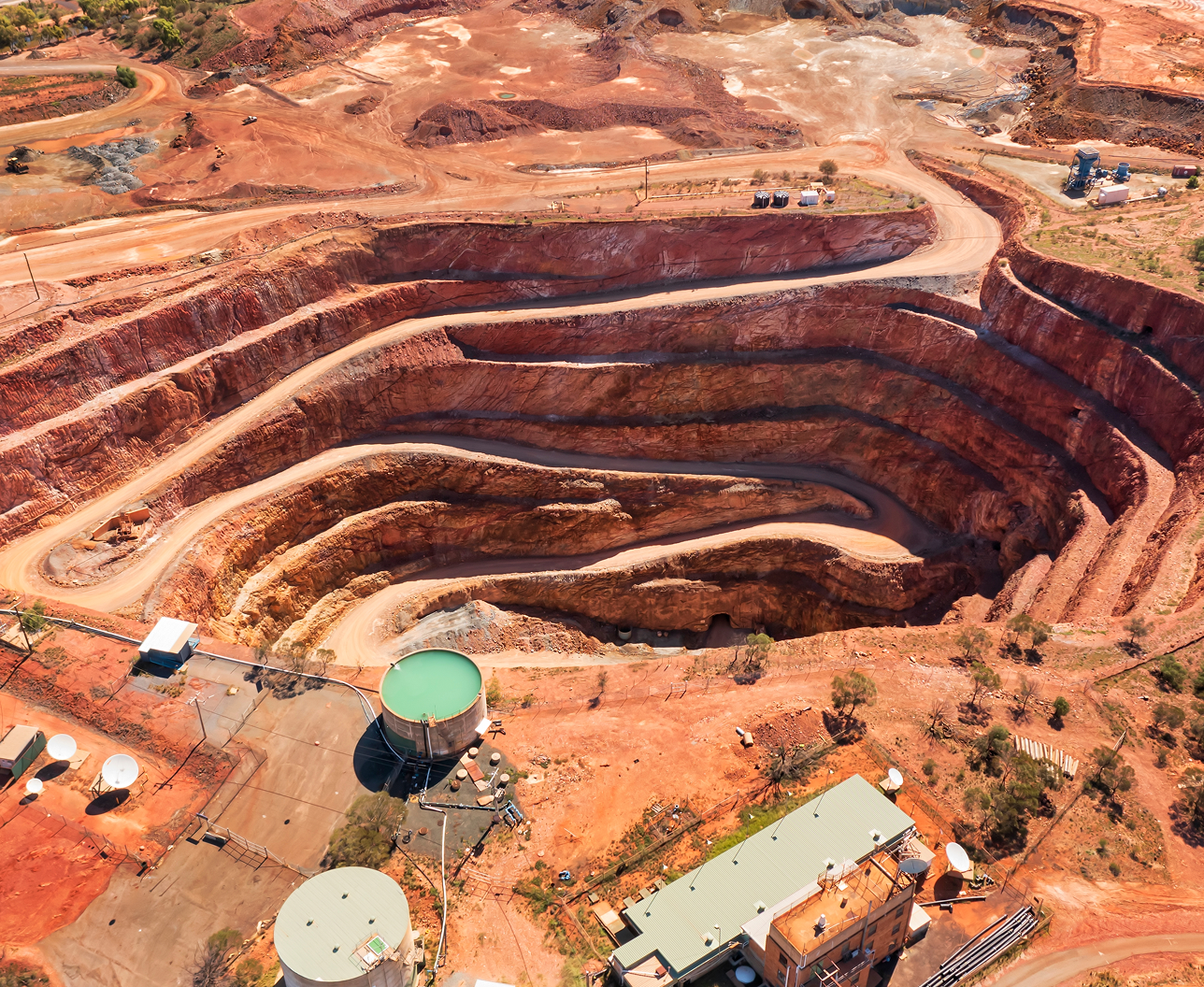
"We hadn’t had much luck with mobile plant maintenance solutions in the past. Our frontline maintenance technicians didn’t want to use them because of poor UI/UX. They’d rather use paper, meaning we received a poor return on investment and achieved none of our operational objectives."
Cary Brunson
Principal Advisor, Asset Management at Newmont Mining
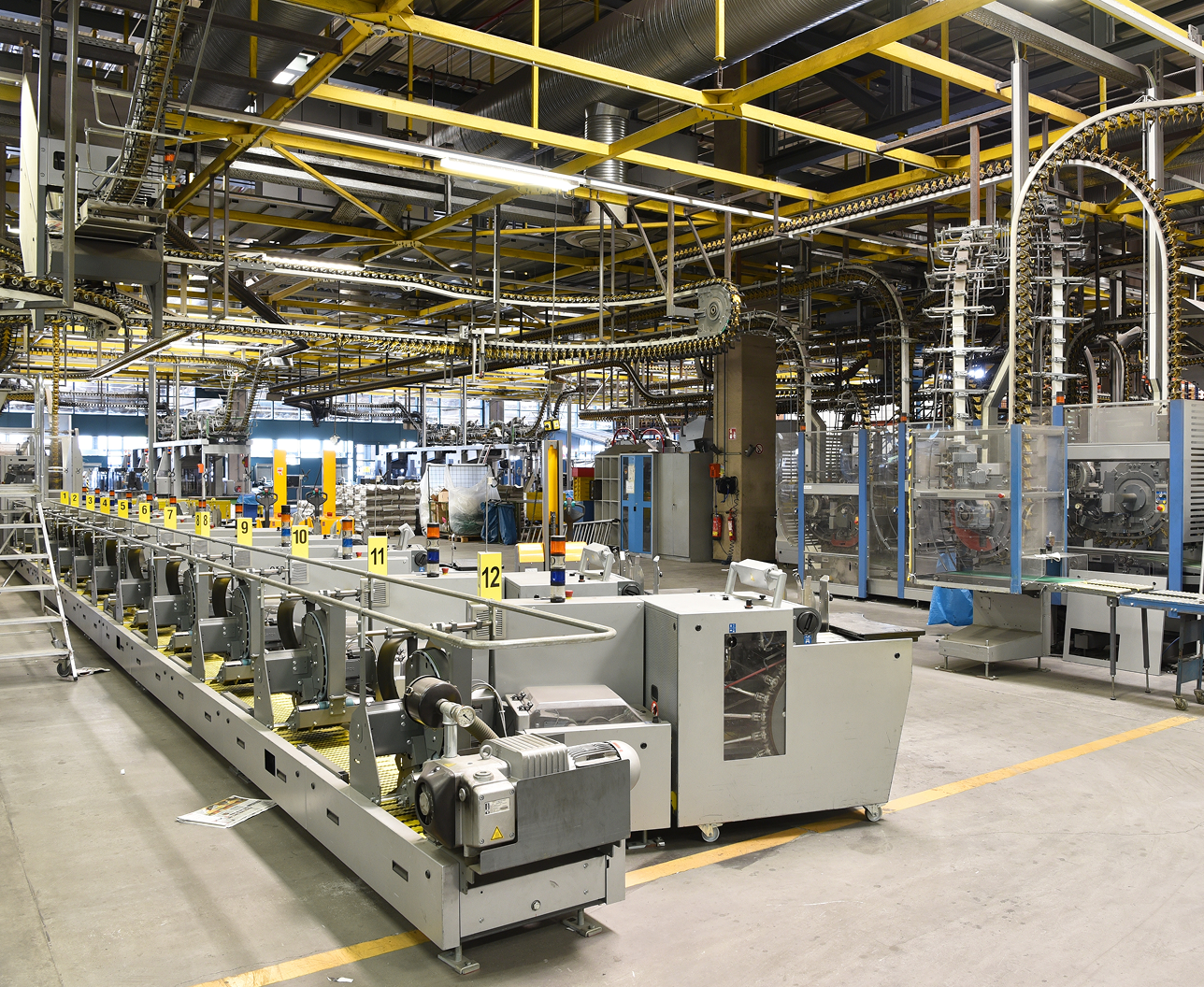
"We wanted to make our workers more autonomous, independent, and proactive. We wanted to give them data at their fingertips. With Innovapptive’s mobile maintenance solution, they’ll get that."
Emily Hebert
Director of Operational Excellence, Sabert Corp.
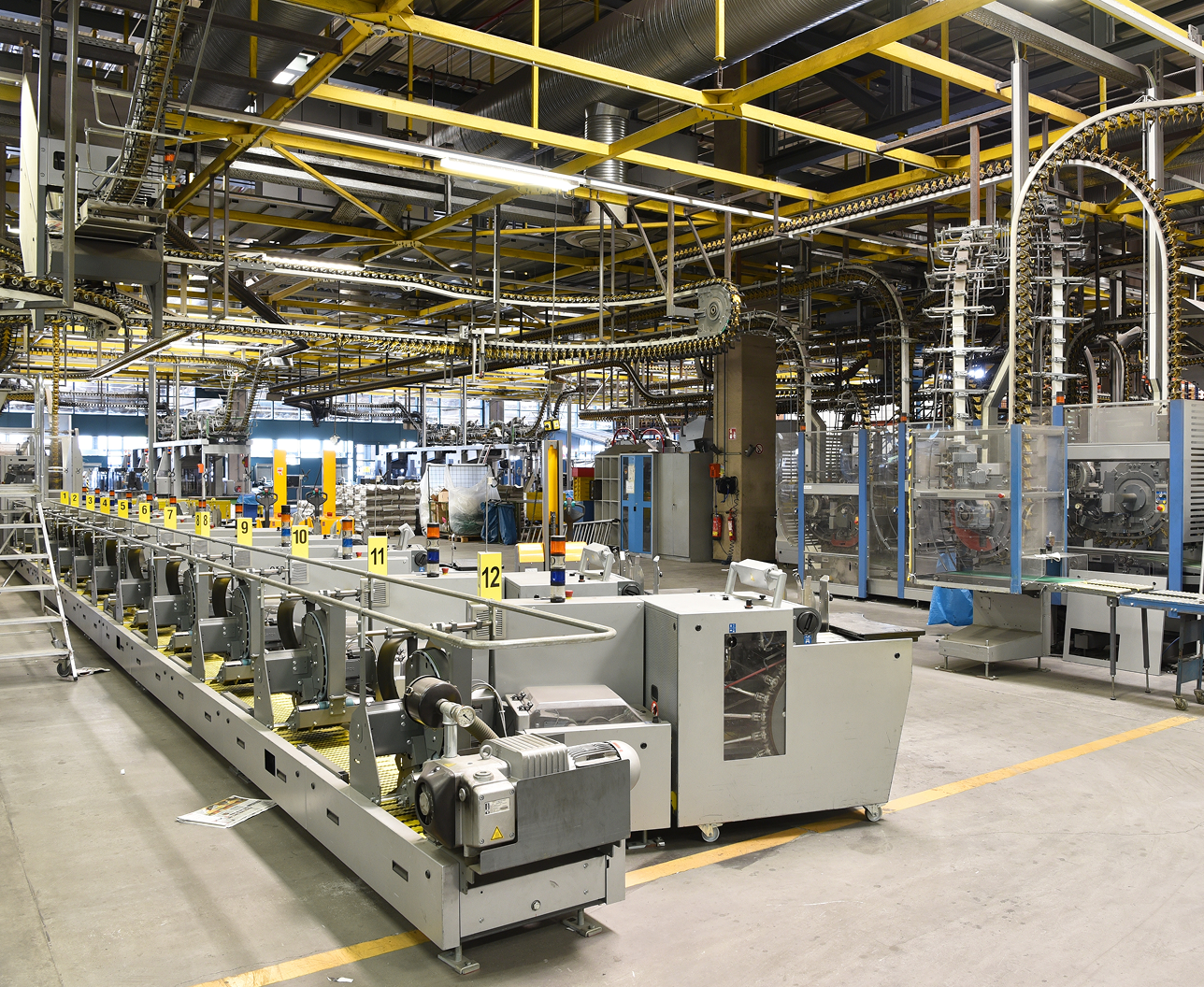
"One of the greatest benefits has been our ability to index over 1,200 photos and 420 videos in just 3 years, directly during work order execution. This has made information transfer smoother and has helped standardize work order templates across operations."
Thierry Copin
Director of Continuous Improvement, Tafisa Canada
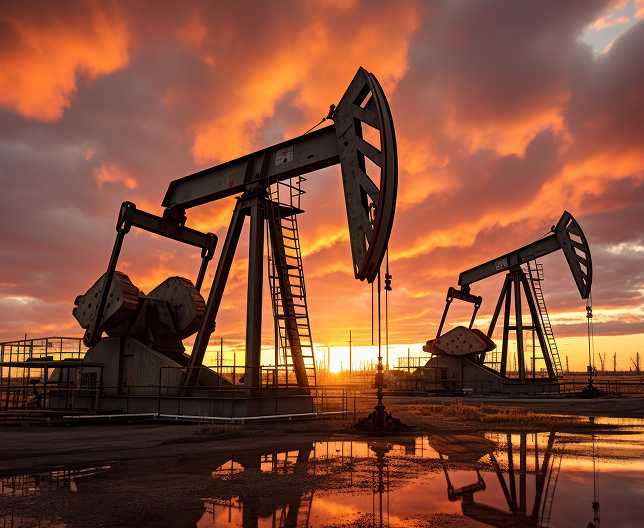
"Since the start of the project we have been nothing but pleased with the quality of the service we've received from Innovapptive. The whole team from the sales team to the project team have been nothing but supportive"
Christopher Lathrop
Enterprise Solution Architect, Par Pacific
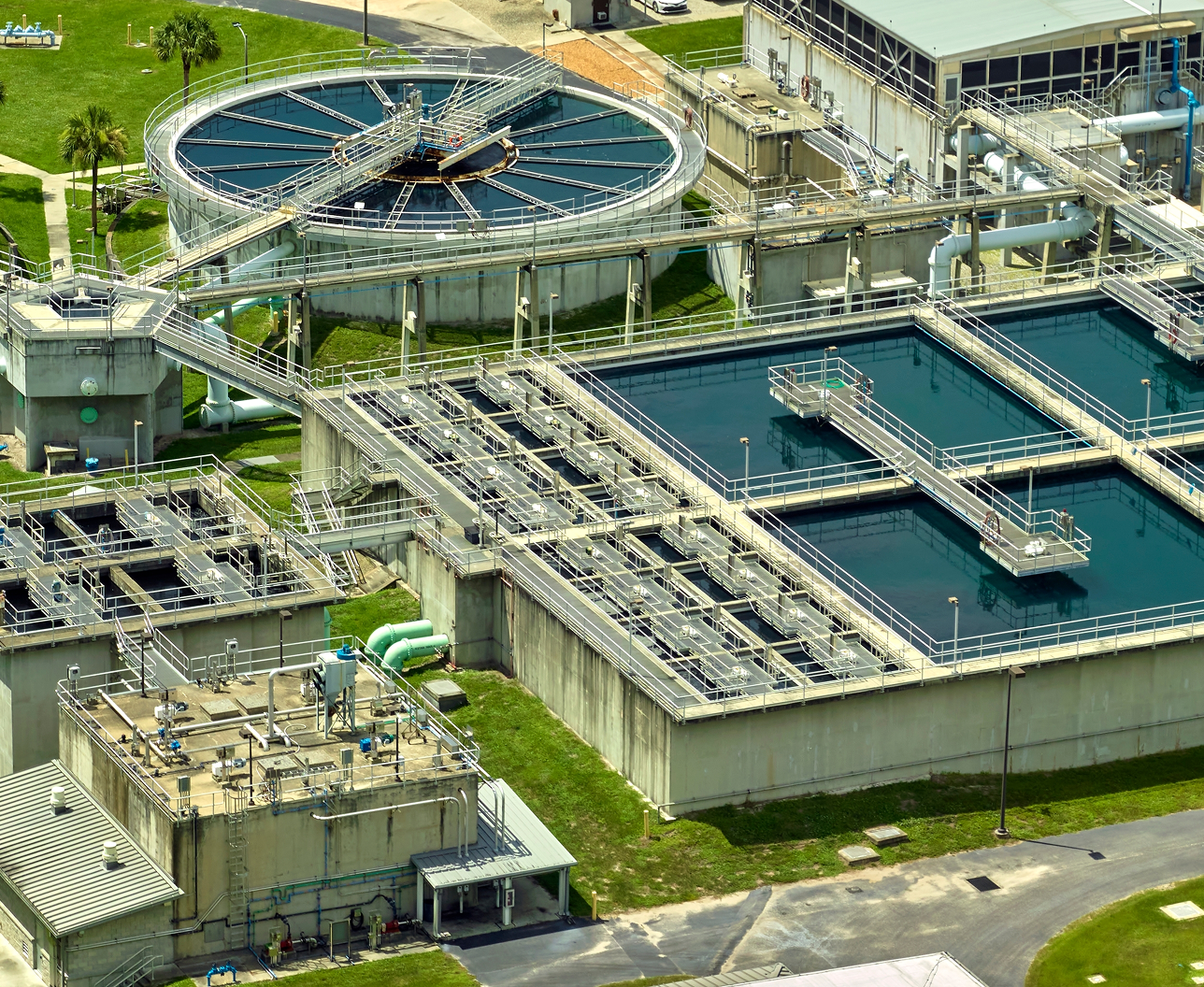
“I’d say hands down, that was the best technology implementation in project management. Everything was on time, on budget. Quite frankly, I hadn’t seen anything like it before in my 10+ year career. I loved it."
Alton Echols
Director of O&M Programs, Loudoun Waters
Improve Maintenance Efficiency, Eliminate Downtime Surprises.
.webp)
Single Pane of Glass
Manage work orders, digital permits, and spare parts inventory in a unified system. Gain real-time visibility into end-to-end maintenance workflows—eliminate silos.
.webp)
AI-First Workflows
Access AI agents like AI Plan for automated work orders, AI Detect for real-time issue detection, and AI Assist for troubleshooting guidance—enhancing efficiency and reliability.
.webp)
Connected Systems
Seamlessly integrate with top ERPs like SAP and IBM Maximo, along with historical asset data, for predictive maintenance and automated workflows.
.webp)
Value 360 Implementation
Deploy faster with Innovapptive’s structured Value 360 model, ensuring measurable impact. Accelerate adoption, maximize ROI.
Have Questions? We’ve Got Answers!
How does Asset Condition Monitoring prevent unexpected equipment failures?
Asset Condition Monitoring uses real-time data to track the health of equipment, detecting early signs of wear or malfunction. By analyzing trends and failure patterns, predictive maintenance systems can alert teams to potential issues before they result in unexpected breakdowns, reducing unplanned downtime and costly repairs.
What are the benefits of Predictive Maintenance Analytics in oil and gas?
In the oil and gas industry, Predictive Maintenance Analytics helps reduce operational disruptions by forecasting equipment failures based on historical data and real-time condition monitoring. It enables early detection of anomalies, allowing maintenance teams to perform repairs before critical failures occur, improving asset reliability, reducing downtime, and minimizing operational costs.
How is predictive maintenance applied in the industry?
Read Our Latest Blogs Curated by Industry Experts
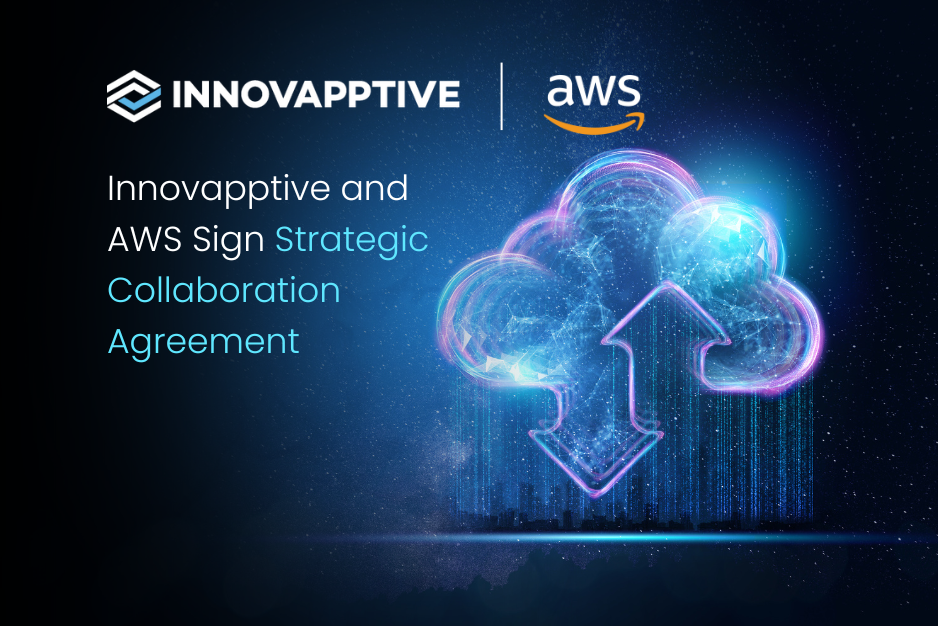
- 20-08-2025
Building the future of Industrial Operations with Innovapptive and AWS
Most manufacturers have already gone digital. Yet business outcomes haven’t moved in step. Many Connected Worker tools simply extend ERP interfaces to mobile devices. They digitize tasks but don’t fix how the work flows between operations, maintenance, safety, and inventory. Each team ends up in its own application. Data gets stuck. Outcomes stay flat. These “extender solutions” support individual roles in isolation, not the plant as a whole. So the core problems, contractor overuse, low ...
Read More