Five Common Challenges in the MRO Value Chain
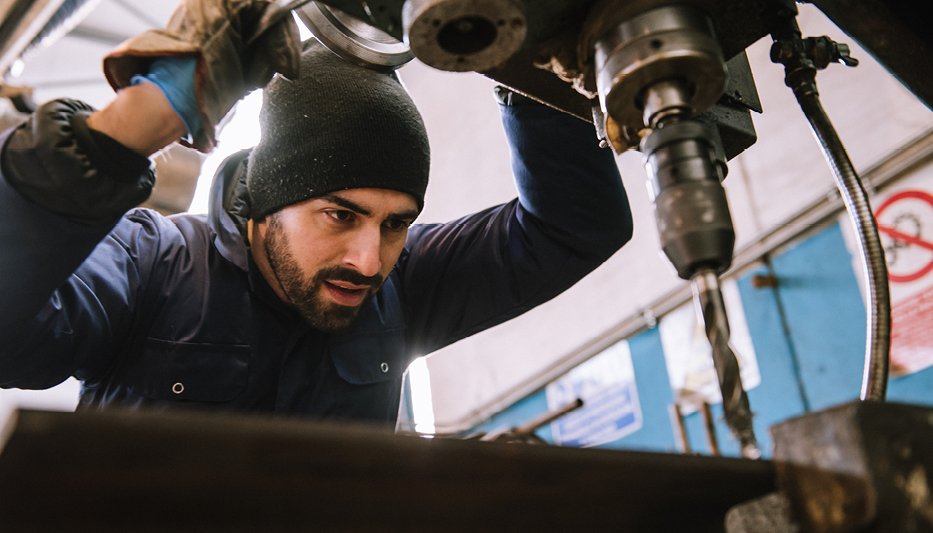
The idea of value chains was developed by famous business thinker Michael Porter back in the 1980s. It focuses on the series of linked activities that add value to a product or organization. This includes the supply chain but also incorporates a number of other elements, like product design and quality. Applying value chain thinking to maintenance, repairs and operations (MRO), it’s only when equipment is installed or repaired that real value is added to the organization.
MRO value chains are complex and span the globe. If you are on an offshore oil production platform off the coast of Malaysia, then it is likely that much of the equipment and spare parts required will have undergone a long journey from North America, Europe or China. Here are five key challenges for MRO value chains.
Limited Value Chain Integration
There is limited integration between different parties in the MRO value chain. This is apparent if you compare the MRO value chain with the food value chain. In food, value chain partners, which may include farmers, manufacturers and retailers, work closely together. They share information on sales and future demand and collaborate to ensure the value chain is able to respond.
There is much less collaboration in the MRO value chain. Equipment and parts suppliers may have implemented auto-identification (barcoding) of materials in their own operations, but those same barcodes can’t be read by their customer.
Maintenance and Supply Chain operate in silos
Maintenance and supply chain have separate reporting lines in most organizations. These organizations haven’t worked closely together in the past, even to the extent there is a“them and us” mentality. Innovapptive does a lot of work in MRO and we’ve recently started to see these silos being broken down. Some organizations have started to set up a single reporting line or at least joint teams to address problems.
Better collaboration helps you start to look at trade-offs that benefit both organizations such as implementing no technician “walk-ups” to the warehouse to collect parts and instead provide an outbound delivery service to drop-off points around the site. This increases technician wrench time and also improves warehouse productivity through less operational disruption.
Low Maintenance Productivity, Operational Visibility and Inventory Accuracy
Companies have invested significant sums in their enterprise resource planning (ERP) systems over the past 20 years but many remote workers in the field, factories and warehouses remain disconnected and have to manage with inefficient, paper-based processes. Maintenance engineers need to return to the office to confirm a completed work order in the ERP system or collect their next assignment. There is also a time lag between physical work and updates to the ERP system, so managers don’t have true real-time visibility of operations.
Weak or Missing MRO Processes
There are important MRO processes that are not effectively covered by today’s ERP systems. To give some examples:
- Kitting — This involves the assembly of work orders in the warehouse in advance of them being required in the field to support something like a shutdown or turnaround. Many companies have been forced to develop their own customized solution to fill this gap.
- Returns Process — Some parts ordered against a work order will not be required, as the technician does not know exact requirements until the work is started. Often the material doesn’t get returned to the warehouse and ends up being stored in cupboards and desks, known as “squirrel stores”. This can add up to a substantial inventory value when you have upwards of 100 technicians doing this across a site. This inventory is not visible in the ERP system and is often called “grey inventory.”
- Preservation — This is a unique process in MRO warehouses. Insurance spares and equipment are kept in case of critical failures in the plant. These are slow movers and may be in the warehouse for years. They will require routine maintenance in the warehouse such as greasing or lubrication. Many companies do not have a robust preservation process, meaning that parts and equipment are not fit for purpose when required.
- Rentals and warranty — These are often poorly controlled outside the ERP system using spreadsheets.
Poor Maintenance Planning
A poor planning process can cause a vicious cycle of low technician wrench time and rising maintenance backlog. Poor maintenance disciplines are characterized by a high proportion of corrective work orders, waiting for things to go wrong before they get fixed. The whole value chain will be in firefighting mode. This results in a high-cost operation providing a poor service and with high levels of equipment downtime.
Innovapptive's technology solutions can help organizations tackle the challenges of MRO, such as improving maintenance productivity, operational visibility, and inventory accuracy. Click here to learn more about how Innovapptive can help you improve your MRO value chain.
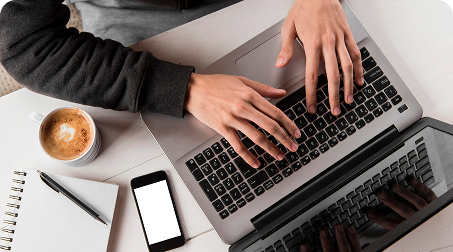
See It In Action
Schedule a personalized demo to see how our solutions can help your business thrive.
- 20-08-2025
Building the future of Industrial Operations with Innovapptive and AWS
Most manufacturers have already gone digital. Yet business outcomes haven’t moved in step. Many...
- 22-04-2025
The $3.6B Unlock: Solving the Chemical Industry’s Labor Crisis and EBITDA Pressure in One Move
“Constraints don’t slow innovation—they force it.”
- 21-04-2025
Chemical Industry's Margin Erosion: A Wake-Up Call for Operational Efficiency Amid China's Oversupply
The global chemical industry is facing mounting challenges, with revenue declines and shrinking...