The Key to Maximizing Your Wrench Time
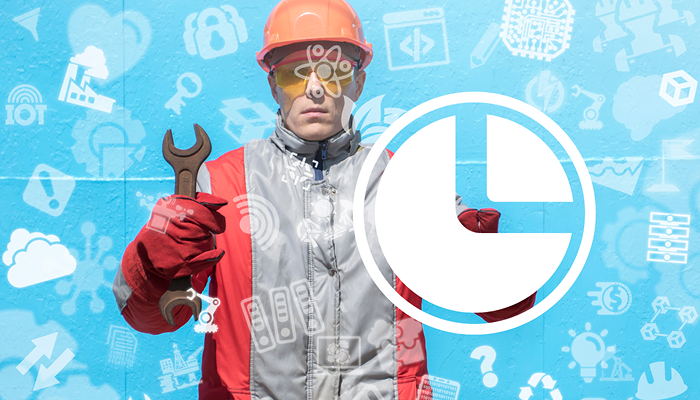
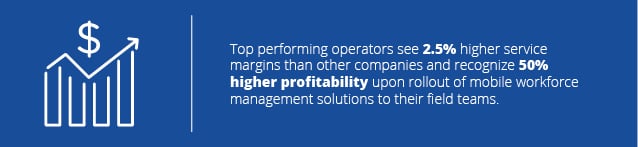
The money is in "efficiency" in maintenance organizations and the proof is in the pudding.
Many best-in-class manufacturing organizations relying on mobile employees have already learned how mobile apps and integrated back-end platforms can replace inefficient paper-based workflows. This has opened up a new world of effectiveness and productivity. Effective manufacturing organizations are ranking high on all spectrum's higher productivity, higher customer satisfaction levels, lower operating expenses, higher compliance levels and recognize more service revenue than the competition.
But tremendous profitability is not all that sets best-in-class manufacturing organizations apart from their competition. In fact, only a small percentage (22%) of organizations still rely heavily on paper-based forms, based on a study by the Aberdeen Group. Instead, a majority of manufacturing organizations have automated their paperwork, inventory management, dispatch
Delivering ROI
Reactive maintenance and preventive maintenance programs are expensive. Additionally, they can also bring about issues with process and manufacturing reliability and performance. Organizations with a highly mobile maintenance workforce should integrate mobility into operational tasks to drive productivity and optimize costs.
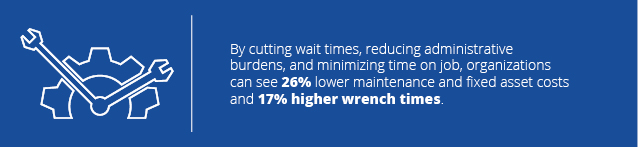
Innovapptive’s Connected Workforce Platform empowers manufacturing organizations with the tools they need to provide a superior, personalized customer experience that boosts customer loyalty and creates new opportunities. Organizations give their customers (internal and external) convenient access to their billing, contracts, customer service, support calls, and insight on service disruptions. The solutions within the Connected Workforce Platform put visibility in organizations’ hands and empower highly productive, comprehensive environments leading to reduced service times, improved service quality and timeliness.
Improved wrench time is a key driver in Innovapptive’s Connected Workforce Platform. Innovapptive's mWorkOrder
With Innovapptive's
To find out more about Innovapptive’s Connected Workforce Platform, and mWorkOrder with RACE™ Dynamic Forms.
Want to Discover More?
Innovapptive – a Connected Worker Platform provider – has a simple mission: “Connect and create conversations between people, machinery and work processes while improving people’s lives.” Innovapptive offers the only Connected Worker Platform that digitizes the last mile of your front-line workers into SAP and IBM (watch a short video here). We’d like to show how our Connected Worker Platform and related applications can help you successfully start and complete your journey to more efficient, safe and productive plant operations. Schedule a free demo today by calling 844-464-6668 or or by clicking here.
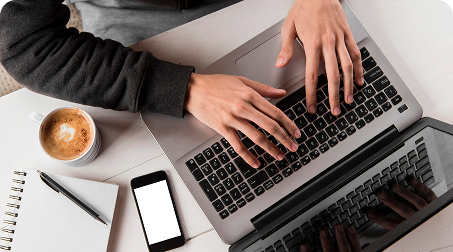
See It In Action
Schedule a personalized demo to see how our solutions can help your business thrive.
- 20-08-2025
Building the future of Industrial Operations with Innovapptive and AWS
Most manufacturers have already gone digital. Yet business outcomes haven’t moved in step. Many...
- 22-04-2025
The $3.6B Unlock: Solving the Chemical Industry’s Labor Crisis and EBITDA Pressure in One Move
“Constraints don’t slow innovation—they force it.”
- 21-04-2025
Chemical Industry's Margin Erosion: A Wake-Up Call for Operational Efficiency Amid China's Oversupply
The global chemical industry is facing mounting challenges, with revenue declines and shrinking...