Four Maintenance Processes You Need to Digitalize
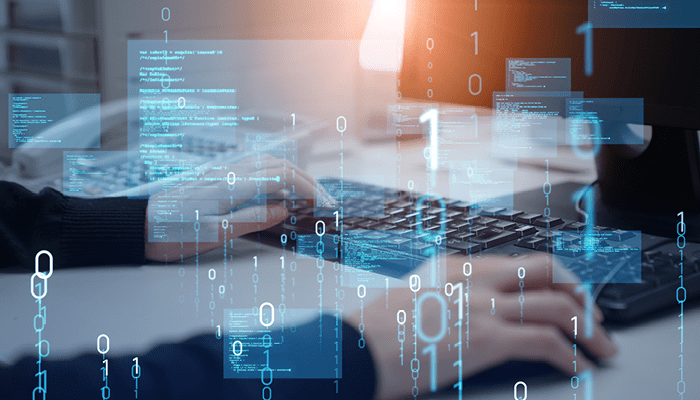
Companies are embracing digital transformation more than ever before. The industrial world is seeing an influx of digital solutions for practically every area of the business. Companies need to perform critical evaluation of data gaps within their industrial environment and decisively invest in digital technologies like a mobile EAM.
Here are four key areas that require immediate attention of companies to help them break communication silos and optimize processes.
Maintenance Planning and Scheduling:
Maintenance planning and scheduling processes need to be data-driven. They require an efficient communication mechanism for planners and schedulers to stay on top of key data collected from different sources across the company.
Conventional paper forms and siloed software solutions don’t provide real-time rounds data and information on availability of parts and resources. How can a planner or scheduler know if an equipment is on the verge of potential failure and needs immediate attention while sitting in the back office juggling paper forms? Would he even know what parts and tools are required and if they are available readily?
This gap between field and back-office creates an urgent need to digitialize planning and scheduling using mobile plant maintenance solutions.
Operator rounds:
Every single minute of equipment uptime matters for asset-intensive companies and unexpected downtime hurts their bottom lines. Operators often come across situations where they identify a critical issue and need to push a notification or have a work order created immediately.
Unfortunately, most operators are ill-equipped in the field. They still carry clipboards and walk over to the back-office to submit the paper forms after finishing rounds in the field. This excessively increases the time to fix critical issues, leading to unnecessary downtime.
Replacing paper forms with mobile solutions and connecting operators with ERP systems in real-time expedites the rounds process. This enhances occupational safety and the operational efficiency of industrial equipment.
MRO Value Chain
The MRO value chain plays a critical role in a plant's productivity. Sometimes the unavailability of a nut can hold up a production line and incur losses to the company. MRO is also a domain which can be a source of risky purchases and rogue buying behavior, resulting in high inventory carrying costs.
To ensure smooth operation of production lines and keep inventory costs in limits, companies need to get a comprehensive view of their MRO value chains. Digitalizing MRO processes through a mobile Connected Worker platform breaks data silos and connects supply chains and MRO for better view into the availability of spare parts, upcoming work orders and future predictions. This helps inventory managers make well-informed decisions about procurement.
Work Instructions
Skills gaps in the front line workforce is a key challenge facing asset-intensive companies as they deal with the Great Crew Change. As experienced technicians retire, most of their tribal knowledge about critical equipment, processes and plant operations gets lost.
Paper-based work instructions and manuals which are periodically updated have been popular ways to store knowledge for years, but they have serious limitations. When technicians come across unprecedented scenarios, they don't find an easy way to record the knowledge for future use. When the same or similar case occurs again, maintenance teams need to go back to the drawing board.
Digital work instructions help companies bridge this gap and solve other major challenges, including productivity and occupational safety.
Want to know how Innovapptive’s EAM solution breaks data silos and eliminates skills gaps and ghost assets?
Book a customized live demo of our mobile EAM solution here.
You can also reach out to us at 1-844-464-6668 and talk to our Connected Worker platform experts.
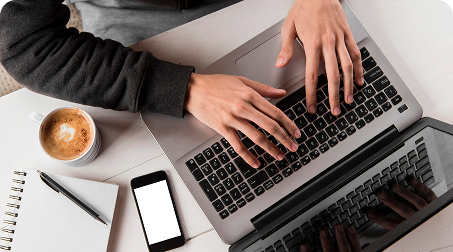
See It In Action
Schedule a personalized demo to see how our solutions can help your business thrive.
- 20-08-2025
Building the future of Industrial Operations with Innovapptive and AWS
Most manufacturers have already gone digital. Yet business outcomes haven’t moved in step. Many...
- 22-04-2025
The $3.6B Unlock: Solving the Chemical Industry’s Labor Crisis and EBITDA Pressure in One Move
“Constraints don’t slow innovation—they force it.”
- 21-04-2025
Chemical Industry's Margin Erosion: A Wake-Up Call for Operational Efficiency Amid China's Oversupply
The global chemical industry is facing mounting challenges, with revenue declines and shrinking...