How Digital Technology is Improving Autonomous Maintenance
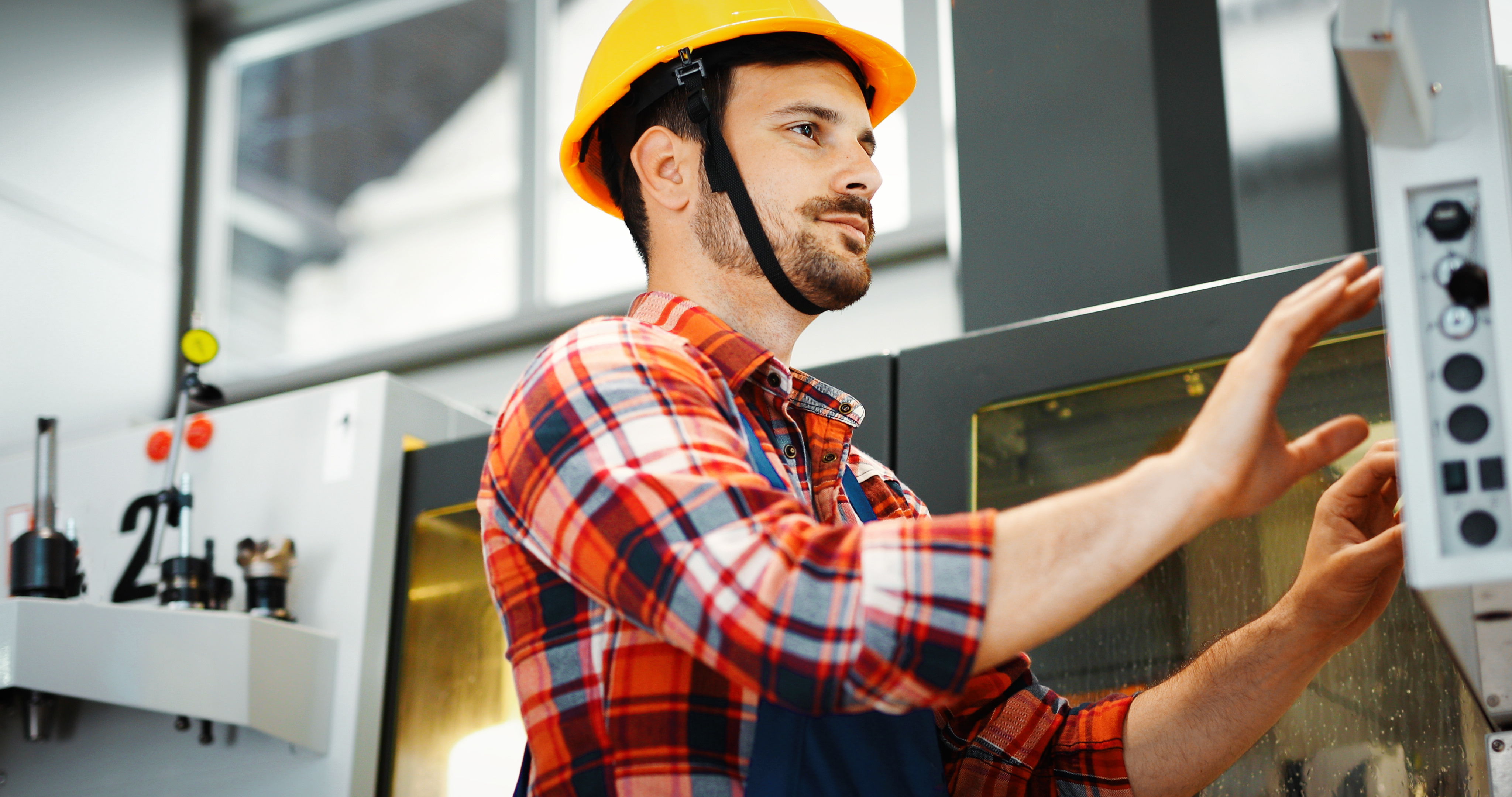
Autonomous maintenance, whereby machine operators take on some responsibilities for equipment maintenance, is one of the eight pillars of Total Productive Maintenance (TPM) developed in Japan in the 1970s.
The rationale behind autonomous maintenance is very intuitive: to maximize production output and product quality, you need to minimize unplanned equipment downtime and defects. Who better to do that than the machine operators themselves? Operators know their own machines better than anyone.
Their experience allows them to recognize unusual noises and vibrations, a clear signal that things are about to go wrong. They can be trained on inspections, routine maintenance tasks and how to fix common problems without the need to call on maintenance technicians.
Autonomous maintenance’s main benefit is to improve overall equipment effectiveness (OEE), the key measure of manufacturing productivity and quality. An OEE score of 100% means you are manufacturing at 100% quality (only good parts), 100% performance (as fast as possible) and with 100% availability (no unplanned stoppages). When done properly, autonomous maintenance can be a major contributor to improving OEE.
Many companies have followed the well-trodden, seven-step approach to deploying autonomous maintenance, which includes operator training, developing maintenance standards, inspection routines and a focus on continuous improvement. One major pitfall frustrating these efforts is that new processes are often paper-based, falling outside the scope of existing systems.
Autonomous maintenance can lead to a proliferation of paper forms including checklists, inspections forms, standard operating procedures (SOPs) and training material. Valuable information remains outside of the system with paper-based processes, making it nearly impossible to analyze and derive business insights.
We strongly believe at Innovapptive that an autonomous maintenance program needs to go hand-in-hand with the deployment of digital technologies. The diagram below shows how digital technologies can support key components of autonomous maintenance.
Let us look at the five critical success factors for autonomous maintenance and how digital technologies can help:
- Operator knowledge on machinery and basic maintenance — Deploying autonomous maintenance involves cultural change. Suddenly the operator is given a bigger role in maximizing machine output and product quality. This change needs to be supported by proactive change management.
There are practical ways that digital technologies can help with training and implementation. Don’t expect operators to read through OEM maintenance documentation. Instead, produce simple videos showing how to complete routine maintenance and clean equipment. Operators can be issued tablets or smartphones to access refresher training and support their new responsibilities. Most operators embrace the increased responsibility that comes with autonomous maintenance, but you have to help them along the way. - Develop clear maintenance standards — Autonomous maintenance incorporates a lean manufacturing approach known as 5s: sort, set in order, shine, standardize, and sustain. Keeping equipment clean and lubricated reduces the chance of breakdown and product defects. Setting standards includes what parts of the machine need to be cleaned and lubricated and how often. A detailed set of work instructions or SOP would then explain the specific steps required to complete the work, including important safety steps that need to be adhered to.
Again, there are big benefits to having digital work instructions and SOPs that give all the information the operator needs on a tablet or smartphone. They’re easy for the operator to use and can be updated quickly to reflect changes in procedures. - Ensure rigorous inspection and monitoring — You're now ready to deploy autonomous maintenance onto the shop floor once your operators are trained and standards defined. The operator will be expected to carry out regular inspections as a way of pre-empting problems, in addition to operating and observing machinery. Digital inspection checklists with built-in validations are a very powerful way of ensuring that all checks are completed. Operators themselves can provide input into the development of inspection checklists, since they develop such an in-depth knowledge of their own machines, such as knowing which bolts are likely to come loose and at what frequency.
- Integrate new maintenance processes with systems of record — So you're now up and running with autonomous maintenance, but if you don’t have integrations with your existing systems of record then you have a very big piece of the jigsaw puzzle missing. New maintenance processes and data will be orphaned and you are leaving a lot of money on the table.
The best way to explain the power of integration is to give an example. While an operator is carrying out a routine machine inspection, she notices there is a small crack on the conveyor belt taking bottles into the filling machine. She raises an urgent notification on her tablet linked directly to the ERP system. This is immediately visible to the maintenance supervisor who assesses the impact and allocates the work to a technician. Integration enables improved collaboration between operations and maintenance, which will have a positive impact on OEE. - Focus on continuous improvement — Continuous improvement is one of the key principles of autonomous maintenance and wider lean thinking. Lean manufacturing encourages a continual focus on incremental process improvements.
For example, say the current lubrication work instructions identifies five points on the machine that need to be lubricated every 100,000 parts produced. However, the operator has noticed that performance starts to deteriorate after 70,000 parts, causing more breakdowns and product defects. The maintenance supervisor reviews the issue and decides to increase lubrication frequency based on 70,000 parts produced, resolving the problem.
If all inspection checklists, work instructions and SOPs are in a digital format, it makes it very easy to make changes like this and respond to the need for continuous improvement.
Innovapptive’s Connected Worker Platform (CWP) offers a portfolio of solutions to support the deployment of autonomous maintenance in your organization. It provides the tools to digitalize all your maintenance processes, fully integrate those processes with your systems of record and the flexibility to respond to fast changing business requirements.
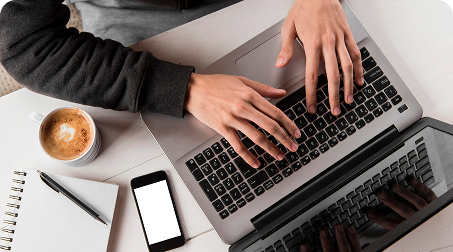
See It In Action
Schedule a personalized demo to see how our solutions can help your business thrive.
- 20-08-2025
Building the future of Industrial Operations with Innovapptive and AWS
Most manufacturers have already gone digital. Yet business outcomes haven’t moved in step. Many...
- 22-04-2025
The $3.6B Unlock: Solving the Chemical Industry’s Labor Crisis and EBITDA Pressure in One Move
“Constraints don’t slow innovation—they force it.”
- 21-04-2025
Chemical Industry's Margin Erosion: A Wake-Up Call for Operational Efficiency Amid China's Oversupply
The global chemical industry is facing mounting challenges, with revenue declines and shrinking...