How Interactive Dashboards Can Improve Industrial Maintenance
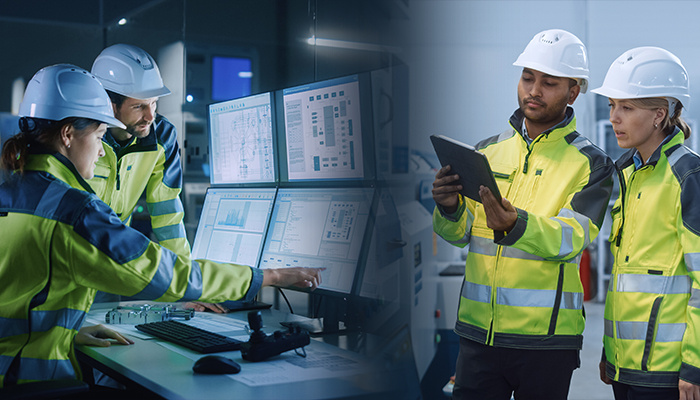
Key Takeaways
Unplanned downtime is costly: Unplanned downtime can cost manufacturers up to $260,000 per hour. Interactive dashboards help predict and prevent breakdowns by providing real-time visibility into equipment conditions.
Predictive maintenance saves time and money: Dashboards reduce machine downtime by 30-50% and extend asset life by 20-40%, ensuring timely, data-driven maintenance interventions.
Reactive maintenance is inefficient: 58% of maintenance teams still rely on reactive maintenance. Dashboards help shift focus to proactive strategies, reducing unnecessary downtime.
Introduction
For industrial companies, maintaining equipment reliability is essential. Equipment downtime doesn't just affect production; it can cause significant financial losses, safety risks, and reputational damage. As plants grow more complex, so does the task of maintaining them. Whether it’s ensuring the availability of critical spare parts or avoiding unexpected breakdowns, industrial maintenance supervisors and managers are under immense pressure to optimize operations.
One of the biggest challenges these teams face is accessing real-time, actionable data. The traditional reliance on paper-based systems or static reports makes it difficult to stay ahead of potential issues. As more companies turn to digital solutions, interactive dashboards have emerged as a game-changer for maintenance teams.
In this blog, we'll explore the major challenges industrial maintenance teams face and how interactive dashboards can help overcome these challenges. We'll also take a deep dive into how Innovapptive’s interactive dashboards can boost performance and minimize costly downtime.
Performance Problems Industrial Companies Are Facing
Industrial maintenance teams face a range of operational hurdles that directly impact performance. Let's take a closer look at four key challenges that hinder operational efficiency:
Unplanned Downtime
Unplanned downtime is the bane of industrial companies. Unexpected equipment breakdowns not only disrupt production but can also lead to hefty financial losses. A study by the Aberdeen Group found that 82% of companies experienced unplanned downtime over the past three years, and it can cost manufacturers up to $260,000 per hour. These breakdowns often stem from a lack of real-time visibility into equipment conditions. Without timely data, maintenance teams can't predict failures, leaving them in a constant state of reaction.
Inefficient Industrial Maintenance Schedules
Balancing preventive and reactive maintenance can be tricky without real-time insights. Too much focus on reactive maintenance leads to costly equipment failures, while excessive preventive maintenance wastes valuable resources. Maintenance managers are often caught in the middle, unable to pinpoint the optimal time for interventions due to a lack of visibility into equipment performance.
According to Plant Engineering, 58% of maintenance teams still rely on reactive maintenance, meaning they address issues only after a failure occurs. This reactive approach leads to inefficiencies, with teams missing opportunities to conduct targeted, predictive maintenance that could prevent breakdowns.
Poor Resource Utilization
Inefficient resource management is another significant challenge for industrial plants. Maintenance teams often face the issue of not knowing where resources—spare parts, tools, or personnel—are when they need them most. This lack of visibility delays repairs and leads to overstocking or stockouts, increasing carrying costs and downtime.
Poor resource utilization also extends to personnel. Without insights into technician availability and skills, it becomes difficult to assign tasks optimally, leading to underutilization of labor or misallocation of technical expertise.
Data Overload Without Clarity
Industrial plants generate vast amounts of data from machinery sensors, maintenance logs, and ERP systems. However, without the right tools to sift through this information, data becomes a burden rather than an asset. Maintenance teams can quickly become overwhelmed by this data overload, unable to prioritize what matters most, let alone take action on it.
This challenge is amplified when teams rely on static reports, which provide only historical snapshots, limiting their ability to react swiftly to evolving conditions on the ground.
What is an Interactive Dashboard?
Interactive dashboards have become an essential tool for modern industrial maintenance teams. Unlike static reports, these dashboards present real-time data in a visual, customizable format. They provide insights into critical performance indicators, enabling users to drill down into specific data points and make informed decisions faster.
Key features of interactive dashboards include:
- Real-Time Data Visualization: Dashboards pull live data from various sources such as sensors, ERP systems, and IoT devices, providing up-to-the-minute insights.
- Customizable Views and Filters: Users can personalize dashboards to display only the most relevant KPIs, adjusting views based on their needs (e.g., asset health, work order status, or spare part availability).
- Drill-Down Capabilities: Dashboards offer a deeper dive into specific data points, allowing maintenance managers to explore detailed information behind performance metrics.
Modern technology such as artificial intelligence (AI) further enhances dashboards, allowing them to analyze equipment performance and suggest optimal maintenance times. AI can even predict when a piece of equipment is likely to fail, giving maintenance teams the foresight needed to avoid costly breakdowns.
Benefits of Interactive Dashboards for Industrial Maintenance Performance
So, how exactly do interactive dashboards solve the key maintenance management challenges that industrial companies face? Let’s explore the main ways they can improve operational efficiency.
Real-Time Equipment Monitoring
Interactive dashboards give maintenance teams a real-time view of equipment performance. Data from machine sensors and other sources feed directly into the dashboard, showing critical metrics such as temperature, vibration, or pressure. Maintenance teams can act immediately when performance indicators deviate from normal, preventing equipment from deteriorating to the point of failure.
For example, if a pump begins to show signs of wear due to overheating, a dashboard can alert the team before the pump fails entirely. This proactive approach allows for targeted maintenance management, reducing downtime and extending equipment lifespan.
Improved Decision-Making
With interactive dashboards, maintenance managers no longer need to rely on static reports or guesswork. They can view real-time KPIs and performance metrics, allowing for faster and more informed decision-making. Managers can see where their resources are allocated, track ongoing work orders, and monitor technician performance—all from a single platform.
Dashboards also allow managers to spot trends. If a particular piece of equipment frequently requires repairs, the dashboard can highlight this, helping teams identify potential chronic issues that need long-term solutions.
Optimized Preventive Maintenance
Preventive maintenance is most effective when timed just right. With access to real-time equipment data, maintenance teams can optimize their schedules to ensure interventions occur before equipment fails—but not so frequently that resources are wasted. Interactive dashboards can track the operating hours, performance history, and condition of critical assets, recommending the ideal time for preventive maintenance.
This shift from reactive to predictive maintenance leads to fewer unexpected failures and longer equipment lifecycles.
Increased Collaboration
Interactive dashboards also improve communication between different teams. By providing access to the same real-time data, operations, maintenance, and back-office teams can work together more effectively. For instance, if the maintenance department schedules a repair, the operations team can adjust production schedules accordingly. Real-time data also ensures that back-office teams are aware of the spare parts and tools needed for upcoming repairs.
This cross-departmental collaboration reduces delays and ensures that maintenance management activities are completed efficiently, minimizing disruptions to production.
How Innovapptive’s Interactive Dashboards Can Help Industrial Maintenance Teams
Innovapptive’s interactive dashboards are specifically designed to address the needs of industrial maintenance teams. By combining real-time visibility, data-driven decision-making, and predictive maintenance capabilities, Innovapptive’s solutions help teams work smarter, not harder.
Real-Time Maintenance Visibility
Innovapptive’s dashboards offer an in-depth, real-time view of maintenance activities. Supervisors and managers can track work orders, monitor equipment health, and see inventory levels at a glance. This visibility allows maintenance teams to move from a reactive approach to a proactive one, preventing breakdowns before they occur.
For example, Innovapptive’s mWorkOrder solution enables technicians to log updates in real time. As they complete tasks or face challenges, their supervisors can see the status instantly on the dashboard, helping prevent bottlenecks and ensuring that tasks are completed efficiently.
Data-Driven Decision Making
Integrated with SAP and other ERP systems, Innovapptive’s dashboards enable teams to track key performance metrics such as technician productivity, work order backlog, and repair times. Managers can use this data to identify inefficiencies, address resource gaps, and make informed decisions about maintenance management strategy.
In addition, by tracking trends over time, Innovapptive’s dashboards can help maintenance teams identify recurring issues. For instance, if a specific motor frequently breaks down, the data can reveal the need for a long-term fix or replacement.
Optimized Resource Allocation
Innovapptive’s dashboards make resource allocation more efficient. Maintenance teams can see at a glance which technicians are available, what tools are required, and whether the necessary spare parts are in stock. This helps minimize downtime caused by missing resources and ensures that tasks are completed on schedule.
With Innovapptive’s mInventory solution, maintenance teams gain real-time visibility into spare parts movement within the warehouse. Dashboards track inventory levels and can even flag low-stock items before they run out, reducing the risk of costly delays due to part shortages.
Predictive Maintenance Capabilities
Through the integration of operator rounds and digital inspections, Innovapptive’s dashboards support predictive maintenance by analyzing data from equipment sensors and historical maintenance logs. This allows teams to predict equipment failures and schedule maintenance activities ahead of time, avoiding unexpected breakdowns.
For industrial plants where even a few hours of downtime can result in millions of dollars in losses, this predictive capability is invaluable. Maintenance teams can rely on Innovapptive’s dashboards to extend equipment lifecycles and reduce the frequency of unexpected failures.
Conclusion
Interactive dashboards are improving maintenance performance in industrial settings by offering real-time data, improving decision-making, and reducing unplanned downtime. For maintenance supervisors, managers, and directors, having access to a clear, interactive view of equipment health and maintenance management activities can make the difference between a smoothly running plant and one constantly battling breakdowns.
Innovapptive’s solutions go beyond traditional dashboards by integrating mobile, cloud, and ERP systems, delivering comprehensive, real-time insights that empower maintenance teams to take proactive action. Whether your team is monitoring equipment health, tracking work orders, or managing spare parts inventory, Innovapptive’s interactive dashboards enable you to optimize every aspect of your maintenance operations.
- Reduce unplanned downtime: Get ahead of equipment failures with predictive insights and proactive maintenance management strategies.
- Improve resource allocation: Allocate tools, spare parts, and personnel more efficiently, ensuring minimal delays and optimal task completion.
- Make informed decisions faster: Real-time, customizable dashboards allow maintenance managers to respond to issues immediately, optimizing both preventive and reactive maintenance efforts.
- Boost collaboration across departments: Operations, back-office, and maintenance teams all benefit from having access to the same real-time data, improving communication and coordination.
For industrial plants where every minute counts, moving away from reactive maintenance to a data-driven, proactive strategy can significantly reduce downtime, increase equipment lifespan, and improve overall operational efficiency.
FAQ
Q: What is an interactive dashboard in maintenance?
A: An interactive dashboard is a tool that provides real-time data on KPIs like equipment health and work order status, allowing users to filter and explore data for better decision-making.
Q: How do interactive dashboards reduce downtime?
A: Dashboards monitor equipment in real time, alerting teams when performance deviates from normal, allowing proactive action to prevent breakdowns.
Q: What’s the difference between reactive and predictive maintenance?
A: Reactive maintenance fixes equipment after it fails, while predictive maintenance uses data to anticipate failures, reducing downtime by up to 50%.
Q: Why is data visibility crucial in maintenance?
A: Real-time data visibility allows teams to track equipment health and resources efficiently, preventing bottlenecks and improving decision-making.
Q: How do dashboards optimize preventive maintenance?
A: Dashboards schedule maintenance based on real-time data, preventing failures and maximizing equipment lifespan.
Q: Can dashboards improve collaboration?
A: Yes, they provide shared access to real-time data across teams, improving communication and reducing delays.
Q: How does Innovapptive improve maintenance visibility?
A: Innovapptive’s dashboards offer real-time insights into work orders and equipment health, enabling proactive maintenance.
Q: How does Innovapptive support data-driven decisions?
A: Integrated with ERP systems, Innovapptive tracks key metrics, helping teams make informed decisions with real-time data.
Q: What are Innovapptive’s predictive maintenance features?
A: Innovapptive analyzes data to predict equipment failures, reducing downtime through timely repairs.
Q: How can I request an Innovapptive demo?
A: Request a demo here to see how Innovapptive’s dashboards can improve maintenance performance.
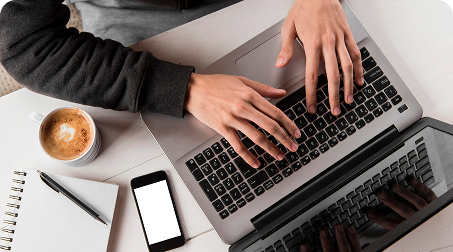
See It In Action
Schedule a personalized demo to see how our solutions can help your business thrive.
- 20-08-2025
Building the future of Industrial Operations with Innovapptive and AWS
Most manufacturers have already gone digital. Yet business outcomes haven’t moved in step. Many...
- 22-04-2025
The $3.6B Unlock: Solving the Chemical Industry’s Labor Crisis and EBITDA Pressure in One Move
“Constraints don’t slow innovation—they force it.”
- 21-04-2025
Chemical Industry's Margin Erosion: A Wake-Up Call for Operational Efficiency Amid China's Oversupply
The global chemical industry is facing mounting challenges, with revenue declines and shrinking...