How Mines Can Optimize Lubrication Programs with a Mobile EAM Solution
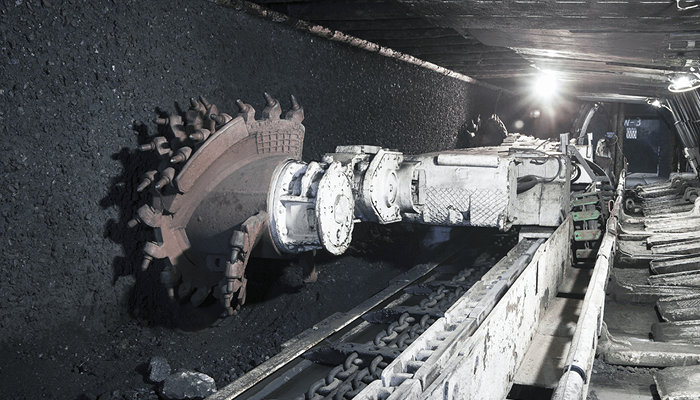
Lubrication is the lifeblood of industrial equipment.
But more than 60% of bearing failures are due to ineffective lubrication resulting from poor lubricant selection, contamination and improper application. The mining industry, where critical equipment experiences high wear and tear, faces huge productivity losses due to lubrication-related failures. Mining companies need to adopt mature digital capabilities to achieve optimal lubrication and boost equipment reliability.
The mining industry uses heavy machinery like large mining trucks, hydraulic mining shovels and large dozers. These machines place different demands on lubricants. Original equipment manufacturers (OEMs) prescribe in their service manuals the specifications for lubricants that should be used on these components to maximize their performance and safety. The wrong application of lubricants or inconsistent use of appropriate ones shortens the operating life of equipment. In worst-case scenarios, this causes catastrophic equipment failures.
Roadblocks to optimal lubrication in mines
Traditional, manual maintenance systems based on paper present several significant challenges when it comes to a lubrication program. Oil analysis and vibration analysis help miners detect abnormal wear, predict the time to equipment failure and determine proper use of lubricants. But this real-time data is often delayed in reaching decision makers. When a decision is made to work on a piece of equipment, young technicians performing jobs also may lack enough experience to apply these oils properly, leading to either under- or over-lubrication.
Under lubrication causes premature failure and increases component wear and maintenance costs. Over lubrication is equally harmful for mining equipment as it puts stress on lube points, leads to excess heat build-up, and increases equipment downtime.
Maintaining oil cleanliness is another major challenge to mine maintenance managers. Several regulatory standards (eg. ISO 4406) suggest measures to contain oil contamination. However, this knowledge may not be fully transferred to field-level technicians. This compromises oil cleanliness management, giving way to lubrication-related equipment failures in mines.
Though most mining companies use maintenance management solutions, they’re often siloed and disconnected from other programs like inventory management and fixed asset management. Maintenance technicians with dated information on paper forms waste time searching for the right lubricants. Inventory managers struggle to maintain balanced oil inventory levels without accurate information on lubrication planning and scheduling.
When the goal is to achieve optimal lubrication, companies should integrate frontline technicians into the asset management environment. Here’s where most mining companies fail because of manual asset data collection and distribution.
How a mobile SAP plant maintenance solution helps
Empowering every maintenance technician with the right digital tools and training lays the foundation for a strong lubrication program. Mobile SAP plant maintenance solutions help mining companies enhance their frontline maintenance technicians’ knowledge on oils.
These digital solutions integrate plant maintenance programs, inventory and fixed asset management programs with SAP. Frontline technicians access these platforms on smartphones and handheld devices and don’t need to carry clipboards.
Every stakeholder in the lubrication program, including operators, maintenance managers, technicians and inventory managers feed real-time asset data into the SAP system. This includes oil analysis, vibration analysis, risk assessment, lubrication planning, recommended oils, stock levels, and availability. Technicians and managers can access this data from SAP and know exactly what equipment needs attention at any given time.
To help young technicians apply oil properly to the equipment, digital work instructions offer visual support and guidance from experts. When mines get new equipment and components, maintenance managers can update information about new procedures and create work instructions quickly using no-code/low-code configurable forms on the solutions.
For example, maintenance managers can use Innovapptive’s RACE™(Rapid Application Configuration Engine) technology in their mobile EAM solution to convert paper forms and checklists into digital forms in less than 30 minutes. This helps frontline staff perform operator rounds and execute work orders as per the updated standards and latest methods.
Efficient lubrication program requires proper training and data management, which is easily achievable in the digital era. The challenge is to find the right solution that delivers the promises of modern technologies and helps them establish a fail-proof lubrication program.
Innovapptive offers a best-in-class mobile EAM solution that breaks conventional data silos and creates a unified mine maintenance ecosystem, facilitating an efficient lubrication program. Book a customized live demo of our mobile EAM solution here.
You can also reach out to us at 1-844-464-6668 and talk to our Connected Worker platform experts.
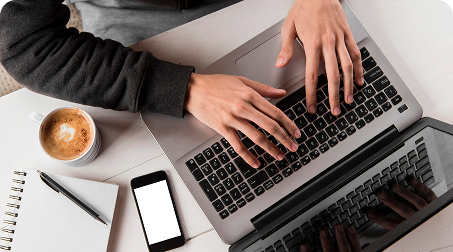
See It In Action
Schedule a personalized demo to see how our solutions can help your business thrive.
- 20-08-2025
Building the future of Industrial Operations with Innovapptive and AWS
Most manufacturers have already gone digital. Yet business outcomes haven’t moved in step. Many...
- 22-04-2025
The $3.6B Unlock: Solving the Chemical Industry’s Labor Crisis and EBITDA Pressure in One Move
“Constraints don’t slow innovation—they force it.”
- 21-04-2025
Chemical Industry's Margin Erosion: A Wake-Up Call for Operational Efficiency Amid China's Oversupply
The global chemical industry is facing mounting challenges, with revenue declines and shrinking...