How Mobile Operator Rounds Reduce Manufacturing Downtime and Improve Plant Safety
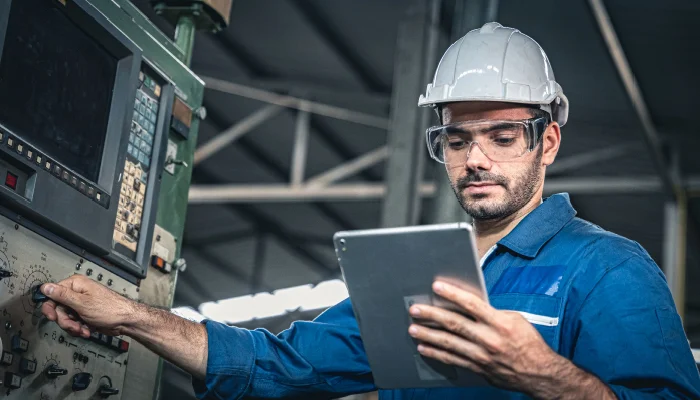
American manufacturing plants are making do with increasingly older equipment, with a high percentage of production machines averaging 20 or more years of active operational service. Relying on aging machinery comes with substantial risks and potentially big costs. The good news is connected worker technology and mobile operator rounds offer a painless, easy-to-implement solution.
Run-to-Fail Maintenance Causes More Problems Than It Solves
Older equipment runs a greater chance of mechanical failure, resulting in lost production and revenue. Aging machines that require more maintenance also are increasingly prone to being involved in employee accidents, which increases lost work hours and leads to compliance violations.
Manufacturers are naturally hesitant to buy new machinery due to high replacement costs. At the same time, many companies (more than half) still employ reactive, run-to-fail maintenance programs. This combination – older equipment and run-to-fail maintenance – seldom works out well. Ultimately, plants using this inefficient combination suffer:
- An average of up to 800 hours a year in unplanned downtime
- Higher maintenance costs of up to 50%
- Additional undue stress on the entire production line and frontline workers
But you don’t need to take on the high cost of replacing machinery in order to increase uptime and reduce safety risks. The right technology can deliver those benefits at a much lower cost.
Transform Your Maintenance Program via Mobile Connected Worker Technology
More than eight out of 10 industrial plants experienced at least one unplanned downtime incident over the past three years. What’s worse, the average number of incidents was two equipment outages.
Maintenance directors and managers are constantly looking for ways to keep machinery humming while minimizing lost technician work hours due to accidents. The key to overcoming both these costly challenges is real-time, accurate information.
Right now, more than two-thirds of American manufacturing plants simply don’t know when their aging equipment is up for repair or replacement. That lack of knowledge increases maintenance costs, decreases machinery uptime and leads to unsafe conditions. If they could just raise their level of knowledge, isn’t it logical they could solve all of these problems?
Plants like these conduct daily operator rounds to uncover and report potential operational and safety issues. Unfortunately, they’re too often conducting rounds using paper forms and clipboards. This manual process results in delays in getting critical information into the hands of supervisors and managers for appropriate and timely action. The report is essentially rendered useless. Instead of issues being addressed promptly, they fester and grow into greater – and more costly – problems.
Connected worker technology offers an answer.
Rather than slow, cumbersome paper forms, technicians conduct operator rounds using mobile devices, such as a smartphone, tablet or wearable. Techs report their findings in real time with no paperwork to file and no delay. Directors, managers and supervisors can follow along as the inspection is taking place, communicating and collaborating with the technician at the site of the problem, whether it’s an equipment issue or a safety hazard. They’re now forewarned and forearmed, meaning they can give instant directions to the tech or cut an immediate work order to correct the situation… before it worsens.
Be Forewarned and Forearmed about Plant Maintenance and Safety
It’s easy to learn more about how a Mobile Operator Rounds solution can transform your plant’s operations for the better using real-time information? Simply schedule a free online demo today or call us at 844-464-6668 to speak to one of our experts. They’ll be ready to answer your questions and show you the path to more efficient maintenance and greater safety.
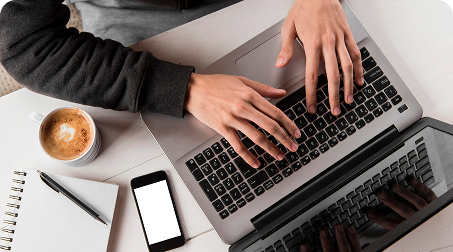
See It In Action
Schedule a personalized demo to see how our solutions can help your business thrive.
- 22-04-2025
The $3.6B Unlock: Solving the Chemical Industry’s Labor Crisis and EBITDA Pressure in One Move
“Constraints don’t slow innovation—they force it.”
- 21-04-2025
Chemical Industry's Margin Erosion: A Wake-Up Call for Operational Efficiency Amid China's Oversupply
The global chemical industry is facing mounting challenges, with revenue declines and shrinking...
- 21-04-2025
Why Wrench Time Isn’t Improving: The Hidden Costs of Traditional Maintenance Scheduling
For years, industrial leaders have relied on a common but flawed assumption: "Better planning and...