How Mobile Plant Maintenance Can Help You Hit Key Metrics
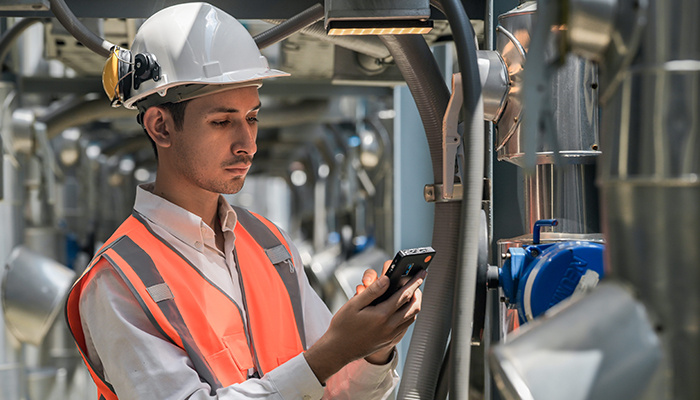
Key Takeaways
- 50% Faster Repairs: Mobile plant maintenance solutions cut Mean Time to Repair (MTTR) by up to 50%, reducing downtime and speeding up recovery.
- 30% Less Downtime: Mobile work order management systems lower equipment downtime by up to 30%, improving operational efficiency.
- >98% Uptime: Achieve over 98% asset uptime with real-time monitoring and predictive maintenance, minimizing disruptions.
Introduction
Tracking key maintenance metrics is crucial for optimizing plant performance, reducing downtime, and ensuring equipment reliability. A mobile plant maintenance solution featuring work order management can help maintenance managers achieve these goals by providing real-time data, automating workflows, and improving decision-making. In this blog, we’ll explore the five essential maintenance metrics every manager should track:
- Mean Time Between Failures (MTBF)
- Mean Time to Repair (MTTR)
- Overall Equipment Effectiveness (OEE)
- Planned Maintenance Percentage (PMP)
- Downtime Percentage
Digital transformation in maintenance is a great way to future-proof your processes while meeting goals. Discover how a mobile plant maintenance/mobile work order management solution can help you improve these metrics and enhance operational efficiency.
The 5 Key Maintenance Metrics Every Manager Should Track
When it comes to optimizing plant operations, tracking the right maintenance metrics is essential. These five metrics are crucial for improving efficiency, reducing downtime, and ensuring that equipment is reliable.
Mean Time Between Failures (MTBF)
What It Is: MTBF measures the average time between equipment failures. It’s a key indicator of how reliable your machinery is and whether it’s prone to unplanned breakdowns.
Why It’s Important: A high MTBF means that your equipment runs for longer periods without failure, which translates into fewer interruptions, lower maintenance costs, and more reliable production.
Challenges with Traditional Methods: Paper-based systems make it hard to accurately track MTBF. Manual logs can easily miss details or contain inaccuracies, leading to unreliable data. Without real-time insights, predicting failures and planning maintenance becomes difficult.
Mean Time to Repair (MTTR)
What It Is: MTTR calculates the average time it takes to repair equipment after a failure. This metric includes the time spent diagnosing the issue, obtaining parts, and performing the repair.
Why It’s Important: The faster you can repair equipment, the less downtime your plant experiences. Reducing MTTR minimizes production delays, helps you stay on schedule, and reduces costs associated with idle machinery.
Challenges with Traditional Methods: Using paper-based processes, work orders often get delayed, misplaced, or routed inefficiently. These inefficiencies slow down repair times, extending MTTR. Additionally, finding relevant documentation or spare parts often takes longer without a centralized, digital system.
Overall Equipment Effectiveness (OEE)
What It Is: OEE is a comprehensive metric that measures how well equipment is being used compared to its full potential. It factors in availability (uptime), performance (speed), and quality (output).
Why It’s Important: OEE gives you a clear picture of how efficiently your equipment is running. A high OEE score means your equipment is operating at its peak capacity with minimal interruptions or quality issues.
Challenges with Traditional Methods: Paper-based systems often lack the real-time data needed to accurately calculate OEE. Without automated data collection and analysis, it’s difficult to measure performance consistently, identify issues, or optimize productivity.
Planned Maintenance Percentage (PMP)
What It Is: PMP is the percentage of your maintenance time that is spent on planned, preventive maintenance rather than reactive, unplanned repairs.
Why It’s Important: A higher PMP indicates that your team is performing proactive maintenance to prevent equipment failures. This reduces the likelihood of unexpected downtime, extends the life of equipment, and leads to lower repair costs.
Challenges with Traditional Methods: Paper-based systems make it hard to ensure that preventive maintenance tasks are scheduled and completed on time. Without automation, tasks may get missed, leading to a higher reliance on reactive maintenance.
Downtime Percentage
What It Is: This metric measures the percentage of time that equipment is unavailable due to repairs, maintenance, or failures.
Why It’s Important: High downtime leads to lost production and higher operational costs. Reducing downtime is crucial for keeping your plant running efficiently and meeting production targets.
Challenges with Traditional Methods: Paper logs make it difficult to track downtime events accurately and analyze root causes. Without real-time data, it’s hard to take proactive steps to reduce downtime.
Problems with Traditional, Paper-Based Maintenance Systems
While these five metrics are essential to improving plant efficiency, traditional, paper-based systems make it difficult to track and improve them. Here are the key challenges maintenance managers face when relying on outdated processes:
- Manual Data Entry Errors: Paper-based systems are prone to human error. Work orders can be lost, details can be entered incorrectly, or data can be incomplete. This leads to inaccurate maintenance records, which makes it difficult to track metrics like MTBF and OEE.
- Delayed Workflows: With paper-based work orders, communication is often slow and inefficient. Work orders need to pass through multiple hands before they reach the right technician, resulting in delays that extend MTTR and increase downtime.
- Limited Visibility into Real-Time Data: One of the biggest disadvantages of paper systems is the lack of real-time visibility. Without up-to-date information, maintenance managers are forced to make decisions based on outdated data, making it difficult to plan preventive maintenance or respond quickly to failures.
- Time-Consuming Data Analysis: Gathering and analyzing data from paper records is a labor-intensive process. Maintenance teams spend valuable time searching through logs, entering data into spreadsheets, and compiling reports. This leaves little time for proactive decision-making.
- Inconsistent Preventive Maintenance Scheduling: In a paper-based system, preventive maintenance tasks are often missed or delayed. Without automated reminders and scheduling, maintenance teams may focus more on urgent repairs, increasing reliance on reactive maintenance and decreasing PMP.
How Mobile Plant Maintenance Can Solve These Problems
A mobile plant maintenance solution can address the inefficiencies of traditional systems and help maintenance managers hit key metrics. Here’s how digital solutions offer significant improvements over paper-based processes:
- Real-Time Data Access and Visibility: With mobile plant maintenance systems, maintenance teams can access real-time data on equipment performance, repairs, and preventive maintenance tasks. This immediate visibility allows managers to track metrics like MTBF, OEE, and downtime in real time, enabling more informed and proactive decisions.
- Automated Workflows for Faster Response Times: Mobile plant maintenance solutions eliminate delays caused by manual work orders. Work orders can be created, assigned, and updated in real time, ensuring that technicians receive tasks quickly and efficiently. This reduces MTTR and helps keep downtime to a minimum.
- Improved Preventive Maintenance Scheduling: Digital maintenance systems automate preventive maintenance scheduling, ensuring that tasks are completed on time and reducing the risk of unplanned equipment failures. This leads to a higher PMP and reduces the likelihood of costly repairs and downtime.
- Centralized Data and Reporting: Mobile plant maintenance platforms collect and store data automatically, making it easy to track equipment history, performance trends, and maintenance costs. With centralized data, maintenance teams can quickly generate reports, identify inefficiencies, and make data-driven decisions to improve overall performance.
- Mobile Access for Technicians: Technicians can access work orders, equipment history, manuals, and spare parts inventory directly from their mobile devices. This means repairs can be completed faster, with fewer delays caused by searching for information or waiting for parts. As a result, MTTR is reduced, and equipment is back online sooner.
Choosing the Right Mobile Plant Maintenance Platform: Introducing Innovapptive’s Digital Solution
Now that we’ve explored how a mobile plant maintenance/mobile work order management solution can improve your team’s performance, let’s take a closer look at how Innovapptive’s mobile plant maintenance application can specifically help you meet critical metrics:
- Increasing MTBF with Real-Time Monitoring: Innovapptive’s platform provides real-time monitoring of equipment performance, enabling maintenance managers to detect issues early and schedule preventive maintenance before failures occur. Predictive analytics tools help extend MTBF by addressing potential problems before they result in downtime.
- Reducing MTTR with Mobile Work Orders: With Innovapptive, technicians can receive, update, and complete work orders from their mobile devices in real time. This allows for faster repair times, as technicians have immediate access to equipment history, spare parts inventory, and relevant documentation. As a result, MTTR is reduced, and downtime is minimized.
- Boosting OEE with Automated Performance Tracking: Innovapptive’s mobile plant maintenance solution tracks OEE by measuring availability, performance, and quality in real time. With real-time data and automated workflows, maintenance managers can identify inefficiencies, optimize equipment performance, and achieve higher OEE scores.
- Improving PMP with Automated Preventive Maintenance: Innovapptive automates preventive maintenance scheduling, ensuring that tasks are completed on time and reducing reliance on reactive maintenance. This increases PMP, leading to fewer equipment breakdowns and more efficient use of maintenance resources.
Impact of Mobile Plant Maintenance on Downtime Reduction
By offering real-time visibility into equipment health and automating key maintenance tasks, Innovapptive helps maintenance teams minimize downtime. The platform’s analytics tools also help identify the root causes of downtime, allowing managers to address recurring issues and prevent future interruptions.
Conclusion: Why Mobile Plant Maintenance/Mobile Work Order Management is the Future
Meeting critical maintenance metrics like MTBF, MTTR, OEE, PMP, and downtime percentage is essential for the success of any industrial plant. Traditional, paper-based systems make it difficult to track these metrics accurately or respond to maintenance needs quickly. By switching to a mobile plant maintenance solution like Innovapptive’s, maintenance managers can streamline their processes, reduce errors, and make data-driven decisions that improve equipment reliability and operational efficiency.
Innovapptive’s mobile plant maintenance/mobile work order management solution provides real-time data, predictive analytics, and automated workflows to help maintenance teams perform at their best. If you’re ready to take your maintenance operations to the next level, Innovapptive’s mobile solution can help you hit your maintenance metrics and keep your plant running smoothly.
FAQ
- Q: What is mobile plant maintenance, and why is it important?
A: Mobile plant maintenance is a digital system that helps manage work orders and equipment performance through mobile devices. It streamlines processes, provides real-time data, and improves key metrics like MTBF and OEE.
- Q: How does mobile plant maintenance improve Mean Time Between Failures (MTBF)?
A: By offering real-time monitoring and predictive analytics, mobile maintenance helps identify issues early, allowing for preventive maintenance that extends the time between failures.
- Q: How can mobile work order management reduce Mean Time to Repair (MTTR)?
A: Mobile work orders allow technicians to receive and complete tasks instantly, reducing delays caused by paperwork and speeding up repairs.
- Q: Why is Overall Equipment Effectiveness (OEE) important?
A: OEE measures how efficiently equipment is used. A high OEE means fewer disruptions, better performance, and higher productivity.
- Q: How does mobile plant maintenance increase Planned Maintenance Percentage (PMP)?
A: Mobile systems automate preventive maintenance scheduling, ensuring tasks are done on time and reducing unplanned downtime.
- Q: What are the main challenges with paper-based maintenance systems?
A: Paper systems lead to manual errors, delays in work order handling, limited visibility into real-time data, and missed preventive maintenance, making it harder to meet performance goals.
- Q: How does real-time data from mobile plant maintenance improve decision-making?
A: Real-time data helps managers monitor equipment and repairs instantly, allowing them to make quick, informed decisions that improve key metrics like OEE and downtime percentage.
- Q: How does Innovapptive’s mobile plant maintenance solution improve MTBF?
A: Innovapptive’s solution uses real-time monitoring and predictive analytics to catch issues early, helping prevent equipment breakdowns and increasing MTBF.
- Q: How does Innovapptive’s mobile work order solution reduce downtime?
A: Innovapptive speeds up work order processing and gives technicians instant access to equipment history and parts, reducing repair times and downtime.
- Q: What are the key features of Innovapptive’s mobile plant maintenance solution?
A: Key features include real-time mobile work orders, predictive analytics, automated preventive maintenance, real-time reporting, and SAP integration for seamless operations.
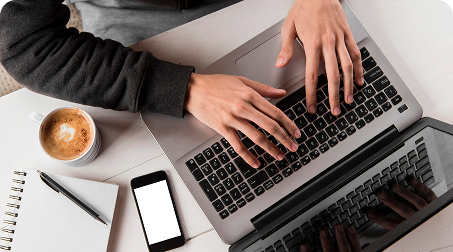
See It In Action
Schedule a personalized demo to see how our solutions can help your business thrive.
- 20-08-2025
Building the future of Industrial Operations with Innovapptive and AWS
Most manufacturers have already gone digital. Yet business outcomes haven’t moved in step. Many...
- 22-04-2025
The $3.6B Unlock: Solving the Chemical Industry’s Labor Crisis and EBITDA Pressure in One Move
“Constraints don’t slow innovation—they force it.”
- 21-04-2025
Chemical Industry's Margin Erosion: A Wake-Up Call for Operational Efficiency Amid China's Oversupply
The global chemical industry is facing mounting challenges, with revenue declines and shrinking...