Improving Warehouse Order Picking Using an SAP Mobile Inventory Solution
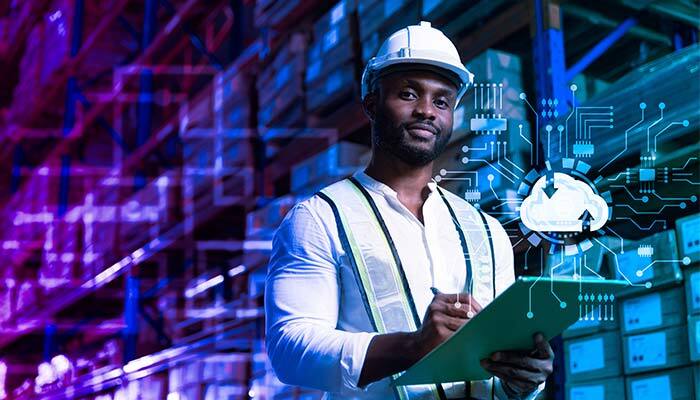
A poorly-run warehouse suffers organizational and customer service problems. An SAP Mobile Inventory Solution can help distribution centers of all sizes improve processes, accuracy, and productivity, especially when it comes to warehouse order picking. By streamlining operations, these solutions reduce manual errors and enhance overall efficiency.
What is Order Picking? Picking is selecting the right materials and quantities in a warehouse to complete a customer's order. Customers could be external clients buying finished products or internal customers, such as maintenance staff, ordering spare parts.
As picking is the most labor-intensive warehouse activity, typically occupying more than half of all staff, optimizing picking processes can lead to significant cost savings and improved employee satisfaction. Picking is also the primary interface between the warehouse and the customer. It can have a big impact on their operations if the customer receives the wrong product or picking is delayed.
Key Elements of Efficient Order Picking
An efficient picking operation depends on several components working effectively together: people, process, warehouse layout, equipment, data, and technology. Let’s take a quick look at each of these areas.
People and Process
While robot picking is now a reality, most warehouse operations are still dependent on people to pick orders. With current labor shortages and high staff turnover, the onus should be on keeping the picking process as simple as possible. New staff members need to quickly acquire product knowledge, with modern warehouses often containing thousands of Stock Keeping Units (SKUs). Utilizing technology, such as mobile inventory solutions, can help new employees quickly gain product knowledge and improve training efficiency
Expect initial productivity to be lower until the staff completes training. Picking instructions should be clear and simple, only providing the user with the information they need to do the job, e.g., product description, quantity and bin location.
Warehouse Layout and Equipment
Fundamental warehouse design seeks to minimize the movement of staff – travel time is wasted time. For picking, this includes locating fast-moving products in the most accessible parts of the warehouse, e.g., ground floor bins, closest to the dispatch bay.
The product pick sequence should follow the logical warehouse layout to avoid the picker having to backtrack, which adds time. Avoid locating similar products next to each other which often leads to picking errors. Providing the right equipment for the job is also critical. If you’re picking full pallets, a forklift truck will be ideal, but it’s not the best tool for case picking because of the time to mount and dismount (a powered order picker will be more suitable).
Data
Maybe data isn’t the first thing that comes to mind when thinking about an efficient picking operation, but it’s hard to find a warehouse operation today that doesn’t suffer from data challenges. Warehouse data relating to products, suppliers, customers and warehouse bins must be accurate. If this data is incorrect, warehouse operations will slow down, including the critical picking operation.
One of the biggest challenges for many warehouse operations is SKU proliferation, including new products, pack sizes and promotions. The old product must be exhausted before picking new stock, which adds complexity to picking operations.
Technology
Given the importance of picking in serving customers with the right product in the right quantity and at the right time, it’s surprising how many businesses still operate using paper pick sheets. Embracing digital solutions not only modernizes the warehouse but also enhances data accuracy, which is crucial for effective inventory management.
Customer orders are captured in the Enterprise Resource Planning (ERP) system – like SAP – pick sheets are printed, the warehouse staff picks products, they write quantities picked and additional information on the sheet, and then the sheet goes to the back office for confirmation in the ERP.
In many industry verticals – e.g., oil and gas, mining, and utilities – it’s still common to find warehouse processes, including picking, being operated without any barcodes and scanning.
Paper-based picking operations are time-consuming, which negatively impacts warehouse productivity. Moreover, they’re more prone to error, increasing the possibility of the customer receiving the wrong product or quantity.
Picking is an area ripe for technology intervention, whatever a warehouse's size or level of operational complexity. For a Maintenance, Repairs, and Operations (MRO) warehouse supplying spare parts to technicians in a factory or the field, a positive first step will be to deploy barcodes in the warehouse with a mobile scanning solution that integrates directly with the ERP system.
Benefits of SAP Mobile Inventory Solutions
Implementing SAP Mobile Inventory Solutions provides numerous benefits, including:
- Increased Efficiency: Streamlined processes reduce the time spent on manual tasks.
- Improved Accuracy: Real-time updates minimize errors in order picking.
- Scalability: The system grows with your warehouse operations.
- Enhanced Training: New employees can learn quickly through user-friendly interfaces.
Instead of a paper pick sheet, the warehouse picker arrives for work armed with a mobile inventory management solution that lists every product in the warehouse, quantity, and bin location. The picker moves to the first bin location, scans the product with a barcode scanner to confirm it's the correct choice, and confirms the quantity of product picked, which the mobile solution automatically updates in real-time with the backend ERP system. A mobile solution offers improved productivity, picking accuracy, and real-time visibility into operations.
Complex warehouses can justify a bigger investment in technology, but such expenditures may not be applicable in every situation. To determine where your warehouse falls, start with the operational challenge you want to solve, not with a technical solution. Robots may be great for a high-volume e-commerce warehouse but can't be justified in a small spare parts warehouse.
By adopting an SAP Mobile Inventory Solution, warehouses can position themselves for future growth and scalability.
Ready to Make a Change? We Can Help
If your warehouse remains stuck in an operational time warp with an inefficient paper picking process, you may want to consider the range of technology options now available. Innovapptive, a mobile warehouse management solution leader, has developed a customizable, easy-to-use mobile inventory application that increases warehouse productivity and accuracy. View a free demo here or call 888-464-6668 to learn more. Our experts are ready to answer your questions, listen to your needs, and configure a solution to overcome your warehouse challenges.
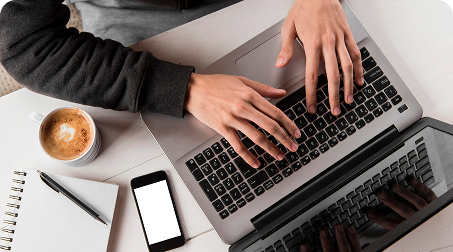
See It In Action
Schedule a personalized demo to see how our solutions can help your business thrive.
- 20-08-2025
Building the future of Industrial Operations with Innovapptive and AWS
Most manufacturers have already gone digital. Yet business outcomes haven’t moved in step. Many...
- 22-04-2025
The $3.6B Unlock: Solving the Chemical Industry’s Labor Crisis and EBITDA Pressure in One Move
“Constraints don’t slow innovation—they force it.”
- 21-04-2025
Chemical Industry's Margin Erosion: A Wake-Up Call for Operational Efficiency Amid China's Oversupply
The global chemical industry is facing mounting challenges, with revenue declines and shrinking...