Key Components of a Successful Mining Operator Rounds Program
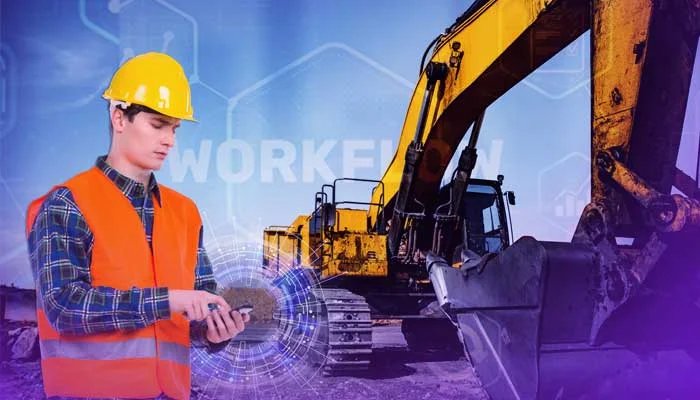
Amidst Industry 4.0 headwinds, mining (one of the oldest and highest-risk industries) is exploring innovative methods of automating equipment and minimizing environmental impact. Leading mining corporations seek ways to cut costs, and mobilize their processes such as operator rounds by experimenting with new technology. However, effective digitalization measures for frontline mining personnel are still inadequate, which might jeopardize the bottom line and wreck the mining industry. For the mining sector to thrive, the digital ecosystem must expand to integrate frontline employees and reduce field inefficiencies.
Frontline efficiency in mining largely depends upon operator rounds that monitor operations. They are critical for ensuring equipment dependability, long-term production, and occupational safety. Their efficiency is determined by the quality and accuracy of data obtained by an operator that helps companies examine, manage, and improve mining processes.
Despite this, many mining companies disregard digital optimization of operator rounds for efficiency in mine maintenance and continue to rely on paperwork to execute their task, which is where the problem lies.
Challenges to Mining Maintenance Operating Rounds
Currently, mining faces the following challenges in executing successful mining maintenance operator rounds:
Paperwork: Paperwork lacks real-time and reliable information for immediate corrective actions when safety or equipment maintenance issues are detected. Such information hampers decision-making. Nonetheless, it is widely used in the mining sector, contributing to extra non-valued operations, delayed follow-ups - decision, production, and distribution inefficiencies - and increased costs.
Safety and Maintenance Concerns: Mining staffs run complicated equipment in climatically hazardous and harsh situations. Mine upkeep is difficult with this combination. The average mine maintenance manager deals with lots of challenges, such as continual machine repair, aging equipment, limited budget, and safety concerns. To address these concerns, the right information related to mining fields is required.
Reactive Maintenance
Mining companies use expensive equipment. Any unpredictable equipment failure can stifle production and significantly reduce profits. Remote equipment monitoring takes time to get expert maintenance support for unplanned downtime or failure. Such delays and expenses impact the budget and profitability adversely.
In 2022, the top 40 mining corporations had operational costs of around $742 billion. And, it’s estimated that a typical mining operation devotes 35-50% of annual expenditure to asset maintenance and repairs. MRO (maintenance, repair, and operations) operator round challenges such as these makes digitization of operator rounds critical. By digitizing, mining companies can not only enhance their daily functioning but also avoid catastrophic disasters.
Replacing fragmented solutions with remote and mobile solutions that enable successful operation and maintenance even in low bandwidth areas can be a game changer, favoring the mining industry's transition to Industry 4.0.
Digital operator rounds can assist mining stakeholders in organizing, conducting, sharing, and reviewing site maintenance and operations and substitute error-prone hardcopy audits with an efficient electronic approach. They can help to avoid redundant labor and guarantee that all field operators have real-time visibility.
What Makes Mining Maintenance Operators Round Program Successful?
Mobile solutions are the key components of successful mining maintenance operators' round programs. Leveraging mobile solutions can greatly enhance the effectiveness of maintenance operator rounds. Mobile solutions include:
Mobile devices or tablets with software programs to access digital checklists, record results, and gather data in real time reducing the need for manual documentation and enabling improved information gathering and processing. Likewise, mining field inspection software may assist personnel in executing jobs swiftly, recording data efficiently, and reducing the scope for manual mistakes.
Integration with CMMS, ERP, and asset management systems using integration modules with APIs enables seamless transfer of data and supports proactive maintenance planning. Such integration can help technicians acquire reliable, vital
information in a shorter span even remotely on mobile devices. The high-value data thus obtained can also help with high-risk modeling. Personnel may also readily see previous, current, and upcoming inspection rounds.
Browser-style modernized browser interfaces on mobile devices, Android, Windows, and handheld computers can facilitate easy data collection and tracking field activities.
Wearable technologies having specialized software installed to capture voice and movement data can make mining a hands-free process and help with immediate expert assistance.
Management center for managing individual program components like scheduling, auditing, information collecting, and management.
Workstation: The desktop interface allows for executing procedures that are comparable to mobile operator rounds.
Support peripherals such as RFID and barcode scanners, vibration probes, temperature guns, and wireless communication devices allow for easy access to equipment information, eliminating the need for manual searching and paperwork. Scanning codes can also initiate preconfigured checklists or procedures specific to the scanned equipment, ensuring thorough inspections.
The cornerstone of operational excellence is the operator. As the industrial environment adjusts to advancements in technology, mining operators will need to be flexible to stay ahead of the curve and effectively conduct field operations. As mines go deeper and the likelihood of a collapse and hazard increases, operators will also need to delve deep into data to operate in this high-risk environment.
Upgrade Your Mine Maintenance With Innovapptive
Innovapptive's mobile operator rounds solution helps mine maintenance teams improve safety, reduce downtime, and improve compliance. The solution provides operators with the information they need when they need it, including step-by-step procedures, equipment diagrams, and operating history.
Schedule a free demo today and see how Innovapptive can help you improve your mine maintenance operations.
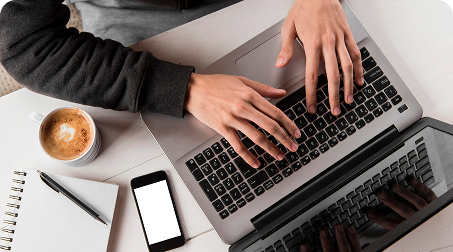
See It In Action
Schedule a personalized demo to see how our solutions can help your business thrive.
- 20-08-2025
Building the future of Industrial Operations with Innovapptive and AWS
Most manufacturers have already gone digital. Yet business outcomes haven’t moved in step. Many...
- 22-04-2025
The $3.6B Unlock: Solving the Chemical Industry’s Labor Crisis and EBITDA Pressure in One Move
“Constraints don’t slow innovation—they force it.”
- 21-04-2025
Chemical Industry's Margin Erosion: A Wake-Up Call for Operational Efficiency Amid China's Oversupply
The global chemical industry is facing mounting challenges, with revenue declines and shrinking...