Making Safety Training Lessons Stick with Digital Work Instructions
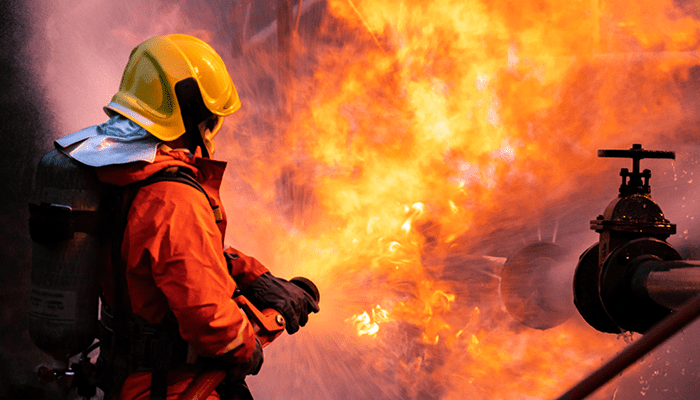
A massive explosion rocked the Phillips Petroleum Company’s Pasadena chemical plant on October 23, 1989. It shook the area, registering 3.5 on the Richter scale while killing 23 workers and injuring another 130.
That incident spurred the formation of Houston’s Health and Safety Council (HASC). This industry association of area petrochemical plants is dedicated to improving the safety and compliance of each of its member companies. The council today offers customizable, state-of-the-art safety, health and environmental training, certification, contractor pre-qualification and background screening among other services.
The Phillips explosion was later determined to have been caused when a large quantity of flammable gas ignited during a routine maintenance check on a polyethylene reactor. Nineteen of the workers killed were Phillips employees while the others were outside contractors.
Maintenance checks and turnarounds are some of the most dangerous times at any chemical or petrochemical plant, especially when regular plant workers have to interact with contractors that may be unfamiliar with the facility, its layout and safety procedures.
HASC has greatly expanded in the more than three decades since its 1990 founding not long after the Phillips Pasadena explosion. The organization offered a single safety training course taught by volunteers in a one-room building at its beginning. Today, it delivers more than 2,000 different courses to employees of more than 3,000 member companies and 12,000 non-member ones.
HASC was hardly the first such industrial safety council nor is it the largest. Louisiana’s Alliance Safety Council (ASC), formed in 1958, boasts 8,000 member companies. ASC was a founding member of the Association of Reciprocal Safety Councils. This national network standardizes safety courses to minimize redundant training and allow contractors to get credit for training as they travel from facility to facility.
Getting the Most from Safety Council Courses with Digital Work Instructions
Safety councils like HASC and ASC provide a needed service to chemical companies. They demonstrate the value of collaboration and cooperation between companies and industries toward a common goal. Plants would have to shoulder a greater burden to ensure the safety of their sites and their workers without these collective resources.
The industry’s changing demographics mean chemical and petrochemical plants are having to hire younger, less-experienced frontline maintenance workers to fill staffing gaps. The safety councils offer one method of safety and work skills training. But what happens when trainees return to the plant and their jobs? How can their training be reinforced and the learning continue?
One component of a connected worker strategy provides an effective answer. Digital work instructions let veteran maintenance technicians remotely mentor and guide less-experienced coworkers using smartphones, tablets and hands-free wearables such as smart glasses.
If one of those new hires is working to repair a faulty valve, the experienced technician can be in constant digital communication with him via a two-way conference call and offer instructions, deliver advice and answer questions in real time. The veteran can also send PDFs that spell out standard operating procedures (SOPs) and safety protocols. This happens seamlessly, no matter the distance between the two workers.
This ensures the valve repair is done right safely the first time, cutting down on costly reworks. The rookie technician can have his safety council training reinforced and expanded upon, ensuring the company realizes a positive return on that educational investment and mitigating the risks of incidents, fines, penalties and lost production.
Learn More about How Digital Work Instructions Can Improve Chemical Plant Safety
Innovapptive, a pioneer in providing connected worker platforms for the chemical industry, offers a digital work instructions solution that can deliver greater plant safety while minimizing downtime and revenue disruptions. Innovapptive understands chemical companies’ unique safety needs. That’s why our Digital Work Instructions product offers the ease of use, functionality, flexibility and agility chemical plants and their frontline workers want.
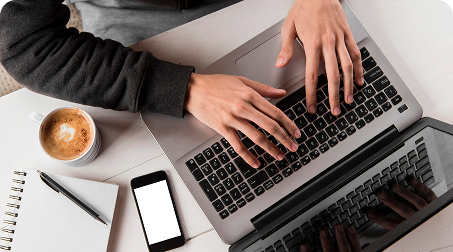
See It In Action
Schedule a personalized demo to see how our solutions can help your business thrive.
- 20-08-2025
Building the future of Industrial Operations with Innovapptive and AWS
Most manufacturers have already gone digital. Yet business outcomes haven’t moved in step. Many...
- 22-04-2025
The $3.6B Unlock: Solving the Chemical Industry’s Labor Crisis and EBITDA Pressure in One Move
“Constraints don’t slow innovation—they force it.”
- 21-04-2025
Chemical Industry's Margin Erosion: A Wake-Up Call for Operational Efficiency Amid China's Oversupply
The global chemical industry is facing mounting challenges, with revenue declines and shrinking...