Mastering Gemba Walks for Continuous Improvement
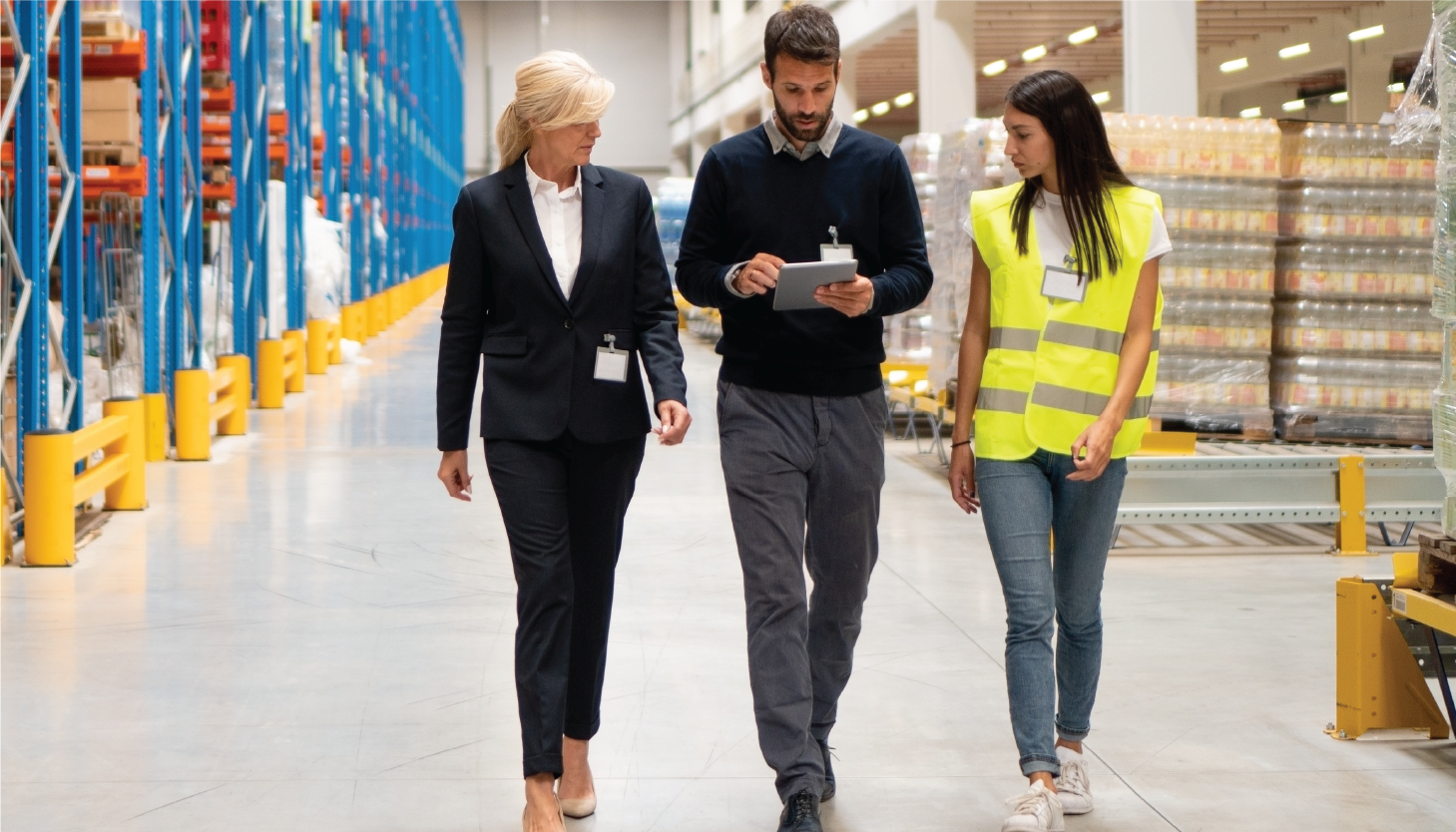
Effective leadership in operations hinges on the ability to identify, analyze, and resolve inefficiencies in real-time. For managers and plant supervisors striving to drive continuous improvement (CI), Gemba walks offer a practical, data-driven method to optimize processes and enhance collaboration. When structured and standardized, Gemba walks equip leaders with actionable insights that lead to significant operational benefits.
This blog will explore what Gemba walks are, their importance in operational excellence, and how a standardized approach can empower management teams to better achieve their CI goals through improved scheduling, streamlined data collection, precise analysis, and enhanced collaboration.
What Is a Gemba Walk?
The term "Gemba" is derived from the Japanese word meaning "the actual place" or "where the real work happens." A Gemba walk is a structured practice where managers and supervisors visit the shop floor or operational site to observe workflows, communicate with team members, and identify areas for improvement.
Gemba walks are not about fault-finding—they aim to foster understanding and collaboration between management and frontline workers. By actively participating in the operational environment, managers can uncover inefficiencies, test workflows, and gather the contextual insights needed to implement meaningful process changes.
Key Principles of a Gemba Walk
- Go and See: Physically visit the location where the operations occur. Observing processes firsthand provides invaluable insights that aren't evident in reports or data alone.
- Engage and Ask: Interact with employees and ask thoughtful questions. Workers often have untapped knowledge about bottlenecks and suggestions for improved processes.
- Respect the Flow: Avoid disrupting workflow during the walk. The goal is to observe current operating conditions as they happen.
These simple yet impactful principles ensure that managers gain a holistic understanding of day-to-day activities while maintaining a collaborative, non-disruptive approach.
Why Are Gemba Walks Crucial for Continuous Improvement?
Continuous Improvement (CI) thrives on an organization’s ability to identify inefficiencies and implement lean, effective solutions. Gemba walks serve as a CI enabler by helping managers bridge the gap between theoretical problem-solving and real-world implementation.
Here are the ways Gemba walks elevate CI efforts in manufacturing and industrial operations settings:
- Enhanced Communication: Visiting the shop floor fosters direct communication between management and employees, creating an environment where insights flow both upward and downward.
- Data-Driven Insights: Observing operations firsthand reveals real-time pain points and opportunities for streamlining workflows.
- Employee Empowerment: Collaborating with team members during the walk fosters a culture of mutual respect, empowering staff to share feedback and take ownership of proposed changes.
- Faster Problem Resolution: Potential issues can be identified and addressed faster through direct observation and discussion.
- Improved Operational Alignment: Gemba walks ensure management and operations teams are aligned on priorities and improvement initiatives.
Standardizing Gemba Walks for Optimal Results
While Gemba walks are inherently beneficial, their true potential is unlocked through standardization. Standardized Gemba walks provide a repeatable framework for scheduling, data collection, and analysis, ensuring consistency and long-term impact.
1. Implement a Scheduled Approach
Random or infrequent Gemba walks often fail to generate the momentum needed for meaningful improvements. Instead, create a Gemba calendar with fixed times for walkthroughs.
Benefits of Scheduled Walks
- Managers develop the habit of regularly engaging with ground-level operations.
- Employees know when to expect leadership on the floor, fostering open communication.
- It ensures continuous improvement is prioritized consistently across shifts and teams.
2. Optimize Data Collection
Raw observations on their own lack the structure needed to translate insights into action plans. Equip managers with robust frameworks for collecting, categorizing, and prioritizing data.
Steps to Standardize Data Gathering
- Use standardized templates to record observations.
- Categorize issues into groups such as efficiency bottlenecks, safety concerns, or equipment performance gaps.
- Document feedback from frontline teams for later analysis.
3. Analyze and Address Key Findings
Data gathered during Gemba walks must be analyzed systematically to uncover root causes and develop actionable solutions.
Tactics for Effective Analysis
- Leverage software tools designed for operational data analysis, such as predictive analytics platforms.
- Set clear KPIs to assess the impact of previous CI initiatives.
- Develop visual reports to share pain points and solutions with the broader team.
4. Cultivate Collaboration
One of Gemba walks' strongest attributes is their ability to deepen collaboration between management and workers. Standardizing team communication and feedback loops can help sustain this momentum.
Fostering Long-Term Collaboration
- Hold regular post-Gemba huddles to review insights and discuss next steps with all relevant stakeholders.
- Include team leads in the planning and execution of CI initiatives.
- Celebrate incremental successes to keep morale high across teams.
Gemba Walk Success Stories
Organizations that incorporate structured Gemba walks into their operational framework often see measurable improvements in efficiency and collaboration. For instance, a leading manufacturing plant implemented standardized Gemba walks to address inefficiencies in their supply chain. Over six months, they achieved a 20% reduction in process downtime while improving employee engagement levels.
Another case involved a plant supervisor using Gemba data to advocate for replacing legacy machinery. The result? A 95% increase in production output within just three months of upgrading the equipment.
These real-world examples underscore the value of a structured, collaborative approach to Gemba walks.
Next Steps to Transform Your CI Approach
Gemba walks have the power to transform both processes and culture. By taking deliberate steps to standardize scheduling, structure data collection, foster collaboration, and analyze results consistently, managers can drive exceptional outcomes across their organization.
If you're looking to build a culture of continuous improvement or take your operations to the next level, start incorporating standardized Gemba walks into your daily workflow. Need more resources on streamlining data collection and enhancing collaboration? Feel free to explore our whitepaper or consult one of our experts for tailored insights.
Achieving operational excellence begins on the floor—and it starts with Gemba.
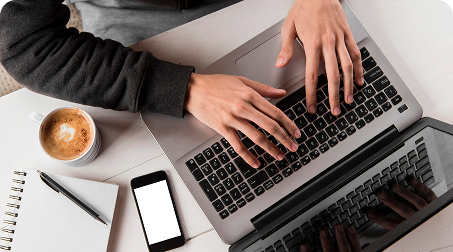
See It In Action
Schedule a personalized demo to see how our solutions can help your business thrive.
- 20-08-2025
Building the future of Industrial Operations with Innovapptive and AWS
Most manufacturers have already gone digital. Yet business outcomes haven’t moved in step. Many...
- 22-04-2025
The $3.6B Unlock: Solving the Chemical Industry’s Labor Crisis and EBITDA Pressure in One Move
“Constraints don’t slow innovation—they force it.”
- 21-04-2025
Chemical Industry's Margin Erosion: A Wake-Up Call for Operational Efficiency Amid China's Oversupply
The global chemical industry is facing mounting challenges, with revenue declines and shrinking...