Mine Maintenance Strikes Gold with mWorkOrder and IBM Maximo
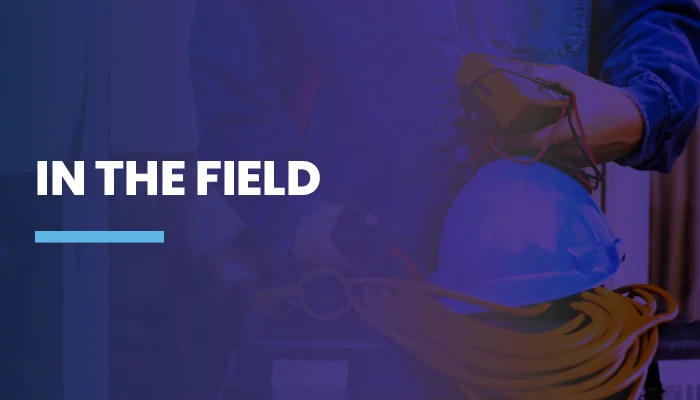
Mining is a challenging and often dangerous industry. It faces special problems in terms of daily equipment and machinery maintenance. Of the risks that mining comes with, safety is the greatest of all. Mines use dangerous and complex equipment to extract metals and minerals from the earth and process them for further use. This equipment suffers from frequent breakdowns, threatening production shutdowns and stopping revenue flows.
To keep the operations running, mines need human intervention from frontline workers and maintenance technicians, making them irreplaceable resources. Unfortunately, many mining companies have failed to equip their frontline workers with technological advancements.
Scenario
A major global mining company focused on the exploration and production of lead with extensive operations around the world seeks to empower its frontline maintenance technicians and operators to work more effectively, safely and efficiently.
The company was looking for a mobile solution that could provide the required information, guidance and resources its frontline workers needed to efficiently perform their jobs. The mine uses the IBM Maximo asset management system to help its maintenance team, but it only digitizes a portion of the mine’s operational data. The maintenance staff still uses a legacy system that doesn’t meet the needs of modern workers.
The mine has tried several mobile applications in the past but their frontline maintenance technicians didn’t want to use them because of poor UI/UX. Additionally, poor network availability in remote locations, complex workflows and security risks were key factors triggering resistance to change. The frontline workers would rather use tried-and-true conventional methods, despite their limitations. Not being able to find a suitable mobile application the workers will consistently use has led to poor return on investment, more reworks, higher overtime and lower productivity.
Mine executives worry they may never be able to rectify this increasingly expensive and unworkable situation. They want a mobile plant maintenance solution that is:
- Easy-to-understand UI/UX
- Works in online and offline modes
- Offers rapid synchronization capabilities
- Enables faster and easier data collection
Challenges
The mining company has invested considerable sums in equipment maintenance and upkeep to minimize downtime. Each of its mines has a maintenance staff charged with ensuring equipment such as drill tools, earthmovers, excavators, crushers, feeders, conveyors, etc., are in proper, safe working order.
The workers in the globally widespread mines lack onsite guidance in case they need expert advice. In times like this, new hires find themselves in a fix. They feel stuck and are unable to complete the assigned task on time. The trial-and-error method they’re reduced to using causes errors, loss of time and rework.
There are several other challenges, such as:
- Ensuring workflow efficiency
- Assuring correct data collection, sharing and accuracy
- Dealing with lengthy synchronization
- Overcoming issues of poor UI/UX
- Ensuring safety compliance
Solution
The mining company needs to understand that despite earlier disappointing experiences with mobile plant maintenance apps, mobile-first technology can have a positive impact on their operations if they could find a vendor that met their unique needs.
They need a mobile maintenance data collection and sharing solution that can be integrated with IBM Maximo to enable their maintenance team to adopt an efficient proactive maintenance process. They also want a solution that makes frontline workers’ lives easier, and that facilitates faster and safer completion of work.
Innovapptive’s mWorkOrder for IBM Maximo can help the mining company simplify and digitalize their EAM processes. mWorkOrder for IBM Maximo automates inefficient maintenance processes. It eliminates manual data capture, enables immediate electronic work order assignment, boosts data accuracy and timeliness, permits guided work instruction and improves wrench time, leading to greater asset uptime, fewer backlogs and a safer plant.
The mobile maintenance solution utilizes native mobile devices such as smartphones, smartglasses, smartwatches, scanners and barcode readers to empower mine maintenance technicians and operators to accomplish their jobs faster, better and safer. It supports remote online guidance with digital work procedures, videos and an option to connect with offsite subject matter experts via two-way conferencing to get digital work instructions.
The intuitive UI/UX makes the tool usable, accessible, desirable and findable. It can be integrated into wearables including smart glasses and smartwatches, to enable voice-based, hands-free operations from anywhere on the mine site. It works in online and offline modes and is ideal for mining companies with widespread operations in remote locations lacking Wi-Fi connectivity.
The solution includes prepackaged and reconfigurable use cases including - assembly, quality control, inspections, changeovers, equipment setup, installations, field services and more.
mWorkOrder for IBM Maximo in Action
The production descriptions above are nice, but how about an example of the solution in an actual field situation?
The mine has a diesel generator that’s been acting up in recent days. This generator supplies power to a key piece of production equipment. If the generator goes down, it could affect production for several hours or more.
Carlos, the mine maintenance supervisor, gets a report the generator is having problems again. Carlos is facing a technician shortage and is understaffed today. As other technicians are already on projects, he dispatches Mike, a relatively new and inexperienced technician to perform an inspection on the generator and report back.
Mike hops in his truck and drives to the generator location, which is distant from the maintenance shop on the far side of the site. Mike looks over the generator, opens some panels and discovers the problem: A fuel shut-off valve is malfunctioning and cutting off fuel when it’s not supposed to do so. The valve appears near total failure, but Mike can’t be sure as he hasn’t worked on this brand before and is unfamiliar with it. The tech school he attended used a competing generator brand for classroom simulations.
Mike whips out his smartphone. However, rather than making a call, he uses the device to pull up the mWorkOrder application. Mike’s only been on the job for two months, but he likes mWorkOrder. The UI is very intuitive and he quickly learned to make use of it. Once opened, Mike digitally fills out a generator inspection form, noting the fuel valve problem on the checklist. The young technician then automatically uploads the completed form to the mine’s back office IBM Maximo system.
Back at the maintenance shop, Carlos gets a notification that Mike has finished the inspection and pulls up the results. He understands this is a serious problem that needs immediate attention. Carlos knows Mike doesn’t have the needed experience to tackle this issue, but he has no other technician he can send to take Mike’s place. Yet Carlos doesn’t worry or panic. Unlike under the mine’s old legacy system, Carlos has a convenient remedy in hand that will help get the situation resolved with a minimum of disruptions, even with a new hire in the field.
The maintenance supervisor creates an emergency work order, assigns it to Mike and sends a notification to the technician to meet via a two-way conference. Mike dons his smartglasses and connects with Carlos, who is in his office at the maintenance shop. Mike tells Carlos about the fuel valve but says he’s unsure of how to repair it. Carlos instructs Mike to use his smartphone to take a photo of the valve and send it to him. Mike complies.
Carlos looks over the photo and immediately recognizes the problem. He’s seen this before at another mine when he was a technician. Carlos tells Mike to hold on a minute, he has the solution.
Carlos uses mWorkOrder’s annotation feature to make some notes on the picture. He then pulls up an electronic SOP and makes a pdf of the fuel valve specification page from the manufacturer’s troubleshooting guide. He sends the annotated photo, the SOP and the pdf to Mike, who is still standing two miles away in front of the generator.
Mike receives and opens the documents. He then proceeds with the repair as Carlos watches via the smartglasses camera and offers instructions. It’s a simple, but critical repair that takes only a few minutes. However, had the repair not been made today, the valve likely would have failed within a short time, causing a production halt.
Under the mine’s legacy system, Mike would have had to:
- Return to the maintenance shop to turn in the inspection
- Wait for a paper work order to be created
- Get on a computer
- Search for the SOP
- Dig through a binder for the manufacturer’s guide
- Look for the veteran to ask some questions
- Return to the job site
- Conduct the repair
- Hope it was properly done with no reworks
Instead, with mWorkOrder for IBM Maximo (as well as the SAP version), Mike never had to leave the generator. He was able to:
- Conduct the inspection
- Automatically upload the results to the back-office system
- Receive an emergency work order while in the field
- Take a photo of the malfunctioning part to share with his supervisor
- Get guided work instructions via a two-way conference call
- Conduct the repair
The result is:
- Greater productivity
- Less downtime
- No rework
- No backlog
- No safety incident
Expected Benefits
Based on our previous customer’s best experiences, mWorkOrder users can realize up to a:
- 98% higher asset uptime
- 20% greater wrench time
- 50% drop in work order backlogs
- 26% lower maintenance costs
- 40% reduction in safety incidents
To learn more about how Innovapptive and our mWorkOrder mobile plant maintenance solution for IBM Maximo can help your mine streamline workflows, improve data accuracy, boost safety compliance and increase frontline worker productivity, read our ebook. Then schedule a free demo or call 844-464-6668.
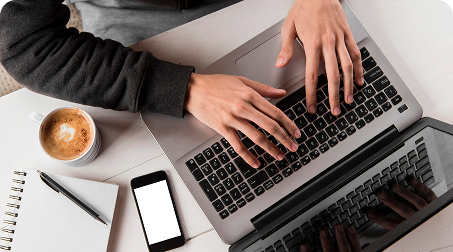
See It In Action
Schedule a personalized demo to see how our solutions can help your business thrive.
- 20-08-2025
Building the future of Industrial Operations with Innovapptive and AWS
Most manufacturers have already gone digital. Yet business outcomes haven’t moved in step. Many...
- 22-04-2025
The $3.6B Unlock: Solving the Chemical Industry’s Labor Crisis and EBITDA Pressure in One Move
“Constraints don’t slow innovation—they force it.”
- 21-04-2025
Chemical Industry's Margin Erosion: A Wake-Up Call for Operational Efficiency Amid China's Oversupply
The global chemical industry is facing mounting challenges, with revenue declines and shrinking...