Not Getting the Picture? PDF/Image Markup Makes Operator Rounds and Work Order Communications Crystal Clear
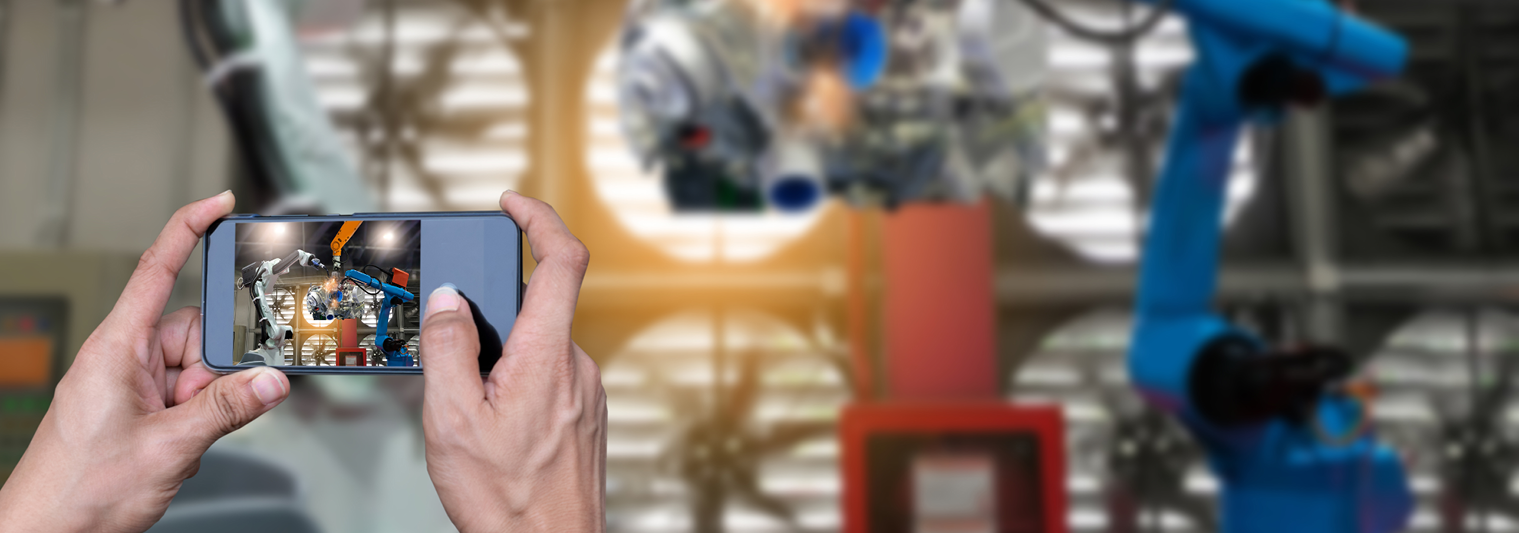
Effective asset management and maintenance programs rely on clear communications between supervisors and staff. Garbled instructions and misunderstood directions result in reduced wrench time and frequent reworks to fix a problem. In this blog, discover how digital transformation technology can:
- Eliminate time-consuming and error prone paper processes,
- Make for more faster, more efficient operator rounds,
- Improve communication between a supervisor and field maintenance technicians,
- Increase technician wrench time and productivity,
- Ensure work is done right the first time,
- Cut down on unplanned shutdowns due to improper maintenance.
Operator rounds serve a valuable purpose at any industrial facility. It’s during these walkthroughs where equipment is observed, issues uncovered, and problems reported. Without them, production and performance would quickly deteriorate. It’s imperative that operator rounds be done seriously and thoroughly.
Many plants and industrial organizations rely on a paper process when conducting operator rounds. A technician walks around with a clipboard in hand, physically documenting potential problems that must be addressed. When any are found, the paper form is dutifully passed up the chain of command for further action.
However, it’s not always a smooth trip up the chain. A technician may get distracted by a fellow employee eager to talk about last night’s ballgame and leaves the form incomplete to fill out later. A supervisor gets the incomplete form, but can’t read it now because of other, pressing matters, so it languishes on a desk. Add to that, the tech has gone home early due to a sick child. So, nothing is done.
Unfortunately, the technician found a leaking valve on a key piece of production equipment. Due to his haste to get to his child, he scrawled a quick note about the valve, but his writing was sloppy, and the supervisor couldn’t make out the valve’s location or the severity of the problem. That night, the valve failed, causing production to halt until the source of the problem could be found. But it had already been found earlier in the day, just no one could make out the note.
This needn’t happen to your organization. Digital transformation technology offers real-time communication, collaboration and confirmation between a supervisor and staff to ensure small problems don’t grow into large ones.
What is digital transformation? Essentially, it’s the integration of digital technology into all areas of a business, fundamentally changing how you operate and deliver value to customers. It’s rethinking old operating models and becoming more agile in your ability to respond to issues, customers and rivals. More specifically, it’s a business cultural change.
Many companies offer electronic operator rounds solutions. Each of these products have their benefits. One solution – mWorkOrder – stands out in the marketplace. mWorkOrder is offered by Innovapptive, a mobile-first digital transformation provider. Innovapptive understands the unique needs of the industrial marketplace. Its solutions meet these one-of-a-kind requirements.
Innovapptive’s mWorkOrder adds clarity and improves communications between a supervisor and a technician. Suppose an inspector notes a faulty pump during a round. The inspector notes the problem in real time using a mobile, hand-held device. The maintenance tech assigned to repair the pump, however, is new and unfamiliar with this brand and model number. The supervisor can immediately send a PDF of a maintenance troubleshooting guide. Not only that, the supervisor can electronically mark up the guide with additional notes and instructions to help the tech better understand and repair the problem the first time.
Or, let’s say neither the supervisor nor the tech knows the pump brand, model number or specs. In this case, the tech can take a picture of the pump’s tag and send it to the supervisor. The tech can also photograph the problem area and add callouts, draw in arrows and add shapes to illustrate the situation. The supervisor now sees the model number and sends the right guide, without the tech ever having to leave the pump’s location.
Finally, supervisors, managers and directors can digitally sign work order documents as part of the approval process. PDFs and photos become a permanent part of the work order, providing documentation of repairs and a history of that asset.
With mWorkOrder and the PDF and Image Markup functionality, users see a host of benefits. These include:
- Faster operator rounds,
- A more efficient and accurate digital work order process,
- Clearer communications between supervisors and technicians,
- Greater wrench time and productivity,
- Fewer reworks, which reduces unplanned production shutdowns.
To learn more about mWorkOrder’s PDF and Image Markup capabilities, click here sign up for a free demo or call us at 844-464 6668. Our experts are standing by to introduce how digitally transforming your operator rounds can turn a business challenge into an advantage.
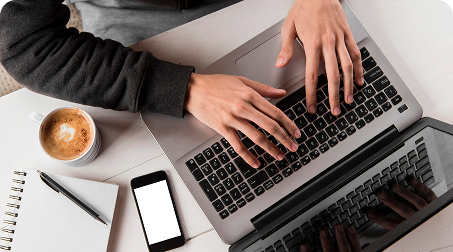
See It In Action
Schedule a personalized demo to see how our solutions can help your business thrive.
- 22-04-2025
The $3.6B Unlock: Solving the Chemical Industry’s Labor Crisis and EBITDA Pressure in One Move
“Constraints don’t slow innovation—they force it.”
- 21-04-2025
Chemical Industry's Margin Erosion: A Wake-Up Call for Operational Efficiency Amid China's Oversupply
The global chemical industry is facing mounting challenges, with revenue declines and shrinking...
- 21-04-2025
Why Wrench Time Isn’t Improving: The Hidden Costs of Traditional Maintenance Scheduling
For years, industrial leaders have relied on a common but flawed assumption: "Better planning and...