Proactive Utility Maintenance Using Mobile Operator Rounds
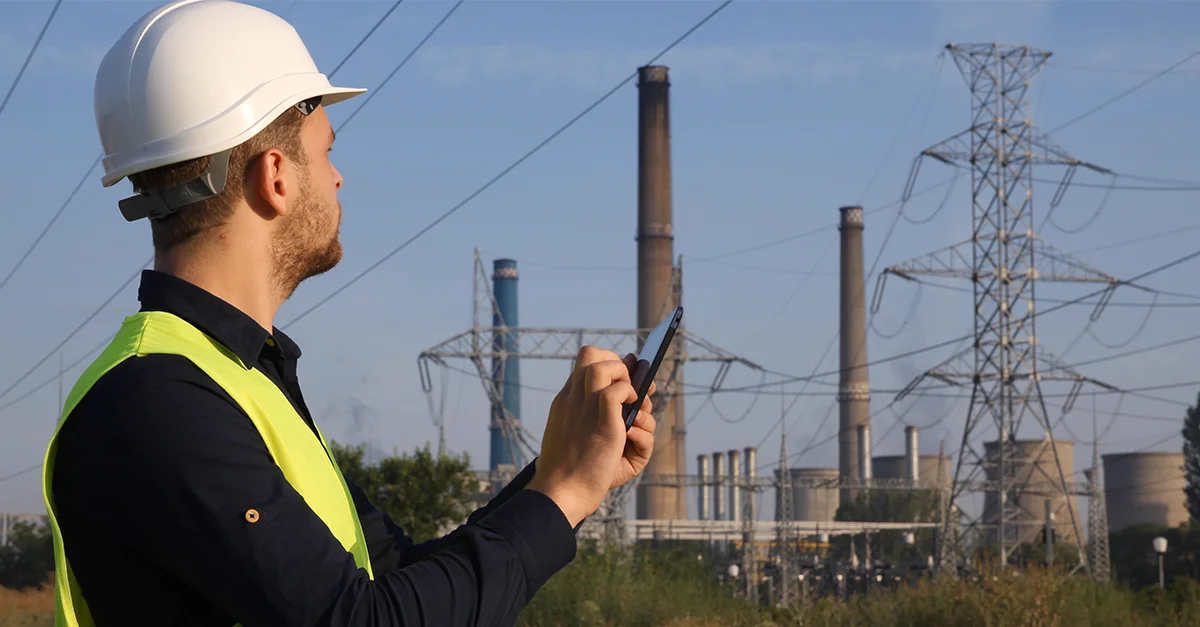
Utilities want greater asset uptime. Paper asset inspections are slow and inaccurate. Mobile operator rounds quickly identify equipment and safety issues so that utility maintenance departments can take proactive action before they become downtime-causing problems.
One hour of unplanned downtime costs utilities $300,000 on average. On top of the monetary costs, utilities may face customer attrition due to poor services. So, utilities should keep looking for ways to enhance their maintenance operations. Utility networks are extended and more complex than that of other industries. They need a more agile frontline workforce to stay proactive and deliver better service to their customers. Let’s see how mobile operator rounds solutions will help.
Challenges Facing Utility Operators Rounds
Utilities are more vulnerable to natural disasters than any other asset-intensive industry. They’re the first to take the blow when a hurricane or an earthquake hits. For example, Hurricane Irma left more than 60% of Florida’s population without power in 2017. Such natural calamities cause a $20 to $55 billion loss for utilities every year. Though they have no power to prevent them, they can speed up maintenance activities to prevent further losses.
Utilities are upgrading their equipment and toolkits with latest technologies and innovations to deliver faster services. There’s still room for improvement. In frontline operations like operator rounds, most utilities are still using paper forms and checklists. These conventional practices are holding them back from leveraging the full potential of digital transformation.
Paper-based operator rounds, inspections and checklists bring problems that erase many of the task’s benefits. These issues render the inspections ineffective at best, useless at worst. They also lead to increased costs, lost productivity, revenue disruptions, and potential fines and penalties.
An operator round inspection needs to be thorough to be effective. A static paper checklist just can’t achieve this. It’s not easy to alter a paper checklist or form to reflect changing business or operational needs. Furthermore, an inspector may skip checklist items or leave them uncompleted. Decision makers need the completed checklist quickly to figure out what action to take.However, paper-based operator rounds are static objects. The information remains unseen and unknown until the technician completes the form and turns it in or manually uploads data into an enterprise resource planning (ERP) system, such as SAP.
Leveraging Mobile Operator Rounds Solutions
Mobile devices (smartphones, tablets, wearables, etc.) replace paper checklists and binders, enabling technicians to collect accurate, mission-critical information in less time. Technicians access digital forms on their device to conduct the round. These digital forms are dynamic, unlike paper checklists, meaning they can be quickly and easily changed on the fly to better meet a plant’s situational needs. The data is immediately uploaded into the back-office system, letting decision makers view inspection results in real time.
Technicians scan equipment barcodes and complete the digital form by checking customized data fields to indicate the present operational status and safety condition. That information is immediately uploaded electronically into the back-office system. Decision makers can view inspection information on their own mobile device or on a desktop app. They can also communicate and collaborate with the technician as he or she is conducting the round. This means nothing is overlooked, questions or concerns can be instantly addressed, risk and threat levels quickly ascertained, and action taken before downtime is incurred or a safety threat emerges.
To sum up, mobile operator rounds solutions help you overcome these key challenges by replacing paper-based processes:
- Lack of real time visibility
- Lack of real time data visibility
- Low/no value data
- Lack of risk modeling
Want to Learn More about Mobile Operator Rounds?
Our experts are always happy to help you learn more about mobile operator rounds solutions and how it helps your utility? Schedule a free demo today or call us at 844-464-6668.
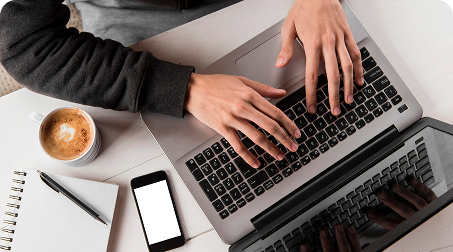
See It In Action
Schedule a personalized demo to see how our solutions can help your business thrive.
- 20-08-2025
Building the future of Industrial Operations with Innovapptive and AWS
Most manufacturers have already gone digital. Yet business outcomes haven’t moved in step. Many...
- 22-04-2025
The $3.6B Unlock: Solving the Chemical Industry’s Labor Crisis and EBITDA Pressure in One Move
“Constraints don’t slow innovation—they force it.”
- 21-04-2025
Chemical Industry's Margin Erosion: A Wake-Up Call for Operational Efficiency Amid China's Oversupply
The global chemical industry is facing mounting challenges, with revenue declines and shrinking...