Root Cause Analysis: Identifying and Eliminating Problems at Their Source
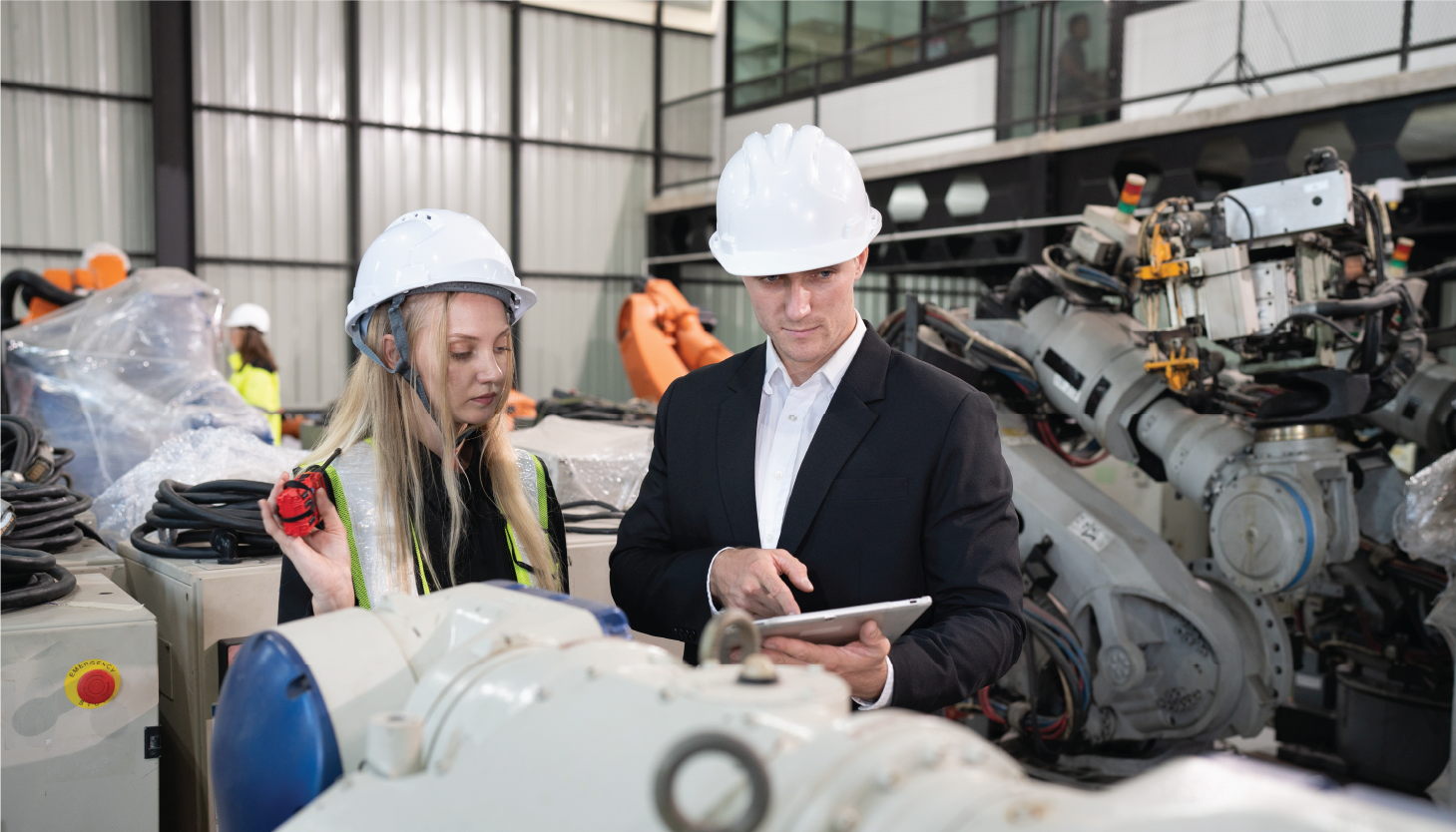
Introduction: Why Root Cause Analysis Matters
Workplace safety and compliance issues often arise due to overlooked systemic problems rather than isolated incidents. Simply fixing what’s broken without addressing the root cause leads to recurring failures, downtime, and increased risks. Root Cause Analysis (RCA) provides a structured way to investigate incidents, identify their root causes, and implement long-term solutions.
By using RCA techniques like 5-Why RCA, Fishbone Root Cause Analysis, and the Ishikawa Fishbone RCA, businesses can move beyond treating symptoms and instead address the real problems that cause safety risks, equipment failures, and compliance breaches.
Understanding Root Cause Analysis (RCA)
Root Cause Analysis is a systematic process used to uncover the primary reasons behind failures, defects, or safety incidents. Instead of addressing surface-level symptoms, RCA digs deeper to identify fundamental issues that, if resolved, prevent recurrence.
Effective RCA methods are widely used in RCA facility management, workplace safety programs, and compliance-driven industries like chemical manufacturing, oil & gas, and mining.
Key RCA Techniques:
5-Why RCA
The 5-Why method involves repeatedly asking “Why?”—typically five times—to drill down to the root cause of a problem.
Example: A machine breakdown investigation may start with, "Why did the machine stop?" and continue until the true cause, such as inadequate maintenance, is revealed.
Fishbone Root Cause Analysis (Ishikawa Fishbone RCA)
Also called the Ishikawa Fishbone RCA, this technique visually maps out potential causes of a problem, categorized into groups such as People, Process, Equipment, Materials, Environment, and Management.
Example: If workers frequently report injuries, a Fishbone RCA diagram may reveal poor training, faulty equipment, or hazardous work conditions as contributing factors.
Failure Mode and Effects Analysis (FMEA)
FMEA is a proactive RCA method used to assess potential failure points before they lead to real problems. By ranking issues based on severity and likelihood, organizations can prioritize risk mitigation.
Fault Tree Analysis (FTA)
FTA uses a top-down approach to trace problems back to their origin by mapping out events in a logical sequence. This is particularly useful for safety-related incidents and compliance investigations.
Applying RCA in Facility Management and Risk Compliance
Many safety incidents and operational failures stem from preventable issues. RCA facility management practices ensure that problems are thoroughly investigated and permanently resolved rather than repeatedly occurring.
Example: In a chemical plant, a minor equipment failure might seem like a routine issue. However, 5-Why RCA could reveal that improper maintenance scheduling led to gradual deterioration. A Fishbone Root Cause Analysis might highlight poor training or defective components as additional contributing factors.
By applying Ishikawa Fishbone RCA and other RCA methodologies, organizations can:
✅ Prevent recurring incidents✅ Ensure compliance with safety regulations
✅ Improve equipment reliability and reduce downtime
✅ Enhance worker safety and operational efficiency
Challenges in Traditional RCA Processes
Despite its benefits, RCA can be time-consuming and prone to human error when managed manually. Some common challenges include:
- Data silos: Information is often scattered across spreadsheets, paper reports, and disconnected systems.
- Delayed investigations: Without a structured process, RCA efforts take longer, increasing the risk of repeat failures.
- Inconsistent documentation: Lack of standardized reporting can lead to incomplete or inaccurate root cause identification.
- Compliance risks: Failure to conduct proper RCA can result in regulatory fines, operational disruptions, and reputational damage.
To address these challenges, digitization is key.
Digitizing Root Cause Analysis with Innovapptive
Traditional Root Cause Analysis (RCA) methods rely on manual processes, spreadsheets, and disconnected systems, making investigations slow, inconsistent, and prone to human error. A digitized RCA approach streamlines investigations, standardizes documentation, and ensures faster resolution of safety incidents and operational failures.
Innovapptive helps organizations overcome these challenges by:
- Automating RCA workflows to quickly identify the root cause of incidents and defects.
- Capturing real-time data through mobile-enabled reporting for accurate and timely analysis.
- Ensuring compliance with built-in regulatory tracking, reducing the risk of fines and violations.
- Facilitating collaboration across teams to drive faster decision-making and corrective action.
By eliminating paperwork and centralizing RCA processes, Innovapptive enables organizations to proactively prevent incidents, improve operational efficiency, and maintain compliance with industry standards.
Take Control of RCA – Request a Demo
Identifying and eliminating root causes is essential for a safer, more compliant workplace. If you’re looking to digitize your RCA process and prevent recurring incidents, it’s time to explore a modern solution.
Schedule a demo today to see how Innovapptive can transform your risk management and compliance efforts.
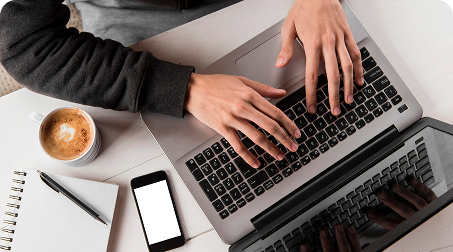
See It In Action
Schedule a personalized demo to see how our solutions can help your business thrive.
- 22-04-2025
The $3.6B Unlock: Solving the Chemical Industry’s Labor Crisis and EBITDA Pressure in One Move
“Constraints don’t slow innovation—they force it.”
- 21-04-2025
Chemical Industry's Margin Erosion: A Wake-Up Call for Operational Efficiency Amid China's Oversupply
The global chemical industry is facing mounting challenges, with revenue declines and shrinking...
- 21-04-2025
Why Wrench Time Isn’t Improving: The Hidden Costs of Traditional Maintenance Scheduling
For years, industrial leaders have relied on a common but flawed assumption: "Better planning and...