Stop Endangering Your Company, Employees and Assets; Digitally Transform Risk Assessment
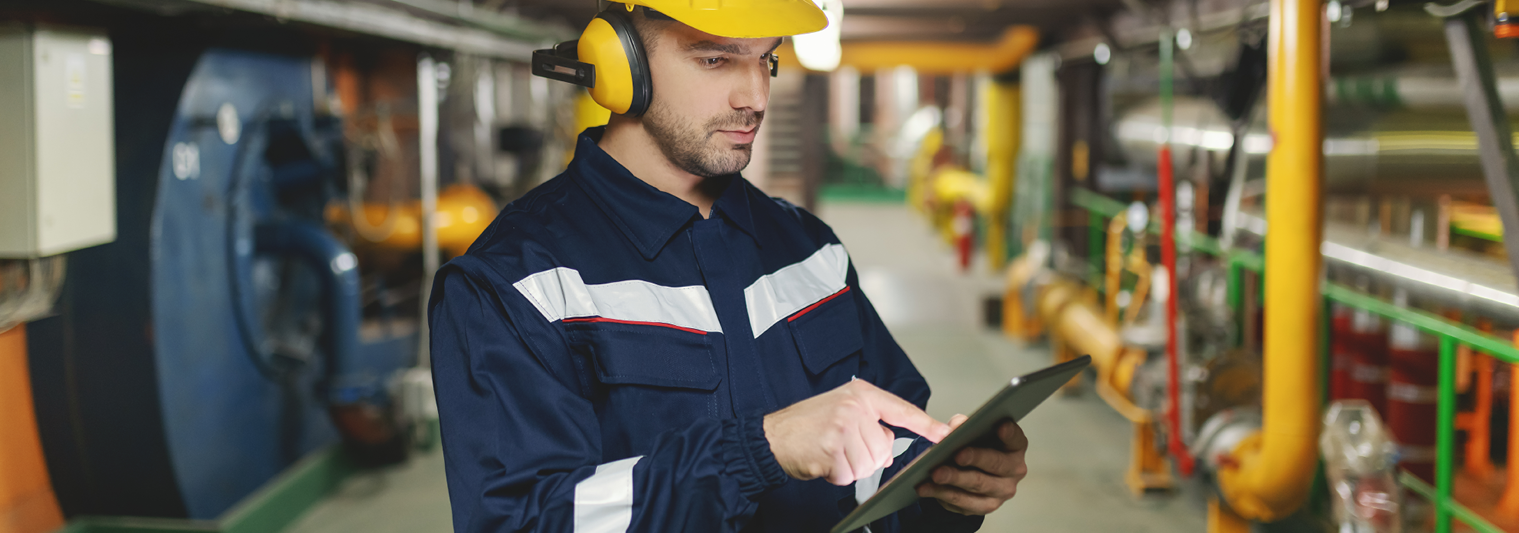
A proper risk assessment process is a key part of any well-run asset management program. In this blog post, learn how digital transformation technology can:
- Make risk assessment inspections and reporting easier to conduct and share,
- Bolster your company’s compliance and safety efforts,
- End error-prone paper documentation,
- Provide an electronic history of past problems,
- Enable you to avoid costly unplanned shutdowns.
Companies in asset-intensive industries – oil and gas, chemical processing, mining and metals, utilities, and manufacturing – face risks every day. Unfortunately, not every organization takes assessing risks as seriously as they should. Some companies believe risk assessment interferes with normal day-to-day operations. Others think it offers little value versus time, effort and money spent. This attitude leaves them exposed. So, they’re often unprepared when those risks become reality.
Lack of a well-designed risk assessment program can cost a company dearly. Obviously, loss of assets and production pose the biggest risks. There are also human expenses to consider, such as injuries, lost productivity and turnover when workers leave what they consider to be an unsafe environment.
Such facilities face government fines, sanctions and lawsuits that eat away at revenues and profits. Additionally, companies may jeopardize customer relations when a risk-related shutdown delays order delivery. Too many angry clients can tarnish a company’s reputation, which complicates the sales process.
Someday a worker will notice a safety problem. Perhaps a vessel is leaking a hazardous material, or rotating equipment isn’t in proper repair. It’s not a matter of if, but when.
Digital transformation offers a way to design and implement an effective risk assessment program that protects your company, its assets, employees, revenues and reputation.
What is digital transformation? Essentially, it’s the integration of digital technology into all areas of a business, fundamentally changing how you operate and deliver value to customers. It’s rethinking old operating models and becoming more agile in your ability to respond to issues. More specifically, it’s a business cultural change.
There are many digital risk assessment software packages available in the market right now. Each has its benefits. One such solution is mWorkOrder from Innovapptive, a mobile-first digital transformation provider. Innovapptive understands the industrial market’s unique needs and has designed its products to meet those requirements.
mWorkOrder offers a robust digital solution to inspect and report potential problems before they occur. Clients can prioritize, assign, manage and track work orders to fix the situation. All in real time. All in an easy-to-use package that works with any mobile device, be it a smartphone, scanner, wearable, etc.
mWorkOrder’s real strength comes from its concurrent solution, RACETM Dynamic Forms. Using these products in tandem, you can create a customized electronic risk assessment inspection list and matrix that best meets your specific needs:
- Develop a comprehensive checklist to find problems in the making,
- Classify a situation by its likelihood of occurring,
- Rate risks by their potential consequences to people, assets, the environment, your company’s reputation, etc.,
- Determine a problem’s potential impact before it affects your bottom line.
With RACE Dynamic Forms and mWorkOrder, pick the assessment fields based on what’s important to you.
mWorkOrder is SAP-certified and works well with other back-office ERP systems. Maintenance crews and inspection teams, equipped with easy-to-use mobile devices, can quickly and effectively scan your assets and enter crucial information, cutting time-consuming and error-prone paperwork. Maintenance managers, planners and schedulers view real time data from the field via desktop dashboards. They can then digitally prioritize, assign and track repair projects, cutting potential risks and minimizing costly downtime.
The result is a total transformation of your operations:
- Risk assessment is no longer a burdensome chore that interferes with day-to-day operations,
- Compliance and safety regulations have been met,
- Real-time digital updates have replaced the cumbersome manual paper process,
- Problems have been documented and electronically stored, providing a valuable history to help spot current and future risk trends,
- Less chance of an unplanned shutdown hurting production.
To learn more about mWorkOrder and RACE Dynamic Forms, click here to schedule a free demo or call us at 844-464 6668. Our experts are standing by to introduce how digitally transforming your risk assessment can turn a business challenge into an advantage.
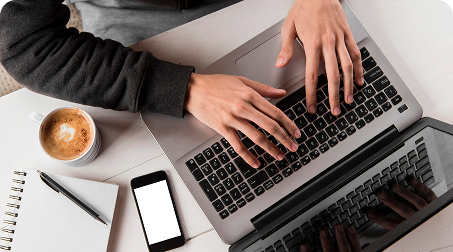
See It In Action
Schedule a personalized demo to see how our solutions can help your business thrive.
- 22-04-2025
The $3.6B Unlock: Solving the Chemical Industry’s Labor Crisis and EBITDA Pressure in One Move
“Constraints don’t slow innovation—they force it.”
- 21-04-2025
Chemical Industry's Margin Erosion: A Wake-Up Call for Operational Efficiency Amid China's Oversupply
The global chemical industry is facing mounting challenges, with revenue declines and shrinking...
- 21-04-2025
Why Wrench Time Isn’t Improving: The Hidden Costs of Traditional Maintenance Scheduling
For years, industrial leaders have relied on a common but flawed assumption: "Better planning and...