Using Guided Work Instructions to Prevent Tribal Knowledge Loss at Industrial Plants
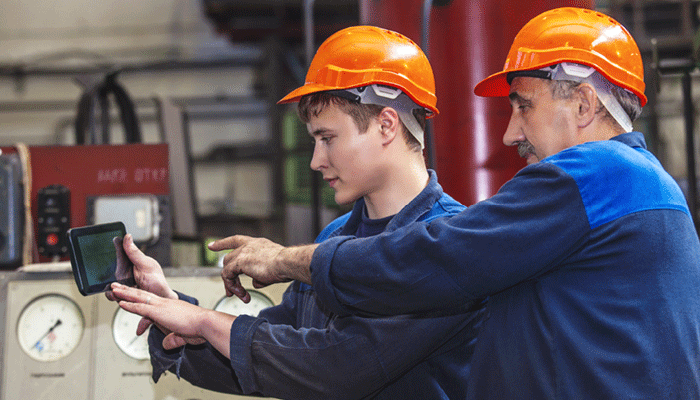
The Great Crew Change is upon us. If you haven’t heard of this phenomenon yet, you soon will. It’s going to have a tremendous impact on your plant’s operations and talent recruitment efforts for years to come.
What is the Great Crew Change? 451 Research describes it as a “demographic time bomb,” and gives this definition:
“… a common term used across the industrial sector to describe the ongoing retirement of a large body of experienced workers in factories and construction. It is usually linked to the lack of replacements to adequately absorb the skills and experience required for continued operation.”
According to the U.S. Bureau of Labor Statistics (BLS), the median age of all workers employed in America today is 42.3 years. That includes all industries, from heavy manufacturing to the local fast food outlet.
For some businesses, such as shoe stores, like Foot Locker, the median age is a youthful 25.7 years. At Internet companies, such as Google, it’s a little older, at 34.0. Most industries fall around the overall median of 42.3. However, at industrial plants, the median age is frequently older. For example, as of January 2020, the BLS gives these figures for various industries:
- Chemicals: 44.6
- Oil & gas (upstream): 42.9
- Oil & gas (downstream): 42.4
- Mining: 47.6
- Utilities: 45.4
- Pulp & paper: 46.7
- Food processing: 41.9
- Beverage manufacturing: 39.3
- Pharmaceuticals: 43.8
- Medical equipment: 44.5
- Manufacturing: 44.1
These numbers show that of the major industry groups, oil & gas is at the overall median age level, and food & beverages is below. All others are above, with mining the highest.
What does this mean, how does it relate to the Great Crew Change, and most importantly, why should you care?
The Baby Boomer generation, those born between 1946 and 1964, is now well into the retirement years. The oldest Baby Boomers, in fact, have already left the workforce, but millions more are approaching the end of their careers. Generation X, those born between 1965 and 1980, followed the Baby Boomers and are now set to take their place in senior plant positions. However, there are far fewer Gen X’ers than Baby Boomers, and not nearly as many Gen X’ers went to work in industrial plants. This creates a problem.
Baby Boomers have accumulated a huge reservoir amount of knowledge and experience in their long tenures. Not all of this knowledge is written down and not all of this experience can simply be handed over to a replacement. When the retiring Baby Boomer walks out of the plant gate for the last time, all of that is gone, for good. This is what is known as tribal knowledge (or sometimes, institutional knowledge).
Tribal knowledge is an important asset many companies don’t know they possess or can lose. Like the adage, “You don’t know what you’ve got until it’s gone,” tribal knowledge’s value is often only realized when it’s no longer there and can’t be accessed.
In 1905, Spanish essayist George Santayana once famously wrote, “Those who cannot remember the past are condemned to repeat it.” Santayana couldn’t predict the Great Crew Change. That was far before his time. But we can apply his words to the current situation at many industrial plants.
Older workers know things about your plant’s operations, processes and equipment that just aren’t part of any manual or spreadsheet. When there’s a problem, they draw upon this deep well of knowledge and experience to help them solve issues. They understand what to do in a crisis, and just as important, what not to do to come to a successful resolution. They’ve been through similar situations before. This could be about repairing a faulty valve, conducting a cycle count or performing safety risk assessments.
A younger worker, on the other hand, either has to lean on the older one for mentorship (the ideal solution for everyone) or learn through trial and error (the costlier alternative). Trial and error means past mistakes may be needlessly repeated. Younger front-line workers are “Digital Natives” used to running their life on a smartphone or a tablet. They expect their working life to be no different. They lack tribal knowledge, but will demand to be guided with step-by-step work instructions on smart devices, working closely with a more experienced front-line worker to bridge the tribal knowledge gap.
In a post-COVID-19 world, it gets even more challenging. Companies are required to embrace and practice social distancing guidelines and other safety precautions. We have all already gotten used to working from homes via a video conferencing solution such as Zoom, Cisco Webinars or Microsoft Teams. Industrial companies also need to find ways to enable communication and collaboration between their younger front-line workers and experts. Forward-looking companies are already investing into remote operations centers to house experts to provide remote guidance using digital technologies such as a voice operated smart glass. The remote operations center is then able to carry out a two-way video conferencing between an expert and a young front-line worker to enable over the shoulder coaching with a “What I See is What You See” approach.
Business consultants are making a fortune counseling companies on how to capture valuable tribal knowledge before it leaves. There are solutions, however, that can accomplish this without a hefty consultant’s fee.
Digital transformation offers one such solution. Through a strategy called the Connected Worker, industrial companies are using Connected Worker platforms to author and digitize their guided work instructions so they can be accessed on hand-held mobile devices and smart glasses for hands-free operation. Smart glasses facilitate a two-way video call to drive new ways to impart and transfer valuable tribal knowledge from older, experienced workers to their younger counterparts. How does it work? Let’s go back to the faulty valve mentioned earlier for an example.
A young technician fresh on the job has been assigned to assess and repair a faulty valve. Should this valve fail, it will cause a production shutdown, costing the plant revenues, squeezing margins and potentially endangering an important customer relationship. Sounds pretty critical, right? So why did the plant give such an important task to such an inexperienced worker? Because they are making use of a Connected Worker strategy that enables the young tech with step-by-step, visual (pictures/audio/video) and guided work instructions to carry out a complex maintenance job.
The young front-line worker is in constant contact with a senior technician via smart devices (such as a smartphone, tablet, smart glasses or smart watch). The young worker can readily access necessary information from guided work instructions and operational data from an ERP system, such as SAP. In addition, at a click of a button, the senior technician can monitor the situation at all times using a desktop app and remotely collaborate via a two-way video call. The senior tech can answer any questions and actually see and hear what his younger counterpart is doing from the younger tech’s point of view. It’s almost as if the two are standing together in front of the faulty valve, even though they are really miles away from one another.
With this technology, the senior tech can help younger front-line workers overcome the daily roadblocks and challenges they face on any work order. The senior expert technician can mentor them, in real-time, through any repair process and pass along irreplaceable tribal knowledge that might have otherwise been lost. Thanks to this agile, innovative technology, repairs are made, production continues, revenues keep flowing and the customer is happy. Not only that, the younger techs have learned some valuable lessons they can apply to future work orders due to some time-saving tips the senior tech passed along during the call.
Many companies today are offering Connected Worker solutions. However, not all include the authoring and digitalization of guided work instructions. Nor do they combine these instructions with rich and context-relevant operational data from ERPs, such as SAP, and make them available on smart devices, such as smartphones, tablets and smart glasses.
In the post-COVID-19 world, simply enabling the technician with a mobile app is no longer sufficient. You need to be thinking of enabling hands-free, sight and voice command operations, with on-demand, two-way video conferencing that enables over-the-shoulder coaching capabilities with a remote expert. If you’re concerned about losing tribal knowledge or just want to improve front-line worker efficiency and productivity, you’ll want to be sure any Connected Worker solution you investigate has such a feature.
Questions? Innovapptive pioneers in Connected Worker strategies and offers a comprehensive platform that empowers the front-line worker in the post-COVID-19 era. We take pride in converting “Tribal Knowledge” to digital, step-by-step guided and visual work instructions, and we make them available to front-line workers with a few simple voice commands to help them get their jobs done faster, better, cheaper and safer. Watch a short, two-minute introduction video here. Then, click here to schedule a free demo, or call us at 844-464-6668.
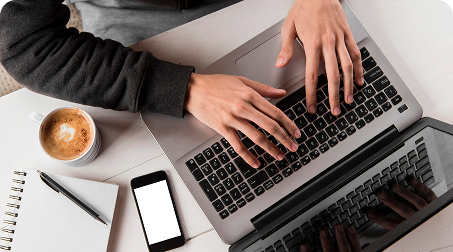
See It In Action
Schedule a personalized demo to see how our solutions can help your business thrive.
- 22-04-2025
The $3.6B Unlock: Solving the Chemical Industry’s Labor Crisis and EBITDA Pressure in One Move
“Constraints don’t slow innovation—they force it.”
- 21-04-2025
Chemical Industry's Margin Erosion: A Wake-Up Call for Operational Efficiency Amid China's Oversupply
The global chemical industry is facing mounting challenges, with revenue declines and shrinking...
- 21-04-2025
Why Wrench Time Isn’t Improving: The Hidden Costs of Traditional Maintenance Scheduling
For years, industrial leaders have relied on a common but flawed assumption: "Better planning and...